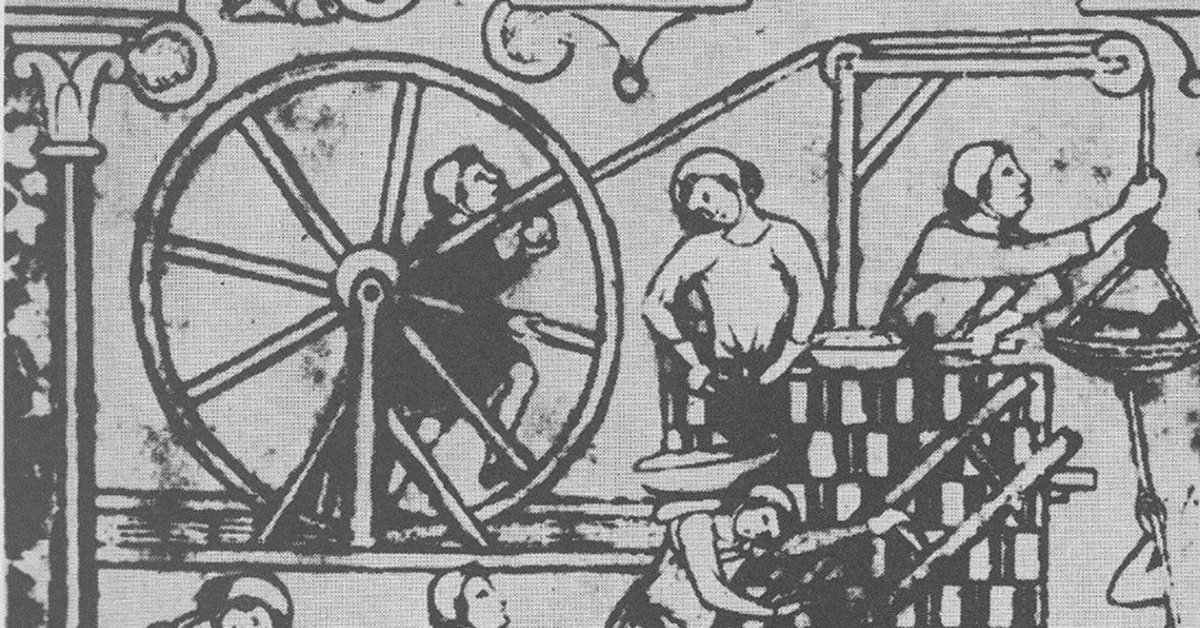
日本の高層建築における施工技術の変遷第2回 揚重
この記事は「建築士2019年1月号」(日本建築士会連合会)に掲載された原稿の文章・図を修正したものです。
ブルネレスキの揚重機械
下図はブルネレスキがフィレンツェのサンタ・マリア・デル・フィオーレ大聖堂のために発明した揚重機械である。牛(スケッチでは馬)が車軸をまわすとギアがかみ合い荷物を上方に運ぶ。これ以前にも人間が大きな輪の中に入り、ハムスターのように輪を回転させ荷物を揚げる等の機械は存在していた(例えばトップの画像は「カテドラルを建てた人びと」ジャン・ジェンペル、SD選書より転載)。
ブルネレスキの揚重機械がさすがルネサンスの幕開けと思わせるのは上下に2つのギアが描かれている点である。中央のギアを上下にすることで、この牛の進む方向を逆転させることなく、荷物を揚げることも降ろすことも可能である。牛はひたすら前に進めば良い。これによって大きな牛に縄を取り付ける手間が大幅に短縮できる。この機械は一日平均50回の揚重を行い、推定3000トンといわれる資材の揚重に大きく貢献した。
図 タッコラが描いたブルネレスキの牛力巻上げ機(フィレンツェ国立図書館、「天才建築家 ブルネレスキ フィレンツェ・花のドームはいかにして建設されたか」、ロス・キング著、田辺希久子訳、2002年、東京書籍より転載)
揚重の重要性
現代の高層建築施工において高所まで資材を運ぶ揚重の重要性は言うまでもない。単純化して考えれば、高さが増えればそれに比例して揚重の距離も量も増えるので、必要な揚重能力は高さの2乗に比例する。
現在、高層建築建設で一般的に使われるタワークレーンが日本に導入されたのは1952,3年頃のことである。清水建設が西独・カイザー社から輸入して東京電力新火力発電所の鉄骨工事に用いたとされる【文献5、6】。初の国産タワークレーンはタワー部をコンクリートで構築したもので、タワー頂部からワイヤーを四方に貼ってタワーを支えていた。自立するタワーを備えたタワークレーンは1962年に開発された。
タワークレーンが登場する以前はマスト、ブームからなるガイデリックやマストを三脚状に構成した三脚デリックが揚重に用いられていた。戦前の丸の内ビルヂング(1923年)ではガイデリック、三井本館(1929年)では三脚デリックが活躍している。丸の内ビルヂングのガイデリックは工事後に清水建設に払い下げられた【文献7】。タワークレーン導入以降も、ホテルニューオータニ本館(1964年、高さ72m)では、平面が三ツ矢型に広がっておりタワークレーンの有効性が低いと判断され、ガイデリック4基と高層部で三脚デリックが使用されている(下写真)。このようにガイデリックや三脚デリックとタワークレーンとの併用期間も見られるが、建築の高層化に従いタワークレーンが一般化していった。
写真 ホテルニューオータニ本館建方「建築生産の技術」(梅村魁編、丸善、1978年)より転載
セルフクライミングのタワークレーン
日本初の超高層・霞が関ビルディング(1968年、高さ147m)ではセルフクライミングのタワークレーンが用いられた。尚、このタワークレーンを製造したのは呉造船所で、戦艦大和を製造したことで知られる。スエズ動乱(1956年)による造船市場縮小を受けて造船各社は陸上部門への進出を図り、呉造船所は、西独シューイング社とクライミングクレーンの技術提携を結び、「呉シューイングクレーン」として製造していた。
