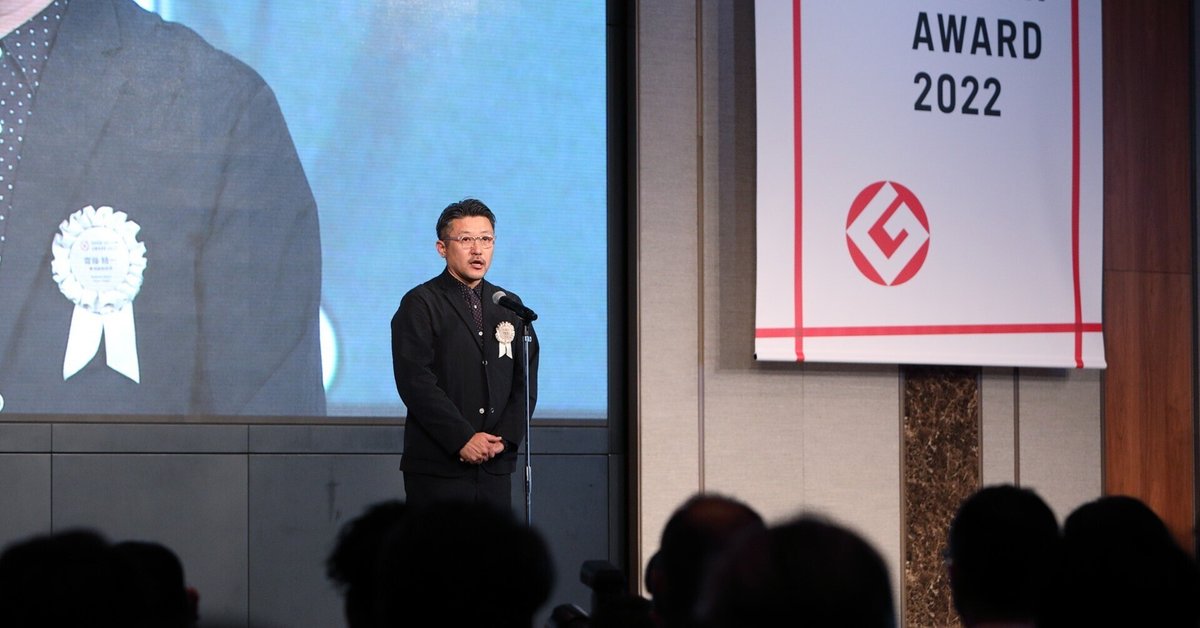
To break away from scrap & build type event settings Seiichi Saito explains the essence of creating “good” and beautiful events
The GOOD DESIGN EXHIBITION 2022 was held from Friday, October 7 to Sunday, November 6. Under the theme of “Change for Good.” we strived to make the exhibition itself even “better” in addition to displaying award-winning works. (The details of actual products can be seen here.) In this article, Seiichi Saito, General Director of the GOOD DESIGN EXHIBITION 2022, revises the tracks of revisiting the event from the perspective of environmental impact.
“Why are we causing a lot of waste to hold an event that lasts for only a few hours?”
When was appointed the General Director of The GOOD DESIGN EXHIBITION 2022, I considered it an opportunity to answer my long-standing question.
I have been involved in many events so far, but I always felt something was off while being in charge of the process from construction to management. Are we doing alright? There must be a better way for society and the earth to organize events.
The theme of this exhibition, “Change for Good.” carries this thought of mine that I have had for a long time.
I believe what changes the norm in the industry is one “precedent.” “We can hold events that are environmentally friendly by using our ingenuity.” If we can prove this, the people next in line would think “We can do the same.” To this end, I wanted to create a successful case in the GOOD DESIGN EXHIBITION.
This article reviews this year’s exhibition and describes the essence of “good” events. I hope that those who are next in line will copy it as they read this article.
Establish a precedent for “good” events and promote bottom-up social changes
What is “good” manufacturing for society and the earth?
In 2022, we are facing the need to reconsider the way things are and the processes by which things are manufactured, including the supply chain, materials, and disposal and reuse after use.
Sustainability, SDGs, and the circular economy...... A code of conduct that addresses urgent global issues is being discussed as a matter of course in the areas of products and fashion that involve “items.” The Good Design Award, which screens the front lines of such items, should follow this movement, or I should say the Good Design Award have to lead the standard of “good” manufacturing.
