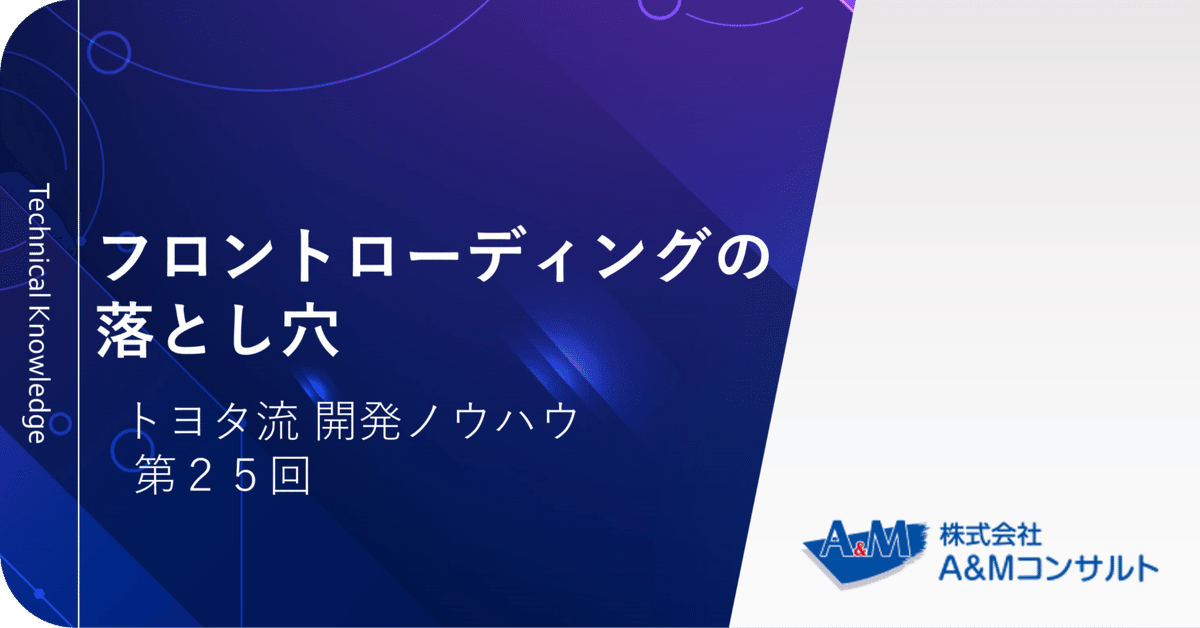
フロントローディングの落とし穴|トヨタ流開発ノウハウ 第25回
◆設計改革の困りごと
設計改革を進めているとこんな困りことを聞くことがよくあります。
1.フロントローディング、フロントローディングって言うけど、設計時にやること増えてない?
2.設計改革をプロジェクトで進めているみたいだけど、そのプロジェクトで決まった内容を実施したとしても工数が減るようには思えない。
3.不具合対応で忙しい時にフロントローディングなんて実施できない!
4.DRBFMってめんどくさいから資料を適当に作って、DRに提出すればいいや。
皆さんは、このような言葉を聞いたことはありませんか?
なにかを改善・改革しようとするときは今までと異なる仕事をしなければならなくなるため、誰でも「めんどくさく」感じるときがあるでしょう。
これがまさにフロントローディング改革(DRBFM・FMEAの実施)の落とし穴なのです。
フロントローディングの本当の目的をしっかりと設計者全員に説明しないと、「やっつけ」の仕事になってしまい、本当に負荷が増えるだけで、何も改善はしません。
では、改めてフロントローディングの定義を確認しましょう!
