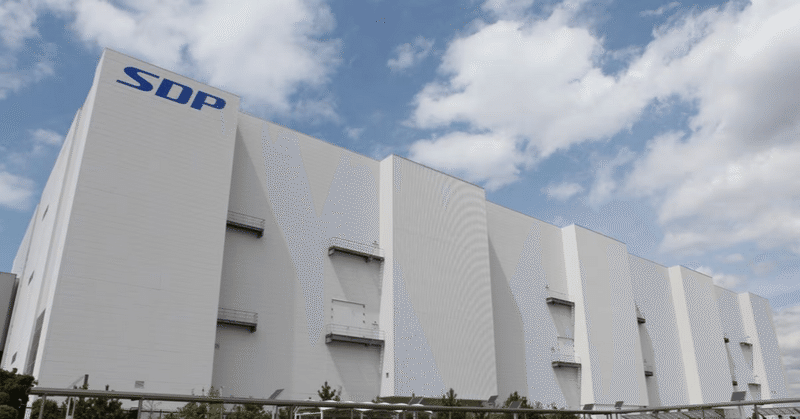
液晶工場の再活用
液晶工場の再活用とは?
最近、液晶工場が半導体生産の拠点として再活用される動きが広がっています。この動きは、日本の技術力を最大限に活かし、コスト削減と効率化を目指すもので、他の企業でも再現可能な成功ポイントが多く含まれています。
1. 液晶工場の現状
液晶工場の課題
液晶パネルの需要が減少し、多くの工場が稼働停止や生産縮小に追い込まれています。例えば、シャープの堺工場はテレビ向け大型パネルの販売不振で稼働率が一時1割まで落ち込みました。
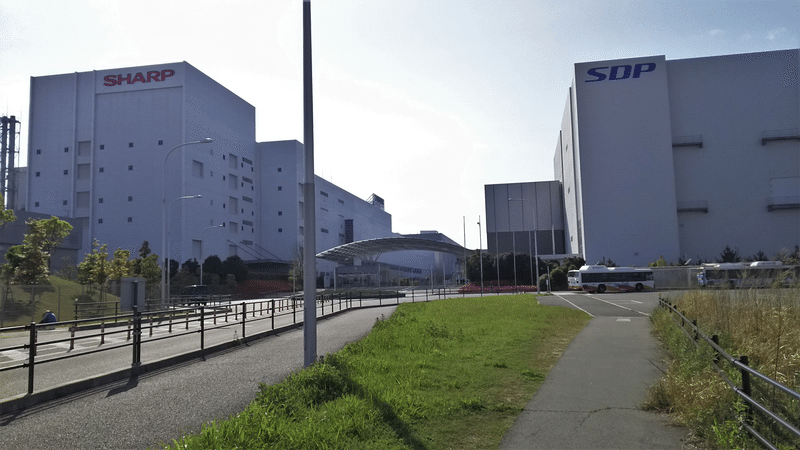
半導体への転用
一方、半導体産業は成長を続けており、液晶工場のクリーンルームやインフラ設備を活用することで、効率的に半導体の生産や研究開発を行うことが可能です。例えば、インテルはシャープの液晶工場を利用して、14社と協力して半導体の「後工程」を研究しています。
半導体の「後工程」とは?
