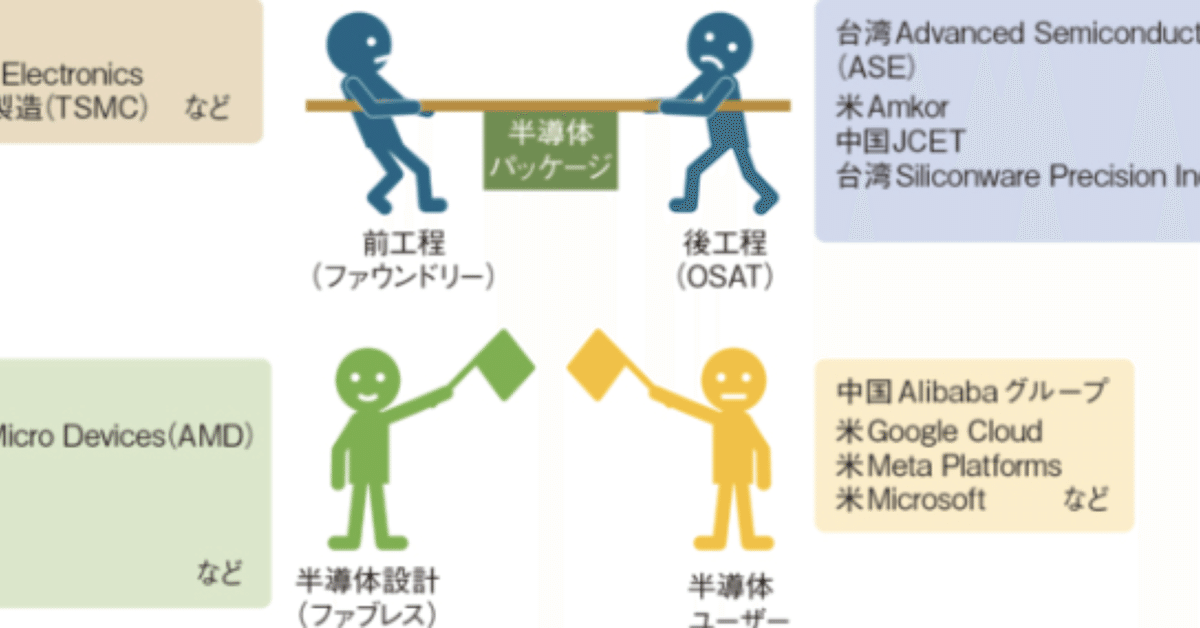
EUVリソグラフィ技術と半導体前工程
EUVリソグラフィ技術(Extreme Ultraviolet Lithography)は、半導体チップの製造において、非常に微細な回路パターンをシリコンウェハ上に転写するための先進的な露光技術です。この技術は、波長が13.5nmの極端紫外線(EUV)を用いており、従来の光リソグラフィ技術よりもはるかに短い波長を使用することで、より高い解像度と微細化を実現しています12。
EUVリソグラフィの主な特徴は以下の通りです:
高解像度:短い波長のEUV光を使用することで、従来の光源では不可能だったナノメートルオーダーの微細な回路パターンの形成が可能になります。
微細化の進展:EUVリソグラフィは、45nmハーフピッチから32nm、さらには22nmハーフピッチまでの複数世代の半導体デバイスの製造に適用可能です
複雑な装置構造:EUV光はレンズを通過しにくいため、反射型の光学システムが必要であり、装置内を真空状態に保つ必要があります
EUVリソグラフィ技術の導入は、半導体産業における微細化の限界を押し広げ、次世代の高性能デバイスの開発を可能にしています。しかし、この技術は非常に高度で複雑なため、EUV露光装置を供給できる企業や、この技術を利用してチップを製造できる半導体メーカーは限られています
EUVリソグラフィ技術は、半導体の微細化をリードするASMLのEUV露光技術として、今後の半導体微細化の未来を主導する企業の全体像を把握し、戦略に生かすことが期待されています。この技術の進化は、デジタル社会の発展だけでなく、安全保障面での国際競争力にも大きな影響を及ぼしています。EUVリソグラフィは、半導体の微細加工技術のキーテクノロジーとして、今や半導体はデジタル化が進む現代社会の営みに欠かせない戦略物資となっています
フォトマスク転写は、半導体や電子部品の製造工程で使用される重要なプロセスです。このプロセスでは、フォトマスクと呼ばれる透明な板に描かれた微細な回路パターンを、光リソグラフィ(フォトリソグラフィ)技術を用いてシリコンウェハー上に正確に転写します
フォトマスクは、ガラスや石英などの透明な基板の上に、特定の回路パターンを薄い金属膜(一般的にはクロム)で描いたものです。このパターンは、半導体の心臓部分となる微細な回路を形成するための「型」のような役割を果たします
リソグラフィプロセスの中心部分であるフォトマスク転写では、フォトマスクに描かれたパターンが光を通してウェハーに投影され、感光材(フォトレジスト)が塗られたウェハー上に同じパターンが形成されます。露光によりフォトレジストの現像液への溶解性が変化し、光の当たった部分が除去されるか残存することにより、次のエッチング工程での被加工対象への溶解、除去処理に対するマスクとなります2。
このプロセスを通じて、半導体チップの各層が正確に重ねられ、最終的な半導体デバイスが完成します。フォトマスク転写は、半導体デバイスの微細化が進むにつれて、より高精度なフォトマスクが求められる非常に重要な工程です
半導体の製造における前工程は、シリコンウェハ上に微細な半導体デバイスを形成するための一連の工程です。以下にその主なステップを説明します:
洗浄工程:ウェハ表面の不純物や汚れを取り除きます。これにより、後続の工程での不良率を低減します ウェハ表面の不純物や汚れを取り除く工程は、半導体製造における品質管理の非常に重要な部分です。この洗浄工程は、ウェハが次の製造ステップに進む前に行われ、以下のような具体的な方法で実施されます:
