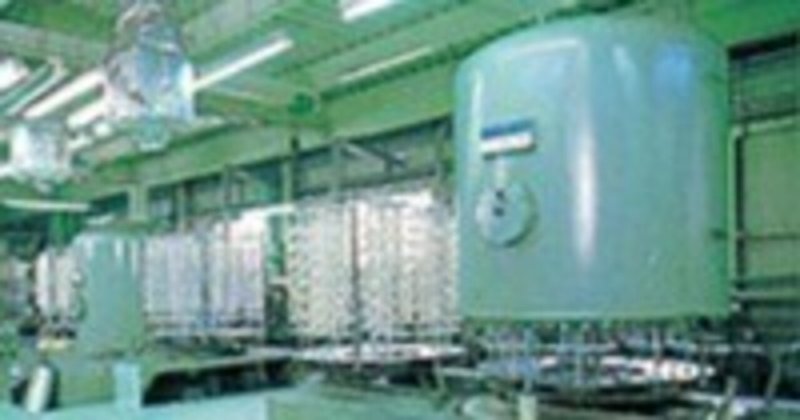
「真空蒸着とメッキの違い」
表面加工技術は製品の外観や性能に大きな影響を与えます。
代表的な技術として、真空蒸着とメッキ(鍍金)がありますが、真空蒸着とメッキは、異なる手法で基板に薄膜を形成する技術であり、それぞれの特徴やメリット・デメリットを理解することは重要です。
今回は、真空蒸着とメッキにおけるそれぞれの工法や特徴や差異について、徹底解説を行います!
【1】真空蒸着の歴史
真空蒸着は、19世紀後半から20世紀初頭にかけての発展を経て、
現代の表面加工技術として成熟しました。
・初期の実験と発見 (19世紀末)
真空蒸着の初期の実験は、化学者のWilliam CrookesやThomas Edisonらによって行われました。彼らは真空中で金属が蒸発する現象を観察しました。
・真空蒸着の応用 (20世紀初頭)
1900年代初頭になると、金属の蒸発により薄膜を形成する技術が実用化され、鏡の製造や光学デバイスに初めて応用されました。
・半導体産業への進出 (20世紀中盤以降)
真空蒸着は半導体産業にも進出し、トランジスタや集積回路の製造プロセスにおいて欠かせない技術となりました。
・微細加工技術への進化 (現代)
現代では、真空蒸着は微細加工技術として進化し、光学デバイスやディスプレイ、センサーなどの製造に幅広く利用されています
【2】メッキの歴史
メッキも古くから行われていた表面処理技術です。
・古代からの利用
メッキの歴史は古代にまで遡ります。 古代エジプトでは、金メッキが彫刻や装飾品に使われていました。
・中世ヨーロッパの技術発展
中世ヨーロッパでは、金属の腐食防止や美的な装飾のために、メッキが広く利用され、金メッキや銀メッキが贅沢品として重宝されました。
・産業革命と大量生産 (18世紀末 – 19世紀初頭)
18世紀末から19世紀初頭にかけての産業革命に伴い、メッキ技術も進化し、大量生産が可能となりました。
・電気メッキの登場 (19世紀末)
航空機やドローンに搭載され、地形や建造物の精密な地図を作成するために使用されます。
・自動車産業との関わり (20世紀初頭)
自動車産業の発展に伴い、クロムメッキなどが自動車の装飾に広く利用され、その後さまざまな産業にも拡大していきました。
【3】真空蒸着の特徴・使用例
(1)特徴
・真空環境 :高真空または超高真空状態で行われます。
・均一な薄膜形成 :蒸発源からの材料供給が均一で、精密な薄膜形成が可能です。
・多様な材料の利用:金属、セラミック、有機物など異なる材料が利用可能です。
(2)メリット
・微細な構造への適用: 微細なパターニングや構造にも適応可能です。
・高い原子対原子効率: 原子対原子の効率が高く、密度の高い薄膜形成が得意です。
(3)デメリット
・高真空状態の維持が必要: 真空度の維持がプロセスの一部であり、機器費用が高額です。
(4)使用例
光学デバイス: ミラー、フィルターなどの微細な構造への薄膜形成。
半導体製造: 配線やコンタクト形成において微細な構造への薄膜形成。
【4】メッキ(鍍金)の特徴・使用例
(1)特徴
・大気中での実行: 通常の大気圧で行われ、真空は必要ありません。
・低コスト : シンプルでコストが低いため、大量生産に適しています。
・高い導電性 : 金属薄膜により高い導電性が得られる。
(2)メリット
・低コスト : 比較的コストが低いため、大量生産に向いています。
・デザインの柔軟性: 様々な形状に適用可能で、複雑な構造へも対応可能です。
(3)デメリット
・不均一性の可能性:
電流密度やイオン濃度に依存し、均一性の確保が難しい場合があります。
・剥離の可能性:
十分な密着性を持っていない場合、剥離が発生する可能性があります。
(4)使用例
・電子機器:コネクタ、基板などの導電性向上や金属部品の保護に利用。
・装飾品 :ジュエリーや時計などの装飾品に金メッキを施し、美と耐久性を兼ね備える。
【5】まとめ
真空蒸着は主に高度な技術と微細加工に焦点を当て、半導体やディスプレイなどの分野で重要な役割を果たしています。一方で、メッキは真空蒸着と比較した場合、低コストで広範な導電性向上や装飾に適しています。また、古くから美的な目的や金属の保護に利用され、その発展には電気メッキなどの技術の進歩が寄与しています。
それぞれの技術ともに、異なるニーズに応えるための進化を継続しており、
現代の工業分野においては欠かせない技術となっています。
安達新産業株式会社は、真空蒸着やスパッタリングの技術をより発展させるため尽力しています。
この記事が気に入ったらサポートをしてみませんか?