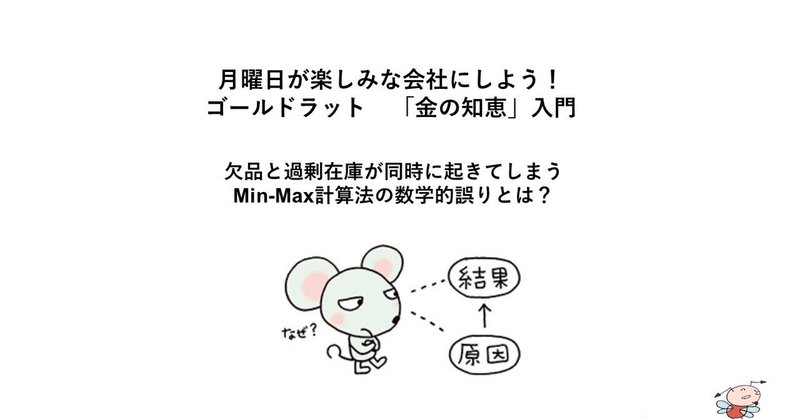
欠品と過剰在庫が同時に起きてしまうMin-Max計算法の数学的誤りとは?
「欠品を出してやる!」とか「過剰在庫を出してやる!」
と思って仕事をしている人はいないですよね?
でも、欠品や過剰在庫をしてしまいます。
どうして欠品や過剰在庫が起こると思いますか?
よく利用されているMin-Maxという計算方法そのものに
アルゴリズムに誤りがあったらどうでしょうか?
これが原因で世界中で欠品とか過剰在庫が起きるのです。
妻と一緒に買い物に行ったときに二人で話していたのですが、
欲しいものが売り切れって年中あるんです。
それどころか、欲しいものが揃ったってことがないんです。
ということは、日常的に欠品してるんですよね。
でも、小売業者は「欠品していない」って言います。
小売業者が欠品していないと言うのは
欠品したものをリストから外すからです。
欠品をなかったことにして売り切れって言うようです。
欠品や過剰在庫引き起こすことは
人間の間違いじゃなくて
コンピューターに入っているアルゴリズムの間違いだったらどうでしょう?
Min-Maxは誤り?
Min-Maxの仕組みについて見ていきましょう。
実はMin-Maxシステムって60年も前のものなんです。
それが今も標準として使われています。
60年間も同じルールを使っているってどうですか?
数学的に言うと明らかに間違っているんです。
60年前のコンピューターで可能な算数のレベルでやってるんです。
Min-Maxには基本設計があります。
直近のある定めた監視期間の平均消費数が主要なパラメータである。
平均消費数に、補充リードタイムと発注単位と安全係数を組み合わせ て、在庫定数(Min値、Max値)を決める。
消費のバラツキ(標準偏差)、陳列スペースの大きさ、過剰在庫や欠品時の損失ダメージバランスなどを勘案して安全係数を決める。
KKD(過去の勘と経験と度胸)で安全係数を決めているんですね。
Min値を下回ったら発注をして、納入されるまでしばらく消費が続いて
納入されたら一気に在庫数が上がる。
こうやって欠品しないようにしているんですね。
次は監視期間のジレンマについてお話しします。
監視期間についてジレンマがあるんです。
「監視期間を長くとるのか短くとるのか」
欠品と過剰在庫を同時に防止し続けるためには、在庫定数がノイズに振り回されない必要があるんです。そのためには、長い期間の消費平均を使うべきとなります。
例えば4週間ずつ、過去の消費を見ていくとトレンドを掴むことができますよね。
一方で欠品と過剰在庫を同時に防止し続けるためには、現実の変化に素早く反応する必要があります。そのためには、短い期間の消費平均を使う必要がある。1週間とか、短い期間で見ていくという方法もあります。
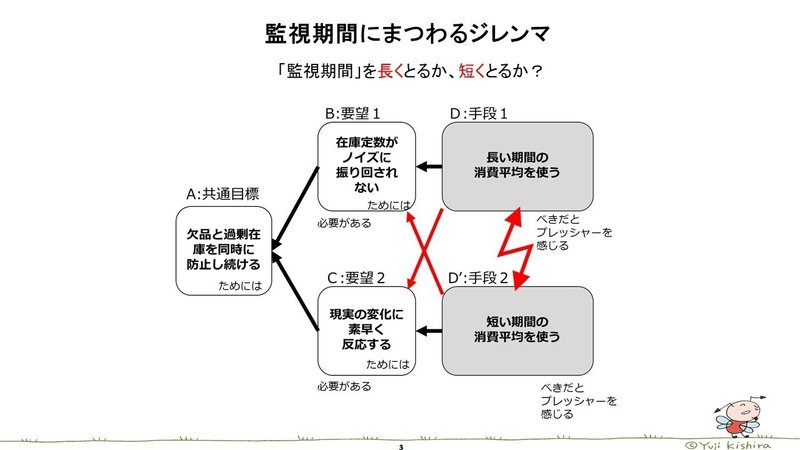
長い期間で見るのか、短い期間で見るのか、これがまだ未解決である。
そこは各企業のノウハウでパラメーター設定してるんですね。
それが実は問題になっているのではないでしょうか?
