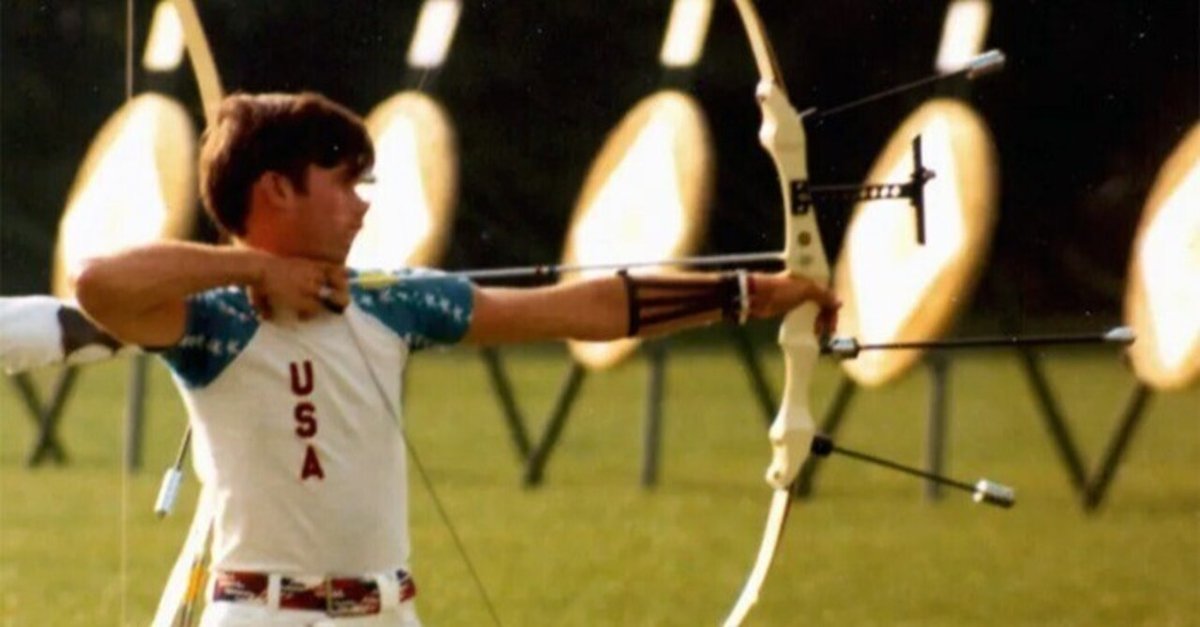
形あるものは、いつか崩れる。
ハンドルが折れるのは、リムほどよくは見かけません。では折れないかというと、そうではありません。それに、折れなかったとしても、アーチャーには分からなくとも、曲がったり、捻じれたりするハンドルもあります。
先に言っておきますが、「形あるものいつかは崩れ」ます。この世の中に「永遠」などはないのです。ただし、どこで壊れるか、いつ折れるかは重要です。
最近では「金属疲労」という言葉が浸透したお陰で、金属は折れない、大丈夫といった神話を信じる人も少なくなり、ハンドルもいつかは折れる、永遠はないと思ってもらえるようになりました。しかし逆に、ハンドルにしても、リムにしても、耐久性ばかりを追いかければ、性能を置き去りにして過剰品質になり、買替需要がなくなります。
シューティングマシンで、30ポンド5000射でハンドルが折れれば問題ですが、50ポンド4万射(これはヤマハが行っていた実射促進耐久テストの公表値です)も持てば、実際の使用では毎日練習しても、20年以上は平気です。女子なら、半永久的に使えるかもしれません。リムも同じことです。
壊れる商品は困ったものですが、壊れなさすぎる商品も、メーカーにとっては困りものなのです。メーカーは品質と値段のどこかで折り合いをつけ、ユーザーはどこかで納得して新しい商品を購入するのです。これが世の常であり、アーチェリーの世界においても然りです。
ヤマハは1977年に「Ytsl」で世界制覇を成し遂げました。しかしこれをモデルチェンジした「YtslⅡ」でハンドル折れを起こし、その対策に長い時間を要しました。このように他のメーカーにおいても同様に、大なり小なりの問題を抱えてきたのが現実です。
1972年ジョン・ウィリアムスはホイット最初のテイクダウン「TD1」でオリンピックを制覇します。しかしそのハンドルは折損が続き、商品となることはなく、3年後の世界選手権でダレル・ペイスが優勝に使ったのは改良された「TD2」でした。

TD1 では一体型のグリップだったものが、「スナップオン」形式に
変更になったモデルでした。。
1984年ダレル・ペイスがロサンゼルスで2個目のゴールドメダルを獲得したのは、「Gold Medalist」です。しかしこのハンドルは市販されてからも、曲がりに悩まされます。何度も形状変更を行いますが、曲がりは1988年にソウルでジェイ・バーズが使ったモデルまで続きます。
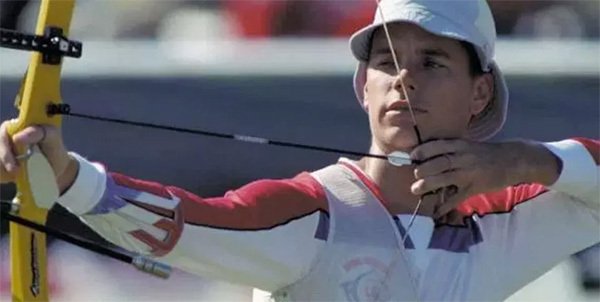
