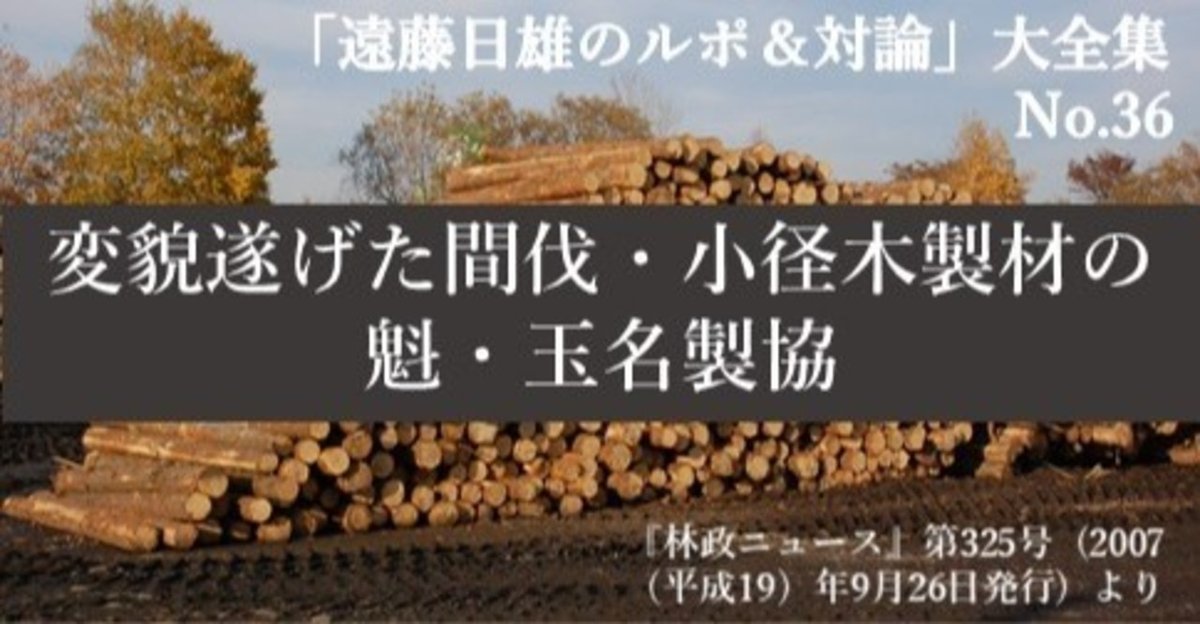
変貌遂げた間伐・小径木製材の魁・玉名製協
昭和50年代前半、国産材製材が役物製材を中心にわが世の春を謳歌していた頃、林野庁は戦後造林した1000万㏊に達する人工林が着実に成熟していることに注目し、それまでの「つくる林業」から「売る林業」へと森林政策を大きく転換させた。「売る林業」体制を確立するためには、まず間伐・小径木の有効利用が不可欠。その先陣を切り、モデルとなったのが昭和52年に設立された玉名製材協業組合(熊本県南関町、以下、「玉名製協」と略称)であった。当時、玉名製協を切り盛りしていたのが、大石駿四郎・代表理事(現在、全木連副会長)である。爾来30年間、玉名製協は時代の荒波にもまれながらも大きく羽ばたき、当初はスギ丸太消費量年間1万5000㎥だった工場も、今では10万㎥を目前にするまでに規模を拡大した。しかも、集成材のラミナ製材を基本とする工場へと変貌した。それは何故か。そして今後の課題は何か。スギを熟知した大石会長に、遠藤日雄・鹿児島大学教授が迫る。
間伐・小径木製材オンリーには不安があった…
遠藤教授
玉名製協は設立当時、大きな反響を巻き起こした。「玉名」の地名は知らなくても、「玉名製協」の名は全国に知れ渡っていると言われたほどだ。
大石会長
「売れない間伐材」をどう製材すれば売れるのか。林野庁、熊本県、製材機械メーカー、大学・国立林業試験場の先生方と一緒になってとことん考え抜いた。
遠藤
当時は手探りの状態だったと思うが。
大石
ツインバンドソーで末口径13㎝以下の間伐・小径木を挽き、9㎝角(母屋)や10・5㎝角(柱)、それに垂木や根太を製材することを基調にした。ただ、間伐・小径木製材オンリーでは不安だったので、台車2台を設置し、受注製材に対応できるようにした。これが現在まで脈々と続いている玉名製協の出発点だ。
ラミナ挽き工場を増設、スギムクはどうしても狂う
その後、玉名製協は第2工場を増設。そして今年6月、第3工場が新設された。いずれもラミナ挽きが基本。第1工場は小径木(末口径16㎝)を、第2工場は中径木(20〜24㎝)を、第3工場は大径木(24〜36㎝)をそれぞれ製材している。
遠藤
今夏、北米西海岸の最新鋭大手製材工場を視察してきた。いずれもセカンドグロス丸太に対応して、製材・加工工程の要所要所にスキャナーを取り付け、太さ、曲がり具合、節、腐れなどを瞬時に読み取り、次の工程に最適の製材方式を指示していた。日本ではそれは無理なのか。
工場の流れを説明する大石会長(右)
大石
外材製材の場合は、例えば丸太の長さが4mあったとして、末口径がほとんど同じだ。ところが国産材、とくにスギの場合は、1本の立木を伐採して玉切っても、元玉、2番玉、…裏木というふうに径級が違う。各玉の歩止まりを考えて効率よく製材するためには、それぞれの径に合った鋸を使うべきだ。
遠藤
日本のスギには特徴があるということか。
大石
そうだ。それを思い知ったのが、柳川(福岡県)の注文住宅用に納材したときだ。海苔業者が住む大変な豪邸で、あらゆる部材を納めた。そこで、スギのムク材は乾燥しようがしまいが、時間がたてば狂うということを身をもって知った。乾燥材でもせいぜい3か月の在庫が限界、それ以上になると時間の経過につれて使えない材が増えてくる。これでは需要の変化に対応できない。
遠藤
ムクKD(人工乾燥)であっても不安が残るということか。
大石
そう断言していい。スギムクKD柱角をつくるには、まず12㎝の粗挽きをして天然乾燥する。その後、修正挽きして10・5㎝角にしても、曲がりや捻れが生じるのは免れ得ない。つまりエンジニアードウッドの要求にはムクでは対応できない。これは長年スギを扱った者でなければわからない経験則だ。