長い期間、4週間のデータを使った例を見ていきましょう。
長い監視期間の消費平均を使うとノイズへは反応しづらくなる。
ただ、急な変化を捉えられない。それで、現実の変化に素早くついていけないということになってしまいます。
在庫定数は消費平均のX日分(例えば5日分)持ってるんですけど
在庫定数は比較的ゆっくり変化変化します。
消費は変動し続けているので、消費の急激な増加に在庫定数の調整が追い付かないことが出てきてしまいます。そうすると欠品してしまう恐れが出てきてしまいます。下のグラフの赤矢印の部分ですね。
一方で消費の急激な減少に在庫定数の調整が追い付かない。そうすると過剰在庫になってしまいます。下のグラフの緑矢印の部分になります。
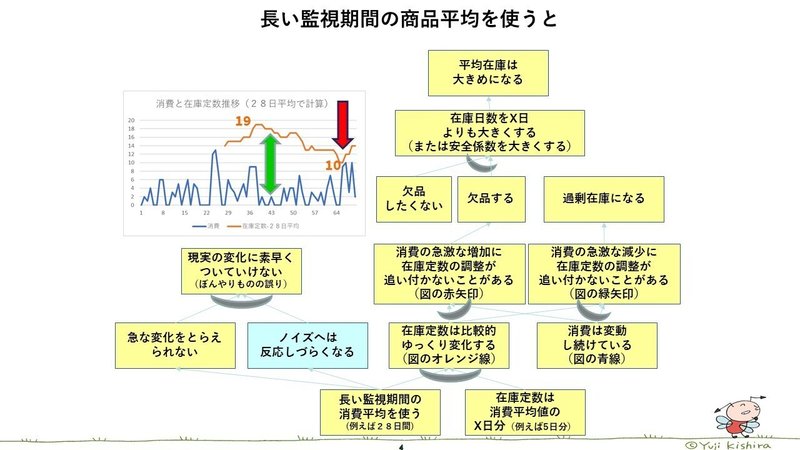
欠品すると「なんでだー!」って怒られるし、
過剰在庫でも「なんでだー!」って怒られる。
欠品と過剰在庫だと、どっちが怒られますか?
欠品したら「なんでないんだー!!」って大騒ぎになりますよね。
欠品したくないので安全在庫を多めに持つ。
人間ですから、やっぱり怒られたくないですよね。
なので、欠品しないように人は動いてしまうんです。
短い監視期間を使うとどうなるでしょうか?
