メーカーの棚卸と消える在庫
はじめに
けーる@ke_ru_noyounamoと申します。
Twitterで様々な人に励ましてもらいながら、何とか東証プライム経理へ転職できることになりました。ありがとうございました。
いつも色んな人の話を一方的に拝見しているのですが、私も何か面白い話を提供できないか?考えてみたところ、表題の話がもしかしたらウケるかもしれないなと思い書くことにしました。
前提条件として、
・売上原価対立法、かつ予定消費単価を用いて売上原価を算定
・バックフラッシュと工程間受け払いは無し
という前提で話を進めます。
私は東証プライム上場の子会社(売上は数千億円規模)で工場経理っぽい仕事をしていて、親会社開発のシステムを親子揃って使用していましたが、上記の状況で何年も棚卸差損とその解析に苦しめられたためです。
(解析もクソもなかったです。。)
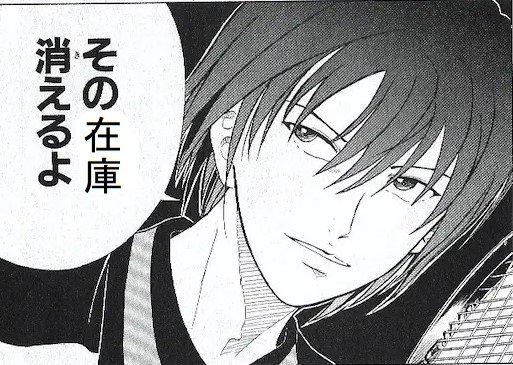
メーカー経理をやったことが無い方も、世の中の同じような悩みを抱えているメーカー経理の方も、楽しんでいただけたら幸いです。
そもそもバックフラッシュや工程間受け払いを導入しないのは何故か?
ちゃんとしたメーカー経理の方であれば至極まっとうな意見だと思いますが、私はバックフラッシュや工程間受け払いをきちんとやらない、導入しないメーカーの方が多数派なのではないかと思います。
バックフラッシュとは?
売上が計上された製品をBOM(部品表)でバラシ、上流工程へ遡って理論的・データ的にどの工程に、部品が何個通ったはず、と在庫の流れを追えるように見える化することです。
(例:製品Aが売上100個→部品Bが200個、工程Cを通過したはず)
帳簿在庫を理論上は工程単位で見えるようになるはず、ということですね。
生産管理が仕入先に部品を発注する際に、完成品の予定生産数量→必要な発注数を計算する必要がありますが、これがシステム化されていれば似たようなシステムかもしれません。
この発注数の計算とシステム的に異なるのは、不良の加味の仕方です。
生産管理は不良が多い工程があれば、
①システムでバラシた必要発注数にハンドで追加する。
②その工程のバラす際に変数をかける。
(特定の部品のバラシ数を本来の数×1.nなど)
いずれかの選択を行うことが多いはずです。
これに対し、バックフラッシュは帳簿在庫の流れを見える化するために、実際に発生した不良品を
①正確な部品品番
②発生した工程
③発生した個数
の上記3点を正確に記録し、データへ反映する必要があります。
これを行うためには工数やコストがかかります。
例えば、仕掛品の部品品番がちゃんと設定されており、BOMに組み込まれているか?
この部品品番の設定は、設計などが担当している場合が多いと思いますが、彼らが求められていることは、
①製品が要求品質を満たす図面になっているか?
②材料や作りがコストのかかるものになっていないか?
あたりで、実際の製造工程における管理のしやすさまで考えが及んでいないことが多いです。このため、正確な部品組付け・製造状況を廃却データに反映できていないことがしばしば起こりえます。(=BOMと原価計算⇔実際に組み付いた部品とがアンマッチになり、帳簿在庫の払い出しが過大・過小になりうる。)
また、実際に製造する従業員の方が、
②実際に発生した工程で
③正確な個数を記録する
のも難しいです。
というのも、実際に製造に携わる方は出来高を常に問われており、生産効率向上を重視しています。このため、廃却データの作成など自分の評価に直結しない作業に工数を割くことを嫌がります。
また、経営サイドからしても、廃却データの精度を上げるために人員や工数を割くことはコスト以外の何ものでもなく、不良品が社外流出せずに不良の原因さえ把握できれば、バックフラッシュなどどうでもよいというスタンスでも否定できません。
更に言えばバックフラッシュはあくまで遡りであるため、後述の消える在庫にとても弱いです。
在庫が消えるとそもそもバックフラッシュをかける始点が存在しないので、思ったような精度が出ず、このためだけにシステム投資をしづらいように思います。
工程間受け払いについて
工程間受け払いがしっかりデータとして取れていれば、棚卸関連で悩むことはぐっと減る印象があります。
(在庫が消えた箇所と日時が可視化され、原因追求が容易なため。)
ただし、工程間受け払いのデータを取るのも全てコストになります。投入数や完成品の数、不良品の数、これらをデータとして取るのが人であろうが、機械であろうが、その分のランニングコスト or 投資が必要になってきます。
メーカーにおける投資の優先順位は、研究開発や新工場、新型生産設備などの優先順位が圧倒的に高く、受け払いのためにコストを割けるメーカーは限られてくるのではないでしょうか?