霞が関ビルディングで使われたタワークレーンの特徴は、旋回体とマストが分離し、旋回体を躯体に固定したまま、それを貫通してマストがせり上がる「分離式」にある。旋回体とマストを同時にクライミングさせるのではなく、旋回体を躯体に固定することにより、せり上がりの安定性や速度が向上した(図)。結果的に、従来のガイデリックでは6日程度かかっていたクライミングが1日で終了した。霞が関ビルディングでは工事中に9回の迫り上げを行っている。清水建設が施工した初の超高層建築である朝日東海ビル(1971年、高さ110m)では、タワークレーンのクライミングに油圧式の機構が用いられた。それまでのワイヤー式のクライミングに比べて安全性がさらに増し、かかる時間も大幅に短縮できたとされる。
霞が関ビルディングの2分割式セルフクライミングタワークレーン(霞が関ビルディング50年記念誌より転載、三井不動産蔵)
圧送
セルフクライミングのタワークレーンと同じく、揚重において大きな生産性向上を実現したのがコンクリートの圧送である。床のデッキプレート等でコンクリートを打設する場合、コンクリートをどのように上階まで運ぶかが課題となる。霞が関ビルディングでは、バッチャープラントで練られたコンクリートを専用エレベーターで揚重した。スランプ6という固練りのコンクリートであったため、バケットを傾けてもコンクリートが落ちず、ホッパーが用いられた。さらに、揚重したコンクリートの水平搬送のため、14階までは猫車(一輪車)が使われたが、15階以上はコンクリートコンベアによって搬送された(写真)。
霞が関ビルディングのコンクリートコンベア(霞が関ビルディング50年記念誌より転載、三井不動産蔵)
定置式コンクリートポンプによる圧送は、1960年代から導入された、1964年に自走式コンクリートポンプ車が実用化され、1966年にはブーム付きのコンクリートポンプ車が輸入された【文献9】。その後、ポンプ圧送は急激に普及したとされ、圧送業者も急激に増加する一方、圧送中の閉塞など多くのトラブルも発生した。
その後、圧送可能な高さは上昇し、初期の事例として竹中工務店が施工した初の超高層建築である横浜天理教館(1972年、高さ102m)では、コンクリートポンプ車によって最上階までの直接圧送を既に行っている(スランプ21)。一方、日本初の高層鉄筋コンクリート造建築ともされる椎名町アパート(1974年、高さ54m)ではスランプ14の固練りのコンクリートを打設するためバケットによる揚重がなされた。徐々にコンクリートポンプの能力が向上すると、比較的固練りのコンクリートでも圧送が可能になり、新宿グリーンタワービル(1986年、高さ109m)ではスランプ18のコンクリートを最上階まで圧送している。現在、日本で最も高いあべのハルカス(2014年、高さ300m)でも最上階まで軽量コンクリートの超高所圧送を実現しているが、これはスランプ23のコンクリートの大臣認定を取得したものである。また、揚重とは異なるが、CFT構造(コンクリート充填鋼管構造)のコンクリート圧入技術も向上し、虎ノ門ヒルズでは高さ207mまで圧入を行った。この際の圧送実験では水平換算距離592mに置き換えて検証している。このようにタワークレーンや圧送の技術向上により、より重い資材や硬いコンクリートをより高所まで運ぶことが可能になった。
