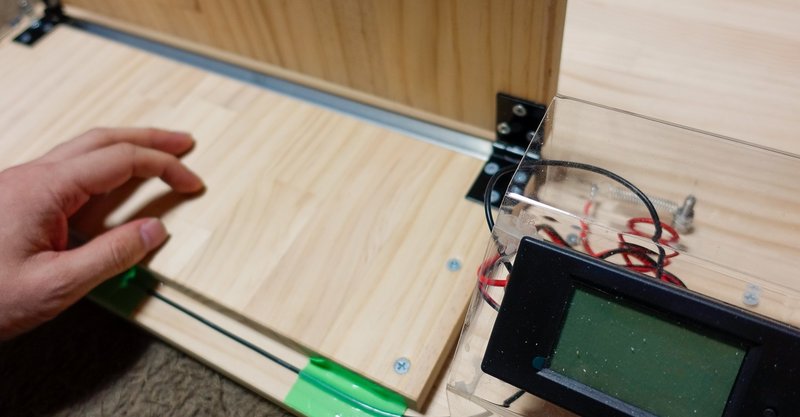
アクリルベンダーを自作しよう
どもどもYanでっす。
本日のお題は「アクリルを綺麗に曲げたいけど、いい道具が売ってないので自作する」でっす。
接着難しい!
アクリルはレーザーカッター使えばかなり綺麗に切断することができます。でもこれだけだと板状のものにしかなりません。平面的なものを立体的にするにはどうするか。
僕もそうでしたけどほとんどの人は、ネジ等で固定する、見栄えをよくするなら接着というのを最初に思い浮かべるんじゃないかと思います。
でもね、アクリルの接着って難しいんです。アクリルはアクリル用の接着剤を使います。たいていは塩化メチレン(ジクロロメタン)が主成分。水みたいにサラサラで、揮発性がとても高い。接着する部分をギリギリまで接近させておいて、そこに針のようなものを使って接着剤を流し込むという形をとります。
上の画像は小さいものを接着してるけど、カメラ片手の作業だったので思い切り失敗しました。
写真撮った後に気泡を押し出そうと頑張りましたが時すでに遅し。アクリルの表面が解け始めていて、すり合わせて空気を押し出そうとすると逆に溶けたアクリルの中に気泡が小さくわかれて混入してしまいました。白や黒みたいな不透明色なら接着で問題ないんですけど、アクリルは透明系が多いので…。
これが長いものとか広い面積になるとどうなるかはお察し…。
そこで曲げですよ!
接着は塩化メチレンじゃない他の接着剤も探すことにして、他にアクリルに立体感を与える方法はないもんだろうかと探していたら、ありました。アクリルは樹脂なので加熱すれば柔らかくなります。二つ折りにしても割れないくらい。
ガスバーナー方式
加熱方法はいろいろあるけど、一番簡単なのはコレ。3Dプリンタの出力物の仕上げでも使うことがあるヤツ。
火があたるか当たらないかの状態で一か所にずっと当てないようにして温めます。アクリルの自重で曲がるくらいに柔らかくなったら加熱をやめて形を決めて冷ませば完成。
YouTubeで見かけたんですけど、看板製作ではガスコンロ使ってたりもするんですね。
この方法のメリットはコストがかからないこと。どんな大きさにも対応ができること。デメリットは火を当てすぎると、アクリルが焦げたり、沸騰して気泡が入ってしまうことと、正確なラインで曲げにくいこと。
ヒーター方式
主に電熱線を使って曲げたいライン付近を加熱して曲げる方法。僕がアクリルベンダーの自作をしようと思ったのは、YouTubeでこの動画を見たからです。
金属加工ではベンダーという工具がよく使われます。この動画のやつはまさにアクリル用ベンダー。他にもYouTubeにはアクリルベンダーのDIY動画がありますけど、ニクロム線を使うやつではバネでテンションを維持する仕組みはどれも共通してました。理にかなってると思うので、モーターコントローラーとニクロム線、バネの組み合わせは真似させてもらいました。
この方式のメリットはまっすぐなラインで曲げられる。角度を決めやすい。バーナーのように温度管理が難しくないこと。
デメリットは1枚の板で複数個所曲げる場合、順番を考えながらやらないと詰んでしまうことがあること。大きな範囲を曲げるのには適さないこと。
どっちも一長一短あるので、使い分けるのがいいのかなーという感じです。
こういう形のアクリルベンダーって売ってないのかなって探したんですけど、ホームユースのやつはどうも日本では販売されてないみたいです。なので自分でつくることにしました。次からはその作り方です。
アクリルベンダーの作り方
材料
・ニクロム線 0.5mm
・引張コイルばね 8 × 28.5mm
