
S30ヘッドライトカバー枠の試作再開
「ビードローラーで作れそう、細心の注意が必要だが」というのを確認して4年過ぎてしまいました。
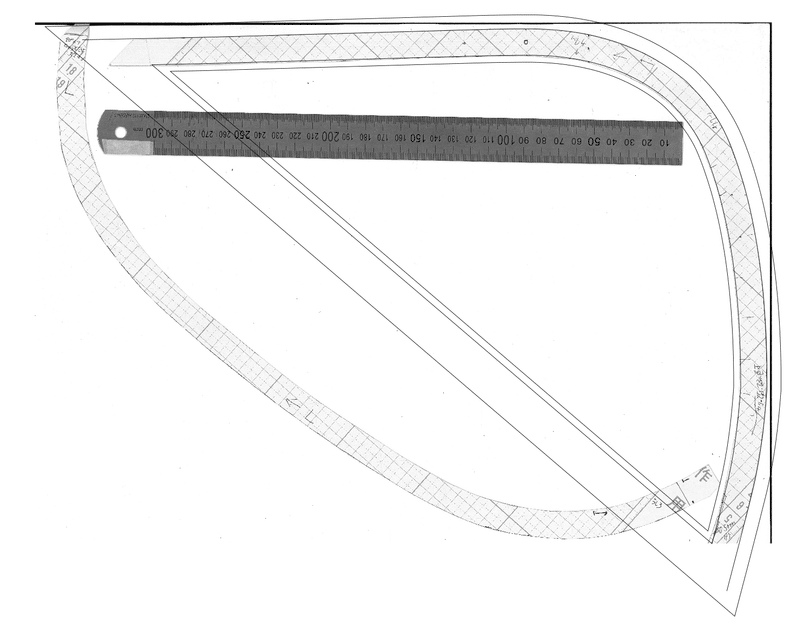
4年放置していた型紙をいじります。自分で切るのは手間だし再現性に欠けるのでレーザーカット外注しようと思ったんですが、形状決定するまでの数度の試作ごとに1セットだけ切って送ってもらうのは煩雑だし単価もバカにならないと思い立ち止まった、といういきさつです。「プラズマCNCで切れるなこれ」いや、プラズマCNC化がうまく動いたらライトカバー枠試作が捗るという皮算用は最初からあったわけで。
