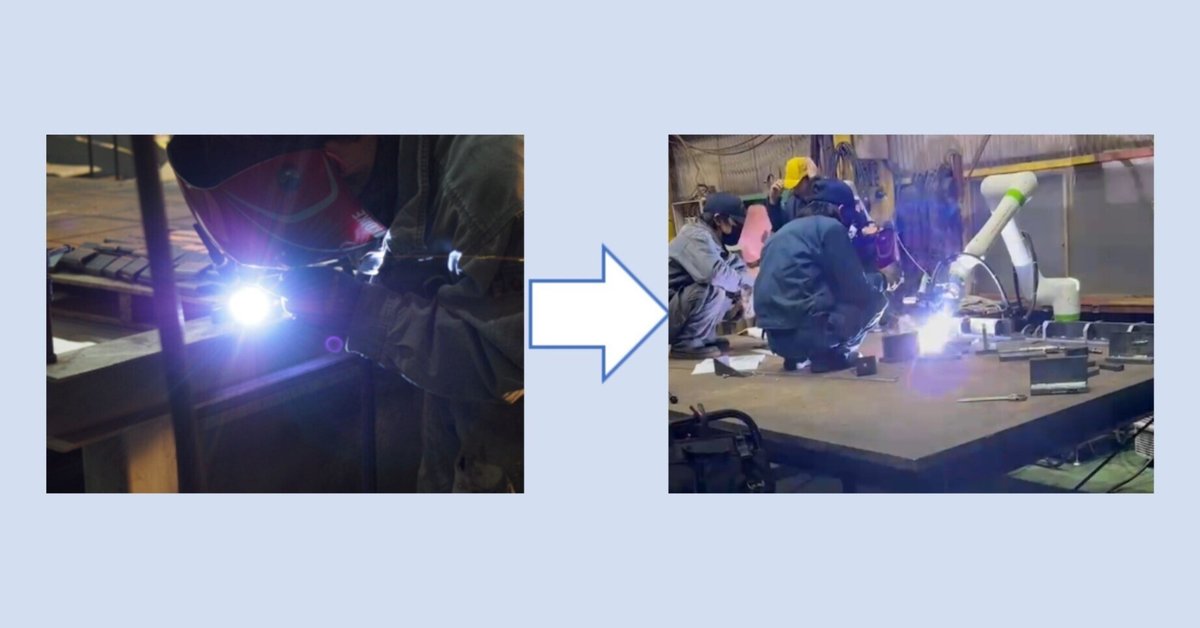
愛媛にスマート工場を!製造工程のDX化で製造業の課題解決に挑む!【株式会社ディースピリット|実装報告】
製造現場のDX化で、人手不足などによる中小製造業者の課題解決に挑む本プロジェクト。愛媛県内の企業を「モデルスマート工場」とし、実装で得たナレッジを県内中小製造事業者に情報発信し、愛媛県全体のDX化に貢献することを目指している。
プロジェクトリーダーである株式会社ディースピリットは、AI、IoT、Robotシステムの企画開発、中小企業向けの各種ソリューションを行っている企業だ。特にAIの開発においては、データ収集から機器への実装まで自社で一貫して行うため、コストパフォーマンスの良いサービスを提供している。
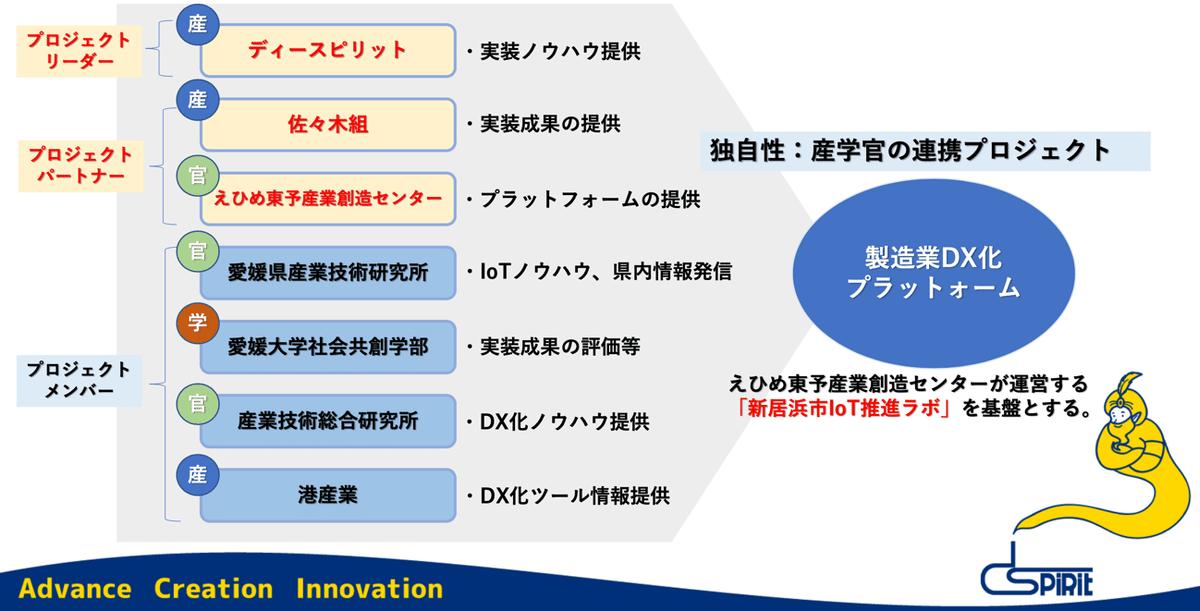
今回、モデル工場として実装された企業は、産業用フレームの製缶、溶接加工、レーザー切断、筐体製作などを行っている新居浜市の「有限会社佐々木組」。