揚重管理
超高層建築の誕生から50年が経つ中で、揚重を担う体制も変化を続けてきた。高層建築で揚重すべき資材の種類や量は膨大である。どのクレーン、エレベーターを使っていつどこに運ぶか、こうした揚重の管理に多くの労力をさく必要がある。従来の低層・中層の建築であれば、専門工事会社がそれぞれの裁量でエレベーター等を使って揚重することも可能であったが、高層建築になると、揚重したい時間にエレベーターに持っていっても、数十分、1時間といった時間待たされることも起こりうる。特に、仕上げや設備は後回しにされやすかったとされる。
そこで徐々に揚重を1カ所で集中的に管理したり、揚重に専従する職人や業者を配置する動きが見られ始める。こうした揚重管理の工夫は霞が関ビルディングの時点で既に見られる。霞が関ビルディングでは、揚重管理のために、日本通運に協力をあおいだことが記録されている。霞が関ビルディングでは、資材を大型(4.0m以上)、中型(1.8~4.0m)、小型(1.8m以下)に分類し、それぞれクレーン、荷用リフト、人荷用エレベーターをあてるとともに、特に小型の資材は集積・荷下ろしの手間を削減するため、パレット化、コンテナ化が進められた。
霞が関ビルディングのコンテナ・パレット(霞が関ビルディング50年記念誌より転載、三井不動産蔵)
このように揚重の仕組みが整ったとしても、実際に誰がエレベーターのオペレータをするか、誰が地上の荷さばきをするか、誰が各専門工事会社の揚重時間を管理するかといった問題が起こる。霞が関ビルディングでは、元請けの担当社員3名からなる揚重事務所を設け、各業者から週間揚重予定を提出させ、毎日の揚重量と揚重階を決定した。朝日東海ビル等でも揚重専従班や揚重コントロールセンターの設置といった取組は見られる。1990年頃になると、揚重センターを設けて、協力会社が直接揚重計画についてやり取りする動きが見られるようになり、梅田センタービル(1987年、125m)では、専門の揚重工を置き、さらに各専門工事会社に揚重計画をコンピュータで入力させる取組が見られる。こうした揚重専従班やエレベータ等のオペレータは土工等が担う場合が多かった。
その後、バブル期の人件費の高騰および人手不足により、専門工事会社の職人が揚重までを担うデメリットが大きくなったことから、首都圏や近畿圏の高層建築施工においては、揚重専門の会社が揚重を担うことが一般化した。現在、東日本では一般社団法人東日本揚重業協会、西日本では一般社団法人揚重工事業協会という揚重業の団体も活動している。
揚重の専門工事会社が特に大きな効果を発揮するのは超高層マンションの施工現場である。高層マンションの施工現場にはボード、断熱材、キッチン、ドア、家具など、多くの種類の体積もかさばる資材が運び込まれる。また、住戸毎に仕上げや設備が異なるといったことも起こるし、揚重された資材は狭い廊下を通ってそれぞれの住戸に運ぶ必要がある。このように部屋まで運ぶことを「間配り(まくばり)」というが、実際の現場では垂直揚重のみ、住戸まで間配り、住戸内の部屋まで指定など、揚重専門工事会社に依頼される内容も工事ごとに様々である。現在、首都圏の高層マンションの現場に行くと、工事用エレベーターやゲートの近くに揚重センターが設けられ、各工事に必要な資材の搬入・揚重等のスケジュール管理を行っている。
