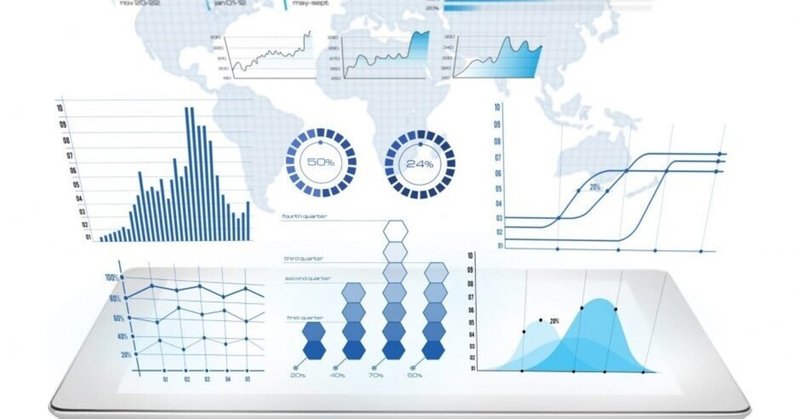
上手ななぜなぜ分析
なぜなぜ分析は机上の理論ではなく、企業(職場)で実行し効果をあげる実践論です。しかし、それが頭でわかっていても人の心理がバイアスとなって邪魔し、適切に運用できている企業は多くありません。
たとえば、「真因」を特定する過程において安易に
「何回繰り返せばいいのか」
という考え方に固執する人がいます。
『5なぜの法則』なんて言葉もありますね(いわゆるトヨタ式)。でも、無条件に5回繰り返せば必ず真因に辿り着けるか?というと答えはNoです。3回で辿り着くこともあれば、10回やっても辿り着かないことはあるものです。
トヨタ式のそれはあくまで統計的に5回前後で答えに達することが多いからそうなっていると言っているだけで、「5回で必ず答えに達する」とも「5回やるべきだ」とも言っていません。自分の頭で考えようとせず、答えだけを欲しがってなんとなく言われたとおりに実施しているだけでは正しい答えを得ることは叶わないということは忘れないようにしましょう。
上手ななぜなぜ分析を進めたければ次のことに注意しなければなりません。
①物事が成り立つ原理原則はどうなっているかを調べる。
(2原主義:原理、原則)
・標準化活動の手順を活用するとよい。
・標準類・単純ミス発生などは分析シートを活用するとよい。
②事実を正しくみる
・3現主義:現場、現物、現実。
・事実確認:データに語らせる。考えや思い込みは含めない。
・みる:見る、視る、観る、看る、診る。
③事実をデータ(数値)で表現する
・層別して、違い/変化/傾向などを確認する。
④データを整理し、因果関係がわかるようにQC手法などを活用する。
⑤因果関係(原因究明)を技術面と管理面に分けて判断する。
・技術面:知識、スキル、認識、環境。
・管理面:標準化(ルール、基準、手順、プロセス、その統制等)。
⑥問題現象を発生させている要因を論理的に分析していく。
(手順に沿って、順序よく、漏れなく出し切る)
・職場や関係部署の担当者にも参画してもらう。
・ブレインストーミング方式を採用する。
・常に「5ゲン主義」、「データ」、「よくみる」で論理的に進める。
(5ゲン主義:3現主義 + 2原主義)
(3現主義: 現場、現物、現実 → 事実の把握)
(2原主義: 原理、原則 → 要因の解析)
その他、個人的に重要視しているのは、要因特定後に『じゃあそれさえなければ、この問題は絶対に起きなかったのか?』と問われた時に「そうです」と言い切れる根拠が成り立つか否かを確認することです。
そこで「実は他にも…」と出てくることがあれば、まだまだ要因は素因数分解しきれていないことを意味します。
また、なぜなぜ分析をする前に必ず事実の整理(層別)を行いましょう。
層別とは、データと同じ共通点や特徴によって、いくつかのグループに分けることを言います。「分ける」ことは、すなわち「分かる」ことです。
たとえば、層別することにより、次のようなことがわかります。
・開発メンバーによって、不良の出方に違いがある。
・利用環境によって、不良のばらつきに違いがある。
層別は、品質管理(Quality control)を進めるうえでとても重要です。まったく異なる層のデータをいっしょくたに分析しようとしても、絶対に期待する答えは返ってこないからです。多くの分析で、第三者が首をかしげるような答えとなっているようなときはいつもこのパターンです。
大抵、物事を一次元的に捉えていて、物事を分解しきれていなかったり、異なる層ごとの分析をしようとしていなかったりしていることが原因です。
①問題を層別に分解し、事実をしっかりつかむ
■事実の確認
・問題が起きたら、まず現場に行く(現場)。
・問題の現物をよくみる(現物)。
(よくみる:見る、視る、観る、看る、診る)
・動きの現実をみる(現実)。
②問題となっている部分の構造(仕組み)や機能(役割)を理解する
■要因の解析(QC手法の活用)
・システム、環境に関する場合はその構造や機能(原理原則)
・業務、手順に関する場合はそのプロセスや流れ、内容(原理原則)
これらはITのみならず、「モノ作り」を生業とする業界であれば如何なる業界であっても同じことが言えます。いわば、エンジニアにとって「常識」の1つにすぎません。
物事が成り立つ原理(理論)で、構造(仕組み)や機能(役割)を見る、また原則(規則、標準類)に照らして、構造(仕組み)や機能(役割)を見ると、必ず真因が見えてきます。
ですから、自分たちの作っているモノの「品質とは?」に対して、
"無頓着な人"
"理解が乏しい人"
"答えを持っていない人"
にとってなぜなぜ分析は鬼門と言えるでしょう。
「エンジニア=ただ作っていればいい」
「仕事=言われたことを忠実にこなす」
「よくわからないけど、とにかく金を稼いでくるのが仕事」
と思っていた人は、おそらくこの答えを持っていないはずです。
・情報の収集・整理のポイントとして、主観(先入観固定概念、推測)に
走らず、客観的に事実を確認しながら情報を収集・整理すること。
・情報は、「何が」「どこで」「いつ」「どの程度」の4つの次元に絞り
収集・整理すること。
・なぜなぜ分析では問題・現象を発生させている要因を、経験・勘・度胸や
思いつきで考えるのではなく、論理的(手順に沿って、順序よく漏れなく
出し切る)な分析すること。
・再発防止対策につながるまで、なぜなぜを繰り返すこと。
5回と言うのは深堀りの目安であって、必ずしも5回にこだわらない。
・突発不具合に対しては「なぜなぜ分析」が有効。
しかし慢性不具合には向かない。慢性不具合には「PM分析」が有効。
・なぜなぜ分析には「特性要因図」「連関図」を用いるのではなく、
「要因系の系統図」や「なぜなぜ分析シート」を活用すること。
・なぜなぜ分析は、問題現象を発生させている要因を論理的(手順に
沿って順序よく、漏れなく出し切る)に分析する方法。
・なぜなぜ分析の実施には、情報がなければ判断(原因究明)は不可能。
・間違った情報や不足した情報からは、問題を正しく判断することは困難。
・なぜなぜ分析には、特性に関する専門知識、固有技術・力量がなければ、
要因の洗い出しは現実的に困難。
このことをどれだけ理解し、どれだけ環境を整え、どれだけ準備できるかがなぜなぜ分析の結果に大きな影響を与えるということを知っておかないと、いつまで経っても上手く活用することは難しいかもしれません。
いただいたサポートは、全額本noteへの執筆…記載活動、およびそのための情報収集活動に使わせていただきます。