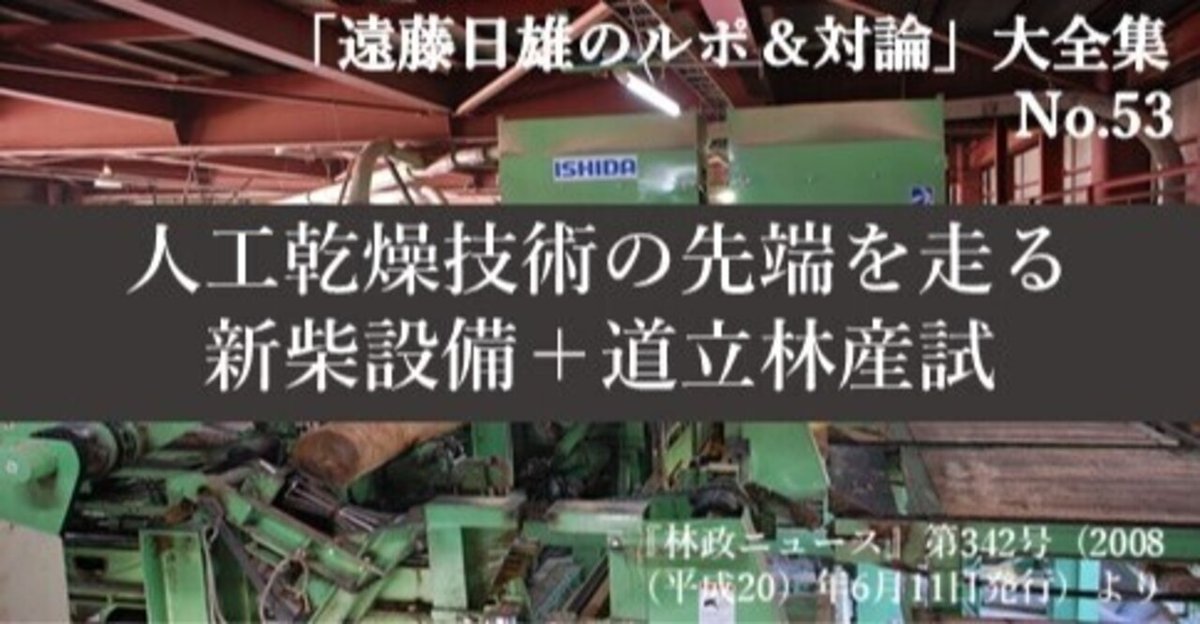
人工乾燥技術の先端を走る新柴設備+道立林産試
現在、国産材製材品に占める人工乾燥材の割合は、わずか20%といわれる。国産材関連業界は挙げて人工乾燥化(KD化)に取り組んでいるが、正念場はこれからという段階だ。そこで遠藤日雄・鹿児島大学教授は、人工乾燥機メーカーのトップ企業である(株)新柴設備(柴豊・代表取締役社長、北海道旭川市)を訪ねた。同社製の人工乾燥機は、全国で過半のシェアを占める。
乾燥機普及の鍵はステンレスパネルの溶接技術にあり
遠藤教授を出迎えたのは、柴社長と幅崎茂工務部長(取締役)。その傍らには、北海道立林産試験場(旭川市。以下、林産試)の浅井定美場長が立っていた。人工乾燥技術をここまで引き上げたのは、新柴設備と林産試の連携であることを窺わせるシーンだ。早速、柴社長は、遠藤教授を工場内で制作中の人工乾燥機の前に案内した。
柴社長
ステンレスパネルの継ぎ目に注目してほしい。この溶接技術が人工乾燥機普及に大きな役割を果たした。
遠藤教授
どういうことか。
乾燥機の自動制御について説明する柴社長(右端)
柴
もともと人工乾燥機は、その躯体を地元の建築業者が、ブロックやコンクリート等で現場施工していた。我々乾燥機メーカーは、躯体が完成してから、内部に乾燥機の各構成機器類、例えばプロペラファンや給排気ファンなどを取り付けていた。しかし、それでは納期が長くなる。また、現場組立時の継ぎ目処理や振動の吸収など技術的に多くの課題を抱えていた。そこで弊社は、躯体を工場内でパネル方式で一貫製造し、それを納入先に運んで簡易に設置する方法の開発に、昭和44年に着手した。その後、改良を加え、昭和59年にはステンレスパネル継ぎ目全溶接技術と自動化制御ソフトを開発した。業界初のことだった。
林産試との共同研究で成果、まず広葉樹の乾燥技術確立
柴豊・(株)新柴設備代表取締役社長
遠藤
新柴設備のこれまでの歩みを教えてほしい。
柴
弊社の創業は昭和30年。当初はボイラーメーカーとしてスタートした。人工乾燥に取り組み始めたのは、その2年後。旭川は道産広葉樹の一大集散地で、家具、建具、フローリング、合板などのメーカーが多数立地しており、そこから人工乾燥技術の要請が来た。昭和48年には、弊社工場内に50石収容タイプの人工乾燥機をパネル方式で製作し、熱源用にボイラーを設置した。
約1年にわたってテストを繰り返し、データの蓄積とハード面の改良を重ねた。テストに供される材は市内のフローリング製造会社から提供してもらい、乾燥しては納入するといった形態だった。その間、ある会社を通じてアピトンの脱脂ができないものかと相談を受けた。そこで、林産試の乾燥科と相談して、昭和49年に成果を得ることができた。これらの期間に得られた厖大なデータの蓄積が、現在のSK式木材乾燥機の基礎をなしている。
遠藤
林産試との共同研究が成果をあげたということか。
柴
当時は、弊社の社員が手弁当で毎日林産試に通ったものだ。林産試の担当研究者も昼夜を厭わず対応してくれ、完成度の高い人工乾燥技術を獲得できた。
遠藤
広葉樹の人工乾燥は難しい。厄介モノ扱いだったブナが利用されるようになったのも、人工乾燥技術が確立されたからだ。
浅井定美・北海道立林産試験場長
浅井場長
スギやカラマツなど国産針葉樹材の人工乾燥技術のベースとして、まず広葉樹の乾燥技術がほぼ確立していたことが、その後の展開につながった。人工林資源の成熟で、今は針葉樹の利用技術だけを意識しがちだが、それだけでは足りない。北海道の森林の7割は天然林で、そのほとんどが針広混交林。天然林の林力の回復に努めれば、いずれ広葉樹資源のさらなる高度利用への技術展開も視野に入る。こうした視点を堅持していきたい。
遠藤
なるほど、難しい広葉樹の人工乾燥に取り組まずに、一気にスギなどの針葉樹の人工乾燥に取り組んでも、その技術に温度差が出る。ピアノなどの広葉樹楽器用材の寸法許容精度はプラスマイナス0・何㎜の世界だ。ところで、新柴設備が針葉樹材の人工乾燥に取り組んだのはいつ頃か。