型紙はまだデジタルデータに落とし込んでいなかったのでInkscapeでパス化→SheetcamでGコード。パス化したあと「閉じたパス」になってることが重要。
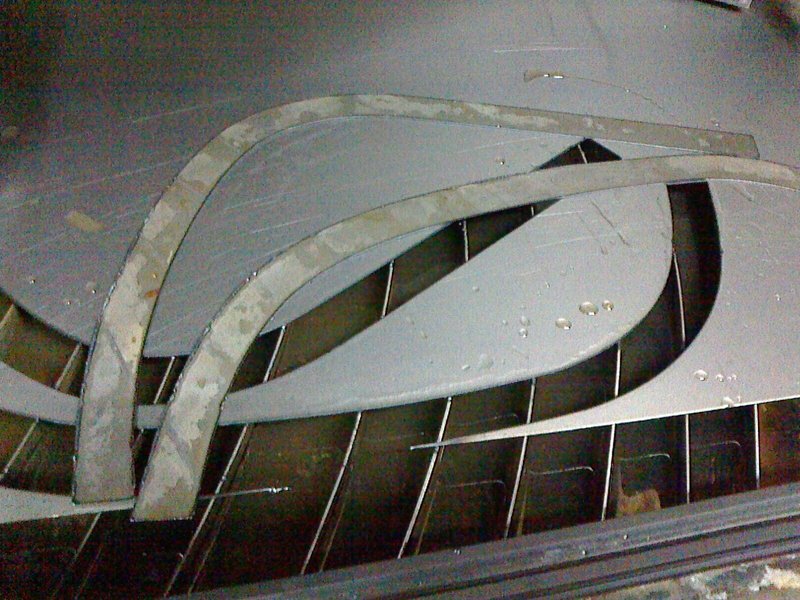
年が明けてから最初の切断、まだお試し程度しか切っていないので緊張が高まりスタートボタンクリックするまで躊躇しましたが、1ミリ板が切れないような設定にはなかなかできないし無事切断。
型紙から切り出した鉄板を材料に曲げていってちゃんと形になるのか確認してなかったので、必要ならパスの修正をしていきます。