短い監視期間、例えば7日間を使うと変化に素早く反応できますが、
1日のインパクトが大きくなる。
なので、ノイズにも過剰に反応してしまいます。
一方で在庫定数は比較的素早く反応します。
すると、在庫定数が低いタイミングと消費が多いタイミングが重なることがあります。
下のグラフの赤矢印の部分です。そうすると欠品になりますね。
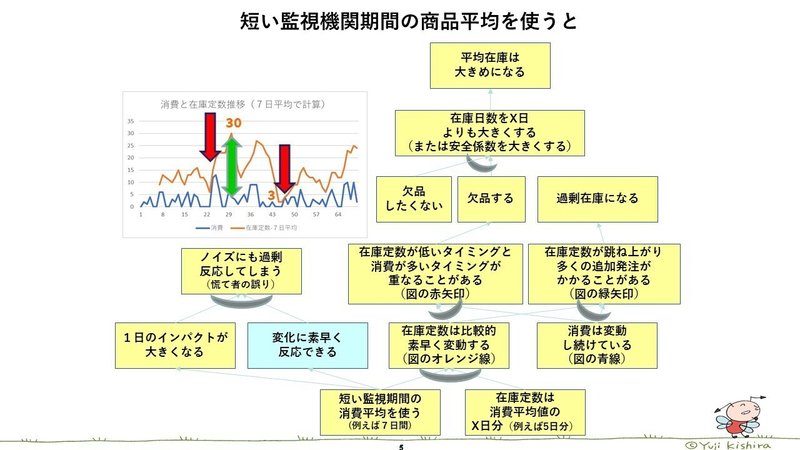
また、在庫定数が跳ね上がり、多くの追加発注がかかることもあるんです。足りない、足りない、足りない、、、となって発注される。
そうすると過剰在庫になりますね。
さて、欠品と過剰在庫、どちらが怒られますか?
やはり欠品ですよね。それで平均在庫が大きくなってしまいます。
Min-Maxをジレンマを解消する
このジレンマを解消するために
「在庫定義がノイズに振り回されない」「現実の変化に素早く反応する」
そのためには浸食面積を色でとらえるというのはどうでしょうか?
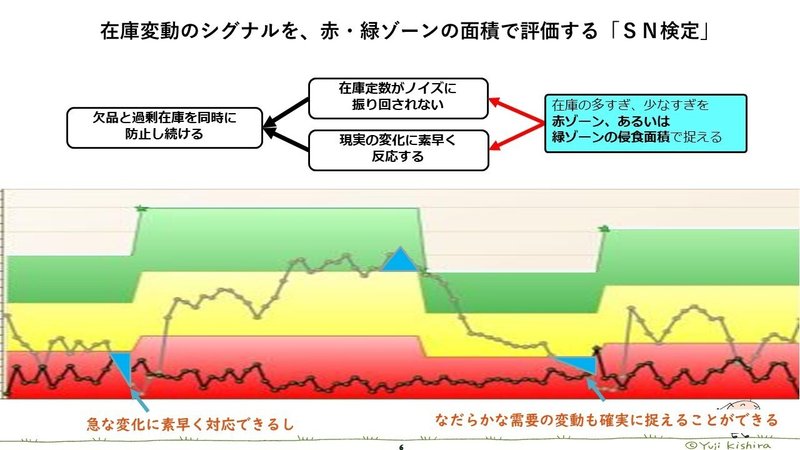
Min-Maxは算数だったのですが、これは積分です。
多すぎ、少なすぎを面積で測れば、ノイズに振り回されずに変化に素早く反応できます。ノイズとシグナルというのがあるのですが、品質管理の世界では常識です。
じょうごの実験ってご存じですか?
