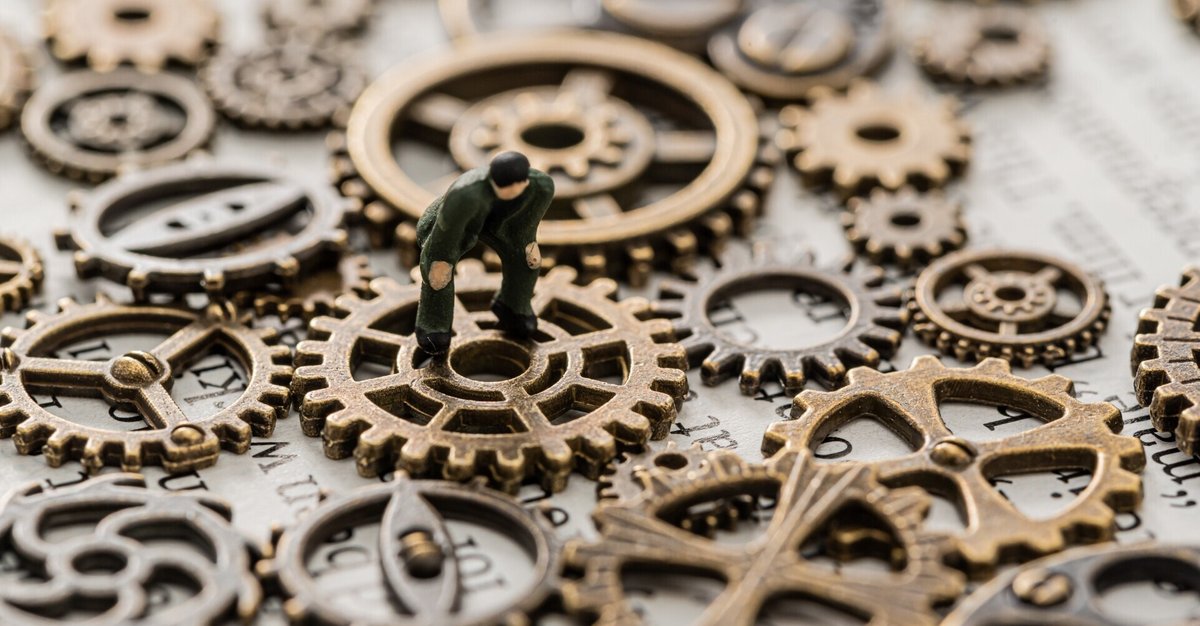
昨日は、ドイツ設備の生産性の高さを少し紹介しましたが、今日は自分の過去の仕事の内容をお話ししたいと思います。
製造技術者にとって設備を新規に購入することは基本的であり、重要であり、大切な業務です。私が初めて設備導入をしたのは、入社して3年目のことです。
当時は、設備導入をするのはベテランの人の仕事であって、まだまだ自分の出番ではないと思っていましたが、急にその番が回ってきました。しかも、一度に違う種類の設備が3台も必要で、我が社初の設備、初の技術、初の工法という、初めてづくしの設備導入だった上に、1台は海外製設備。当時私はその工法に携わったこともなく、おいおい、どうするねん、俺、測定結果の見方もわからんのに・・・と途方に暮れる思いだったのを今でも覚えています。
ですが、この仕事は本当にチャレンジングで、よくこれを入社後数年の新人と同等なヤツにやらせたな、と今では思います。当時、ビビりまくっていた私に向かって当時の先輩(後の上司)が言った「俺がやりたいくらいだよ」というセリフを今でも覚えています。当時は、なんちゅうこと言うねん、ほならあんたがやってくれよ、と思っていましたが、そのセリフからもどれだけチャレンジグでやりがいのある仕事だったかがわかります。
まずは1台目の高周波焼き入れ。これもまた難しかった。高周波焼き入れは以前からやっていたのですが、初めての部位に適用するということで、基礎となる情報はありません。メーカーさんにも手伝ってもらってテストを進めましたが、当時高周波焼き入れって何よ?くらいの知識しかなかったので、今から思えばそりゃそうなるわな、というようなトラブルが続出しました。
専門家であるはずの設備メーカーの人も、意外とアドバイスをくれないんですよね。設備メーカーは少量しか扱っていない場合が多く、量産になった時にどういうところに注意しないといけないか、ということを知らない人が意外と多いように思います。
その時もそんな感じで、とりあえず図面を満足させることはできても、量産設備にどのような仕様を織り込めばよいか、というようなアドバイスはほとんどもらえませんでした。
しかも高周波焼き入れ、というか、熱処理の検査ってすごく時間がかかるんですよ。だからトライをやって測定、トライをやって測定、という作業にすごく時間がかかる。トライはほんの数秒で終わるのですが、1つ測定するのに1時間くらいかかる。夜中までやっても思ったような効果が得られず、1人でずっと測定していると、本当に泣きそうになります。たぶん、高周波焼き入れに携わったことがある人ならば誰しも経験があると思います。
こうやって少しずつ経験を積んでいく中で、いかに失敗を繰り返さないように、他の人が同じ苦労をしないようにするか、次の設備にはどのような仕様を織り込んでいけばよいか、というのを考えることに集中するようになりました。そういう経験を通して、次の人がやっても失敗しないような標準化が私の考え方のベースになっていったのだと思います。
まだ話足りないので、続きはまた明日以降にしたいと思います。
この記事が気に入ったらサポートをしてみませんか?