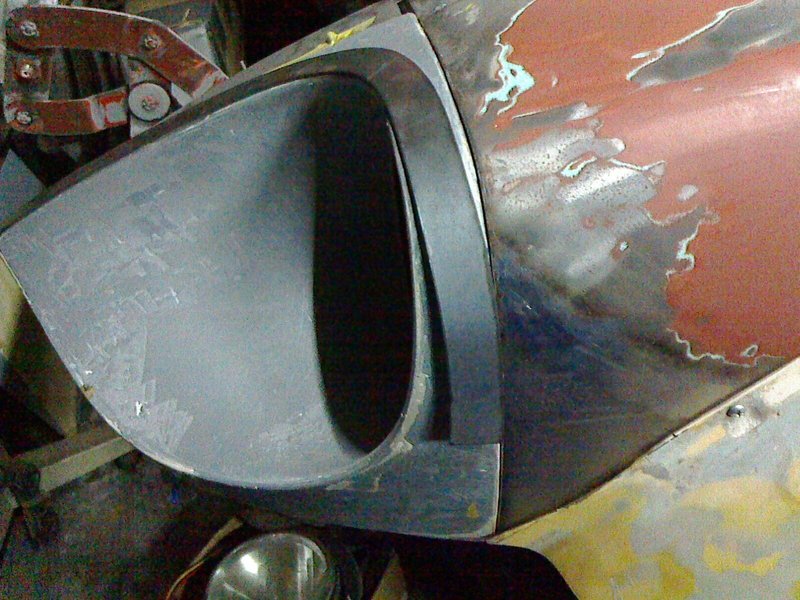
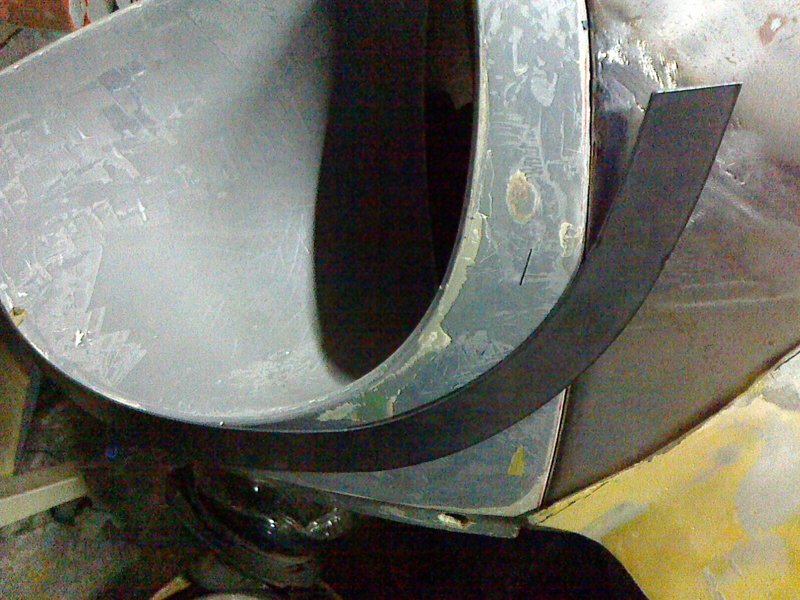
全然ダメっぽいでしょ?枠の広い面はヘッドライトバケットの面と平行でなくて外周側が落ち込んだ形状なんでこんなことになりますがここはスルー、気にせずに曲げていきます。
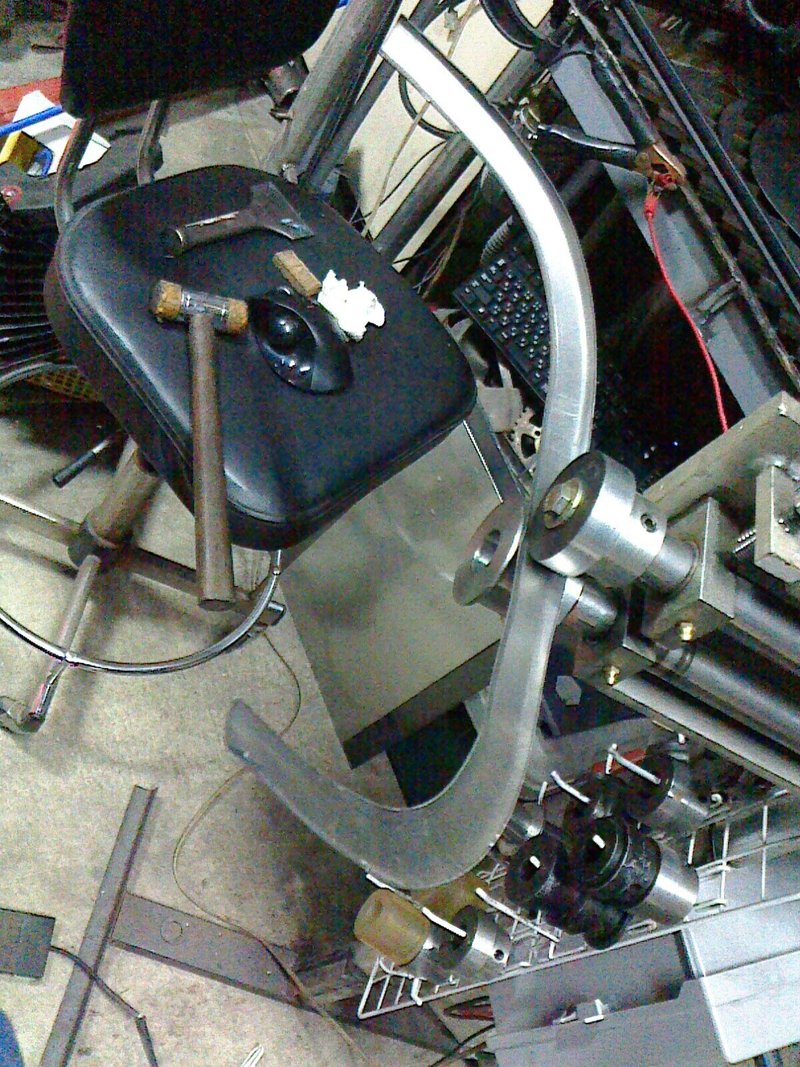
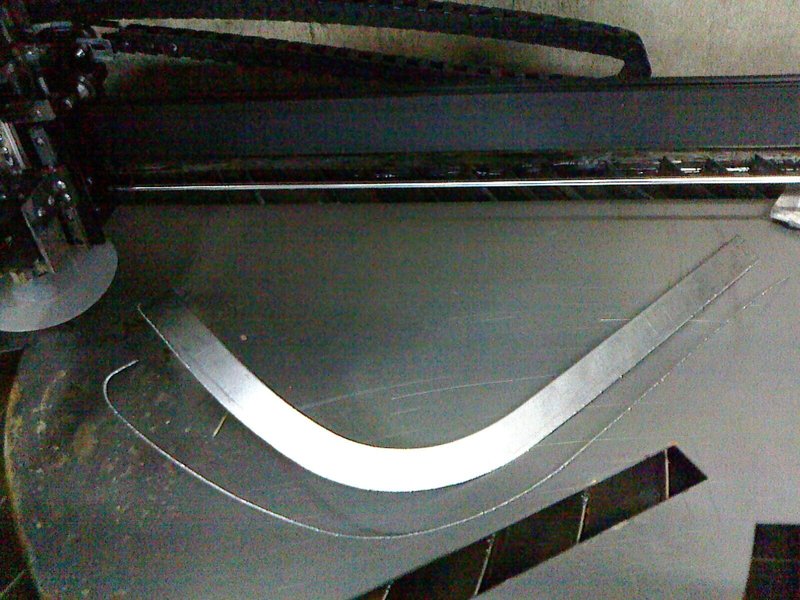
