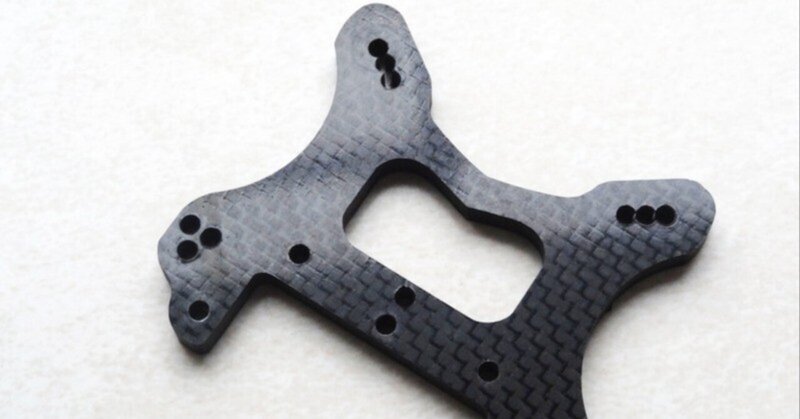
炭素繊維とその複合材の必要性、そしてDX・GXの活用について
最近、炭素繊維やその複合材のリサイクルに関する問い合わせが増えてきています。金属と比較して軽量で高強度である炭素繊維複合材は、産業界で必要とされています。
炭素繊維複合材について詳しく説明すると同時に、大量生産化に向けて製造プロセスにもイノベーションを起こさなければいけませんし、DXやGXも積極的に取り入れていく必要に迫られてきています。
今回は、このような流れをまとめてみました。
1.炭素繊維及び複合材料の歴史
1)炭素繊維の発展
初期の開発:炭素繊維は1950年代及び1960年代に初めて開発され、イギリス王立航空機研究所やユニオンカーバイドコーポレーションによって大きな進歩が見られました。
商業化:1970年代には、東レ、三菱、Hexcel 等の企業が主に航空宇宙用途向けに商業生産を開始しました。
進展:数十年にわたり、製造技術の向上や様々なグレードの炭素繊維の開発により、その用途は自動車、スポーツ用品、風力発電等に拡大しています。
2)複合材料
進化:炭素繊維強化複合材料は、特に高い強度対重量比を提供するため、ハイパフォーマンス用途に理想的です。
革新:樹脂システム、製造技術、ハイブリッド複合材料の継続的な革新により、その特性と用途がさらに向上しています。
3.炭素繊維複合材の特徴
1)素材面
高強度・軽量性
高強度:炭素繊維は非常に高い引っ張り強度を持ち、従来の金属材料と比較して強度が高いため、耐久性の高い構造物に利用されます。
軽量:炭素繊維は重量が軽く、強度に対しての重量比が優れているため、自動車や航空機の重量を減らすことができ、燃費効率の向上に寄与します。
耐熱性・耐腐食性
耐熱性:炭素繊維は高温環境でもその性能を維持することができ、エンジン部品や航空機の高温部分に適しています。
耐腐食性:炭素繊維は化学的に安定しており、腐食に強いため、過酷な環境条件下でも使用が可能です。
2)設計面
設計の自由度
複雑な形状の設計:炭素繊維は織り方や積層方法によって、複雑な形状や特定の強度特性を持つ部品を設計することができます。
カスタマイズ性:素材の特性を細かく調整できるため、特定の用途や機能に合わせたカスタム設計が可能です。
剛性と振動特性
高剛性:炭素繊維は高い剛性を持ち、形状の安定性が求められる部品に適しています。
振動特性:優れた振動減衰特性を持ち、精密機械やスポーツ用品のパフォーマンス向上に貢献します。
3)製造面
製造プロセスの多様性
様々な製造技術:炭素繊維はフィラメントワインディング、プリプレグ、レジンインフュージョンなど、多様な製造技術を活用することができ、製品の特性や製造コストに応じた選択が可能です。
短納期:一部の製造プロセス(例えば、オートクレーブ成形など)は比較的短い製造サイクルを持ち、大量生産が求められる用途にも適応できます。
自動化の容易さ
自動化技術との親和性:炭素繊維の製造は、自動化技術と高い親和性を持ち、ロボットを用いた精密な製造プロセスが可能です。これにより、一貫性のある高品質な製品の大量生産が可能となります。
4)環境面
燃費効率の向上
軽量化による燃費向上:自動車や航空機に炭素繊維を使用することで、重量が軽減され、燃費効率が向上し、二酸化炭素(CO2)排出量が削減されます。
5)耐久性と長寿命
長寿命:炭素繊維製品は耐久性が高く、寿命が長いため、製品のライフサイクル全体での環境負荷を低減できます。
メンテナンスの削減:耐腐食性や耐熱性により、メンテナンス頻度が低減され、長期的なコスト削減と環境負荷の低減に寄与します。
6)リサイクルとサステナビリティ
リサイクル技術の進展:炭素繊維のリサイクル技術が進展することで、使用後の材料を再利用し、資源の有効活用と環境保護に貢献します。