恒常的な人材不足の状態が続き、製造工程の管理や部材の搬送、溶接作業などを手作業で行い、その状況が機会損失にも繋がっていたため、生産性の向上と労働環境改善は緊急の課題であった。手作業で行なっていた工程にAGV(無人搬送車)と溶接ロボットを導入。また製造工程の管理システムも導入したことで“進捗の見える化”が可能となり、ソフト面もハード面もスマート工場化を図ることができた。その実装の様子をレポートする。
佐々木組が抱えていた課題
ベテランの職人による技術力の高さに定評がある佐々木組。しかし、あらゆる工程において進捗管理ができておらずムダが多く、部材の運搬にも手間がかかっていた。ベテラン溶接作業員の高齢化と、後継者がいないなどの課題も山積み。DX化のセミナーや展示会に参加したり、部分的なDXを検討したこともあったが、たくさんの課題を抱えたままDX化に着手できないし、そもそもDX化を相談できるシステムベンダーがいなかった。
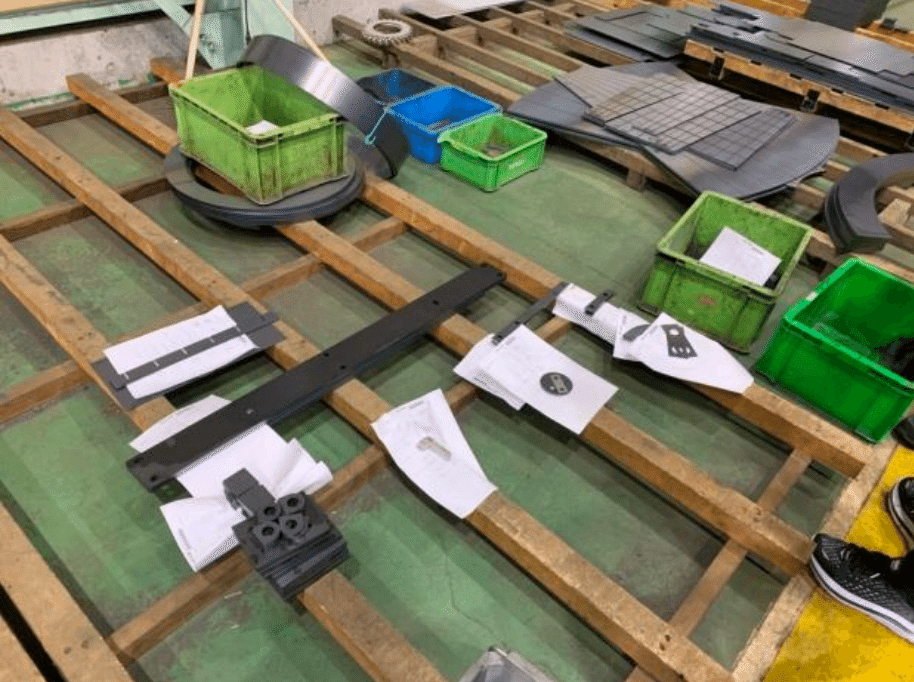

実装前の具体的な課題
●製造工程の進捗状況は、定期的な目視確認のためのムダが多く誤差が大きい。
●製造工程は帳票によるアナログ管理のため情報共有に時間がかかる。