メーカーは業界にもよりますが、原材料費+購入部品費+外注加工費の合計の売上高比の費用比率が約65%〜75%、売上総利益率が20%前後でやっと営業利益率が3%~5%が見えてくる薄利多売のメーカーが多いというのが個人的な感覚です。
不正リスクが一定程度排除できているのであれば、受け払いにコストを割くのは社内的にも理解が得られにくいはずです。
少なくとも私が在籍していたメーカーでは、親子揃ってシステムの刷新が検討されていましたが、現状の帳簿在庫周りの焼き直しのみで、実際の受け払いについては1度たりとも話題になっていませんでした。
(退職を決意した要因とも言えます。。)
在庫が消える様々な要因
さて、皆さんご存知の通り在庫は消えます。
私が経験した消える要因をいくつか紹介して、このコラムっぽい何かを終わろうと思います。
消える要因①BOMが実態を反映しきれていない
例えば、生産能力等の都合上、同じ部品を複数の工程で生産している場合、その単価差がきちんと帳簿在庫から払い出されてるか?を注意する必要があります。
(例:部品Aを、仕入先BとCから6:4で仕入ており、単価差がある。)
仕入先の生産能力の都合によるもので、片方に寄せようとすると投資が必要になり、その投資分の値上げを要求されたりするため、割と起こりえます。
(モデルチェンジの間隔などで投資させてもメリットが出ない、BCP的にも複数の仕入先を持っておきたい.etc)
この問題は、社内でも注意が必要です。
例えば樹脂の射出成形機の場合、設備Aでは2個取り、設備Bでは4個取りなど条件が異なる場合です。
(イメージとしては、プラモの部品。熱して溶かした樹脂を型に流し込み、冷して固める工程です。○個取り=一度に成形できる数)
射出成形は設備によって出力できる圧力の限界があり、また同時に作れる個数が増えるほど、圧力を均一にかけるのが難しくなり、品質的なハードルが上がります。
加えて、2個取りと4個取りでは、材料の無駄になってしまい捨てざるを得ない部分の大きさに差が出ます。
(射出成形機の樹脂が通ってくる経路の部分で差が出ます。イメージとしてはプラモのパーツ群の外枠に相当する部分)
不良品を個別に記録して払い出すのではなく、一定の比率で加味している場合、実態に近い数字になってるか?調べてみてください。
また、在庫が消えるわけではないのですが、複数の製品セグメントに跨がる材料を一括で仕入れて使用している場合、各々の製品セグメントにきちんと仕入データを分けて計上できているか?確認してください。
(スケールメリットを全社で確保しようとする場合に起きがち)
棚卸差損の原因を調査する場合、何ヘクタールもある広大な畑から探すわけにはいかないので、製品セグメント等でどの製品に棚卸差損が多いか?確認してから調査する場合が多いと思いますが、この一括仕入によって帳簿在庫が入り組むと棚卸差損の調査は迷宮入りします。
(あと支給も入り組みを作ってないか見た方がいいです。。マジで。)
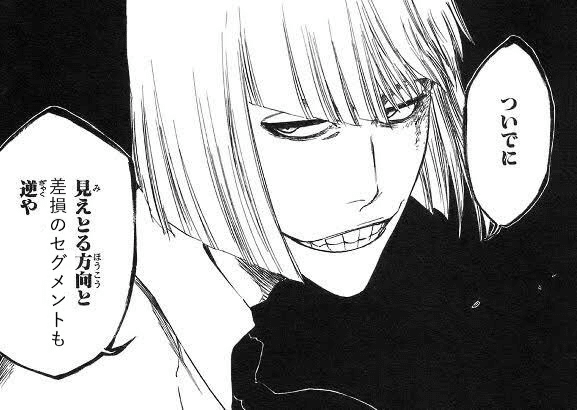
消える要因②社内の泥棒
主に2種類います。
1.品質管理や生産技術、研究開発など自分の仕事に必要なものを、製造と生産管理に許可だけとって、製品・部品を掻っ払っていく人
2.マジもんの泥棒
1の場合、本来は他勘定振替や費用振替によって帳簿在庫から払い出しが必要にも関わらず、伝票計上などの処理を経ずに、製品・部品を持ち出します。