それまでのモデルと同じようには見えますが、
何度も金型変更が行われ、製造時期によって厚さや形状は細部で異なります。
そしてホイットは、形状変更が簡単なNCハンドルになってからも「Avalon」でクラックに悩まされました。
では、どのような基準で弓は作られているのか。メーカーはどんなテストを行っているのでしょうか。近年、ヤマハの撤退以降は詳細とまではいかなくとも、どのメーカーも常識的なデータすら公表しなくなり、実射や実戦でのテストも行わずに商品を発売するのが当たり前になってしまいました。
その結果、何シーズンも続く定番と呼ばれるモデルや名器はほとんど皆無で、新商品やモデルチェンジの名のもとに、ユーザーには分らないクレーム対策の改良が毎年のように行われ、ニューモデルとして発表されています。
そこで、世界最高水準の品質を誇った、日本の「ヤマハアーチェリー」が、ハンドルとリムに行っていた「耐久テスト」を、今一度見ることで予備知識としての、弓の寿命や限界を知っておくのもいいかもしれません。 ヤマハが対外的に公表していた耐久性の基準は、これです。
① 実射促進耐久テスト
「弓の強さ:50ポンド基準」×「耐久性:6万射以上」
ここで言う、「耐久性」は弓の強さと強い相関関係にあるので、ヤマハが実際に製造・販売していたリムの「最上位のポンド数の耐久性」を基準において公表しています。それが表示50ポンドという訳です。
では、50ポンドの弓を誰が射つのか。普通のアーチャーが1年間で射つ矢の数は2万本を超えれば、それは結構練習している方でしょう。週に4日以上、1日100数10本を射つと2万射を超えます。とはいえ、実射耐久テストを人間が行うのでは何年かかるか分かりません。そこで使われるのがシューティングマシン、それも耐久テスト用のマシンです。
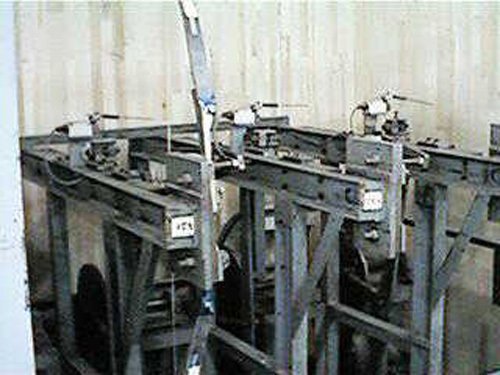
10数台あり、24時間稼働してテストを行います。
これを使って「26インチ引き/40%相当の衝撃負荷空射ち」を、1本のテストサンプルに対して6万回繰り返します。
「衝撃負荷」とは、単純なドローイングの繰返しの静的応力負荷の反復だけでなく、実際のシューティングで弓に作用する衝撃力と同等以上の衝撃力(ショック)を与えるテスト方法を指し、「40%相当」のレベルとは、空射ちのショックと実際のシュートでのショックとの中間レベルの強い衝撃力と考えればよく、分かり易く言えば矢をつがえずに26インチを引っ張ったところから弦を放す(空射ち)動作を、ハンドルを固定した状態で行うのです。
② 熱衝撃(熱冷クリープ)テスト