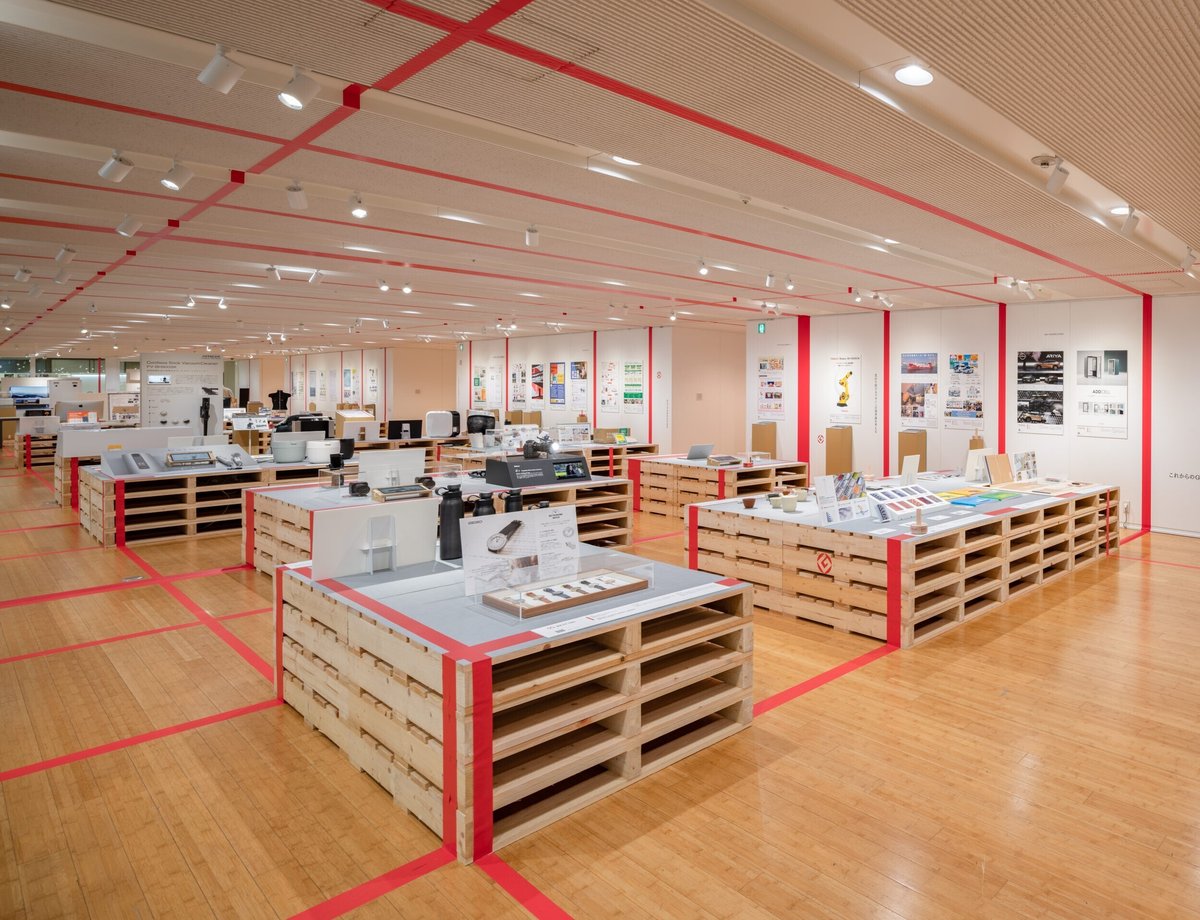
In order to achieve this goal, top creators in various domains, such as graphics, spatial design, and materials, were invited to join the team for the 2022 exhibition. We had copywriter/creative director Toshiyuki Konishi as Concept Director, graphic designer Yoshiaki Irobe as Art Director, architect Yuko Nagayama as Spatial Director, and product designer Jin Kuramoto as Material Director.
The Dream Team strived to make an event based on the concept of “Change for Good.” that produces as little waste as possible.
Most fixtures were composed of reusable pallets rather than newly making pallets. Instead of covering walls with fancy interior materials, a simple technique looping red ribbon tapes around the room was adopted to create a design that can be recognized as an exhibition of the Good Design Award. Thanks to efforts like this, we managed to drastically reduce the amount of post-exhibition waste such as surface materials.