●重量物の運搬や溶接作業は手作業で行っており生産効率が悪い。
●中小製造業者とシステムベンダーをマッチングさせる機会が少ない。
●重労働で身体的な負担が多い工程がある。
●社員募集をしても3K職種のイメージで応募がない。
課題解決のため実装された内容
DXプラットフォームで実装先(佐々木組)とシステムベンダー(ディースピリット)をマッチングした今回の実装プロジェクト。システムベンダーが課題を洗い出し、現状分析。課題解決に向けたDX化の検討を行い、提案企画書の策定。費用、省力化や生産性向上効果を算出し、費用対効果の検証を行った。実装先、えひめ東予産業創造センター、ベンダー3社で契約。DX化の実装を行い、プラットフォームで実装成果の検証、実装事例としてプラットフォームから情報発信するという流れで行われた。今回の実装でDX化による費用対効果も明らかになった。
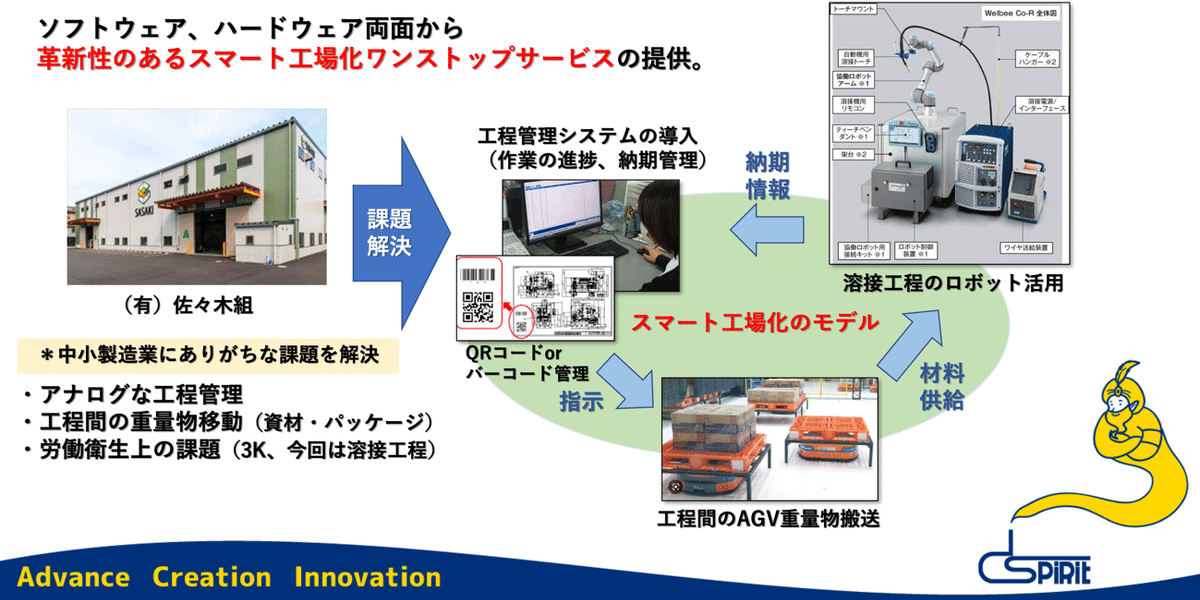
(1)製造工程管理システム導入による工程進捗の見える化
