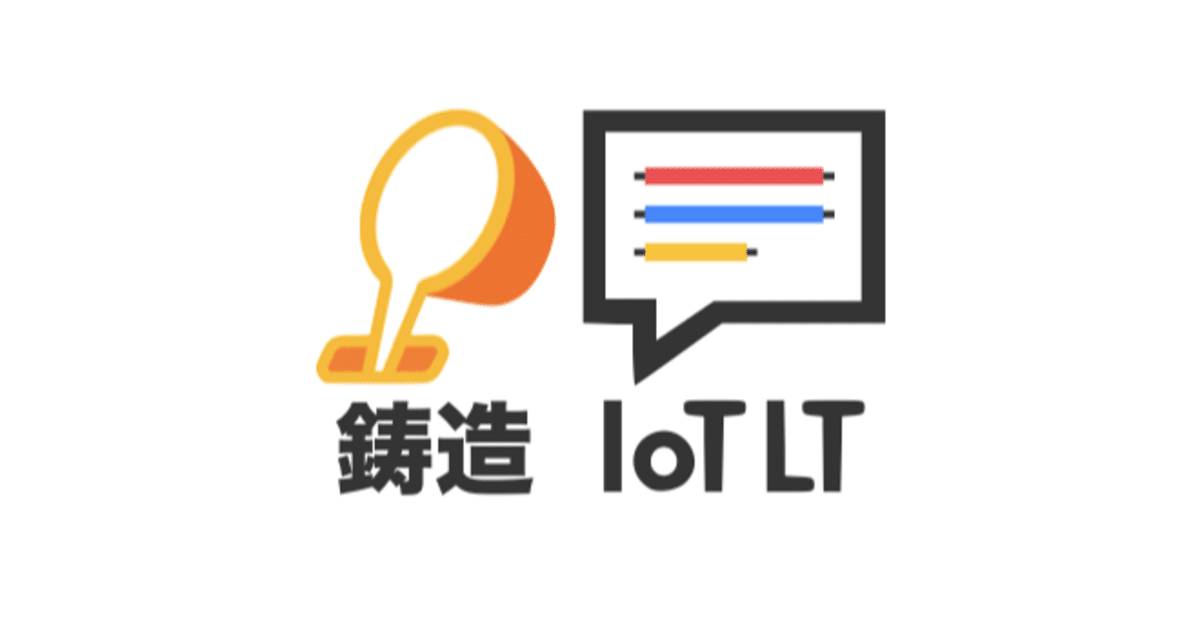
鋳造IoTLT Vol.3 を遅れてレポート
2021/03/09(火)に開催されたIoTLTのスピンオフ企画「鋳造IoTLT」が開催されました。鋳造といえばかつては機械工学科だった私にとって、型の上に砂をかぶせて、上からパンパン叩いて、型抜いて・・・高熱でどろどろに溶けた金属を穴から流し込む・・・・ITって関係あるの?といった世界。いったいどんな世界が広がっているのか?・・・・当日は16:00開始という事でさすがに勤務中なので参加する事ができませんでしたが、Youtube見て復習してみます。
Youtubeはこちらで公開されています。
オープニング 藤原さん
まずは司会の藤原さんから今コミュニティの紹介です。IoTLT本体の紹介に始まり、LightningTalkのルールの説明が行われました。
そして本日のスケジュールです。
ここから「鋳造」の説明です。鋳造はプレスとか切削などのような金属加工の方法のひとつです。溶けた金属を砂や金属で作った鋳型と呼ばれる枠の中に流し込んで形を作るもので、一説んは4000年の歴史がある金属加工法です。
鋳造という加工法は複雑な形状を作ることが出来、様々な形、少量生産から大量生産まで対応する事ができるためマンホールや調理器具、車など乗り物の部品にも使われています。超ハイテクなローテクです。
そして鋳造IoTLTを始めた目的の説明に入ります。鋳造業界は業界内の交流は少なく、業界の外からはよくわからない・・・といった世界です。それを何とかして情報交換を進めようとこの「鋳造IoTLT」を始めました。2019年8月に機械振興会館で1回目が開催され、その後札幌で第2回目が開催されました。コロナ禍ですこし伸びていましたが、今回が再開の3回目です。
M5StackとRaspberryPiでBLE通信し、データの見える化をしてみた:アサゴエ工業 西さん
アサゴエ工業さんには電気炉とキュポラがあります。キュポラは上部より金属材料を入れ、コークスの熱により溶解させる炉です。安全性は十分に考慮された機械ですが、故障などにより危険な一酸化炭素が発生する可能性があり、これを測定してくれないかと現場から依頼がありました。
しかしながら、すでに工場内には監視カメラを設置した関係でIPアドレス不足になっています。そこでIPアドレスを使わないBluetoothのひとつであるBLE(BluetoothLowEnergy)に着目しました。転送速度は遅いのですがセンサーのデータを送るには充分です。
全体の構成としてはデータを送り出すペリフェラルにはM5Stack、データを受ける側であるセントラルにはRaspberryPiを使用しました。全体2万3千円くらいの価格で揃えられます。