We thoroughly stuck to using used materials even for the Good Design Award celebration ceremony which is the grand highlight of the event. The main panel (photocall panel), which is approximately 15 meters long, is often used as a background for commemorative photographs. Its surface is also composed of reused panels. By applying only red tapes on the bare reused panels showing the trace of previous users, we utilized the texture of the materials and expressed a design unique to the Good Design Award.
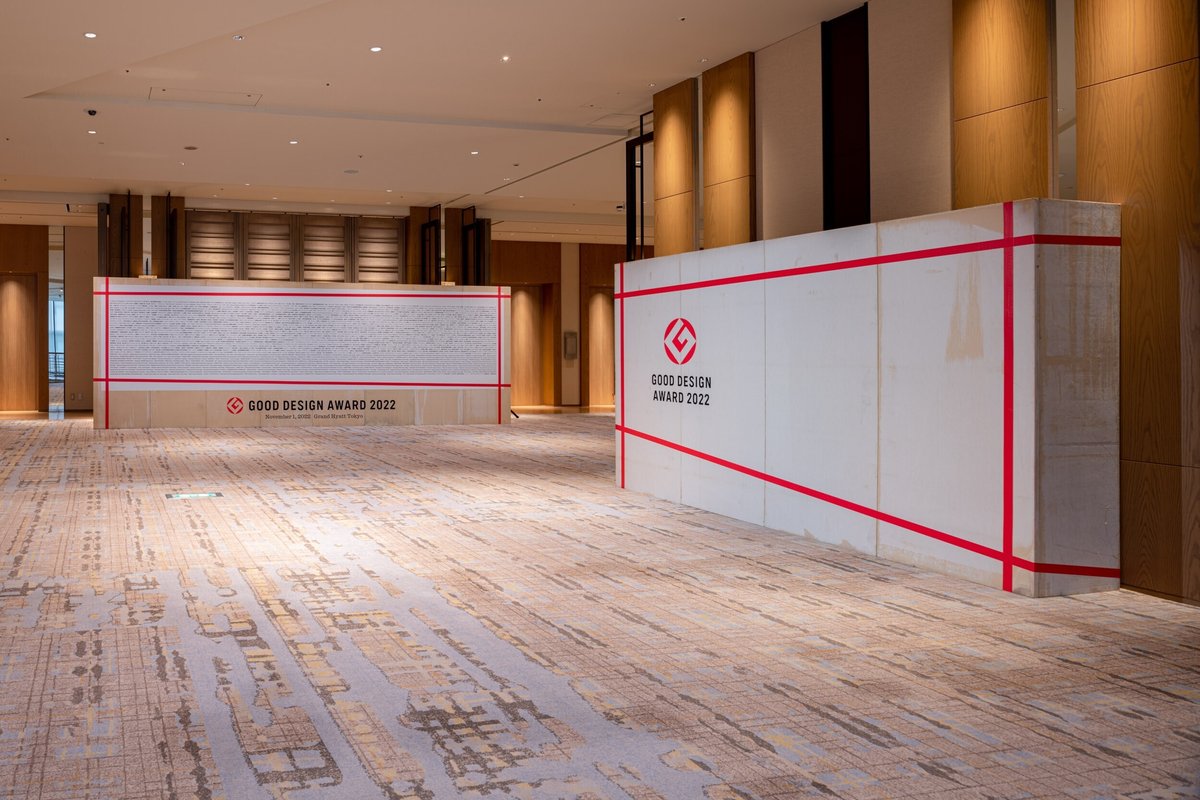
There was an opinion complaining “It has gone overboard” about our using reused materials for the main panel which was the center of the celebration ceremony and had all the names of award winning companies on it. However, I wanted to stick to “Change for Good.” from the beginning to the end.
More than 700 people gathered here, and most of them are involved in manufacturing in some way. That’s why I thought that if these people could experience manufacturing that is “good” for society and the earth and get inspiration, it would have a great impact.
This is my personal opinion, but I think there are roughly two ways to carry out “Change for Good.” One is to make top-down changes from the government and laws. Another way is to increase the understanding of people involved in manufacturing decisions and to change their minds, so that the information can be spread from the field level in a bottom-up manner.
This year, I am approaching the latter with the help of the “public good” called the Good Design Award. I want makers to take the lead in choosing “good” measures. For this reason, I wanted to demonstrate the way “change” should be by myself.