佐々木組では受注後、図面や帳票でアナログな管理で行っていた製造工程管理。原価計算、日報、集計作業などをすべて手書きで行っていたため転記にも手間取り、現場の業務負担も多かった。バーコードを活用した「製造工程管理システム」を導入することにより、発注時から、製品完成までの進捗管理や納期管理を一元管理することが可能になった。転記などの二度手間もなくなり、作業は効率化、製造作業の“見える化”にも繋がった。
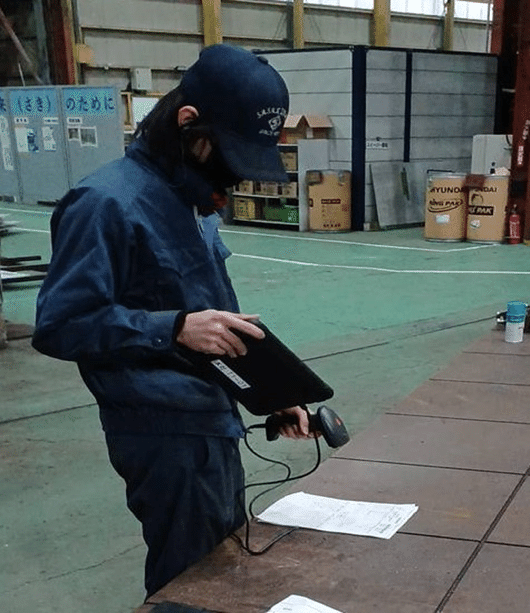
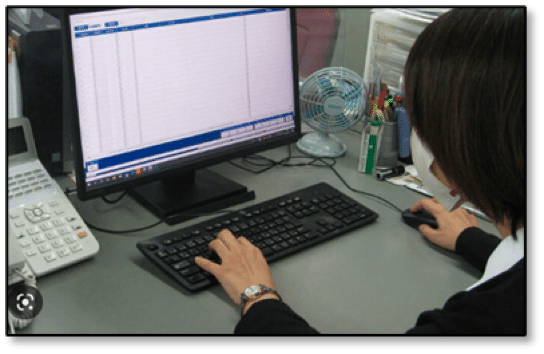
(2)運搬作業・溶接作業の効率化
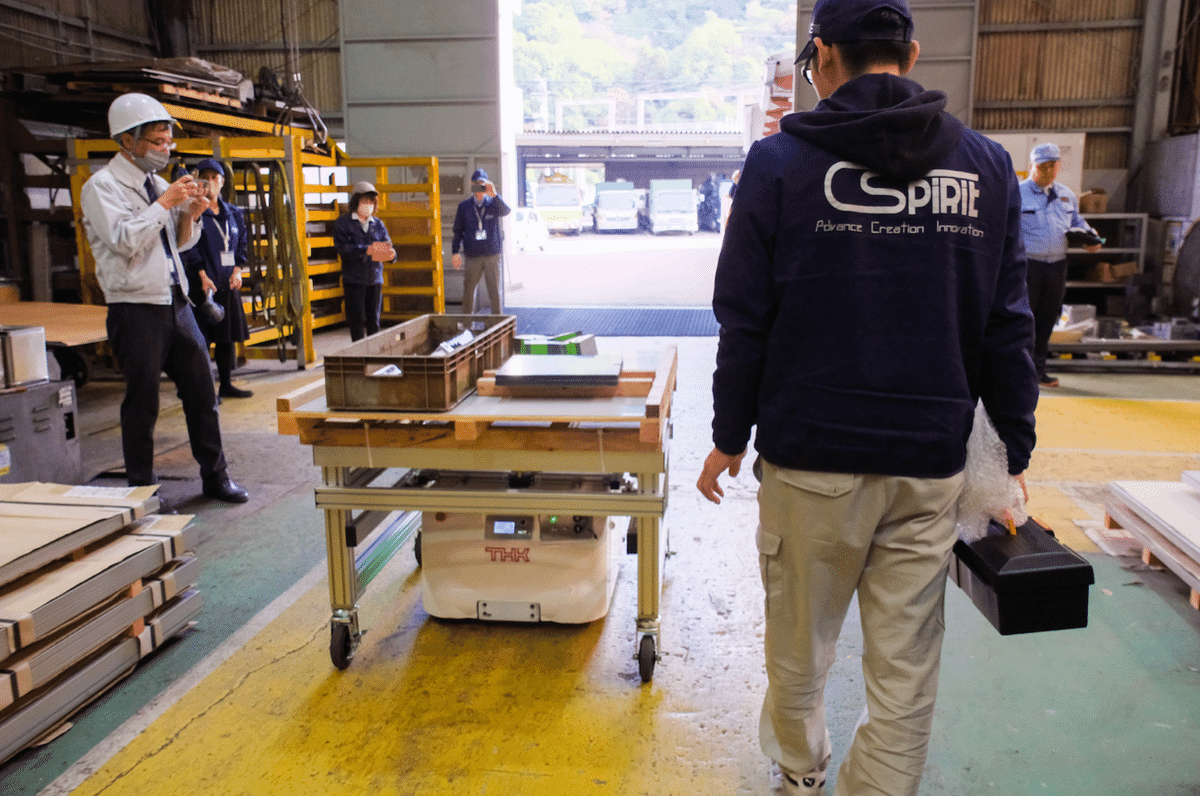
増築を繰り返したことで工場内の動線が悪く、クレーンが繋がっていないため、資材や製造品などを手押し台車を使用して運搬作業を行っていた佐々木組。手押しが不可能なものに関してはクレーンで吊り上げ、乗り継ぎを繰り返しながら移動していたため、徒歩だと1分ほどで移動できてしまう距離なのに、部材の上げ下ろし作業も含めて約25分もかけて行われていた。増設を繰り返した工場間を何度も往復しないといけないため、作業時間のロスも大きく、高齢の熟練溶接従事者には身体的な負担も増えてきていた。