ウェットクリーニング:化学薬品を用いたウェットクリーニングは、ウェハ表面の有機物や金属汚染、自然酸化膜などを除去します。例えば、RCAクリーニングと呼ばれる方法では、アンモニア水と過酸化水素水の混合溶液(SC1)で有機物を除去し、塩酸水と過酸化水素水の混合溶液(SC2)で金属不純物を溶解、除去します
ドライクリーニング:ドライアイス粒子クリーニングなどのドライクリーニング方法もあり、これはウェハ表面の不純物を取り除き、表面を不動態化するために使用されます
浸漬法:ウェハを化学物質や超純水蒸留水に浸すことで、不純物を取り除きます。この方法は多量のウェハを同時に処理できるため、生産性が高いです
スプレー法:回転するウェハに液体や気体の化学物質を噴射し、不純物を取り除く方法です。微細プロセスの高度化や使用物質の変化により、ウェハを1枚ずつ処理するスプレー法の割合が高まっています
乾燥工程:洗浄後、ウェハは乾燥されます。スピンドライヤやIPAベーパドライヤなどの装置が使用され、ウェハ上の水分を効率的に除去します
これらの洗浄方法は、ウェハ表面の不純物を効果的に除去し、後続の製造工程での不良率を低減するために不可欠です。洗浄工程は、半導体の歩留まりを高め、製品の品質を保証するために重要な役割を果たしています。また、洗浄工程は繰り返し行われるため、実施回数が他の工程に比べて多いのも特徴です
成膜工程:ウェハ上に絶縁膜や導体膜などの薄膜を形成します。これらの膜は、電気的特性を持ち、半導体デバイスの機能に直接関与します
ウェハ上に形成される絶縁膜や導体膜は、半導体デバイスの基本的な構成要素であり、それぞれが特定の電気的特性を持ち、デバイスの機能に直接関与します。以下にその詳細を説明します:
絶縁膜:絶縁膜は、主に二酸化ケイ素(SiO2)などの材料で作られ、電気を通さない特性を持っています。この膜は、ウェハ上で異なる電気的領域を分離し、回路間のリーク電流を防ぐために使用されます。また、ウェハを化学的な不純物から保護し、イオン注入段階での拡散を防ぐ役割も果たします1。
導体膜:導体膜は、金属やポリシリコンなどの導電性材料で作られ、電気信号を伝達するために使用されます。これらの膜は、トランジスタのソースやドレイン、配線などの形成に不可欠です。導体膜は、回路間の電気的信号をつなぐ役割を担います
これらの膜は、蒸着工程(Deposition)を通じてウェハ上に形成されます。蒸着工程には、物理気相成長法(PVD)と化学気相成長法(CVD)の2つの主要な方法があります。PVDは金属薄膜の蒸着に主に使用され、CVDは導体、不導体、半導体の薄膜蒸着にすべて使用できる技術です。現在、半導体工程では、CVDが主に使用されており、特にプラズマCVDは低温で形成でき、厚さの均一度の調整や大量の処理が可能なため、最も多く利用されています2。
絶縁膜と導体膜は、半導体デバイスの性能を大きく左右するため、これらをどれほど薄く均一に形成できるかが半導体の品質を決定します。将来的には、さらに一層薄く均一な薄膜が形成できる蒸着技術が求められています
CVD(Chemical Vapor Deposition、化学気相成長)技術は、半導体デバイスの製造において重要な役割を果たす薄膜形成技術です。このプロセスでは、ガス状の前駆体を高温の反応炉内に導入し、基板上で化学反応を起こして薄膜を形成します。CVD技術は、その高精度と均一な薄膜形成能力から、半導体産業において不可欠な技術となっています
CVDプロセスには、以下のような特徴があります:
高品質な薄膜:CVDは、高純度で均一な薄膜を生成する能力に優れており、これがデバイスの特性を最大限に引き出す要因となっています。