こうした場内物流や揚重はICT化による生産性向上の余地が大きく、揚重管理やゲート管理のためのソフトウェアや自動搬送用のロボットも開発されている。一方で、機械のメンテナンスや人員輸送を含めたスケジュール管理、資材搬入時間の急な変更への対応・多職種との調整など、人が臨機応変に対応するアドバンテージが大きい分野でもある。遅れて到着した資材を、センター長自らフォークリフトを運転し、人員輸送を待ってもらって空いたエレベーターに載せるといったことはなかなか自動化が難しいように思われる。
静脈物流・副産物
資材を取り付け箇所まで運ぶことに対し、施工時に発生した副産物や施工後に取り外した仮設資材を持ち帰ることを静脈物流と呼び、この効率化も大きな課題である。例えば、高層建築施工におけるデッキプレートの利点として、サポートが不要ですぐに下階工事を始められるといった利点がすぐに思い浮かぶが、同時に、型枠の脱型作業や脱型した型枠を地上階まで降ろす作業が必要ないメリットも大きい。
さらに環境意識の高まりを受けた1990年の建設廃棄物処理ガイドライン策定、2002年の建設リサイクル法完全施行等を経て、建設時の産業廃棄物の削減やゼロエミッションに向けた動きも活発化した。一例として、2000年竣工のNECルネッサンスシティは自動化施工ABCSの適用事例として知られるが、ここでは物流センターと呼ばれる資材搬送チームが、建設資材の搬出・揚重管理の徹底に加えて、産業廃棄物分別を徹底して行い、約29%の産業廃棄物削減を実現したとされる。こうした廃棄物の回収にも揚重専門会社が関わるケースが増加しており、単に揚重を管理するだけではなく、同時に現場で発生した副産物を回収し下に降ろすなど担う役割を拡大させている。冒頭のブルネレスキの偉大さは、当時から資材を降ろすことの重要性を認識していた点にあるのかもしれない。
参考文献
1 黒坂雅人ほか,日本における高層ビル施工の変遷に関する研究 ―揚重・運搬・情報に着目した生産性向上の取り組み―,第34回建築生産シンポジウム論文集,pp.141-146,2018年
2 嘉納成男、「5.施工史」、「建築業協会賞50年 受賞作品を通して見る建築1960―2009」新建築2009年12月臨時増刊所収、pp.148―173、2009年
3 権藤智之、「構法」、霞が関ビルディング、霞が関ビルディング50周年記念誌編集委員会,三井不動産株式会社発行,pp.248-285,2018年
4 「天才建築家 ブルネレスキ フィレンツェ・花のドームはいかにして建設されたか」、ロス・キング著、田辺希久子訳、2002年、東京書籍
5 清水建設二百年生産編、清水建設株式会社、2003年
6 日本の建設機械、日本建設機械工業会20年の歩み所収、社団法人日本建設機械工業会、2010年
7 三井本館と建築生産の近代化」、石田繁之介、鹿島出版会、1988年
8 建築生産の技術、梅村魁編、丸善、1978年
9 榎本精一、「コンクリートポンプ圧送」、コンクリート工学、Vol.40、pp.72-76、2002年