Three points for designing “good” events
Through this exhibition, I learned three things that are important for creating a “good” event. I will explain the how-to below.
(1) Appointing a material director
The first is to appoint a person in charge of “materials.”
In order to break away from the conventional “scrap & build” type of exhibitions in which materials are gathered for an exhibition and then disposed of after completion, it is important to identify appropriate materials that can be recycled or reused.
For example, there are several methods to recycle plastic, such as “thermal recycling” where waste is incinerated to extract heat, and the “Cradle to Cradle,” which is a circulating product design where plastic is reshaped and recycled. Furthermore, there are various types of plastics, including polycarbonate, polystyrene, and ABS resin
This is why a “material director” who evaluates selection and use of materials plays an important role.
In preparation of this year’s exhibition, Material Director Kuramoto took the central role in decision making on attention to the environment. For example, he decided to use Refinverse, Inc.’s recycled nylon resin “REAMIDE®” which is made from fishing nets to make the chest emblem (rosette) to be used at the awards ceremony. In addition to using materials with low environmental impact, he also examined the recycling of materials and fixtures to be turned into something different after use.
This position is not commonly prepared, but I think material director is an essential position to create “good” events.
(2) Designing based on “resemblance”
The second is to think of designs based on “resemblance.”
Recycled and reused materials have the drawback that as they keep being reused, they may become brown or black in color or look dirty and cheap. However, in creating a “special occasion,” it is essential to produce a gorgeous space.
However, if you form an object with a large surface, you have to consume energy and resources by painting and printing. This time, we adopted a strategy of making the most of “resemblance” based on the policy of “Achieving the maximum impact with the minimum elements.”
Specifically, Art Director Irobe proposed a design focused on “red” lines, which is the key color of this award, so that it would be instantly recognized as a special stage for the Good Design Award. As a result, we believe that we have achieved visual development that fully expresses the Good Design Award.
(3) Design with the “ending” in mind
The third is to making things with their endings in mind.
I have an impression that many modern manufacturing processes do not consider the “ending.” For example, most of us have no idea how to disassemble a broken computer. However, there is the need for future designs to simplify the structures so that anyone can disassemble them to fix or dispose of them with small environmental impacts.
In this year’s exhibition, we promoted the design while thinking about the “ending.”
Selecting materials and designing while taking account of where the materials will end up at. The selection and construction of materials and fixtures are carried out while considering how to clean up...... This event has been accomplished as a result of a series of examinations on the "ending.”
Based on “team building” with team members and clients
Nonetheless, just practicing these three points is not enough. No matter how well we prepare ourselves, “Change for Good.” will not be achieved unless we are able to work as a team in the first place.
As in the past, if each department of space, graphic, and other elements focuses only on its own domain, a lot of waste will be produced. We have to go into each other’s domains and discuss. For this to happen, trust and common understanding among team members is essential.
For instance, the design with the red tape proposed by Irobe influenced not only the graphics but also the direction of the entire space of which Nagayama was in charge. Besides, Nagayama did not only think about space, but also what materials should be used there. In fact, even if no one asked them to do so, Irobe and Nagayama had each been studying “tapes,” and at the meetings, they deepened their studies based on their findings.
It is important to be able to discuss the best way for both sides while penetrating into each other’s domains.