遠藤
その指摘は重要だ。国産材振興策を考える際、この点の議論が欠落したまま、〈ムク派〉対〈集成材派〉といったワイドショー的な意見が出されるケースが多い。
背板利用の幅はぎ板製造が転機になった
間伐・小径木製材から始まって30年、玉名製協は今、集成材用ラミナ専門の製材工場へと変貌した。ラミナの特1等(ピン角)は中国木材(株)伊万里事業所(第 号参照)へ、丸味を帯びたラミナ280はコンパネ用の桟木にしたり、住友林業(株)に納めて木づれパネル(壁下地材)になっている。
遠藤
間伐・小径木製材のパイオニアが、なぜ集成材用ラミナ製材に転換したのか。
大石
昭和60年前後だったと思う。出てくる丸太が間伐・小径木から中目に変わりつつある頃、製材過程で出る背板(「側」)を有効に活用するために、幅はぎ板を製造するようになった。今振り返ってみれば、これがラミナ挽きの原点だったと思う。
遠藤
昭和62年に熊本県で植樹祭があった。あのとき会場で、それまでの合板ではなく熊本県産スギを使った幅はぎ板が使われて話題になったものだった。
大石
植樹祭を契機に幅はぎ板の需要が一気に増えた。大手住宅メーカーもかなり使ってくれた。しかし、阪神大震災の際に、合板のほうが地震(横揺れ)に強いということになり、幅はぎ板の需要は縮小した。そこで問題になったのが、板の使い道だった。
中国木材が救世主、九州全体の丸太流通再編へ
遠藤教授が2年前に玉名製協を訪れたとき、第1工場ではスギ集成平角を製造していた。大石会長の跡を引き継いだ大石彰・代表理事が、スギ集成平角に「E65」を表示したばっかりに、設計基準に合わないという理由で福岡や佐賀の市場では受け入れてもらえないと嘆いていた――そんな“壁”にぶちあたっていた頃だった。
遠藤
スギの集成材製造への転換はスムーズにいったのか。
大石
幅はぎ板の需要が減り、スギをどう利用すればいいのか試行錯誤をする中で、高周波プレスによってうまく積層できることがわかった。これがラミナ製材転換への布石になった。今、振り返ると、製材過程で出る端材処理から幅はぎ板が生まれ、その延長線上に集成材があったということになる。
遠藤
新製品は、かりにつくれるようになっても、安定した販売先を見つけるのが難しい。それなりの苦労があったと思うが。
大石
スギ集成平角が売れず、ラミナの在庫を抱えて途方に暮れていたとき、たまたま中国木材(株)の堀川保幸社長が弊社を訪れた。そこで中国木材伊万里事業所へ、ハイブリッドビーム(米マツとスギの異樹種集成材)用のラミナとして納めないかという提案があった。それからだ、中国木材へのラミナ供給が始まったのは。堀川社長は救世主だった。
遠藤
見えざる神のお導きだ。でも、玉名製協は、スギムク小角製材や幅はぎ板生産過程での貴重な経験があったからこそ集成材製造に辿りつけた。この前過程がなければ、みえざる神は微笑まなかっただろう。最後に、今後の課題は何か。
大石
現在、玉名製協の工場は年間7万6千㎥のスギ丸太を消費している。来年の今頃には10万㎥体制に入っているはず。そこで今後は、九州全体の丸太流通構造の再編に力を入れていきたい。九州は、同じスギ材産地の東北と違って、製材、合板、集成材が緊張関係を維持しながらB材価格を上げている。今後は、製材工場向け、集成材工場向け、合板工場向けの丸太供給システムをそれぞれつくっていくことが大事だ。今、主立った森林所有者とその実現に向けて協議しているところだ。
ラミナを製材するギャングソー
(『林政ニュース』第325号(2007(平成19)年9月26日発行)より)
この記事が気に入ったらサポートをしてみませんか?