今季ア構築したBLEの通信の仕組みですが、ブロードキャストモードと呼ばれるモードでデータの送信をしています。M5Stack側はArduinoで1回/1分でセンサーデータを取得して、BLEでアドバタイジングするプログラムを作りました。RaspberryPi側はPythonで作成しています。BLEのライブラリはBluePiというものを使用しています。
収集した情報はウィングアーク1stさんのBIツールであるMotionBoardのダッシュボードで見える化をしています。
今後の取り組みとしては、他のセンサーデータもRaspberryPiでデータを収集していましたが、ほかのデータもBLEを使ってIPアドレスの問題を解決しようと考えています。
データロガーでコスト低減しちゃった 株式会社キャスト 若林さん
株式会社キャストさんは福島県白河市の工場で大型機械の部品の鋳造をしています。
前回のLT(2019/11)では設備の電力量の見える化をしましたが、今回は見える化の結果、売り上げの減少に対し電力消費量が減少していないという事を解決するため、コンプレッサーという機器に着目しました。
オムロンの簡易電力ロガーでモノタロウで3万3千円くらいで買えるのを2つ使用しました。
コンプレッサーは鋳造に使用する砂を高圧力で送り出す機械ですが、砂再生機から砂を輸送する為に夜間は3号機を追加して動かしていました。これを見えるかした結果、実際には砂を送っていない無駄な時間があることを確認できました。その結果タイマーで必要ない時間を停止したり、インバーター付きの2号機と無い3号機の役割を変えることで改善を図りました。
その結果、年間でのコストダウンは合計で158万円になり、3万3千円のコストを充分に回収できました。
次は温度記録や成分情報の記録を記録する溶解トレーサビリティシステム導入の話をしたいと思います。
資産流用IoT 過去資産を生かしてローコストIoT 長島さん
次は那須塩原の錦正工業の長嶋さん。社長自らITやIoTに理解があり、いろいろチャレンジしている会社だという事です。
キーワードは「セマンティック」 レインボー・サイクロンIoT~メーカーは多種多様、物理層も論理層、それを集めるソフトうケアも多種多様です。タイミングもデータもバラバラなものを繫ごうという取り組みです。
いまさら全部買い替えてそろえるのは無理、CSVに落としてEXCELにあつめるのも無駄の極み・・・・というわけで機械でそれをやろうと考えました。
データベースサーバを繫いだり/SQLite2/3で開いたり/テキストエディタで開いたり/無線LANのパケットを拾ったり/ダミーのサーバーでデータを拾ったり/ブラウザで通信内容を見たり/ブラウザのふりをしたり/どう動いているか予測したり/ブートメディアを調べたり/デバック用の端子を探したり/センサーだけでもアリュデュったりラズパったり・・・
実行手段は諸般の事情でお店出来ませんが、そうしてデータを集めてみた結果です。
出退勤のICカードからお弁当の注文もしています!