持続可能な材料開発:バイオベースの炭素繊維など、環境に優しい素材の開発が進んでおり、将来的にはさらにサステナブルな産業が期待されます。
4.製造プロセスの革新と課題
1)技術的な課題と解決策
プリカーサー製造:
課題:炭素繊維の製造は、プリカーサー(通常はポリアクリロニトリル-PAN)から始まります。高品質なプリカーサーのコストと効率が課題です。
解決策:低コストのPAN、リグニン、ポリエチレン等のプリカーサー材料の革新によりコスト削減が可能です。スピニング技術の向上やプリカーサーの安定化方法も重要です。
炭化:
課題:プリカーサーを炭素繊維に変換する炭化プロセスはエネルギー集約的であり、品質を維持するために正確な制御が必要です。
解決策:マイクロ波アシストプラズマ炭化等の炉技術の進歩により、効率が向上しエネルギー消費が削減されます。温度と張力の自動制御により一貫した品質を保証します。
表面処理:
課題:炭素繊維と樹脂マトリックスを結合するための表面処理が重要です。不均一な処理は弱い複合材料につながります。
解決策:自動化された高スループットの表面処理プロセスにより一貫性が向上します。プラズマ処理や高度な化学コーティングが繊維-マトリックスの接着を強化します。
複合材料の製造:
課題:複合材料の製造にはレイアップ、硬化、仕上げプロセスが含まれ、これらは手間と時間がかかります。
解決策:レイアップ及び硬化プロセスの自動化及びロボット化により、生産速度と一貫性が大幅に向上します。樹脂トランスファーモールディング(RTM)やアウトオブオートクレーブ(OOA)硬化法等の技術が製造を効率化します。
品質管理:
課題:大量生産において高品質を維持するのは、材料やプロセスの変動のため難しいです。
解決策:AI及び機械学習を用いた高度な検査及び品質管理システムを導入することで、欠陥を早期に予測及び検出できます。デジタルツインを用いてリアルタイムで製造プロセスをシミュレート及び最適化します。
2)期待される技術革新
高速生産:高速巻き取り及び表面処理技術の革新は、今後5〜10年以内に期待されます。
自動化:AIを統合した完全自動化生産ラインは、10〜15年以内に主流となる可能性があります。
持続可能な材料:環境規制や持続可能性目標により、今後10年間でバイオベースのプリカーサー及びリサイクル技術の開発が進むでしょう。
5.DXとAIの関わり方
1)製造プロセスの最適化
リアルタイムモニタリング:センサーとIoT技術を使用して、製造プロセスの各ステップをリアルタイムでモニタリングします。データをAIで解析することで、異常を早期に検出し、品質の一貫性を保つことができます。
プロセスシミュレーション:デジタルツイン技術を使用して、製造プロセスの仮想モデルを作成し、シミュレーションを行います。これにより、最適な製造条件を見つけ出し、効率を向上させることができます。
2)設計の高度化
ジェネレーティブデザイン:AIを利用して、複雑な形状や構造を自動生成するジェネレーティブデザインを実施します。これにより、従来の設計では不可能だった高性能な部品の開発が可能になります。
材料設計:AIを用いて、新しい複合材料の特性を予測し、最適な材料組成を提案します。これにより、実験回数を減らし、迅速に新材料を開発できます。
3)品質管理と検査
自動検査:AIを搭載した視覚検査システムを利用して、製品の欠陥や異常を自動的に検出します。これにより、人的ミスを減らし、品質保証が向上します。
予防保全:機械学習モデルを使用して、設備の故障予測を行い、予防保全を実施します。これにより、ダウンタイムを最小限に抑え、製造効率を向上させます。
6.グリーントランスフォーメーション(GX)の推進
1)主要な投資分野
持続可能な材料:
焦点:環境影響を低減するためのバイオベースのプリカーサー及び樹脂の開発。
理由:バイオベースの材料はカーボンフットプリントを低減し、石油ベースのプリカーサーに代わる持続可能な代替品を提供します。