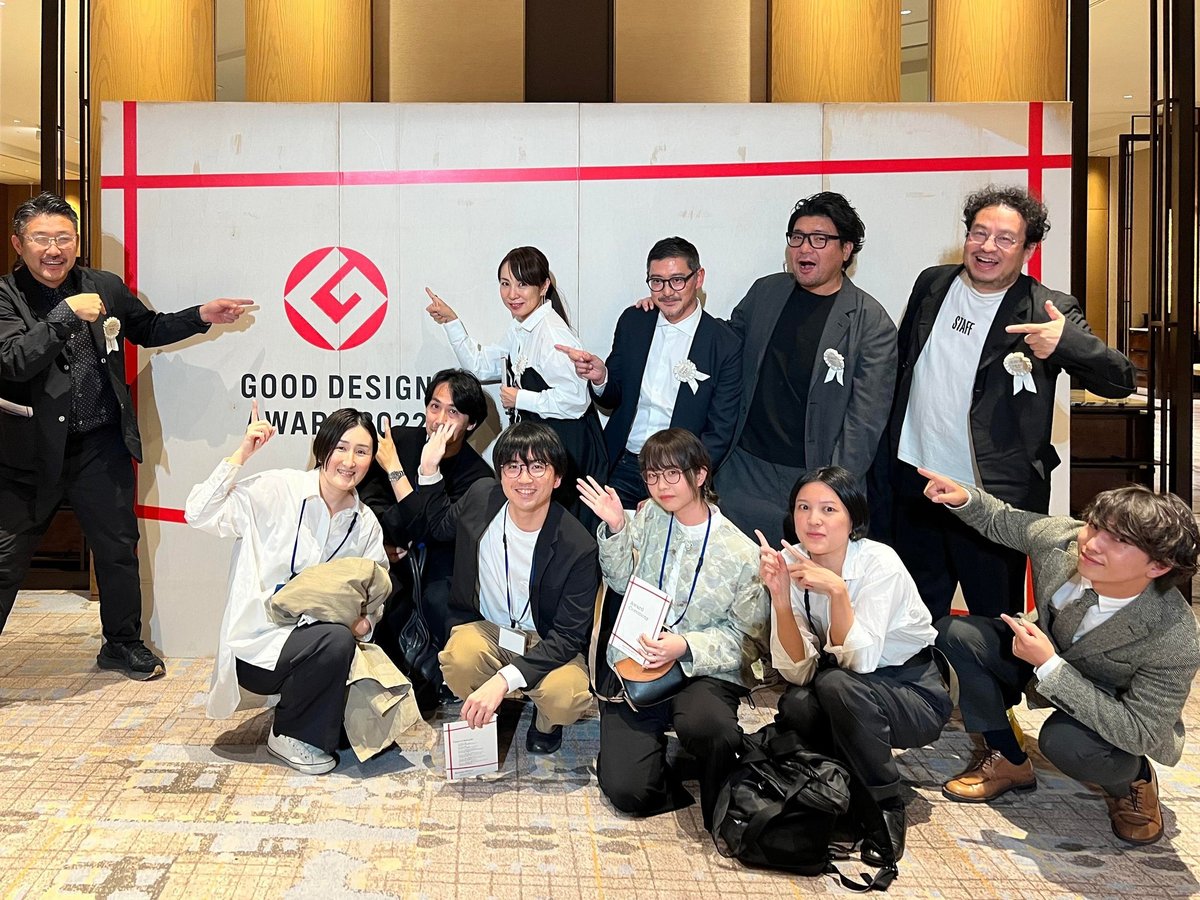
Moreover, it is also important to have a trustful relationship with the client who places an order.
The biggest fortune for us this time was that the Japan Institute of Design Promotion (JDP), the organizer of the Good Design Awards, expressed understanding for what we wanted to do. If the creative team and the client do not work together, it will be hard to make a “good” effort.
For example, the JDP once opposed use of reused panels at a celebration ceremony. The Grand Award Selection and the celebration ceremony is a “special occasion,” and therefore they wanted to make at least this one properly.
Of course I understood what they said, and I even agreed with them at the beginning. However, little by little, I started thinking “Something doesn’t sit right with it.” Then I had an adequate number of discussions with the JDP like “What kind of condition is ‘proper’?”, “If it is covered with white wall papers, can it be called proper?”....... As a result, we could finally have approval from them and decided to use reused panels.
Having had a client like the JDP who sincerely listened to us and discussed with us, and having established trusting relationships in the entire creative team greatly contributed to the success of this exhibition.
When it comes to commissioned manufacturing, clients often say, “I’ll leave it to a professional designer.” However, we also have a request saying “Let’s not do this” frequently from them in the process of manufacturing. This is where the relationship of mutual trust between a client and a designer is tested.
A “good” design can only be realized when the production team and the client, the decision maker of the product, are united.