いろんな事はやっていますが、すべて同じデータベースに保存しています。「つまりセマンティック」です。これらのデータはすべてWebブラウザで使うように作っていますのでブログパーツ的にいろいろなところで使えるようになってます。データを全部持っているのでロボットの座表計算などいろいろなところに再利用ができます。
まとめとしては、データの再利用できるか確認する事、データ形式をそろえる、データを人質にとるサービスに気を付けるなどありますが・・・とりあえずやっても、なんとかなります。
IoTを利用した古い設備のネットワーク化 五位堂工業株式会社 津田さん
次は奈良県の五位堂工業株式会社の津田さんです。五位堂工業株式会社はその祖先が奈良の大仏を作ったとされる由緒のある会社です。
現在の工場の設備は古くはないのですがネットワークにつながるものはほとんどありません。砂の使用量や投入電力量を測定したいのですが、これを誰でも見れて、かつ末端設備に負荷をかけずにモニタリングする方法を検討しました。
導入したものはCONTEC産業のIoT CONPROSYS M2Mコントローラです。(数万円) 産業用なので耐久性に優れ、工場内で使われ、電圧変換が不要のDC24Vでネットワークに接続すればブラウザで簡単に見ることが出来ます。汎用性は低いですがGUIでラーニングコストは低いデバイスです。
これで見える化「稼働状況ミエルくん」を実現しました。高周波電気炉の電力量、温度
バッチ式混錬機での重量、樹脂強度、硬化速度などの要素を取得するようにしました。
まとめです。
使用量を日単位で取れるようになったことで月次の生産情報の精度が上がり、電気炉では作業者別の効率の見えるかによる目標の明確化ができました。情報の見える化は設備自体には影響が少ないがNWなど注意が必要とわかった事です。
次の課題は保守メンテナンスの改善です。
光センサーを使ってみた 石川可鍛製鉄株式会社 塩谷さん
次は石川県の石川可鍛製鉄株式会社の塩谷さんです。
取り組みの内容です。画面は使用している日報入力の画面です。これの左下にあるボタンですが、作業者はこのボタンでそれぞれの作業の進捗度合を登録し、それがSQLServerに送られます。そのデータを元に生産管理のサーバにアップロードしています。
その状況、ボタンが押される時間と次のボタンが押される時間、その時にやっている製品を状況モニタとして表示しています。今がどういう状況でその経過時間がどれくらいか、誰が何の作業をしているのかリアルタイムで見えるようにしています。
それを元に一日の稼働状況を見えるようにして、どのような動きで設備が稼働していたのか見えるようにして活用しています。
ただ今の話ではこのボタンを「行燈ボタン」と呼んでいますが、これを押すのは人なので機器の稼働状態は正確にわかりません。これをシグナルタワーの光を取得して稼働・停止をわかる仕組みを作りたいと考えています。
今回活用したのは子供の教育用で使われている「Ichigojam」というマイコンを使用しました。それで取得しした情報をWifiで接続したサーバに送るためにMixjuiceというネットワークボードを活用しました。
その先端にアナログのトランジスタを接続しまして、投資としては5銭程度でした。
このセンサーの信号をWebサーバー経由でSQLサーバに送ります。光センサーを指でふさぐ~稼働の状況と同じ~を認識しています。光を検知するのが停止の状況になります。これで稼働の状況をリアルタイムで把握することが出来、そのデータを元に改善活動を進めます。
問題個所のモニタリング 佐藤鋳工株式会社 三浦さん
北海道の佐藤鋳工株式会社さんの事例です。
佐藤鋳工さんは契約更新であまったiPhoneを使用して簡単なIoTをやってみた事例を2つ紹介します。
タイマーの見える化
工場内の増設工事の結果、作業者の位置からタイマーを確認できなくなってしまったのを2台のiPhoneを使って改善、タイマー近くで撮影した画像を作業者のそばに設置したiPhoneにフリーのミラーリングソフトを利用して映すこと解決しました。これによりタイマー表示時間の記録制度が向上しています。
シェーカーのモニタリングによる地金見逃し防止
シェーカーとは鋳造ではみ出した地金をふるいにかける機械ですが、ときどきその網目をすり抜けて下のベルトコンベアに落ちてベルトの切断が時折発生閉まっていました。これをiPhone2台で監視する仕組みを作りましたが電波が悪い場所だったので20メートルの長いHDMIケーブルで接続しました。これによりベルトの切断は発生しなくなりました。
今回の改善で現場の人と話すと他のiPhoneからも確認できないかとか、録画をしたり、異物の自動的な判別ができないかなどの要望が出てきました。使わなくなったiPhone100台あるので取り組んでみたくいいアイデアがあったらという事でした