日産の原型を観察すると幅が広すぎたんでトリミング。こういう微調整カットにプラズマは使えません。グラインダー等も試しましたが、一番正確にかつ変形を加えずにカット可能なのはバンドソー(コンター形態)でした。
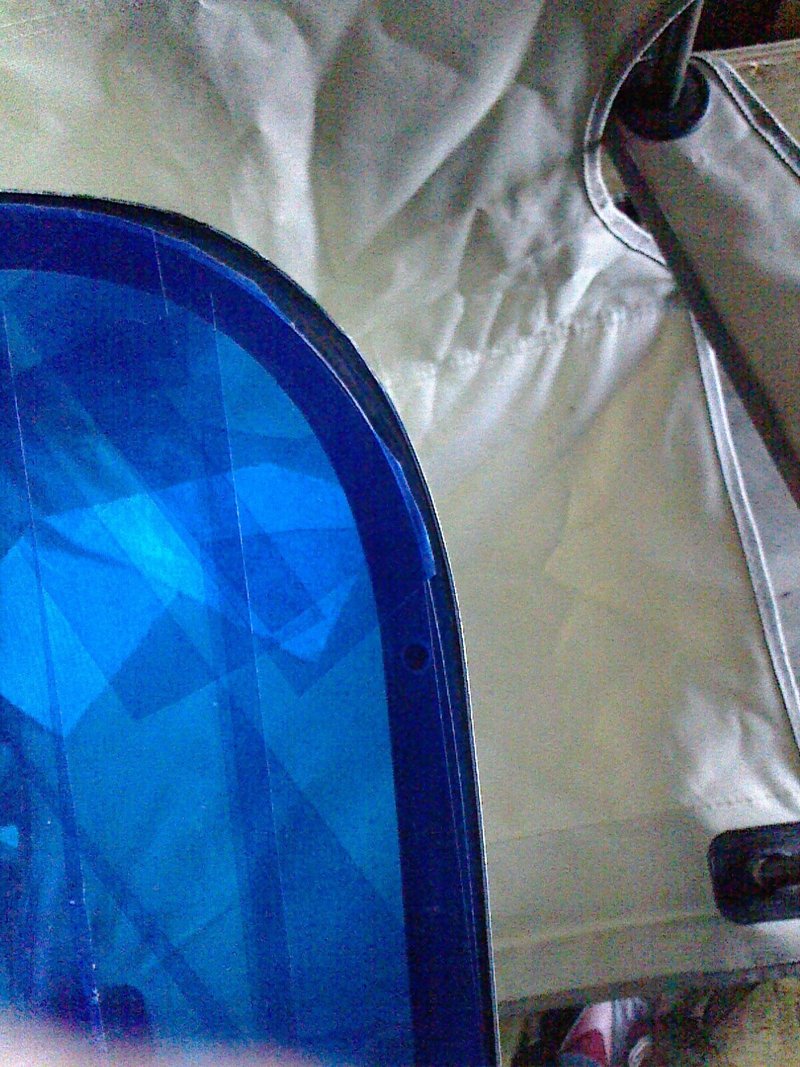
画像はありませんが純正枠とアメリカ製カバー(青は保護フィルムです)のフィットはウソみたいに正確で、パチンと収まりますがこれはダメですねビーディングで変形しています。
「では型紙を修正しよう」ではなくて、ビードローラー加工の限界なのです。↓
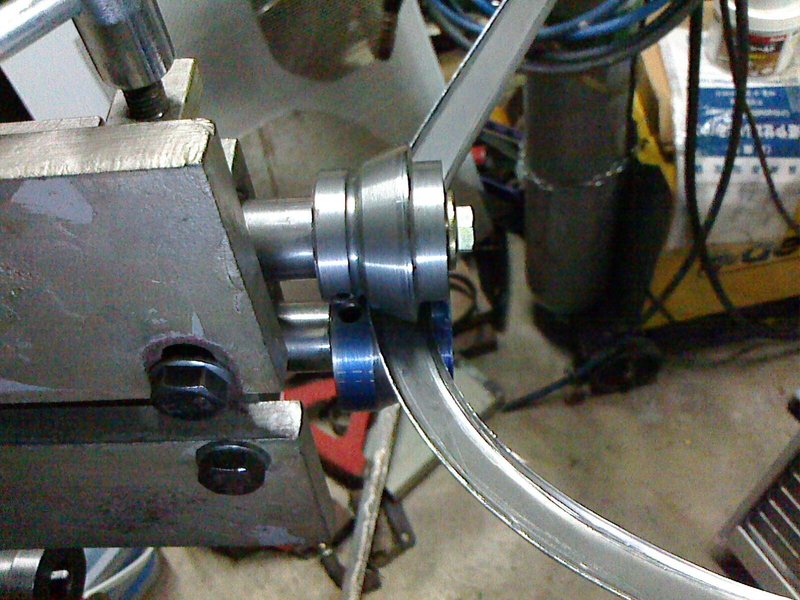