このあたりはしつこく注意喚起をしていくか、伝票を切らずに持ち出すと経理以外も困る仕組みを構築するなどの対策を打っていく必要があります。
工業簿記で言うところの異常仕損は特に要注意で、原因が判明するまで品質管理の指示で廃却を保留するケースがあると思います。
この状態で期末を迎えると、在庫カウント→評価損計上まで注意する必要がありますが、廃却を保留しているものをそもそもカウントする必要があると現場が認識できているケースは少ないと思います。
2はどちらかといえば、東南アジアや新興国を中心とした海外の工場で起こりえます。
経験したケースとしては、監視カメラを映る範囲を認識した上で避け、廃品と混ぜて原材料を持ち出し(回収業者と結託してる)、売り飛ばしていました。
こうした不正リスクは他に詳しい方がいると思うので詳細は割愛しますが、東南アジアはカジュアルに不正がおこるので、対策をオススメします。
(最近発売された佐和周先生の本にも似たような話が書かれてましたね。)
消える要因③各種内部統制の不備
消えるというよりは、もはや注意喚起に近いのですが、ざっと書いて終わりにしようと思います。
原価計算等のシステムの不備
J-SOXなどで監査されると思いますが、それとは別で、金額の大きいもの×製品セグメントで抽出して、BOMと照らし合わせながら原価計算がモレ・ダブりなく計算できているか、チェックしたほうがよいです。
原価計算のシステムはBOM、原価差額と売上原価の計上までと合わさってかなり複雑であると思っており、J-SOXの監査でエラーや不具合を見つけきるのはほぼ不可能です。
闇鍋を解析していると何年も見つかっていない不具合がたまに見つかって、大炎上したりしなかったり。。
棚卸資産の隠蔽
棚卸監査のルート、パターン化されてないでしょうか?
特に儲かっていない工場・会社の場合、設備と設備の間隔が狭く、複数人が歩ける場所が限られているため、ルートがパターン化されがちになります。
数年でぐるぐるしてる場合は要注意です。
ルートを事前に通知せずとも、現場のおっちゃん達に「どうせ来ない」と見透かされるゾーンができあがります。こういったところに変な在庫を隠してるケースがありますので、要注意です。
(フォークリフト使わないと見えないところとか要注意。。)
廃却データの隠蔽
先の盗難もそうですが、不良率を評価指標としてる場合、廃却データを計上せず、こっそり捨てられてることがあるので、注意してください。
私の上司は回収業者からの計量データを見て、廃品データの計上漏れに気づいたことがあります。(げっそり)
大した内容でもないのに、ここまで長々と読んでくださって、ありがとうございました。最後に全然関係ないお気持ちを表明して終わろうと思います。
工場経理としての心得的なもの
工場の地図と棚卸の明細を持って在庫の場所の確認、
あるいはBOM/原価計算明細と製造工程を照らし合わせて見に行く時間を最低月に1度は時間を取った方がいいです。
それで直結する実利があるわけではないのですが、
・場所と在庫の規模感が分かる。
(この場所にこんなに在庫あるわけないやん or 全く無いわけないやん、と稀に気づけます。)
・同じ製品セグメントでも汎用機/専用機や設備の古い/新しい等で加工費の違いが大きく出ることが分かる。
(どちらかといえば、J-SOXなどで説明に役立つ?かも。。)
・山積みにされてる廃却品に気づける。
(これ、ええんか?伝票きったか??頼むで、ほんま。。)
ちなみに製品と会社に愛がないと続かないです。。終
この記事が気に入ったらサポートをしてみませんか?