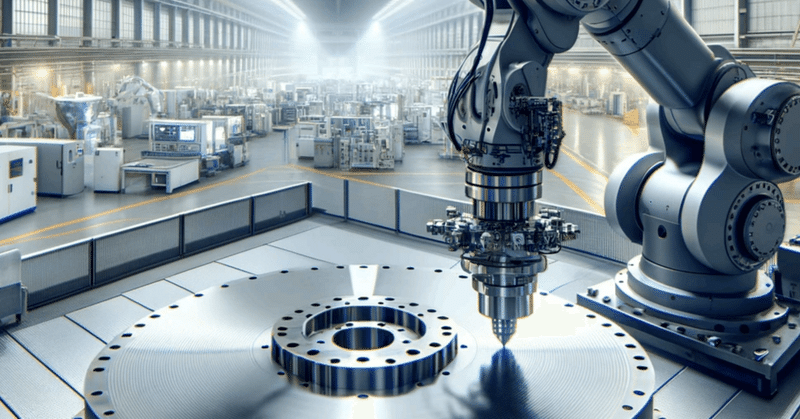
産業用ロボットによる加工自動化の裏側: プロジェクトの実践と学び
こんにちは!アルパカ兄さんです。
産業の未来を形作る上で、ロボット技術はその中心にあります。特に、レーザ加工や切削加工などの加工用途において、その可能性は無限大です。
昨今の電気自動車(EV)への移行は、従来の製造プロセスに新たな課題を投げかけています。大型化するワークに対する加工ニーズが急速に拡大している今、『産業用ロボットによる加工自動化の裏側』を通じて、私が直面した実際のプロジェクト経験を共有します。
この記事では、ロボット加工がどのように実際の製造現場で活用されているか、そしてそれに伴う挑戦や壁、そしてそれらをどのように乗り越えてきたかを深掘りします。
今回は、ロボット技術の一般的な利点に簡潔に触れた後、私の実体験に基づく個人的な視点から、産業用ロボットの可能性を探求します。
この記事を通じて、あなたは以下のことを学ぶことができるでしょう:
ロボット技術がどのように導入され、現場で活用されているか(前編)
ロボット導入時に直面する潜在的な課題とその解決策(後編)
※前編と後編の2部構成です。
ロボット技術に関心がある方々にとって、この記事が新たな発見と実用的な学びの場となることを願っています。
ではでは、よろしくお願いいたします!
大型ワークの自動化:ロボット技術が解決する課題
電気自動車(EV)のバッテリーケースや航空機の機体CFRP材といった1mを超える大型ワークの利用はますます拡大していきます。
それに伴い、大規模な加工機のニーズが高まっていますが、従来のような大型マシニングセンタでは、稼働時間、高コスト、広い設置スペースといった課題があります。
産業用ロボットの使用はこうした問題に対し効果的だとして、その活用が期待されます。ただ産業用ロボットには、その構造上「位置決め精度の悪さ」という課題があるのも事実です。
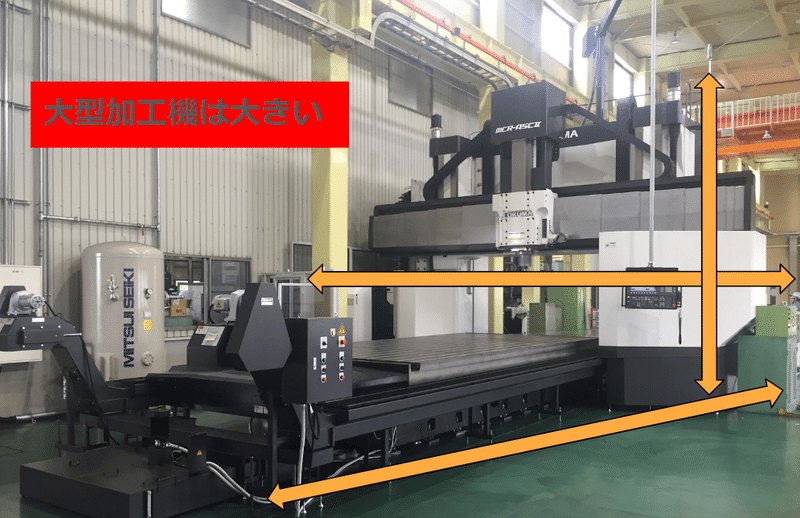
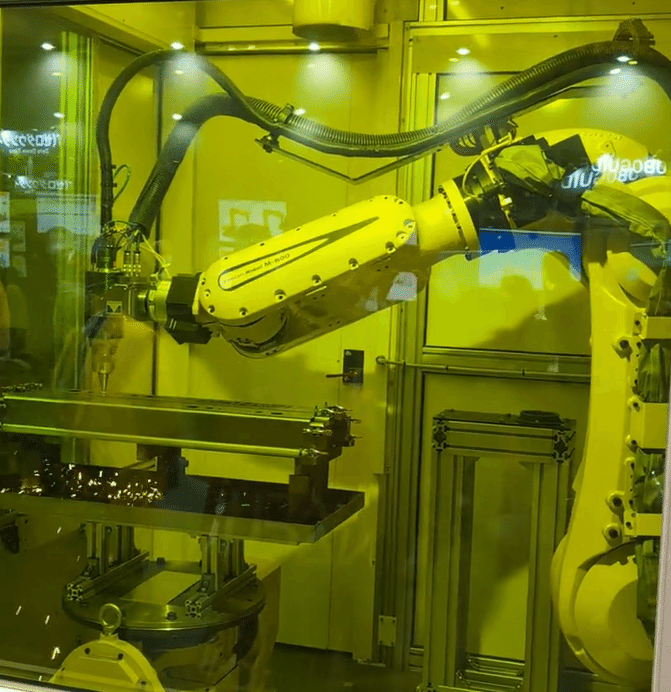
現場から学ぶ:ロボット加工システムの導入事例
このセクションでは、私が経験したロボット加工システムの導入事例をご紹介します。現在、当システムには4台の加工ロボットが導入され、24時間連続稼働しています。
システムの特長:
オフラインティーチング方式を採用し、CADデータからロボット軌跡プログラムを自動生成。
PCを使用して加工条件を簡単に設定可能で、異なる径の工具交換にも対応。
従来のNC加工機に比べ、設置スペースを半分に削減。
