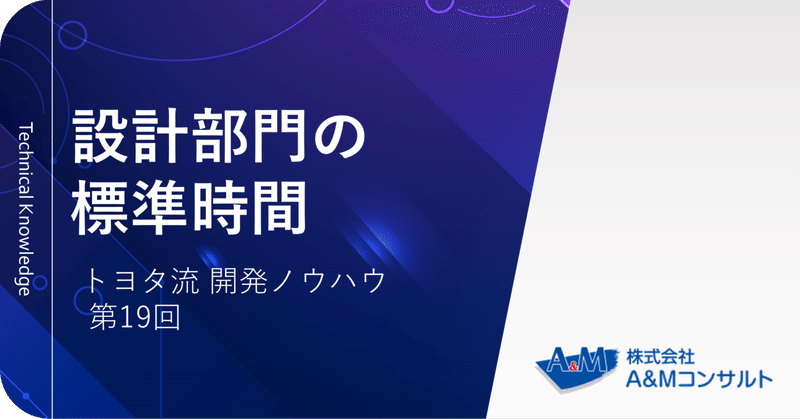
設計部門の標準時間|トヨタ流開発ノウハウ 第19回
■設計の標準時間
突然ですが、皆さんの設計部門に「設計の標準時間」は存在しますか?
私は、様々な製造業の企業様でコンサルタントとして支援をさせていただいておりますが、コンサルタントに転職して約10年間、設計部門内での「設計の標準時間」を聞いたことがありません。
設計の標準時間と言えば、製造部門の1つ1つの作業に対して標準時間が設けられ、その標準時間通りに生産していかなくてはなりません。
例えば自動車メーカーの完成品組立ラインは、流れてくる車体に対して、ある一定の距離が流れるまでに組付けを終了しなければならない、まさに標準時間が設けられており、その時間通りに生産することで1日の生産量が明確に把握できます。
また、モノが流れていないラインであっても、標準時間が設定されており、その標準時間通りに生産していく。
標準時間の定義は、標準時間よりも遅く終わってはいけないことはもちろんのこと、早く終わってもいけません。
早く終わってしまうと、他の生産工程と連動が取れなくなり、ある一部の工程で仕掛在庫が増加してしまいます。
そのような場合には、全体のライン構成を見直すことはもちろんですが、標準時間通りに生産できない理由を明確にしながら、作業改善を行っていかなければなりません。
私は前職の自動車メーカーで、「標準の無いところに改善はない!」と言われ続けてきました。
前述のように標準時間を設定していなければ、生産が遅いか速いかも分からず、仕掛在庫が溜まっている理由もわからなくなってしまいます。
まずは作業手順を明確にし、その作業手順で生産した場合の標準時間を設定していく必要があります。
これは製造改善や製造ライン構築の時には必ず実施することであり、当たり前のことです。
■設計部門と製造部門の作業手順設定
ここで話を元に戻しますが、製造部門では実施されている標準時間や標準作業手順の設定を、なぜ設計部門では実施しないのでしょうか?
さまざまな業種の設計者にヒアリングをすると、決まって次のような答えが返ってきます。
「製造部門のように毎回、同じ設計方法を取るわけではない」
「顧客要求が様々であるため、その要求を予測して標準時間なんて設定できない」
「仮に設定したとしても、その時間通りには設計できない」
「設計は創造的な仕事であるため、時間制約を設けるべきではない」
などです。
私も設計者であったときはそのように考えていました。
「どうせ標準時間内に設計なんてできるわけがないから、適当に計画日程を設定しておこう」と。
ですが、実際実施している設計業務は、本当に標準時間を設定できないのでしょうか?
標準時間が設定できていないのに、出図の日程はどのように決めているのでしょう?
多くの企業は、出荷日程から製造部門のリードタイムを引いた日程が出図日程になっていることが多いのではないでしょうか?
では、その日程で本当に設計可能かどうか、誰が判断していますか?
答えは「誰も判断していない。」です。
その日程で実施しなければならない!と半ば強制的に日程が設定され、出来もしない計画が立案されます。
その結果、出図が遅れ、他の部門から「設計部門はいつも仕事が遅い」「設計部門だけ期限を守らなくても文句を言われない」など、設計部門を責める言葉が投げかけられます。
前述の状態にならないためには、設計者が設計するための標準時間を設定し、様々な案件を標準時間通りに設計をしたとしたら、何日必要などを他の部門に明確に伝えなければなりません(製造部門は実施していること)。
標準時間の必要性を理解してもらったら、次にどのように標準時間を設定するかを検討します。
標準時間設定のための1番重要な考え方は、設計手順であると考えます。
この設計手順が明確になっていない企業様がとても多く感じます。
設計手順とは、どのように設計していくかを設定したもので、設計者毎に設計の方法が異なる状態をつくらないことです。
設計者毎に異なる手順で設計しているから、設計するための時間のバラツキが発生してしまうのです。
そうならないためにも、次のような設計手順を設定しましょう。
■設計手順の具体的作成方法
①製品仕様を設定する。【〇〇工数】
ツール:仕様モジュール
②変化点を抽出する。【〇〇工数】
ツール:変化点管理
③変化点に対しての問題を抽出する。【〇〇工数】
ツール:DRBFM
③全体レイアウトを検討する(基本設計)【〇〇工数】。
ツール:3DCAD+干渉チェックポイント
④新規ユニットのレイアウト制約条件を抽出する。【〇〇工数】
ツール:新規部品設計表
このような設計手順となります。
・各手順に対して、標準時間(工数)を設定する。
・この標準時間は、製品難易度や設計者レベルによって、変わる可能性があるため、重みづけを実施しなければならない。
・製品難易度が高い場合は、全ての標準時間を1.2倍にする、などである。
量産設計は確かに創造的な業務内容であることに違いありませんが、研究開発とは異なり、時間的制約の中で最も高いアウトプットを出す業務です。
ある一定以上のスキルを持った設計者であれば、同じアウトプットが出せるよう設計手順を設定してみてほしいと思います。
設計手順に従って設計しない設計者は、単なる設計者のエゴで業務を遂行しているに過ぎません。
そのような設計者のエゴでは、良い製品は生み出せないと私は考えます。
講師プロフィール
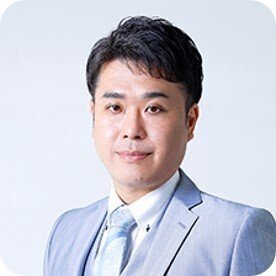
中山 聡史 |株式会社A&Mコンサルト 取締役専務 経営コンサルタント
2003年、関西大学 機械システム工学科卒、トヨタ自動車においてエンジン設計、開発、品質管理、環境対応業務等に従事。ほぼ全てのエンジンシステムに関わり、海外でのエンジン走行テストも経験。2011年、株式会社A&Mコンサルトに入社。製造業を中心に自動車メーカーの問題解決の考え方を指導。2015年、同社取締役に就任
主なコンサルティングテーマ
設計業務改善/生産管理・製造仕組改善/品質改善/売上拡大活動/財務・資金繰り
主なセミナーテーマ
トヨタ流改善研修/トヨタ流未然防止活動研修/開発リードタイム短縮の為の設計、製造改善など
※2023年9月現在の情報です
近著
この記事が気に入ったらサポートをしてみませんか?