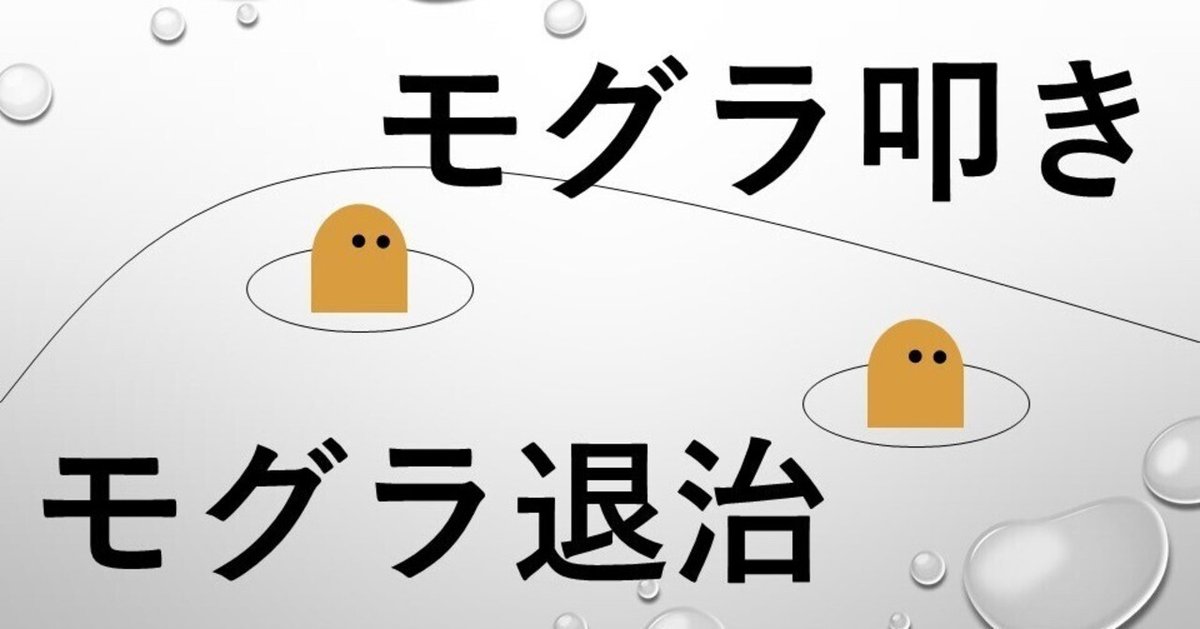
苦痛から解放!トラブル解決はこの2つ
品質管理はサボってもバレないことが多いことから、考え方が重要である旨を前回記しました。
正しい結果を出したければ、正しい思考(考え方)と、正しい行動を取ることであり、以下のように整理しておきましょう。
《 結果 = 思考 ✕ 行動 》
思考はマイナス10(間違った考え)からプラス10(正しい考え)
行動は0(何もしない)からプラス10(実行する)
従って、結果はマイナス100からプラス100になります。
品質管理に限らず、良い結果を出したければ思考と行動に分けると、改善に向けたヒントが掴める可能性が高くなります。
さて、得たい結果(品質目標の達成)を実現するために参考にして欲しい思考と行動を、品質管理の10原則として記します。
1 品質第一の原則 品質を最優先として生産する
2 顧客志向の原則 顧客の要求満足(CS)を考え方の基本とする
3 プロセス重視の原則 仕事の質的向上で継続的にCSを実現する
4 不良ゼロの原則 常に品質トラブルゼロに向けて努力する
5 【 】の原則
6 【 】の原則
7 3現主義の原則 事実に基づいてトラブルを解決する
8 原因対策の原則 真因を追究し対策する
9 類推の原則 類似点から他を推し量ることでトラブルを防止する
10 標準化の原則 誰でも同じ結果が期待できる仕事の仕方を決める
どれも必要な思考ですが、この上位にある経営の目的は、顧客満足(CS:Customet Satisfaction)だけではないことを知りましょう。
もうひとつの目的は、品質コストを下げることですが、3つある品質コストについては次回記載する予定です。
品質コストを下げることで、ムダな手間とお金を使わない会社になり、原価低減に直結することを押さえておきましょう。
従って「24のムダ」の中に「不良のムダ」があり、
(20231221版https://note.com/kid839/n/n42e67a3cb1a3)
不良を造らないことはムダな原価を使わない有効な一手なのです。
さて、品質管理10原則の中で、【 】が2箇所ありました。
この2つは、私が「不良ゼロの二本柱」と強調して伝え、企業様の品質改善を支援し、実績を挙げています。
不良をゼロにしたければ、闇雲に改善するのではなく、この二本柱を知り、そこに技術と技能を集中させ、100個造ったら100個良品の品質システムを構築します。
《 結果 = 思考 ✕ 行動 》を再確認し、
「不良ゼロの二本柱」の思考で、具体的行動に移せば、必ず得たい結果が実現します。
ところで、そもそも「不良ゼロ」はムリと言う方もいますが、私は「100個連続でゼロ」「午前中ゼロ」「1日ゼロ」「1ロットゼロ」「今週ゼロ」「ゼロの月を3ヶ月」などと、努力すれば届くレベルのゼロを目標にして欲しいと提案しています。
例えば、死者数半減という目標は間違っていると考えます。
死者ゼロが原則であり、前出の「不良ゼロの原則」を忠実に実践するよう導いています。
その「不良ゼロの原則」に従い、現場レベルで実践する「不良ゼロの二本柱」を、説明用資料を添付したファイルを載せて紹介します。
この二本柱は、私がソニーでの実務及び指導者の立場として30年超現場を体験し、不良ゼロ実現に向けて必須と考え続けている2大要素です。
製造業は「正しく造れば、正しいモノができる」ことを知り、後半もお付き合いください。
(領収書発行はお申し付けください)
この記事が気に入ったらサポートをしてみませんか?