幅崎茂・(株)新柴設備工務部長(取締役)
幅崎部長
本格化したのは昭和50年代に入ってからだ。もっとも、その前から道産カラマツの脱脂(ヤニ抜き)など人工乾燥技術の確立に向けて、林産試と連携して研究を重ねていた。その成果は、昭和52年に日本木材学会で共同発表した。昭和50年代〜60年代初期が弊社の人工乾燥技術の確立期だった。
遠藤
スギ人工乾燥機の第1号機はどこに設置されたのか。
柴
今から20年前に九州のスギ製材工場に設置したのが最初。当時は、1基10〜20㎥の小さな人工乾燥機だった。
遠藤
今では40〜50㎥が当たり前。100㎥程度の大型乾燥機もある。課題はないのか。
幅崎
人工乾燥室の隅々まで送風ができないなど、改善すべき点がいくつかあったが、それらを解決する装置も開発した。岩手県内に100㎥乾燥機を7機設置完工し、稼働している。
道産カラマツラミナに競争力、次はムク平角など
柱などの構造材分野で、国産材は人工乾燥化に大きな遅れをとってしまった。特に、スギは水分が非常に高く、かつ個体差が大きいという性質があり、抜くのに多大な時間を要するなど、人工乾燥が進まなかった。その間隙を縫うように90年代後半から欧州産ホワイトウッドラミナが大量に輸入された。含水率10%以下という商品性の高さに加えて、コンテナ輸送を駆使してジャスト・イン・タイムの対日供給を行っている。
遠藤
スギやカラマツなどの国産材集成材工場が国内で十数社になった。欧州産ラミナの攻勢に対して、特に東北が踏ん張っている。
浅井
国産材集成材工場でのラミナ製材は、スギよりもむしろ道産カラマツの方が多い。林産試と新柴設備などとの取り組みは、ラミナの人工乾燥技術を加速的に高めた。さらに、道産カラマツの供給力アップによって、皮肉なことに道内ではなく東北でホワイトウッド集成管柱に対抗できる端緒が切り開かれたことになる。
遠藤
なるほど、新しい知見だ。逆にいえば、北海道には高い人工乾燥技術やカラマツ資源が潤沢に賦存していたにもかかわらず、道内製材・加工業界への資本投下が遅れたともいえる。それだけに今後、北海道が東北のカラマツ集成材を後追いする形で産地再編成を図るのか、それとも別の方向を目指すかが問われる。
浅井
そのとおりだ。林産試としては、集成材のほかに有望製品として、例えばカラマツのムク平角であるとか、芯去柱角の製材・加工を考えている。いずれにしても、これらを商品化するためにはそれに見合った人工乾燥技術の確立が要求され、装置の完成度をより高めることや、技術者の養成に注力したい。
調湿管理を徹底し応力を抜く、中途半端はスギ離れ招く
遠藤
林産試は紙・パルプを除く林産研究では、戦後一貫して全国のリーダー格だった。公立試験研究機関と企業の連携こそが新技術確立の地平を切り拓いていくことを改めて痛感する。ところで、競争力のある国産ラミナや間柱を供給するためには、人工乾燥が極めて重要な役割を果たす。ホワイトウッドのような均質性を出せるのか。人工乾燥コストはどうなのか。課題は多い。
柴
きちんとした人工乾燥、特に調湿を厳しく管理して、間柱やラミナの応力(物体に外力が加わったとき、その物体内部に生じる抵抗力)を抜くことが大事だ。この作業で手抜きをすると、ラミナや間柱が曲がったり捻れたりする。
遠藤
平成18年の夏以降、ホワイトウッドラミナや間柱の価格高騰によって、スギへのシフトが起こった。国産材時代へ突入かと期待感が一挙に高まったが、その後のユーロ高にもかかわらず、一部では「スギ離れ」が進んでいる。
柴
中途半端な人工乾燥をしてモルダーをかけても、いずれは化けの皮が剥がれる。今こそ真剣に人工乾燥に取り組むべきだ。そうしないと、真の意味での国産材時代は来ない。
(『林政ニュース』第342号(2008(平成20)年6月11日発行)より)
この記事が気に入ったらサポートをしてみませんか?