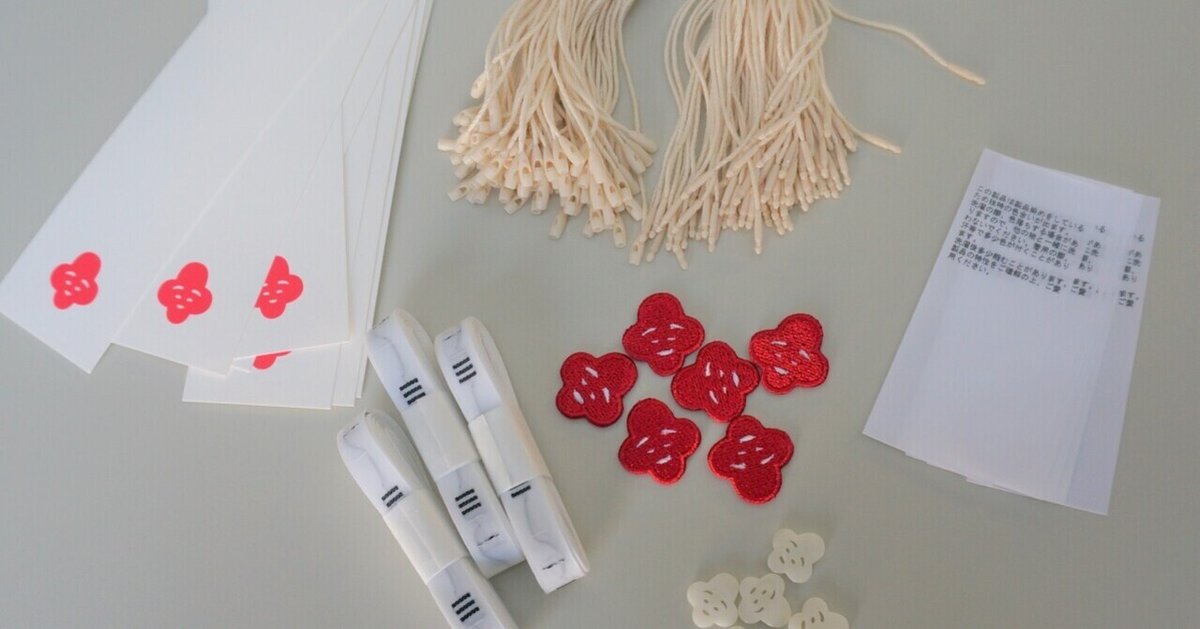
精巧 市場連動生産ストーリー(4)
精巧 市場連動生産ストーリー(4)
こんにちは 近江です。
今回はトヨタ生産システムの導入について、具体的な成果を交えてお話しさせていただきます。
◆トヨタ生産システム(TSS)とは
トヨタ生産方式は、自動車産業や工業製品の工場生産現場のためのものと誤解されがちですが、アパレルのような手工業製品を含めた多くの産業、さまざまな現場の仕事のしかたにも生産性向上をもたらす発想です。
特徴は、サプライチェーンにおける7つのムダ(※)を排除し、生産の都合ではなく、需要のあるものを必要な分だけを作り足す、ジャスト・イン・タイム方式でモノづくりを行おうというものです。
※7つのムダとは・・・作り過ぎのムダ、手待ちのムダ、運搬のムダ、加工そのもののムダ、在庫のムダ、動作のムダ、不良をつくるムダのこと。
生産工程において、設定した目標に向かって、徹底的に無駄を省き、自分の頭で考える少数精鋭のスタッフが、技術を身に着けて成長しながら、生産性を高めてゆくという取り組みです。
当社で取り入れて、成果を上げたトヨタ生産システム(TSS)の特徴を3つお伝えしましょう。
まず、ひとつめは、1日分の生産目標とそれに必要な材料のみを揃えて、生産ラインに投入するという発想です。
TSSでは、当日の生産目標に対して、必要な材料だけを生産ラインに投入します。
多くの工場現場では、過去に余った資材が残っていたり、明日以降の生産に必要な資材が早めに届いて、工場スペースを占領していることが少なからずあります。しかし、TSSでは、そういった、当日不要な素材が現場で混在して、スタッフの手間をかけて目標達成や生産性向上の障害にならないように、原材料の投入コントロールを行います。
これにより、生産ラインのチーム全体にとって、1日の製品生産目標数のゴールが明確になると共に、不要な作業や雑念が発生しないことで、ムダなく、ムリなく、チーム全員が目標に集中できるのです。
ふたつめは、単能工から多能工への作業転換です。
従来は、一人のオペレーターが1日中、同じミシンに座って1つの工程だけを受け持っていました。この方式を単能工と呼びます。納期が十分にある、大人数による、人海戦術的な大量生産には適しているかも知れません。
しかしながら、納期と進捗が管理しづらい、問題が起こっても、その発覚に時間がかかり、リカバリーするのに時間がかかるというデメリットがあります。そのため、問題が起こると納期が遅れるか、あるいは、それを想定して、問題対処を見込んだ十分なリードタイムを確保しておかなければならないものでした。
これに対して、多能工とは一人のオペレーターが複数のパーツをこなせるように訓練し、製品の工程順に並べた立ちミシン(座りミシンよりもミシン本体の作業位置が高い)に沿って、オペレーターは立ったたまま、ひとつの工程を終えると、その後、となりのミシンに横移動しながら、連続する複数の別の工程も行うものです。一人が複数のパートを受け持つようにし、いくつかの工程を終えたら、次の人にバトンタッチして行くようにし、流れ作業で製品を1枚ずつ完成させて行きます。
この方式のメリットは、単能工よりも少人数で、完成品を仕上げることができること、それぞれのパーツが縫い上がった後の待ち時間が大幅に短縮できると共に、時間のかかる工程の作業をチームでカバーし合えることです。
更に、多能工になったオペレーターは、単能工よりも付加価値の高い仕事ができる、つまり、技術を身に着け、前後の工程に配慮のできるプロファッショナル人材に育つことが大きなメリットです。