そこで部材搬送ロボット「AGV※1」を導入。手作業で行っていた重量物の部材搬送を自動化することで、作業量がかなり軽減された。さらに、溶接機やアームロボットを組み合わせて溶接作業を自動化できる「溶接ロボット」も導入。溶接作業そのものの省力化も図ることができた。まだ効果測定中ではあるが、人件費換算で省力化効果があり、生産性向上効果は5.2%という結果が出ている。実際に、AGVと溶接ロボットにより労働環境が改善した佐々木組では、工場内の整理・整頓・清掃・清潔の習慣づけも、自然発生的に始まったという相乗効果も生まれた。
※1 AGV(Automatic Guided Vehicle)
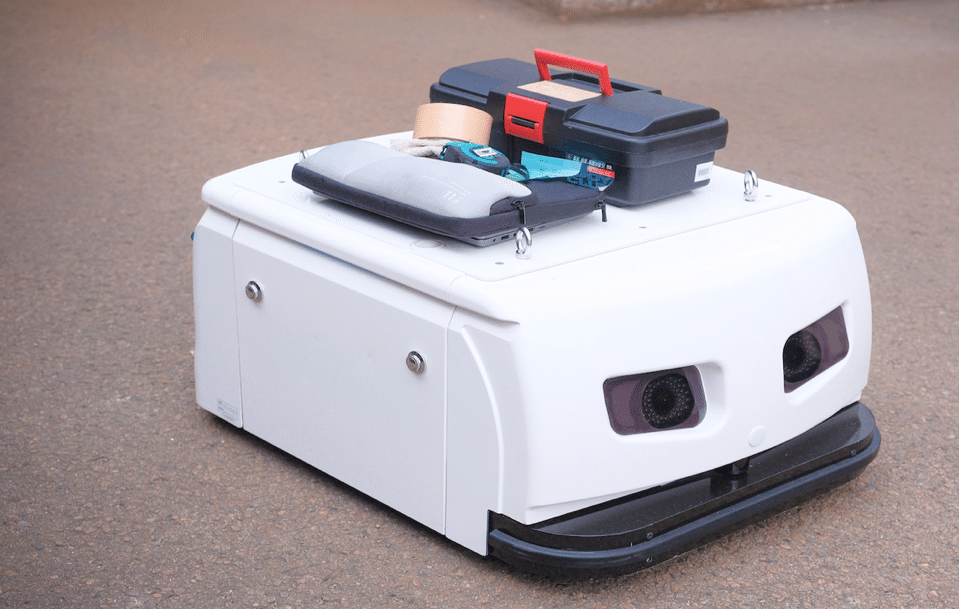
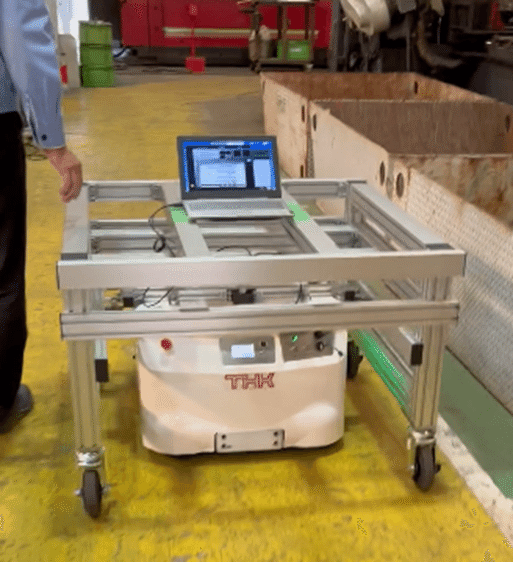
150kgまでの重さに対応する無人搬送台車。台車の上に櫓を組むことで、総重量500kgまでの部材を運ぶことができるので、佐々木組では櫓を組んで使用することに。磁気パネルが発する磁気に誘導されて無人走行するため、直進だけでなく、パネルの数を増やせば複雑な順路でも対応できる。工場によっては床面に磁気テープを敷設する場合もある。
