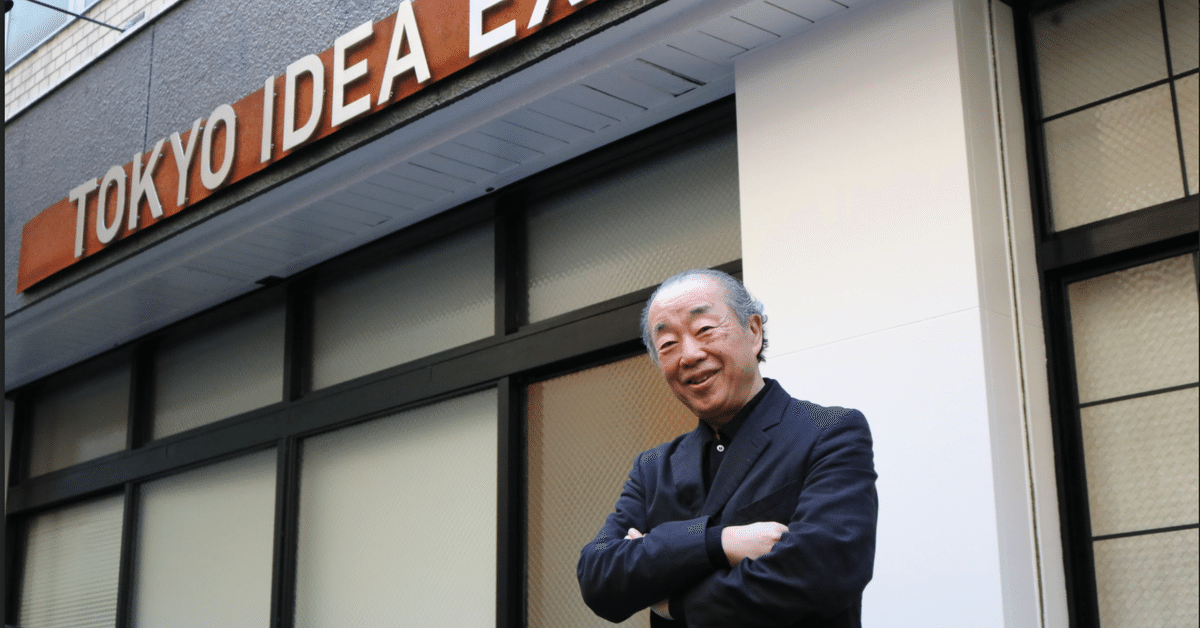
プロセステクノロジーが、あらゆる業界の生産性を高める
こんにちは、リバネス製造開発事業部の藤田大悟です。今回は、ベンチャー企業の皆さんの「製造プロセス」を考える上で、とてもヒントとなる「プロセステクノロジー」に関して、リバネスが発刊している経営者・新規事業の方向けに発刊している『創業応援』に掲載した記事をnoteでもご紹介させていただきます。
今回紹介させていただく方は、20年前、金型製造プロセスの徹底的な分析とそれを元にした管制システムの構築で、業界の革新を生んだ株式会社インクス創業者 山田眞次郎氏です。彼が生み出したプロセステクノロジーを応用して、自動車製造や植物工場、医療現場など、あらゆるプロセスを科学してきた真髄について、藤田大悟が対談した内容を紹介させていただきます。
熟練工100名の業務をバイト2名で行えるようにした脅威的なテクノロジー
藤田:本日はよろしくお願いします。12年越しの取材ですね。リバネスでは2020年に製造開発事業部を発足し、以前取材した当時は想像していなかった、ベンチャーや大手企業の製造の支援もするようになりました。より深い議論ができることを楽しみにしています。
山田:あれから12年で色々な変化がありましたが、変化の時代の中で、ビジネスの世界で再び相まみえて嬉しく思います。
藤田:インクス社の事業が業界に与えたインパクトは今見ても際立っていますね。
山田:1990年当時、株式会社インクスを創業し、金型の熟練工が行っている製造プロセスを徹底的に分析して、プロセスにおける暗黙知の明文化と人の判断をシステムへ実装することで、作業の効率化、工程の最適化を実現し、属人的な要素を削減しました。
藤田:通常45日かかる金型の設計から製造までを45時間にまで短縮したと10年前に伺った時は、本当に驚きました。
山田:金型製造のプロセスを徹底的に明文化し、効率化とシステム化した結果、熟練工100名で行うプロセスをアルバイト2名でもできるようになったことが大きいですね。この考えを「プロセステクノロジー」と定義し、自動車業界や家電業界など様々な製造プロセスの短縮に携わらせてもらいました。
写真:12年ぶりに対談する山田氏と藤田
本当に熟練者にしかできない判断はたったの3%
藤田:馴染みのない言葉ですが、プロセステクノロジーとはどのような技術なのですか。
山田:プロセステクノロジーは、プロセステクノロジーでは、例え一瞬でも人間が脳内で判断を下すプロセスを「1Process-1Decision」という最小単位で定義しました。その1Processの連鎖を構造的に整理し、業務フローと支援システムに落とし込むことで、属人的な要素を一切削ぎ落とし、効率化を計る技術です。
やることは至極シンプルで、担当者へのヒアリングや観察から、どのような情報を元に、どうやって判断し、どのように判断結果をアウトプットするのか、などを下記の図の5つのステップで明文化します。例えば、機械のボタンを押すにあたって何か判断していれば、それが1プロセスです。ボタンを今押すべきか否かを判断するために、機械の表示灯は何色か、材料が問題なくセットされているか、異音はしていないか、などの項目を確認していたら、それが「判断項目」。その判断項目を元に、赤なら危険、青なら問題なしなど、良し悪しを決める「判断基準」、判断はどのような順番でされるのかという「思考手順」、危険だから機械を止める、など思考した結果どのような情報が脳内でアウトプットされるのかという「判断アウトプット」を可視化します。そして、それらの判断結果がどのような言葉や情報として伝達されるのかという「アウトプット伝達方法」、そのツールは紙なのか、システムなのかという「伝達ツール」を明らかにしてくことで、やっと1プロセスが見えるのです。これを徹底的に全ての工程で行い、本人すら無意識で気がつかなかったプロセスを丸裸にして、誰にでも扱えるものにしていくのです。