上下ダイで挟む面を斜面にしているのは、右側のフランジを起こしていく加工で下ダイの右の壁に内Rが干渉するのを回避するためです。
鉄板の曲がりに沿って進めていこうとすると上下ダイ同士が対向しているとこと離れたところが下ダイの右側フランジに当たっちゃうんです。↓普通に作るとこうですが、上の斜めダイセットよりゆるい曲がりしか加工できません。意味わからないむきに例をあげるとディスクグラインダー1ミリ厚切断砥石でR50の曲線を切っていくと切断切り口幅が1ミリより幅が広くなるのと同じです。
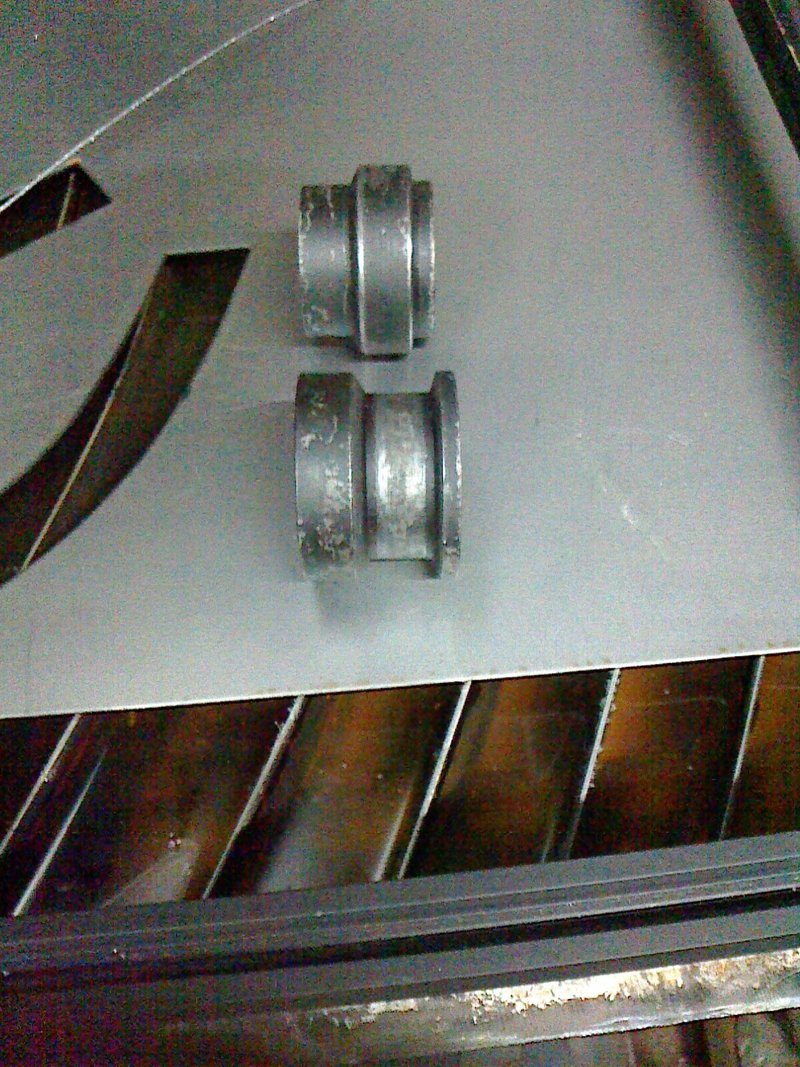
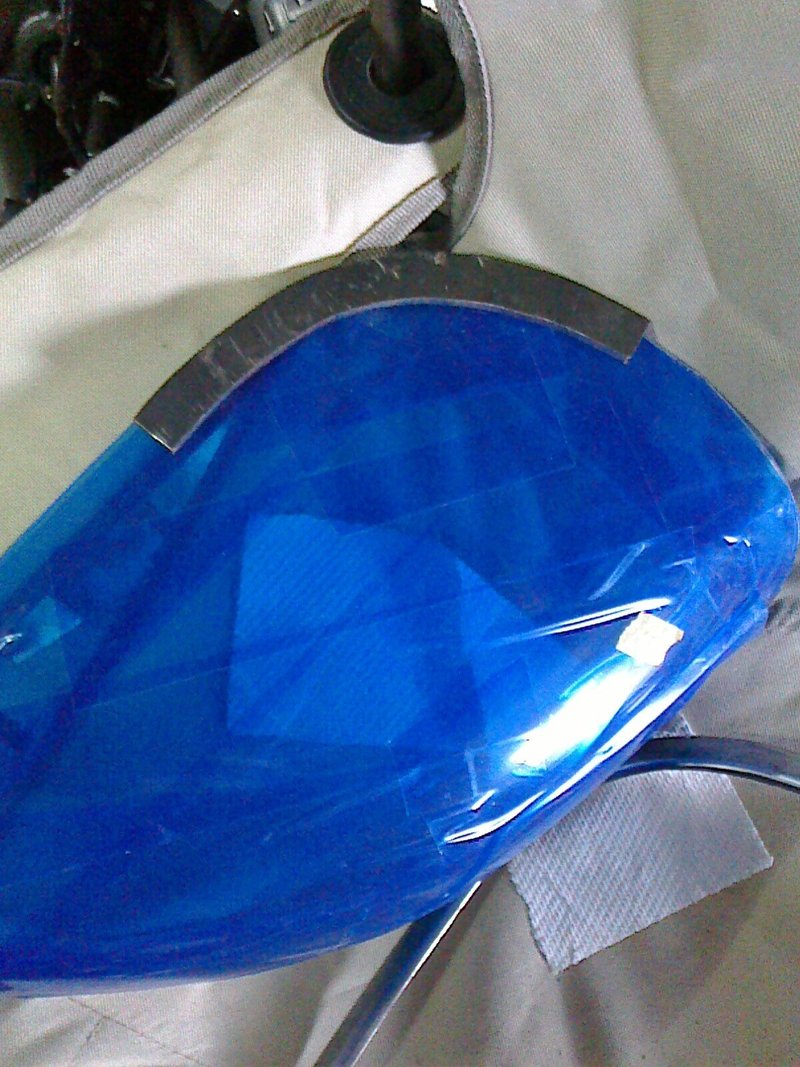