「(-20℃/16時間 + 50℃/8時間)× 10サイクル」
(28インチ引き/連続フルドロー状態保持)
この「熱冷クリープ」は零下20度の冷凍庫と50度の乾燥炉を往復するものですが、単にストリングを張った弓というだけではなく、グリップとストリングの間につっかえ棒のようなものを入れて、28インチを引っ張った状態の形でこれらの過酷な条件に置くものです。
③ 耐乾・耐湿(乾湿クリープ)テスト
④ 耐候(耐紫外線・耐雨)テスト
上記 ① ② のテストは開発段階での仕様決定の重要な評価基準であり、実際にはこの2つのテストを組み合わせた一連の「複合促進耐久テスト」として評価をします。また、並行してそれぞれ個別テストでの評価も行われます。
上記 ③ ④ のテストは、新素材・新製法の開発や新規の樹脂・塗料・接着剤等の使用に対する評価基準として、主に化学的な特性変化のチェックのために行う耐久テスト基準です。
複合促進耐久テストの実施例
熱冷/3サイクル→実射/2万射→熱冷/3サイクル→実射/2万射
→熱冷/4サイクル→ 実射/2万射
開発段階では、「実射促進耐久テスト」を主体に、試作品/サンプル商品等が折損/破壊するまで徹底的に行う「極限耐久性テスト」を実施します。
どの部分が、どれだけの使用数(射数)で、どのような「壊れ方」をするのかを徹底的に調べてデータを積上げ、この膨大なデータを基に、個々の商品について限界強度/限界寿命を高めるハウツーを設計に生かします。
一方、生産段階における「製品の定常的な品質管理基準」として、定期的に工程からサンプルを抜き取り、同様の耐久テストを実施します。
以上、上記 ① ② ③ ④ の耐久テストは、それぞれの商品が「定められた基準を満たしているか」を評価する「耐久性評価テスト」として実施されます。
分かるでしょうか。世界最高水準の品質、スタンダードは、地道なテストの積み重ねで保証されていたのです。
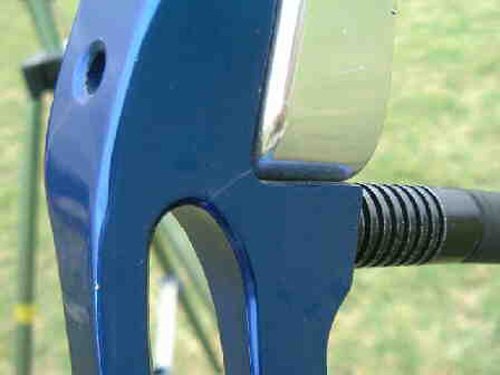
アールの取り方を種々変更を行いましたが、
この部分からのクラックを解消することはできませんでした。
クラックが多発した、HoytのアルミNCハンドル「Avalon」のクレームのような重大な問題も、本来は動的状態でのテストなり検査が確実に行われていたなら、単純な応力集中の問題として、事前に発見できたはずです。また、実際にそれらのノウハウが蓄積されていたなら、もっと迅速な対応も可能だったはずです。
ある意味、これこそが現在のNC旋盤によるハンドル製作の最大のメリットでもあるのです。
この記事が気に入ったらサポートをしてみませんか?