多様な材料:シリコン、ガリウムナイトライド、シリコンカーバイドなど、多様な半導体材料を堆積することができます。半導体製造における「堆積」とは、CVD(化学気相成長)などの技術を用いて、ウェハ上に絶縁膜や導体膜などの薄膜を形成するプロセスを指します。このプロセスによって、半導体デバイスの電気的特性を持つ重要な層が作られます
プロセスの制御性:成膜速度、膜の厚さ、結晶性、純度などのパラメータを最適化することが可能です。
CVD技術にはいくつかのバリエーションがあり、それぞれ特定の材料特性や製造要求に応じて最適化されています:
熱CVD:高温での堆積を行い、薄膜の密度と硬度を向上させることができます。
プラズマ強化CVD(PECVD):低温での堆積が可能で、薄膜の密度と硬度を向上させることができます。
低圧CVD(LPCVD):より均一な薄膜を形成することができ、大量生産に適しています。
原子層堆積(ALD):原子層レベルでの精密な制御が可能で、超微細構造の形成に適しています。
CVD装置の設計と運用には、精密な制御と高い技術力が求められます。反応炉の温度制御、ガス流量の管理、基板の位置決めなど、各プロセスパラメータの微細な調整が必要です。これにより、薄膜の均一性、密着性、電気的特性が最適化され、高品質な半導体デバイスの製造が可能となります
CVD技術は、トランジスタのゲート絶縁膜や配線層の形成、3D NANDフラッシュメモリの製造など、さまざまな応用分野で活用されています。また、CVD装置は生産効率の向上にも寄与しており、大規模な生産ラインでも高品質な薄膜形成が可能となっています
最新のCVD技術革新は、半導体産業のさらなる進化を促しており、原子層堆積(ALD)技術やプラズマ強化CVD(PECVD)技術の進化が特に注目されています。これらの技術は、次世代の半導体デバイスの性能と信頼性を向上させるために重要な役割を果たしています。CVD装置市場は今後も成長が見込まれており、2024年には市場規模が170億2000万米ドルに達し、年平均成長率(CAGR)は5.95%と予測されています。この成長は、半導体デバイスの需要増加と技術革新に支えられています。
CVD技術(化学気相成長)は、半導体産業をはじめとする多くの分野で広く応用されています。以下にいくつかの応用例を挙げます:
半導体デバイス:CVD技術は、トランジスタのゲート絶縁膜や配線層の形成、3D NANDフラッシュメモリの製造など、半導体デバイスの様々な部分の製造に利用されています1。
次世代半導体材料:シリコンカーバイド(SiC)やガリウムナイトライド(GaN)などの高品質な薄膜を成長させることで、パワーデバイスや高周波デバイスに応用されています2。
切削工具:切削工具の刃先部やギアの接触部に、窒化炭素、窒化チタンなどの硬質コーティングを施すために使用されます3。
光源:家電製品のリモコン用赤外発光ダイオードや、交通信号に使われる青色発光ダイオードの製造にもCVD技術が活用されています4。
2次元材料:グラフェンやモリブデン二硫化物(MoS2)などの2次元材料の大規模合成にもCVD技術が利用されており、エレクトロニクス、フォトニクス、エネルギー貯蔵などの分野での応用が進んでいます2。
これらの応用例からもわかるように、CVD技術はその高い制御性と再現性により、特に高品質な材料の製造に適しており、今後もさらなる技術革新が期待されています。CVD技術は半導体産業において広く採用されており、多くの企業がこのプロセスを利用しています。CVD装置は、その高精度と均一な薄膜形成能力から、半導体産業において重要な役割を果たしており、ナノメートルスケールの微細加工技術の進展に伴い、その重要性はますます高まっています