じょうごに色が付いたビーズを落としていくと、毎回落ちたところがばらつきますよね。
ばらつきを抑えるため右に行ったら左に、左に行ったら右に調整すると、どんどんばらつきが広がるんです。
これがノイズに反応してしまっているということです。
統計的変動(変動的要因)と特殊要因を分けましょう。
シグナルが出たから反応しましょう。
ノイズとシグナルを分けましょうと言った方法です。
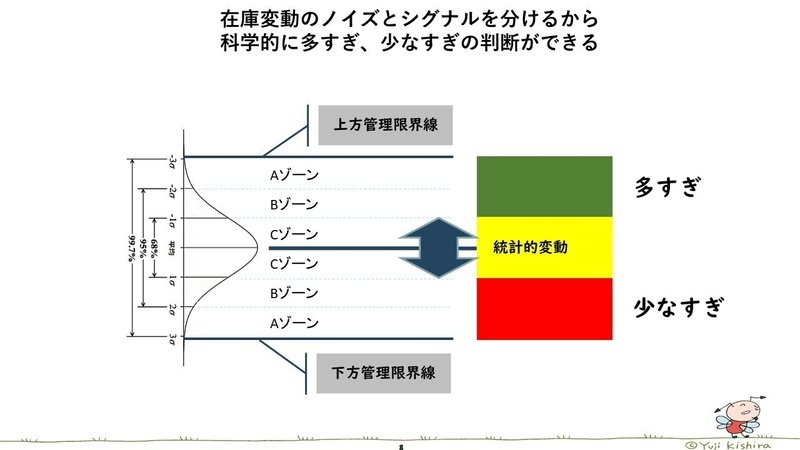
品質管理やモノづくりをやってる方なら常識的に使っている。
Xber-s管理図とか言われる管理図ですが、
色を分けておいて、大きな乖離がでたら対応するというのは
当たり前にやっていることですよね。
このシグナルとノイズを分けるということをやったらどうなるでしょうか。
シグナルとノイズの分離が大切であるという考えを使うとどうなるか。
1シグマ、つまり統計的変動といわれるばらつきと、それを越えたときのシグナルで分けることができます。
DBMは、ノイズとシグナルを分離する許容区分を在庫のばらつきが変化し続ける環境に合わせて調整し続けます。
これにより、シューハートの管理図の適用範囲を拡大しているのです。
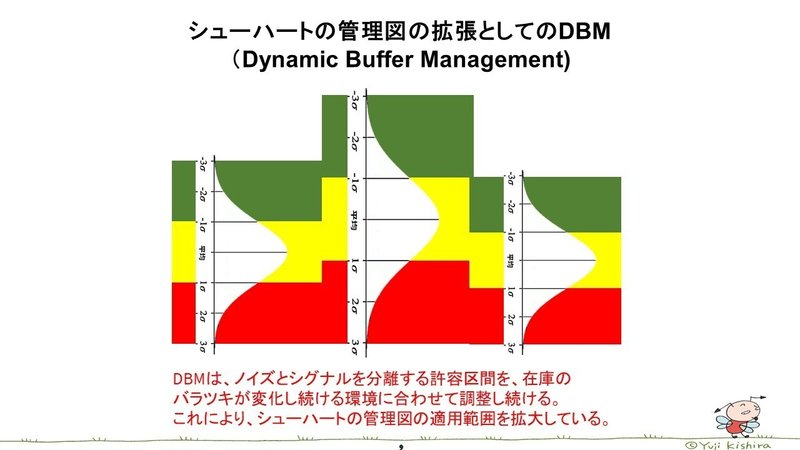
つまりノイズとシグナルを分けるという、品質管理の知見は在庫管理にも使えるのです。コンピューターの中のアルゴリズムだけで欠品と過剰在庫を解消することができたら素晴らしくないですか?
現場も売れていることが分かれば、言われなくても作ろうと思いますよね。
どの色が優先か誰でもわかり、売れ行きが分かるとモチベーションも上がる。店頭で行っていることが工場までわかると、全体最適のサプライチェーンとなります。
より正しい公式を使った方が、結果はよりよくなる。
誤った公式がらはやっぱり誤った答えが出てくる。
ずっとそういう状況があるのであれば、公式そのものを疑う必要があったってことですね。
◆Onebeatを導入した事例を知りたい方はこちら↓
https://www.1beatjapan.com/casestudy?utm_source=note&utm_medium=casestudy&utm_id=20240222_1200note
◆過剰在庫と欠品を防ぐためのお役立ち動画を視聴したい方はこちら↓
https://www.1beatjapan.com/video?utm_source=note&utm_medium=video&utm_id=20240222_1200note
◆Onebeatのカタログ請求をしたい方はこちら↓
https://form.k3r.jp/goldrattjapan/brochure?utm_source=note&utm_medium=video&utm_id=20240222_1200note
この記事が気に入ったらサポートをしてみませんか?