データを活用するための見せ方:仮説と検証トライ 新東工業株式会社佐藤さん
次は新東工業さんの発表はIoTそのものよりももっと泥臭い「データの重要性」についての内容です。今回は鋳物の不良と砂の状態について着目し、あえてばらつきを発生させて比較テストを行いました。鋳造の工程の中で砂は使用されますが、その砂はリサイクルされる為、砂の処理としても循環する工程があります。この中で砂の状態が鋳物の不良を左右するという仮説です。
鋳物の不良には「焼付き不良」というのがありますが、これは微粉と呼ばれる小さなゴミに起因すると考えました。またそれを洗い流す水分の含有量との関係についても検証しました。この憲章は社内研修とコラボレーションして実施しました。
その結果を、下図のような標準器の様な十字型の座標で部粉や水分の量のばらつきを見える化して検証しました。
検証の結果、砂の管理が鋳物の品質にとって重要という事がわかりました。
砂運搬コンベアの稼働状況の見える化(途中経過)~思うように進んでいない事例:株式会社明石合銅 明石さん
明石合銅さんの話は砂運搬コンベアの不具合(砂の山盛り)を早期に発見し対処するための取り組みです。コンベアのトラブルの前にはモーターの過負荷があるのではないかと仮説を立て、電流値を測定しようと考えました。
最初はアナログの電流計を取り付け、それを人力で測定する方法でやってみましたが、やはりこれは大変でした。
そこで県が行った4日間のIoT研修会に行ってIoT研修でラズパイを使用して測定結果を記録する方法を学びました。
研修後に早速測定に必要な機材を手に入れ、苦労しながら自力で取り組みましたが、電流計をラズパイに送る方法がわからず、外部の人に聞いて新たに部材を購入しましたが、かなり時間がかかってしまいました。
そして何とか測定できるようになりましたが、今度はなんだか測定したデーターが思っていた数値と違う状況になり、ここで停滞してしまいました。
この状況を打破するために外部の支援を頂くとかを模索していますが、アイデアや知見がありましたら宜しくお願いします。
研修会などでIotの実現が安価にできることを学ぶことは重要ですが、それを実際に動かすためには基礎知識が必要なのも事実です。
熱処理炉の見える化 株式会社メタルヒート 柴田さん
メタルヒートさんは安城市にあって鋳造業ではなく熱処理業の会社です。ネッ処理業界は鋳造業界よりもマイナーで小さな会社が多いです。熟練工による作業が多く属人化されやすく、技術継承が課題となっています。
これを解決するために熟練工の行っている作業の状況をそれそれの測定すべきファクターに落とし込みました。
そのファクターを測定できるよう設備を一新し稼働させました。これにより監視、観測がリアルタイムで把握できるようになりましたが、今後はそのデータを技術継承にどう生かすかを模索しています。また新工場や海外の工場への展開も実施・計画しています。
生産管理を・・してみる 横道さん
ジェイテックさんは鋳物加工などを行っている15人ほどの会社です。横道さんは元々センサー関係の電気設計をで働いていましたが、実家に帰ってきて、そこで渡されたのがJISQ9100という航空関係の規格の対応の仕事で、やってみたら紙ばかりでやってられないということで、EXCELマクロやACCESSでやりましたが、もう一歩なので仕事の合間に勉強してMySQLを使って落ち着きました。
SentOS上のPCサーバーで運用しています。ログインするとますは出退勤のデータの表示になります。
TopページではSNS機能が搭載されています。
ビックリマークで不具合の発生が示され、詳細の情報にリンクされます。これで監査があっても慌てなくて済むようになりました
そのあと品証や営業など様々な立場の仕事をしましたが、そのたびに機能強化をし、今のような形になっています。納期管理でいうとこのような感じになっています。
デザインは外部の方に一部お願いしています。製造トレーサビリティにも連携しています。ドラッグアンドドロップで操作することが出来るようになっています。
モノつくりのエースのような人も管理側に回ることなく現場で腕を振るってほしい・・・そういった想いで省力化を図る事が大事
製品に紐づけることでデータの価値はものすごく上がるので会社の資産という事で価値をあげていく事になります
プロトアウトスタジオの紹介 のびすけさん
次はIoTLT主催ののびすけさんからプロとアウトスタジオの事例紹介です。