主要なCVD装置メーカーとしては、アプライドマテリアルズ、東京エレクトロン、ラムリサーチなどが挙げられます。これらの企業は、最先端の技術を駆使し、高品質なCVD装置を提供しており、半導体デバイスの性能向上と信頼性確保に欠かせません
また、CVD技術は材料の選択肢が広く、多様な半導体材料を堆積することができるため、異なるデバイス構造や用途に応じたカスタマイズが可能です。さらに、CVD装置は生産効率の向上にも寄与しており、大規模な生産ラインでも高品質な薄膜形成が可能となっています
このため、CVD装置は半導体産業だけでなく、太陽光発電やディスプレイ産業など、他の高技術産業でも広く利用されています。CVD装置市場は今後も技術革新とともに進化し続けるでしょう1。CVD技術の進化は、デジタル社会の発展だけでなく、安全保障面での国際競争力にも大きな影響を及ぼしています
リソグラフィ工程:フォトリソグラフィ技術を用いて、フォトマスクに描かれた回路パターンをウェハ上に転写します。この工程により、トランジスタやその他のデバイスの微細な構造が形成されます リソグラフィ工程は、半導体製造における最も重要な工程の一つで、ウェハ上に微細な回路パターンを形成するために使用されます。この工程は、以下の主要なステップから構成されています:
レジスト塗布: ウェハ全面に感光性材料である「レジスト」を均一に塗布します。レジストは、特定の波長の光に反応して性質が変化する材料です
レジスト塗布は、半導体製造におけるリソグラフィ工程の初期段階で行われる重要なプロセスです。この工程では、感光性材料である「フォトレジスト」をウェハ全面に均一に塗布します。フォトレジストは、特定の波長の光に反応してその溶解性が変化する性質を持つ材料です
具体的な塗布の手順は以下の通りです:
レジストの液滴下:まず、ウェハの中心にフォトレジストの液体を滴下します。
スピンコート:ウェハを高速で回転(スピン)させ、遠心力を利用して液体レジストをウェハ全面に均一に広げます。
プレベーク:ウェハに塗布された液体レジストをホットプレートで加熱し、溶剤を蒸発させてレジストを乾燥させます。これにより、レジストがウェハにしっかりと固定されます
このプロセスにより、レジストはウェハ上に薄膜として均一に塗布され、次の露光工程に備えます。露光工程では、フォトマスクを使用してレジストにパターンを転写し、その後の現像工程で露光された部分のレジストを除去することで、微細な回路パターンが形成されます。
フォトレジストの性質として、光によって硬化する光硬化性樹脂の一種であり、紫外線(UV)を感光性樹脂に当てることで、緻密な三次元構造を層ごとに固めることが可能になります。この特性は、3Dプリンティング技術や医療分野での充填材料など、多岐にわたる分野で利用されています
レジスト塗布は、半導体デバイスの微細化が進むにつれて、より高精度な制御が求められる非常に重要な工程です。この工程の精度が半導体デバイスの品質と性能を大きく左右するため、半導体製造においてはクリーンルーム内で厳格な環境管理のもとで行われます。
また、フォトレジストの種類や塗布方法は、使用される光源の種類や製造するデバイスの要求に応じて選ばれます フォトレジストには、主に露光された際の化学反応によって分類される「ポジ型」と「ネガ型」の2種類があります。また、使用される光源の種類によっても分類されます