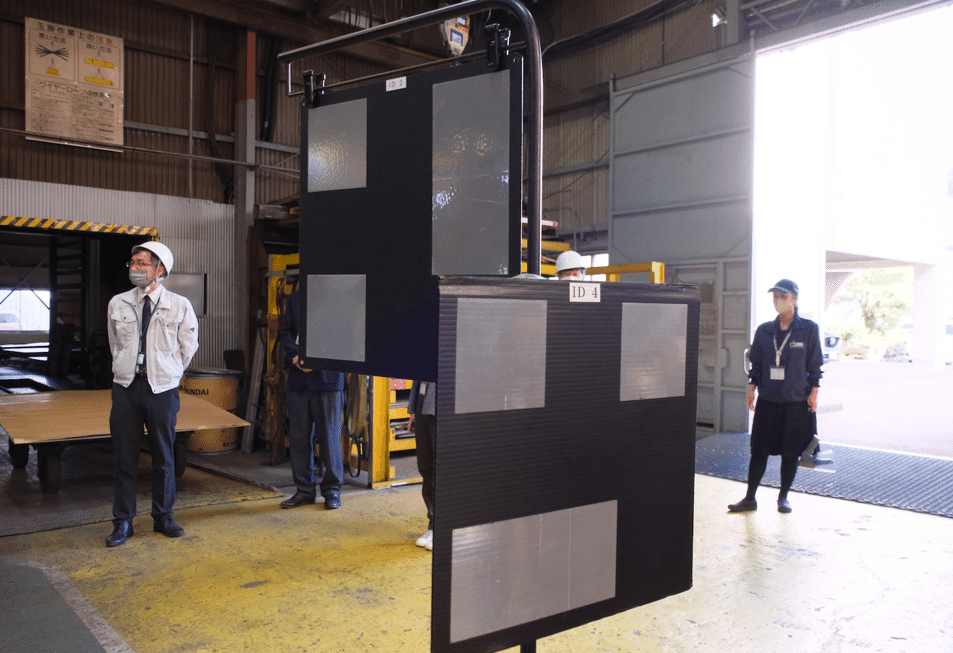
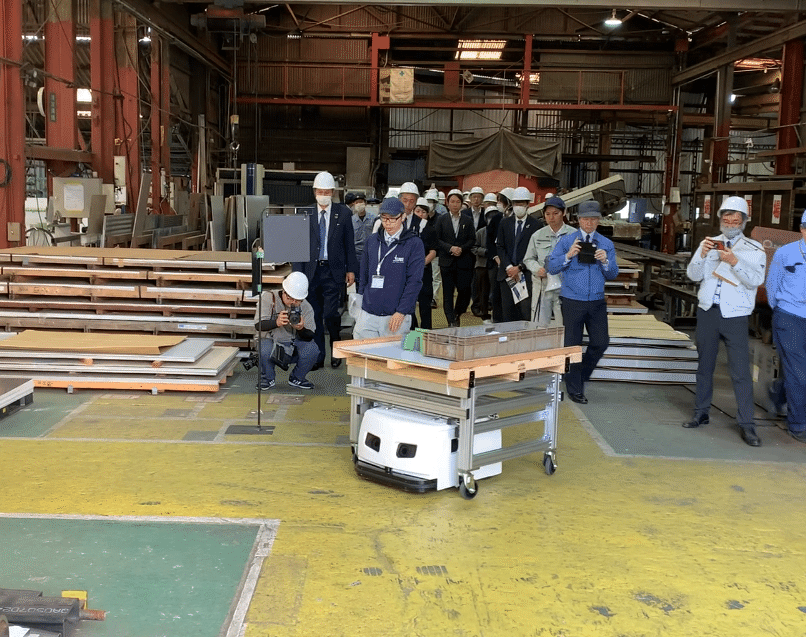
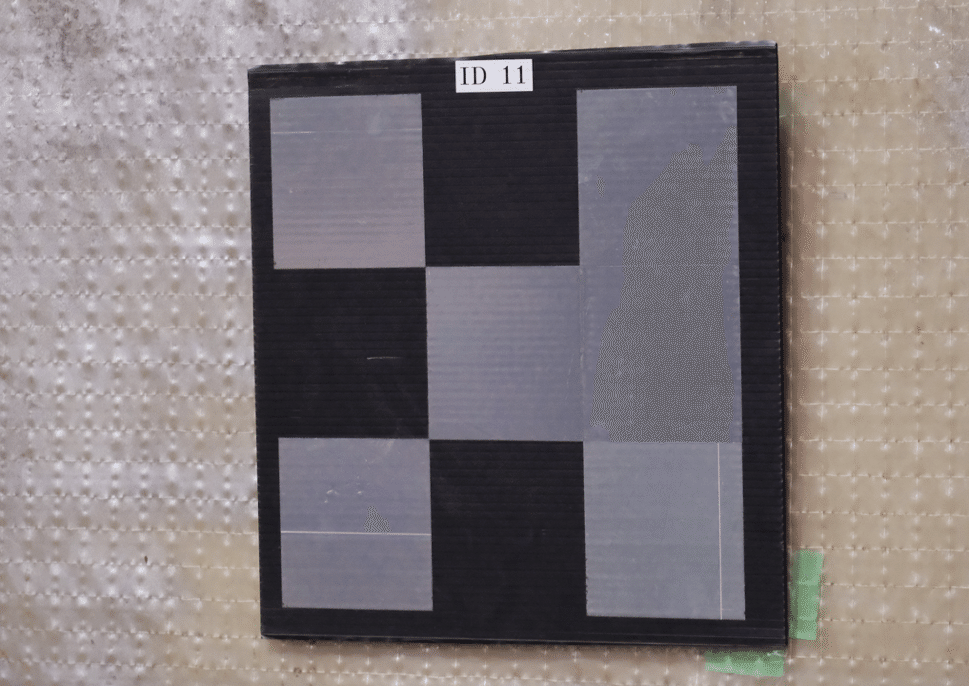
佐々木組で行われた勉強会の実施概要
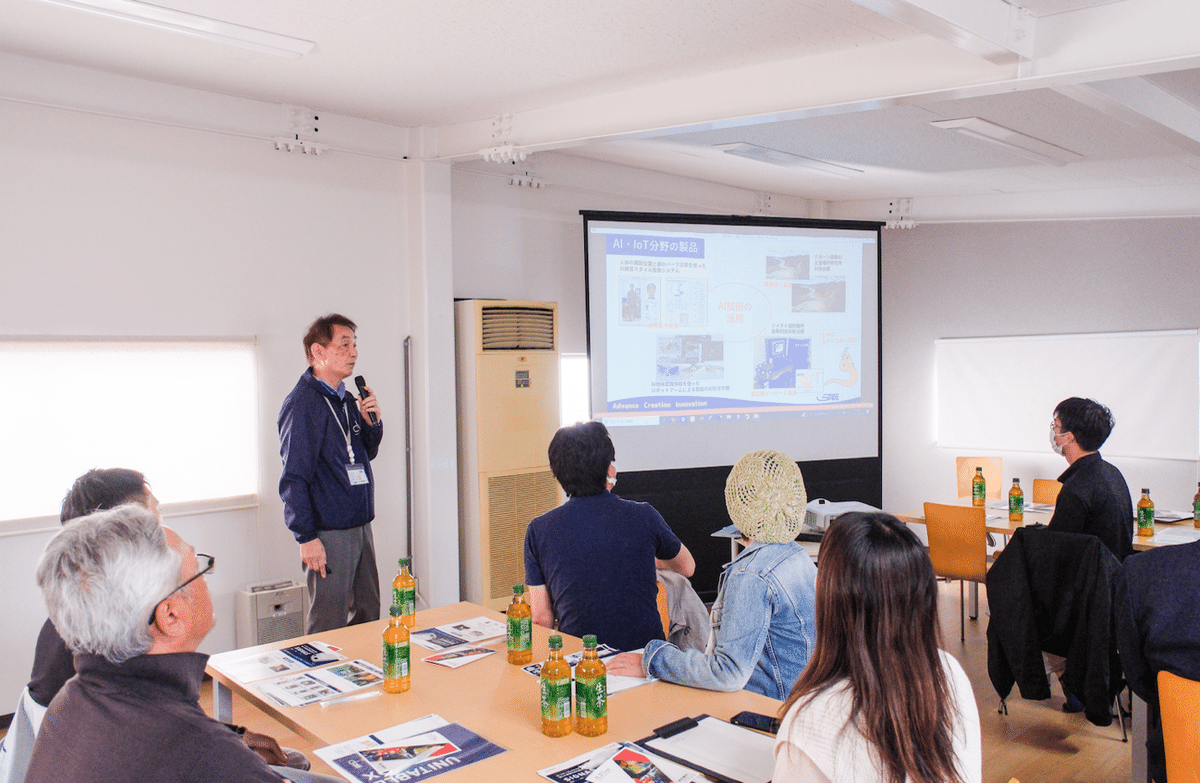
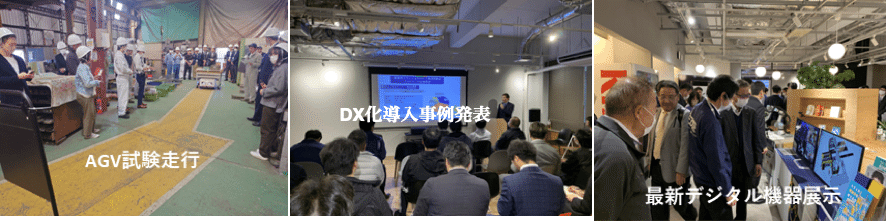
中小製造事業者のDX化実装事例や最新デジタル機器を見てもらうことを目的に、新居浜市で1回、他のプロジェクトとの合同で松山市で2回、合計3回の「ものづくりDX勉強会」を実施。1回目の新居浜で開催された勉強会には24名の参加。松山市で開催した勉強会には、2回目は59名、3回目は62名(いずれもWeb参加者含む)の参加実績があった。