生産効率を従来比200%に向上させ、完全な省人化(4人から0人)を実現。
プロジェクト背景:中小製造企業の挑戦
このプロジェクトの顧客は、建築資材の加工を行う中小製造企業です。
従業員は100名未満で、従来は全ての加工作業を人手で行っていました。
しかし、24時間稼働の過酷な作業環境と深刻な人手不足に直面し、自動化の必要性に迫られました。
自動化設備の導入はこれが初めてで、資金の制約、限られた設置スペース、多品種小ロットの生産ニーズが課題でした。
これらの課題に対し、オフラインティーチング方式のロボットシステムが最適な解決策として提案されました。
プロジェクト要求:複合材加工の精密な挑戦
対象ワークは、樹脂複合材(CFRP/GFRP)で作られたパネル部品です。
サイズは最大2m x 1m x 20mmで、穴加工(丸穴、四角穴)と切欠き加工の2つのパターンがあります。
加工のサイズは固定されておらず、様々な要求に対応する必要があります。
要求精度は、原点からのXY距離で±1mm以内であることが求められています。
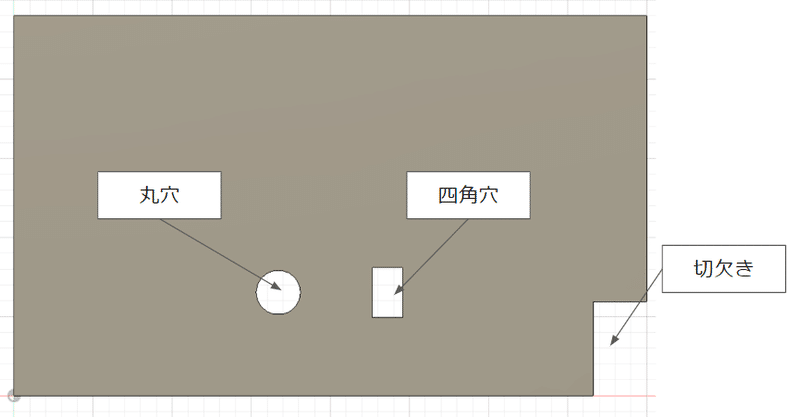
システム構築:ロボット加工の心臓部
このシステムは、加工ロボット、加工テーブル、ツールステーションの3つの主要部分で構成され、設置スペースはわずか2.5m x 2.5mで済みます。具体的なプロセスは以下の通りです:
①搬送装置がワークをテーブルに配置
②加工テーブルがワークを正確に位置決めし固定
③必要に応じてロボットが工具を交換
④加工開始
私たちは、加工精度と範囲を最適化するために、大型で汎用性の高いロボットを選定しました。
可搬重量:200kg/動作リーチ:2500mm
ロボットハンドは、スピンドルモータ、エンドミル、集塵ホースで構成され、インバータ制御により高速回転で加工を実現します。
ツールステーションにはφ3~φ10までのエンドミルが用意され、ロボットは上位システムで指定された工具に自動で交換します。
加工テーブルは、ワークを正確に固定し、加工精度を保証します。
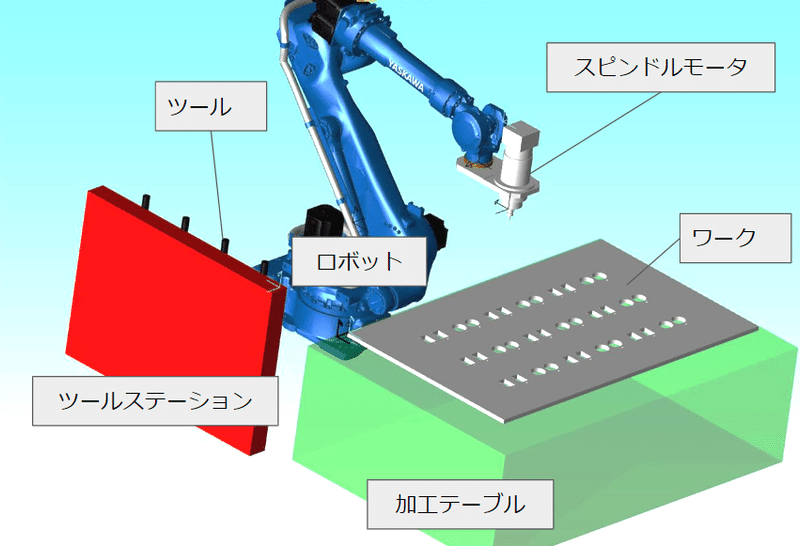
加工の流れ
加工データはPCからPLCを通じてロボットに転送され、以下のステップで加工が進行します:
1. PLCからマスタジョブの発令
2. 加工データを取得
3. 加工プログラムの呼び出し
ロボットプログラムは、加工データを変数で管理し、各加工パターンに応じたプログラムが実行されます。
その加工データはPCで定義されPLCから転送されます。
具体的には以下の変数があります:
[実行PRG番号/工具番号/加工送り速度/加工侵入速度/加工座標]
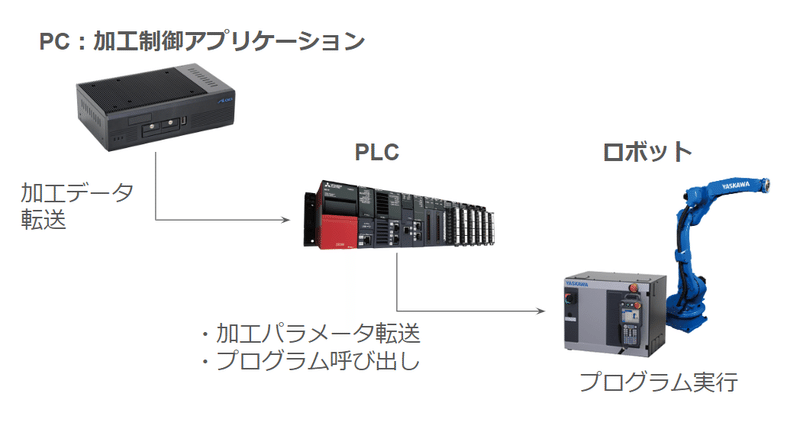
NC加工機ではGコードひとつで加工しますが、ロボットにそのような機能はありません。なのでロボット加工では、座標値やパラメータを一つ一つ転送しないといけません。
PLC間のデータ取得やレジスタ管理のプログラム作成及び確認作業が伴い、工数もかかりましたしデバッグが面倒でした。
ロボットプログラミング
加工プログラムは、ドリルやエンドミルを使用して様々な形状の加工を行います。
例えば、丸穴はドリルで一発貫通、丸穴や四角穴のトリミングはエンドミルで一周し、切欠き加工はエンドミルで二方向からのアプローチを採用します。
プログラム作成では、加工条件のテストを繰り返し、最適な設定を見極めることが重要でした。
ロボット加工プロジェクトの実行計画
ロジェクトの実行計画は、仕様決定から詳細設計、そして現地調整に至るまで、以下の段階を経て進行します:
仕様決定と構想検討
ロボット加工テスト
主要機器の選定
社内でのロボット加工テスト
詳細設計とオフラインティーチング
社内据付工事と試運転
出荷と現地調整
実証実験:ロボット加工の可能性を探る
ロボット加工の実現可能性を探るため、我々はロボットメーカー、スピンドルメーカー、工具メーカー、そしてエンドユーザーと密接に連携し、加工テストの準備と実施を行いました。
様々な加工条件のもとでテストを実施し、最適な条件を見極めることで、プロジェクトの成功に不可欠な情報を得ました。
詳細検証:社内テストによる加工条件の最適化
実証実験に続き、更なる加工条件の詳細検証を目的とした社内テストを実施しました。
この段階では、実際の装置に合わせた詳細な検証を通じて、加工条件と工具の最適化を図りました。
様々な試行錯誤とともに、加工テストはプロジェクトを次のフェーズへと進めるための重要なステップでした。
このプロセスを通じて、ロボット加工の技術的課題への深い理解と、それらを克服するための創造的なアプローチが必要であることが明らかになりました。次回は、これらの課題にどのように対処し、最終的に成功に導いたかについて詳細をお伝えします。
まとめ・次回予告
本記事はここまでとなります!最後まで見ていただきありがとうございました。
ロボット加工の導入は決して簡単な道のりではありません。
特に位置決め精度の課題に直面します。
この課題に対する具体的な解決策は、次回の記事で深掘りする予定です。
ぜひお楽しみに。
質問やさらに議論したい点があれば、遠慮なくコメント欄に投稿してください。
この記事が気に入ったらサポートをしてみませんか?