別のアプローチ法として叩くかプレスで押すダイも4年前に作っておいたので、この部分だけはビードローラー以外の方法で賦形する方法もあります。
なんにせよ一個目の試作の役目は終わり、プラズマカット2セットめに進みます。パスの修正は無しで。
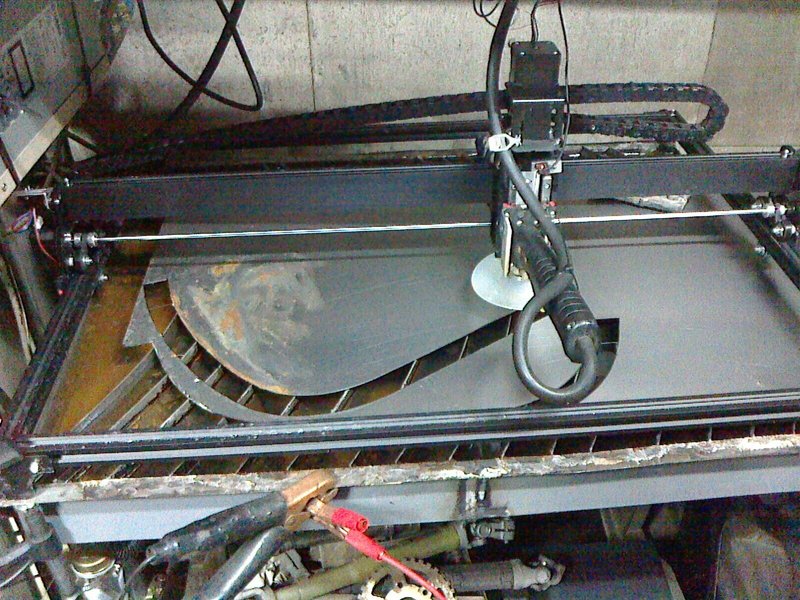
今日は位置決めまでで終わり。トレーの水で錆びてますが、あまりアルカリにしすぎるとヌルヌルするし塩ふいたように結晶ができるのでこのくらいで。
まとめ
プラズマCNCは図面通りにさくっと切断してくれるので試作がはかどります。