本プロジェクトの事業概要の説明から始まり、佐々木組からの課題説明、ディースピリットからのスマート工場化に向けた取り組み内容の説明と成果報告を行い、その後に意見交換を行った。また、製造事業者の課題を明らかにするため、アンケート調査や聞き取りなども行い、具体的な取り組みを検討して、省力化や生産向上に対してどのようなDX化が最適なのかも協議した。
次年度以降の実装計画と見立て
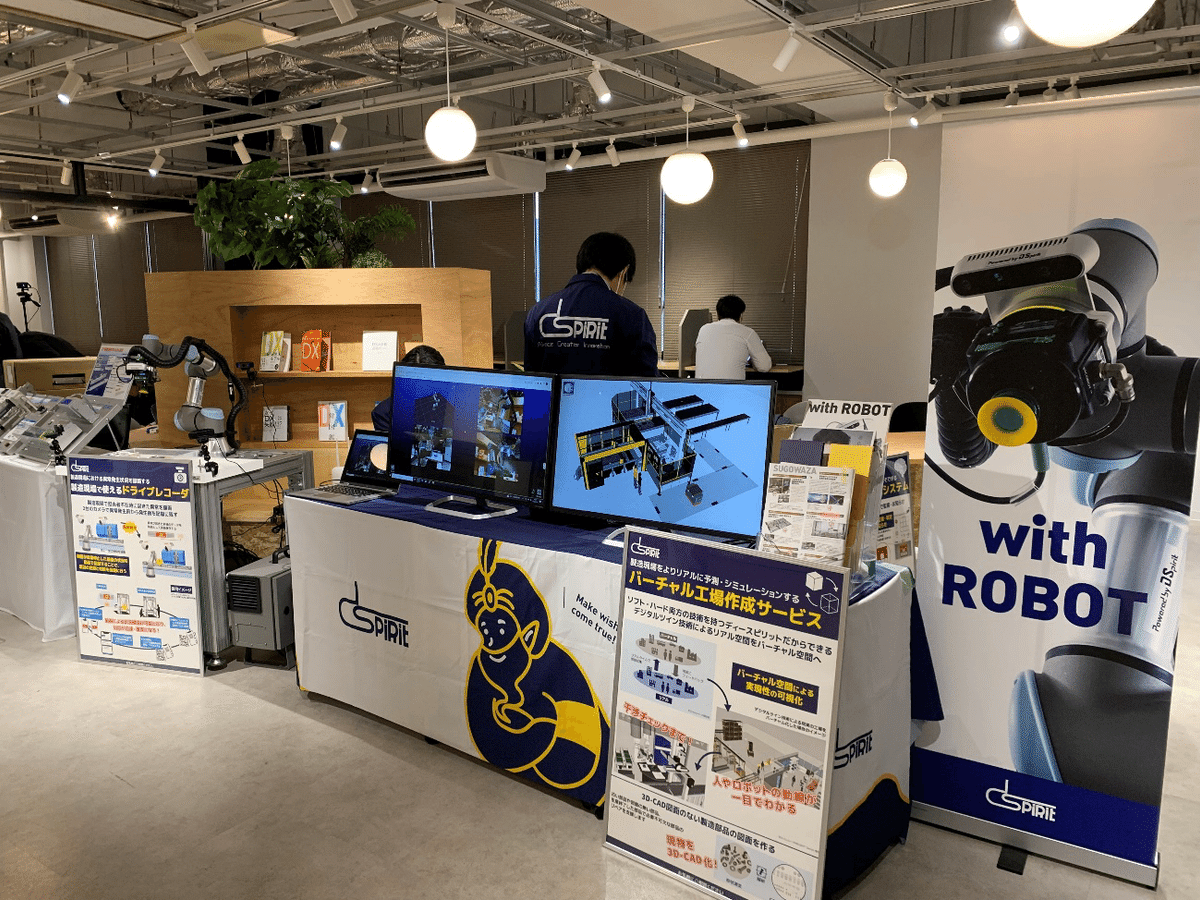
今回の実装により、佐々木組では製造工程の進捗管理、製造部材の運搬回数、溶接時間、労働環境、省力化効果、生産性向上の効果があり、機会損失の改善が見られた。製造現場では、人材不足や労働環境の悪さ、手作業などが効率化に大きな影響を与えているため、この成功事例を多くの愛媛県内の中小製造事業者に情報発信する必要がある。
今回の佐々木組でのスマート工場化実装プロジェクトをモデルケースとし、生産性向上の知見や各種データ、ノウハウを産学官の連携プロジェクトである「製造業スマート工場化プラットフォーム」と連携しながら、愛媛県内の製造業界に還元していくことを目的としている本プロジェクト。現在、DX化プラットフォームにはすでに問い合わせが9件、マッチングに関しても6社の実績がある。今後3年間でスマート工場化効果は約12億6千万円に、具体的な計画としては下記を想定している。
①スマート工場の実装目標
モデルスマート工場(佐々木組)と同規模のDX化を3年間で10事業者
② DX化プラットフォーム
まずは東予地域の約1000件の製造事業者をターゲットに。その後は愛媛県内の約2000件の製造事業者に拡張予定
③スマート工場化セミナーを開催
えひめ東予産業創造センターおよび「新居浜loT推進ラボ」、愛媛県産業技術研究所を通じて、中小製造事業者へのスマート工場化セミナーを開催予定。
今後3年間で東予地域の約1000件の製造業者のうち10社のスマート工場化を目指す。既存の実装先において、十分な省力化効果と生産性効果を得ており、継続的な運用のための費用や体制は確保できている。今後、国の補助金等を活用してAGVや溶接ロボットの増設を検討していく予定となっている。

■公式ホームページ
https://dx-ehime.jp/
\SNSもやっています/
■Instagram
https://www.instagram.com/tryangle_ehime/
この記事が気に入ったらサポートをしてみませんか?