・DCモータースピードコントローラー
・DCマルチメーター(オプション)
・電源(12~24Vくらい)
・電線 AWG16以上くらい
・板
・アルミチャネル
・蝶番 2個
・固定用のネジ
ニクロム線
アクリルベンダーのヒーター部分に使用。スチロールカッターとかに使われてる銀色の線と同じ。実際のヒーター部分の長さ+15cmほど余裕を持ったがなさが欲しいところ。僕が買ったのは5mリールだったので片方の端を固定してから必要な長さ+5cmくらいで切って使ってる。
引張コイルばね
ニクロム線は熱膨張で伸びてしまうので、両端を単に固定してしまうと垂れさがって、周囲のアルミチャネルに触れて一気に熱が奪われてしまう。そこでテンションを保つために片方をバネで引っ張ってあげるのにコレを使う。今回使ったのは8 × 28.5mmのもの。ばね選びは難しくて、単体のばねを買おうとしても上手くいかないときに買いなおしになる。なので結局はこういうやつを買って、使えそうなのを選ぶ方が手間もお金も節約できるということが多い。
DCモータースピードコントローラー
これを使ってニクロム線に流す電流をコントロールしてあげる。何A流すと何度になるというのは、外気温によっても変わってくるので、電源の最大値を超えない電流に制限してあげるという意味合いの方が強いかもしれない。
単純に計算すると12Vの電源を使う場合、ニクロム線0.5mm(50cm使用する)の抵抗値は約5.5Ω/mだから2.75Ω。オームの法則(E = IR)から
12V = I × 2.75Ω
I = 4.4A
電源の電圧を20Vにすると電流は最大でだいたい7.3Aくらい。
電流が多く流れるほど昇温時間は速くなる。12Vだったら5A以上のもの、20Vだったら8A以上のものなら電源の定格は超えないはず。手持ちのノートPCのアダプタとかを流用する場合で、回路に最大で流れる電流よりもアダプタの出力が低いときは、このコントローラーでアダプタの最大出力を超えないように制限できるという形。
DCマルチメーター(オプション)
これはなくても大丈夫。こういう工作をする人ならばテスターは持っていると思うのでテスターでも代用できる。
僕が買ったのはコレで、計測用のシャンク抵抗が内蔵されているので、端子に入力と出力を接続してあげるだけで電圧、電流、消費電力が表示される。
僕はアクリルベンダーを使ったことなかったので、急速に昇温するよりはゆっくりの方が作業しやすかろうと12Vの電源を使ってるのだけど、12Vなら最大でも4A程度しか流れないので電源の最大値も超えないし、このメーターはオンになってるなーとかの目安にしかなっていないという状態。
電源
上でも書いたけど12V~20Vくらいが適正範囲じゃないかと思う。12Vのアダプタで使えそうなのが家になかったので、適当に買ったやつ。
最大値の半分くらいしか電流流れてないので、安心。
電線
それなりに電流流すので太目の電線を用意しておきたいところ。
だいたいの目安として電子工作でよく使われるAWG24は2.5Aくらい、AWG20だと5A、AWG18だと6.5A、AWG16だと11.5Aが流せる許容範囲。
12V電源ならこれくらいのやつで大丈夫。6.5A以上流すのであれば、AWG16とかもっと太いのが必要になる。小巻きのリールってあまり見かけないのでメートル単位の切り売りになると思う。
板
近所のホームセンターにちょうどいいMDFが売ってなかったので、僕はパイン集成材を使ってるけど多分MDFの方が経年変化の反りが少ないと思う。
600mm × 400mmくらいのが2枚だったかな? 1枚はそのまま台座として使って上に400mm × 150mmで切り出した板を2枚使ってる。