最近DXは話題になっていますがDXはある程度自分でやっていかないとコストもかかるし融通きかない・・持続しないという事があります。社内である程度プロトタイプまでやらないと・・と思います。プロとアウトスタジオでは技術者を育成するというのではなく、ツールを迂回こなすことに注力しています。
事例としては長野の製造業の工場勤務の方のエラーを検知して状態を可視化するとか、他の方の搬送ロボの様なもの・・・どうやって課題を解決するか・・・課題発見能力に重点を置いています。
今は法人向けのDX人材向け教育をやっていますが、競争領域ではある程度テクノロジーが必要で時間が必要になりますが、それいがいの非競争領域がありますが、こちらはちょっとした工夫で出来るという事があります。
企業からはこれを短期間で出来ないかという話があり模索したのですがPowerAutomateDesktopでも難しく感じるという事で最近はEXCELをベースにしたカリキュラムを考えています。・・・これの練習台になっている企業を募集しています。
製造業自分でやってみた事例 大川さん
MotionBoardのウィングアーク1stの大川さんによる製造業の事例紹介です。東京商工会議所のものづくり推進委員など社外活動も多くやっています。
早速事例紹介です
ミツミ製作所さん:金属の切削加工業で無償のスケジューラやOneDriveやGmailなどのツールを使いきって情報共有のスピードアップを実現し、商談時に「帰って検討」から「それならできます」まで変化。
平澤製餡所:多品種少量生産のあんこの製造においてタブレットを導入し、システムを使わずEXCELを工夫して業務の効率化そしています。技術継承のために動画をつくったりという工夫も行っています。
タカハシさん:ゴムパッキンの製造業で大量の伝票処理をEXCELやACCESSで自ら作ってから外部にシステム化をお願いするなど自分たちで改善を行っている会社で必要のないキーボードを簡略化したり、バーコードを徹底活用するなどの改善も進めています
旭鉄工さん:3種類のセンサーで清算数や停止時間などを徹底的に可視化して、この仕組みをパッケージ化して同業者に販売しています。
ここで告知です。
まずは東京商工会議所のセミナーです
そしてウィングアークさんのセミナーです
GAFAMI&OSSwithCP:データをつくる 杉山さん
杉山さんは燕三条で樹脂機械部品加工をしていて、個人的にはシェアスペースを運営したり、ものづくり学園燕というコミュニティを運営したり、様々な会社のアドバイザーをしたりしています。
儲ける方法には2つあって、売り上げをあげるか経費を抑えるかですが、今日は経費のほうを話をします。
これには情報が必要で、商法収集はGAFAを駆使してバーz他yるで行います。結果、視野が広まり思い込みと慢心が亡くなります。
MI&OSSですが PowerAutomateDesktopとEXCEL(Microsoft)そしてNODE-RED(IBM)この組み合わせが最強かなと思いますそして、オープンソース~CADではOpensCAD、FreeCADなどがあり、GoogleではAIは無料で公開されています。
Googleで提供されるAIによるMediaPipeHandsやTeachable Machineでは現場ではキーボードは使いにくいという問題の解決につながると思っています。
そして中国部品を使っていろいろと試作して、その中でだんだんいいものを作っていく事を考えています。
カメラで既存設備をデジタル化 アンビエントデータ株式会社下島さん
アンビエントデータの下島さんはカメラを使った既存設備からのデジタルデータ取得の方法の話です。制御盤のランプやメーターを読み取ってデータにします。使うのは普通のWebカメラとラズパイです。
事例としては静岡の栗田産業さんで電気を大量消費する電気炉とボトルネックになりがちなショットブラストからのデータ取得を行っています。
まずショットブラストです。制御盤の前にカメラを設置してランプをと見込ませています。
カメラの映像です。色を識別しデータをクラウドに送って可視化しています。
これにより異常停止を検出し、通知したりできるようになります。
電気炉の事例です。こちらはアナログデータの映像を撮影し、それを解析してメータの針を認識して角度を計測します。
これをクラウドに送り込んで電力消費量のモニタリングしています。
アドビ円とデータでは現場でのIoTを支援するセミナーやコンサルをやっています。
<IoTLT>
業界初 IoT縛りの勉強会・LT会です
Facebook グループで情報が流れています
Qiita Organizationsはじめました
Youtubeチャンネル (LTのアーカイブ) - コロナウィルス対策でオンライン活性化していきます。
この記事が気に入ったらサポートをしてみませんか?