Summary: A sense of balance between “beauty” and “good”
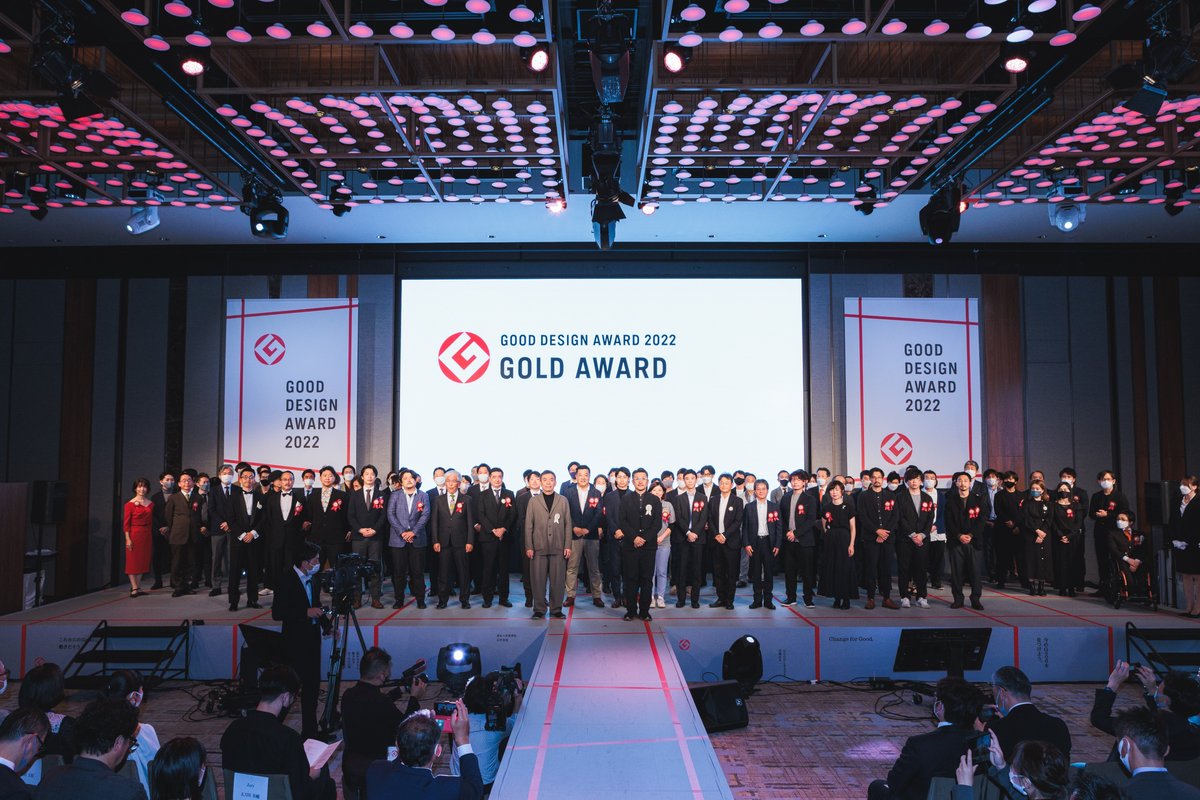
“Everything is in harmony with no discomfort.” ── When I saw the completed form of the exhibition, I felt so happy.
In other words, it means “no one notices.” There is no self-assertion that “we used recycled materials” and therefore no one would even mention it. I think things should be this way, everyone realized later on and said “Oh, was almost everything there really made of recycled or reused materials?”
I believe that the use of reused panels at this year’s exhibition turned out successful because it was “beautiful.”
It was in perfect harmony without being overshadowed by the fancy ambience of the exhibition site or badly standing out because of the texture of reused materials.
What is important is a balance between the “accelerator” of beauty and the “brake” of environmental impact.
If we focus only on recycling or reusing, the selection of materials and the extent of expression and design will be limited. It is like slowing down by putting on the brakes too strongly.
We will continue to seek the optimal “good” that is environmentally friendly without sacrificing beauty. I think that is the most important thing.
Of course, I’m not presumptuous enough to say that “I’ve found the ultimate answer.”
I want to reduce waste more thoroughly from next year on, and to establish a system of who wishes to take them so that we can give out all the materials until the last single sheet of plywood.
More to the point, we believe that not only physical materials but also the relationships of the people involved can be made more sustainable. We recently launched a Discord community for judges and award winners. Instead of posting information about good design on SNS like fireworks, we want to nurture a relaxed community centered on enthusiastic people who are involved in manufacturing. This year, we started an experimental attempt to see if we could build such a place.
So far, we have released “recipes” that we have tried and failed through the award exhibitions to the public. With a precedent and instructions, you will not have to reinvent the wheel. Please try it and you can chalk it up to me, “Saito has done it so we can do it too.”
I wish that the precedent that I left will lead to a long-lasting stream of “Change for Good.”