投資規模:世界的に数億ドル規模のR&D投資が見込まれます。
リサイクル技術:
焦点:炭素繊維複合材料のライフサイクル終盤の処理を効率的に行うリサイクル技術の進歩。
理由:効率的なリサイクルにより、埋め立て廃棄物が削減され、貴重な材料が回収されることでライフサイクル全体のCO2排出量が低減されます。
投資規模:効率的なリサイクルプロセス及びインフラストラクチャの開発には、数千万ドルから数億ドルの投資が必要です。
エネルギー効率:
焦点:炭化やその他の製造プロセスのエネルギー効率を向上させる。
理由:エネルギー消費を削減することで、カーボンフットプリントと運用コストが直接削減されます。
投資規模:製造施設におけるエネルギー効率プロジェクトには、数百万ドルから数千万ドルの投資が見込まれます。
ライフサイクル分析及び最適化:
焦点:製造から廃棄までの環境影響を最適化するための包括的なライフサイクル分析ツールの導入。
理由:ライフサイクル全体を理解し最適化することで、改善及び革新の余地が特定されます。
投資規模:ライフサイクル分析ツールの開発及び統合には、数百万ドル規模の投資が必要です。
7.現在の導入例
1)製造プロセスの革新
東レ:東レは、高性能炭素繊維の製造において、省エネルギー炭化や高度な表面処理等の最適化技術を先導しています。
Hexcel :Hexcel は、先進的なRTMプロセス及びOOA硬化法を含む、自動化された複合材料製造技術に投資しています。
2)DXとAI導入
ボーイングの航空機製造(リアルタイムデータ解析):ボーイングは炭素繊維複合材料の製造において、製造ライン全体にセンサーを配置し、リアルタイムでデータを収集しています。AIを使用してデータを解析し、製造プロセスの最適化と品質管理を行っています。
トヨタ自動車の複合材料部品製造(ジェネレーティブデザイン):トヨタはAIを利用して、車両部品の軽量化を目指したジェネレーティブデザインを行っています。これにより、炭素繊維複合材料を使用した新しい部品設計を迅速に進めています。
東レの材料開発(材料設計):東レはAIを活用して新しい炭素繊維複合材料の特性予測を行い、効率的に新材料を開発しています。AIによるシミュレーション結果を基に、実際の試作回数を減らし、開発期間を短縮しています。
Hexcel の製造プロセス自動化(自動化システム):Hexcel は製造プロセスにAIを組み込んだ自動化システムを導入しています。これにより、複合材料のレイアップおよび硬化プロセスを自動化し、一貫した高品質の製品を効率的に生産しています。
三菱ケミカルの品質管理(視覚検査システム):三菱ケミカルは、AIを搭載した視覚検査システムを導入し、炭素繊維複合材料の製品検査を自動化しています。これにより、欠陥検出の精度とスピードが向上し、品質保証のレベルが高まっています。
3)グリーントランスフォーメーションの取り組み
バイオベースのプリカーサー:東レの子会社であるゾルテック等の企業が、リグニンベースのプリカーサーを持続可能な代替品として探求しています。
リサイクルプログラム:欧州連合のRECYCLEプロジェクトは、炭素繊維複合材料の効率的なリサイクル技術の開発に焦点を当て、実行可能なリサイクルインフラストラクチャの確立を目指しています。
8.投資動向
持続可能なファンド:大手企業や投資ファンドは、持続可能な材料及び技術にますますリソースを投入しています。例えば、三菱ケミカルは、環境に優しい複合材料の開発に大規模な投資を発表しました。
9.結論
炭素繊維及び複合材料産業は、製造プロセスの革新及びグリーントランスフォーメーションへの強い焦点を通じて、著しい進歩を遂げることが期待されています。技術的な課題に取り組み、持続可能な実践に投資することで、業界は大量生産、コスト削減、環境影響の低減を達成し、2050年のカーボンニュートラルという世界的な目標に沿うことができます。
この記事が気に入ったらサポートをしてみませんか?