◆フロントローディングの定義
「製品開発のプロセスで業務の初期工程に負荷をかけ、作業を前倒しで進める手法のことであり、できるだけ早い段階で多くの問題点やリスクを洗い出し、対策し、初期段階から設計品質を高めること」
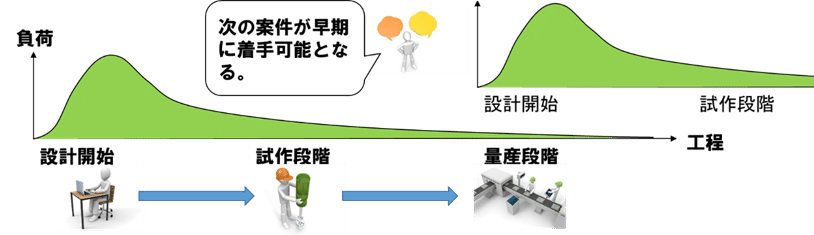
横軸に工程をとり、縦軸に負荷(設計者の工数)でフロントローディングを表してみました。
上記のイメージ図のように、設計の初期段階に負荷をかけることにより、設計品質レベルを高めます。その結果、設計途中に発生する図面の描きなおし、評価のやり直しなどが減少し、量産スタート時点で設計での初期不良が大幅に減少します。
最も工数を有するのが、まさに量産の初期の部分。このタイミングで不良を発生させてしまうと、製造を止めないためにも早急に対応策を検討しなければなりません。
しかし、本来このような不具合は発生してはいけないものですし、設計初期段階で問題の未然防止策を検討できていれば、対応しなくても良い不具合です。
「このような部分に工数をかけている現状から脱却しましょう!」
が本来のフロントローディングの意義です。
また、フロントローディング改革において重要なツールであるDRやDRBFMも単なるイベントや資料作成の意味で実行してしまうと効果は表れないでしょう。
皆さんが対応している不具合の工数を確認してみてください。多くの工数が発生しているのではないでしょうか。また、不具合が発生した時に損失金額を計算している企業もありますが、損失金額の中に設計者の対応工数が含まれていないことが多いのです。
実際のところ、多くの金額がこの不具合対応に使ってしまっています。
コストダウンを検討する前にこの不具合を減少させなければ、コストダウンした意味がないぐらいの損失となってしまうでしょう。
◆フロントローディングの進め方
ではフロントローディング改革を効果的に、設計者が納得する形でどのように進めればいいのでしょうか。
先ほどお話しした損失金額と設計者の対応工数がキーポイントです。
1.損失金額(サブの目的)
損失金額を1つの製品に戻した場合に大幅なコストダウンと同じ効果が見られると思います。
2.設計者工数(メインの目的)
不具合対応した工数、図面の描き直し工数、評価やり直し工数が全て0だった場合、どれぐらいリードタイムが短縮できるか検討します(フロントローディングに必要な工数が増加するので正確には0に換算することは出来ませんが、分かりやすく説明するためにはこのような仮定でも問題ないと考えいます)。
そのリードタイム分早く仕事が終わるのです。さらには次の案件に早期に着手でき、初期段階から設計品質を高めることができます。
≒設計者が楽に仕事を進めることができる上で、新しい案件、付加価値の高い製品への開発検討が実現できます。
このような目的をしっかりと設計者全員に説明し、フロントローディング改革は設計者自身にとってもメリットがあると理解してもらわなければなりません。
その結果、DRBFMなどのツールが有効的に活きてきます。
また、コストダウンがなかなか進まない企業にもこのフロントローディングの必要があるかもしれません。
コストダウンは機能を維持したまま、コストを減少させることが目的ですので、検討に時間がかかります。
その時間はどうやって捻出するのでしょうか。
量産初期段階で不良が発生している状況で他の案件のコストダウンが検討出来るでしょうか。
結局のところ、時間的余裕がどこかになければコストダウンも出来ません。この時間的余裕を作るためには設計品質を初期段階から高めることが必要になってきます。
皆さんいかがでしょうか。
「品質」という言葉を「製品の品質」にだけ当てはめてはいけません。
日本の製造業が強いのは「製品の品質」もそうですが、この「プロセスの品質」を高める事が出来ている結果、製品のQCDのレベルが高くなるのです。
「品質は当たり前、今の時代はコスト!」確かに昔はそう言われていたかもしれませんが、もう時代は令和。
プロセスの品質に目を向けて、改革を進めていってほしいと思います。
講師プロフィール
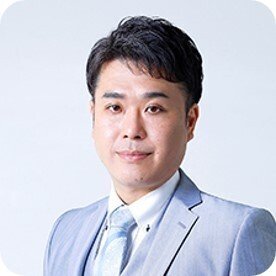
株式会社A&Mコンサルト
代表取締役社長 | 中山 聡史
2003年、関西大学 機械システム工学科卒、トヨタ自動車においてエンジン設計、開発、品質管理、環境対応業務等に従事。ほぼ全てのエンジンシステムに関わり、海外でのエンジン走行テストも経験。
2011年、株式会社A&Mコンサルトに入社。製造業を中心に自動車メーカーの問題解決の考え方を指導。
2015年、同社取締役に就任
2024年4月、代表取締役社長に就任
主なコンサルティングテーマ
設計業務改善/生産管理・製造仕組改善/品質改善/売上拡大活動/財務・資金繰り
主なセミナーテーマ
トヨタ流改善研修/トヨタ流未然防止活動研修/開発リードタイム短縮の為の設計、製造改善など
※2024年6月現在の情報です
近著
この記事が気に入ったらサポートをしてみませんか?