ポジ型フォトレジスト: 露光された部分が現像液に対して溶解性が増大し、現像によって露光されなかった部分が残ります。一般的に、金属イオンを含まない有機アルカリ溶液で現像されます。微細なパターン形成に適しており、半導体製造において広く使用されています。
ネガ型フォトレジスト: 露光された箇所が現像液に対して溶解性が低下し、現像によって露光した部分が残ります。多くの場合、有機溶剤を使用した現像液が用いられますが、環境への影響や微細配線への対応が難しいため、半導体向けでは利用が減少傾向にあります。
さらに、フォトレジストは露光波長によっても分類され、以下のような種類があります:
g線レジスト
i線レジスト
deep-UVレジスト
KrFエキシマレジスト
ArFエキシマレジスト
これらのフォトレジストは、半導体製造の工程で微細な回路パターンを形成する際に欠かせない存在であり、半導体デバイスの小型化や高性能化を実現するためには、各ステップにおいて高い精度が求められます
露光: フォトマスクを使用して、レジストにパターンを転写します。フォトマスクは、所望の回路パターンが描かれた透明な板で、光を通す部分と遮る部分があります。露光装置(ステッパー)を用いて、フォトマスクを通してレジストに光を照射し、パターンをウェハ上に転写します 露光プロセスは、半導体デバイスの製造において非常に重要な工程です。このプロセスでは、フォトマスクとフォトレジストを使用して、微細な回路パターンをシリコンウェハ上に転写します。以下にその詳細な手順を説明します。
フォトレジストの塗布: ウェハ上に感光性樹脂であるフォトレジストを均一に塗布します。これは通常、スピンコート法によって行われ、ウェハを高速回転させながらフォトレジスト液を滴下し、遠心力で薄膜を形成します
フォトレジストの塗布は、半導体デバイスの製造におけるリソグラフィプロセスの初期段階であり、非常に重要です。この工程では、スピンコート法を用いてウェハ上に感光性樹脂であるフォトレジストを均一に塗布します。以下にその手順を説明します。
ウェハの準備: ウェハはクリーンルーム内で洗浄され、塗布前には無塵で乾燥した状態に保たれます。
スピンコート: ウェハをスピンコーターのチャック上に固定し、ウェハの中心にフォトレジスト液を滴下します。
回転開始: ウェハを低速で回転させ、フォトレジスト液がウェハ全体に広がるようにします。
高速回転: ウェハの回転速度を上げ、遠心力によって余分なフォトレジスト液がウェハの端から飛び散り、均一な薄膜が形成されます。
回転停止: 必要な膜厚に達したら回転を停止します。膜厚は回転速度と時間、フォトレジストの粘度によって制御されます。
膜厚の測定: 均一な膜厚が得られたかを確認するために、エリプソメトリーなどの測定装置を使用して膜厚を測定します。
このスピンコート法により、ウェハ上には均一で平滑なフォトレジスト膜が形成され、後続の露光プロセスで高精度なパターン転写が可能となります。膜厚の均一性は、デバイスの性能に直接影響を与えるため、この工程は非常に重要です。また、塗布されたフォトレジストは、プリベークによって溶剤を蒸発させ、硬化させる必要があります。これにより、露光時の解像度が向上し、現像プロセスでのパターン形成が容易になります。
プリベーク: 塗布されたフォトレジストを加熱して溶剤を蒸発させ、レジストを硬化させます。これにより、露光時の解像度が向上します
露光: フォトマスクをウェハ上に配置し、露光装置(ステッパー)を使用して紫外線を照射します。フォトマスクは透明なガラス板で、所望の回路パターンが描かれており、光を通す部分と遮る部分があります。光はフォトマスクを通過し、パターンに対応する部分のフォトレジストを硬化させます