アルミチャネルに面する部分は平らなのが望ましいけど、反対側は多少曲がってても大丈夫。厚さはアルミチャネルと相談して決める必要がある。アルミチャネルは10mm、12mm、15mmって感じでたいていどこのホームセンターにも売ってる。今回はアルミチャネルと同じ高さの一番薄い板が15mmになるので15mmの板を使ってる。
アルミチャネル
15mmのやつ1mを買ってきてサンダーで切断して端面を綺麗にして使用。このアルミチャネルはニクロム線から直接木材に熱が伝わるのを防ぐ役割と木材を簡単に平行配置できるというメリットがある。
2mm厚さとなると電動工具を使わないと切断が大変なので、15mmで肉厚1mmのがあればそっちがオススメ。アルミチャネルは上の写真の様に底に下穴を開けてから木ネジで底面のパネルに固定している。
蝶番
左右で2個必要になる。幅が大きいとアクリル板をセットできる範囲が狭くなってしまうので3~4cmくらいで平気。木ネジで板に固定する。
ネジ
M5くらいのやや太めのネジ 2本をニクロム線の固定に使う。6mmくらいの穴をあけて下からM5ネジを入れて上側でナットで固定、その上に別のナットで巻き付けたニクロム線を挟むように固定し、ニクロム線への配線もここでナットで固定している。
反対側はスプリングの端をひっかけてナットで挟み込んで固定。この固定のメリットはニクロム線の高さの調整が簡単にできること。
木材やアルミチャネルの固定は木ネジ。経年劣化での反りをなるべく防ぐなら、木工用ボンドと木ネジの併用がオススメ。
配線
配線はいたって簡単。電源からマルチメーターの入力端子に接続して、マルチメーターの出力端子からモーターコントローラーの入力に接続。コントローラの出力端子からニクロム線に接続する。
図の都合でバネの端に結線しているようになっちゃったけど、バネとニクロム線の接合部付近にハンダ付けしている。バネはある程度引っ張った状態にしないとニクロム線が熱膨張したときにテンションを保てないので気を付けよう。
出来上がったものはこんな感じ。メーターとかコントローラーはアクリル板を切り出してベンダーで曲げてつくったけど、初曲げだったので勝手が分からず、温まりきらないうちにまげようとして細いとこが折れました!
とりあえず実際に使い物になるかの確認でもあったので動画にあるような角度を固定する機能とかはありません。必要になったらアクリルを切り出して角度決めできるようにするつもり。
実は、アクリルで有名なアクリサンデーがAC100Vで使えるヒーター部分だけ売ってるんでこれをベースに作ってもいいかもしれないです。
このヒーター部分は、モーターコントローラー、ニクロム線、電源を合わせた役割。この長さで決まってしまっていて、好きな長さでつくれないというのはちょっと不便かも。
まとめ
中華CO2レーザーのネタもやりたかった改造までnoteに書いちゃって、しばらく書くネタないかなと思ったんですけど、アクリルベンダーのこと書いてないことに思い至って曲げ方と一緒に書いてみました。
アクリルを切る方法は何もレーザーカッターだけではなく、直線ならPカッター1本あれば切れます。切って終わりじゃなく、その後に一工程加えることでオリジナリティを生み出せるんじゃないかなと思って、曲げ方と一緒に便利なアクリルベンダーの紹介です。
ここから下は記事を購入してくださった方へのお礼とかで、アクリルベンダー作成に関する記事はここまでで完結しています。この記事が面白かった、役に立った、と思っていただけたらサポート、購入お願いします!
ここから先は
¥ 100
僕のノートが役に立った、面白かったと思っていただけたら、スキ、フォロー、サポートお願いします!