藤田:誰にでも扱えるようにと言っても慣れた人にしかできない判断もあるのではないですか。
山田:金型製造の例で言えば、熟練工の思考プロセスを徹底的に明らかにして、仕組み化したところ、熟練者にしかできないことはたったの3%だけしかありませんでした。実は勘やコツでやっているものも無意識を明らかにするとほとんどが誰にでもできることである事実を理解することがとても重要です。
図:脳内のプロセスを明文化するプロセス
製造の智恵は植物工場やガン治療、あらゆる技術開発のプロセスにメスを入れられる
藤田:現在、株式会社プランテックスにて植物工場の自動化を行っているということですが、なぜ製造業ではなく、農業に取り組まれているのでしょうか。
山田:植物工場に取り組む方のお話をたまたま聞く機会があり、聞くところによると、植物工場は、基本的に赤字が当たり前で、日々コスト削減に追われていると伺いました。植物工場の仕組みを聞いて素人ながらに思ったのは、植物の光合成の仕組みなどをしっかり理解して、条件を適切にコントロールすればうまくいくのではないか、コスト削減に走る前にそもそものプロセスの整理が必要なのではないかと考えました。
藤田:人の思考プロセスと植物の成長プロセスは同じということですか。
山田:もちろんプロセス自体は全く異なります。しかし、過去の植物成長に関する知見を結集すれば実現できると考え、植物工場での成長プロセスに関する査読論文300本以上を徹底的に読んで、知見を整理し、植物成長のプロセスを数式チェーンで繋げることで、自動制御の完全閉鎖型人工光型植物工場を完成させました。
写真:応用先の1つとして開発された植物工場
藤田:そこまで徹底的に取り組む山田さんの原動力はどこから来るのでしょうか。
山田:私は、効率の悪いことが本当に嫌いなんです。どんなことでも効率化したいので、私は朝布団から起き上がり、電車に乗り、オフィスの机に座るまでのプロセスを徹底的に明らかにして、その判断項目や判断基準、思考手順を最適化するように努めています。それが故に、妻から急に頼み事をされてしまうと完全にリズムを狂わされてしまうのですがね(笑)。
藤田:私も是非取り入れたいのですが、今日からできる一歩はなにかありますか?
山田:先ほどの朝の工程分析は、簡単に見えますが、この分析方法を体験することで、プロセステクノロジーの本質を理解することができます。私はこの方法で、日本の自動車や電機メーカーなど大企業約80社のあらゆる工程を1/2以下にした経験があり、製造業だけでなく運輸や製薬、ガン治療などでも、最適化していけると確信しています。ぜひ皆さんも、私生活での思考実験でプロセステクノロジーを磨き、世の課題解決に取り組んでもらえればと思います。そして、空いた時間で、ぼーっとしながら未来に想いを巡らせられると良いですね。(文・内山 啓文)
【参考リンク】
株式会社プランテックス
ENGINEERS UNITED SOCIETY
この記事が気に入ったらサポートをしてみませんか?