露光プロセスは、フォトリソグラフィ工程の中心的なステップであり、フォトマスクを使用してウェハ上に微細な回路パターンを転写する方法です。以下にその詳細な手順を説明します。
フォトマスクの準備: フォトマスクは、所望の回路パターンが描かれた透明なガラス板です。パターンは光を遮る材料(オパーク)で形成され、残りの部分は光を通す(トランスペアレント)ことができます。
ウェハの位置決め: ステッパー内でウェハを正確に位置決めし、フォトマスクとの整合を取ります。
露光: ステッパーは、フォトマスクを通して紫外線(UV)をウェハ上のフォトレジストに照射します。紫外線は、フォトマスクの透明部分を通過し、フォトレジストに当たります。
フォトレジストの反応: 照射されたフォトレジストは、光化学反応を起こし、その性質が変化します。ポジティブレジストの場合、露光された部分が溶解性を増し、ネガティブレジストの場合は、露光された部分が硬化して溶解性が減少します。
現像: 露光されたウェハを現像液に浸すことで、露光された部分または露光されていない部分のフォトレジストが除去され、ウェハ上に微細なパターンが形成されます。フォトレジストにはポジティブとネガティブの二種類があり、露光された部分が残るか除去されるかは使用するレジストの種類によります
ポストベーク: 最終的な硬化と安定化のために、再度加熱処理を行います
このプロセスを通じて、ウェハ上に精密な回路パターンが形成され、後続のエッチングプロセスで不要な部分が除去され、半導体デバイスが作成されます。露光プロセスは、高度な精度と制御が求められるため、半導体製造における最も重要なステップの一つです。
現像: 露光されたレジストを特定の液体で処理し、光によって変化した部分を除去または残すことで、ウェハ上に微細なパターンを形成します
エッチング: 現像されたパターンに従って、ウェハ上の不要な材料を化学的または物理的に除去し、回路パターンを形成します
レジストの除去: エッチング後、不要になったレジストを除去し、清浄なウェハ表面を露出させます
リソグラフィ工程は、半導体デバイスの性能と集積度を決定するため、非常に精密な制御が必要です。また、この工程は半導体製造工程の中で何度も繰り返されるため、半導体工場の中心に位置づけられることが多く、その重要性は非常に高いです
最先端のリソグラフィ技術としては、EUV(極端紫外線)リソグラフィがあり、これはさらに短い波長の光を使用して、より微細なパターンの形成を可能にしています。この技術の進化は、半導体の微細化を推進し、高性能化を実現するために不可欠です
エッチング工程:現像されたパターンに従って、不要な膜を化学的または物理的に除去し、回路パターンをウェハ上に形成します1。
イオン注入工程:ウェハに不純物を注入し、N型またはP型の半導体領域を作り出します。これにより、半導体の電気的特性が決定されます1。
熱処理工程:高温でウェハを処理することで、イオン注入された不純物をシリコン結晶内に拡散させ、電気的特性を安定させます1。
平坦化工程:ウェハ表面を平滑にすることで、後続のリソグラフィ工程の精度を向上させます1。
ウェハ検査工程:各種検査を通じて、ウェハの品質を確認し、不良品を排除します1。
これらの前工程を経て、半導体デバイスの基本的な構造が形成されます。その後、後工程に進み、チップの切り出しやパッケージングなどが行われ、最終的な半導体製品が完成します。前工程は非常に精密な工程であり、半導体デバイスの性能を大きく左右するため、クリーンルーム内で厳格な環境管理のもとで行われます