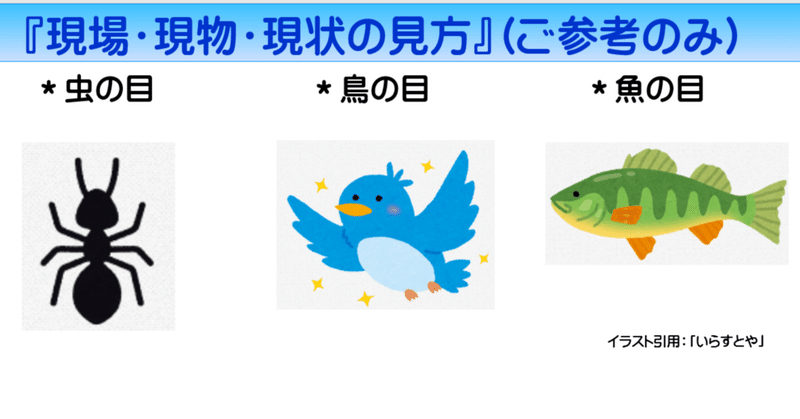
〇品質管理・製造関係者の方へ
私が、新入社員(1978年)から6年くらいは、機械工場の生産技術係でした
会社として「デミング賞を受ける・とる」という目標設定がされて、
品質管理教育をうけるため、毎月・1週間ずつx6か月間=延べ30日、
日科技連の品質管理セミナーベーシックコースに出張教育の機会をいただ
きました
毎月・1週間の缶詰教育を受けて、内容を持ち帰って・3週間の間に実施して、次回の教育の中で発表するという流れがポイント・柱だったと感じます
その後の20年くらい(数社)は「生産技術+品質管理の2つの軸足」で、
「コストダウン&品質保証」が主業務になっていました
したがって、「場内の品質トラブル」「社外クレーム」などは、
かなりのメイン業務となり、「初期対応・工程分析・要因究明・対策実施・
フォローアップ」を沢山、担当&動員してきた経緯があります
従いまして、「工程分析・要因究明」では、数限りなく悩みました
・・・そういう中で、役に立った度合いが高かった手法・やり方を3件
ご紹介しようと思っています
役に立った度合い1位:
*これはダントツで「重点指向」です
・・・あれも・これも・同時に扱うことは、ムリ&非効率的ですね
No1の・一つに絞って・考えて・進めてみると海路が開けます
・・・そして次に、2番目の項目を取り上げる・・・
(パレート図はよく使いました)
役に立った度合い2位:
*やはり単純ですが「時系列のグラフ(層別)」だと思います
・・・データを並べて、視て行くと「おや!?」と引っかかる
ただし、どういうデータを集めるかが超大切で
「量ではなく質」なのです
・・・10件でもよくて、上手に層別する必要があります
必要により「検証データを追加で集める場合」は
立ち会いなどをするくらいに「管理されたデータ」
を集めてください
役に立った度合い3位:
*抽象的に感じるかもしれませんが「現場・現物・現状(3現)」と
思います
・・・(かつてのTV番組ですが「事件は現場で起こっている!」
というフレーズが流行り、通じるところがあるかも)
①現場:
事務所や会議室での検討も必要ですが、現場に行って
自身の直感を使うことも、参考になります(決めつけはNG)
②現物:
これが、「3位」の中ではトップでしょう
壊れた/取り外した部品の現物(捨てられてしまいがち)
この観察・ズーム画像・成分分析などなど、色々ありますね
・・・「現物が 語る事・教えてくれる事」がきっとあります
②現状:
「現物」の周辺の状況・関係者の話・関係者が見逃しているコト
を広角レンズのように視野を広げてみましょう
(関連して見方・視点のたとえ)です:
*虫の目: 小さな虫のように、へばりつくような見方
*鳥の目: 高いところから全体を見渡す見方
*魚の目: 時系列で、さかのぼる/今後を予測する見方
最後に関連図書を1つあげてご紹介します:
*「品質管理の基本」日本経済新聞社 (Amazonで入手可能)
・・・大変コンパクトな1冊にまとまっていて
手元に置いておく「ハンドブックに最適」です
2024.0708
この記事が気に入ったらサポートをしてみませんか?