3つめは、この方式を採用することによって、問題解決のスピードが速くなることです。
従来はパーツごとに完成させ、次の工程に進み、納期の直前に一気に組み立てて、製品を完成させる流れに対して、TSSでは、1枚ずつ、毎日、完成品が出来上がって行くのが特徴です。
つまり、「仕掛品を積み上げる」のではなく、「毎日完成品を仕上げて行く」つくり方です。
完成品が出来上がるスピードが速い、つまり、製品の頭出しが早いということは、不良箇所など問題点にもいち早く気づくことができます。
従来の生産方式と比べて、問題の早期発見、早期対処が可能になるため、問題が発覚したら、一旦、生産ラインを止めてでも、根本的に修正をかけ、再スタートをすることも可能です。
従来のやり方では、問題点が納期直前に発覚して、すでに大量に進んでしまったところをやり直したりして、納期遅れの原因になることが多かったのと比べると、格段に納期と品質が保てるメリットがあるわけです。
日々のゴール、最終納期に向けて、進捗度の確認がしやすいですし、毎日完成品が出来上がるため、後ほど詳しく触れますが、少ロット・短期生産にも適しているのです。
◆トヨタ生産システム(TSS)は間接部門以外でも活用できる仕事術
このTSSの考え方は工場現場のみならず、本社(東京・両国)の間接部門の業務でも活かすことができています。
まずは、本社で製品の生産ロットごとに必要な主素材、附属、関連資材を集め、1回の生産に必要な分だけをまとめて工場に投入することで、「工場現場には無駄なものを送らない」制御ができています。
本社側で投入コントロールをするにあたっても、無駄な資材がー滞留しないように、素材メーカーや資材メーカーさんにも理解、協力してもらい、必要ロットごとの納入納期を遵守してもらっています。
また、社内での「動作のムダ」もなくなるように習慣づけています。
「一度掴んだものは最後まで完結させる」ことを習慣づけているため、当社のテーブルやキャビネットの上に終業時には、何も置いていません。
仕事の終わりと同時に片付くため、すぐに次の仕事に取り掛かれるというのは大きなメリットです。
このように見て行くと、TSSは生産現場だけではなく、多くの場面で応用できる「考え方」と言えそうです。
◆全体を俯瞰(ふかん)して見せることで起こる自発的カイゼン
今、工場では何が起こっているのか?つまり、今、どんな商品を生産中で、次にどんな商品にかかる予定なのか、工場の工程を全体を俯瞰して社員に見せる「大日程計画」の発想もTSSから学んだことでした。
「大日程計画」とは、工場のラインごと、時系列に表された計画表。どこが埋まっていて、どこが空いているのかを可視化したもので、日々、確認しながら、更新しています。社員だれもが閲覧できます。
そして、目の前の優先順位の高い、なおかつすぐにできることから手をつけるのが当社のポリシーです。
「大日程計画」を共有することで、黙っていても営業マンも考え、動き出します。
得意先と約束した納期はすぐに回答でき、・・・
その結果は納期遅れの激減と生産性の向上でした。
TSSの導入の成果はみるみる現れ、当社の生産性は上がり、納期遅れはなくなりました。
次回は、販売に必要な在庫と店頭に必要な安全在庫分だけをつくり足す、「市場連動生産」についてお話させていただきます。
精巧株式会社のHPはこちら http://seiko-co.co.jp/
この記事が気に入ったらサポートをしてみませんか?