半導体製造には大きく分けて「前工程」と「後工程」があります。
前工程: シリコンウェハー上に回路を形成するプロセス。これにはリソグラフィー、エッチング、ドーピングなどが含まれます。
後工程: 前工程で作成された回路を持つウェハーを個々のチップに切り出し、パッケージング(封止)し、最終的なテストを行うプロセス。これにはダイボンディング、ワイヤーボンディング、封止、テストなどが含まれます。
2. クリーンルームの活用
クリーンルームの利点
液晶工場には、微細なゴミやホコリを極限まで減らす特殊なクリーンルームが設置されています。これは半導体の生産や研究開発に非常に適しており、歩留まり(良品率)を高めるための重要な要素です。
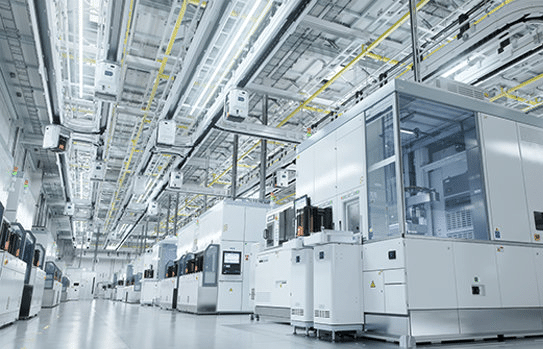
具体的な活用事例
シャープの亀山工場や三重工場では、クリーンルームを活用して新たな生産手法を確立する研究が進行中です。また、ラピダスはセイコーエプソンの液晶工場の一部を借りて、半導体チップの新構造を開発しています。
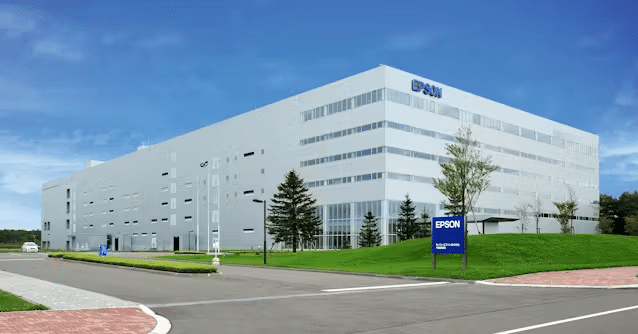
3. インフラ設備の再利用
インフラの共通点
液晶パネルと半導体の生産には大量の水や電力が必要です。このため、既存の液晶工場のインフラをそのまま半導体生産に転用することが可能です。
液晶パネルと半導体の生産には多くの水と電力が必要なのは、製造プロセスが非常に精密で、クリーンな環境を維持するために多くのリソースが必要だからです。
具体的には以下の理由が挙げられます:
洗浄プロセス: 半導体や液晶パネルの製造には、非常に高純度の水(超純水)が必要です。これは、製造過程で使用されるシリコンウェーハやガラス基板を洗浄するためです。不純物が少しでも混入すると、製品の品質に重大な影響を及ぼす可能性があります。
化学処理: 製造プロセスでは、多くの化学薬品を使用します。これらの薬品を適切に処理し、洗浄するために大量の水が必要です。
冷却: 製造装置やプロセス中に発生する熱を冷却するために、水や電力が使用されます。特に、半導体製造では多くのエネルギーが消費されるため、冷却が重要です。
クリーンルームの維持: 半導体や液晶パネルの製造には、微細な塵や汚染物質のないクリーンルームが必要です。クリーンルームの維持には、空気清浄機や湿度調整機器が使用され、これらが大量の電力を消費します。
プロセスの複雑さ: 半導体の製造プロセスは非常に複雑で、多くの工程を経る必要があります。各工程で使用される装置や機械が大量の電力を消費します。
これらの理由から、液晶パネルや半導体の生産には大量の水や電力が必要とされます。
成功ポイント
例えば、三菱電機は熊本県の液晶パネル工場を停止し、その敷地内に次世代半導体の製造棟を建設しました。このように、既存のインフラを最大限に活用することで、新たな設備投資を抑えつつ、生産能力を拡大することができます。
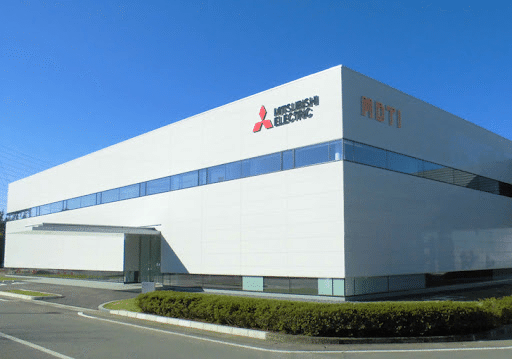
4. 液晶技術の転用
液晶技術の可能性
液晶技術そのものも、次世代半導体の仕上げ工程に応用される可能性があります。ガラス基板に微細な回路を描く技術は、省電力や良品率向上に寄与することが期待されています。
ガラス基板に微細な回路を描く技術が省電力や良品率向上に寄与する理由は以下の通りです:
省電力:
回路の微細化:回路が微細化されることで、電流が流れる距離が短くなり、抵抗が減少します。これにより、電力消費が低減します。
効率的な設計:微細な回路設計により、電子デバイスの効率が向上し、不要な電力消費を抑えることができます。
低消費電力の材料:微細回路の製造には、より低消費電力の材料や技術が使用されることが多く、これも省電力に寄与します。
良品率向上:
高精度な製造プロセス:微細な回路を描くための技術は非常に高精度なプロセスを必要とします。この高精度なプロセスにより、不良品の発生が抑えられます。
均一性の向上:微細な回路を描く技術は、基板全体にわたって均一な品質を保つことができるため、製品のばらつきが減少し、良品率が向上します。
検査技術の進歩:微細回路を描く技術の発展に伴い、検査技術も高度化しています。これにより、製造過程における欠陥を早期に発見し、修正することが可能となります。
これらの要因が組み合わさることで、ガラス基板に微細な回路を描く技術が省電力および良品率向上に大きく寄与しています。
研究開発の進展
インテルやラピダスは、この技術を活用して新たな半導体チップの開発を進めています。これにより、液晶生産設備の一部も再活用される見通しです。
5. 日本の技術力と未来
日本の強み
日本には、多数の液晶生産設備と高度な技術が残されています。政府の半導体復権政策もあり、これらの資産が再び脚光を浴びることとなっています。
他社への影響
他の企業もこの動きに倣い、既存の工場や技術を最大限に活用することで、コスト削減と効率化を図ることができます。例えば、液晶工場の再活用は、初期投資を抑えつつ、新たなビジネスチャンスを創出する手段となり得ます。
液晶工場の再活用は、日本の技術力と資産をフルに活かす戦略であり、他の企業にとっても非常に有益なモデルとなるでしょう。
既存のインフラを最大限に活用し、新たな設備投資を抑えつつ生産能力を拡大する成功事例
テスラ社の「ギガファクトリー」の戦略が挙げられます。
テスラのギガファクトリー戦略
テスラ社は電気自動車(EV)の大量生産を目指して、世界各地に「ギガファクトリー」と呼ばれる巨大な製造施設を建設しています。これらの施設の建設と運用において、テスラは既存のインフラや資源を巧みに活用することで、設備投資のコストを抑制し、生産能力を効率的に拡大しています。
既存インフラの活用例
再生可能エネルギーの活用: テスラのギガファクトリーは、太陽光発電パネルや風力発電を積極的に導入し、エネルギー効率の向上と運用コストの削減を図っています。これにより、工場の持続可能な運用が可能になります。
地域資源の活用: テスラは、工場の立地を選定する際に、地域の資源やインフラを考慮します。例えば、ネバダ州にあるギガファクトリー1では、近隣のリチウム鉱床を活用することで、バッテリー生産に必要な原材料の確保を行っています。
既存施設の再活用: 新たなギガファクトリーを建設する代わりに、既存の工業施設や倉庫を改修して利用することもあります。これにより、建設期間の短縮や初期投資の削減を実現しています。
生産能力の拡大への貢献
これらの戦略により、テスラはバッテリーや電気自動車の生産コストを低減し、生産能力を大幅に拡大させることに成功しています。特にバッテリーのコスト削減は、電気自動車の普及拡大において重要な要素となっています。
テスラのギガファクトリー戦略は、既存インフラの最大限の活用を通じて、新たな設備投資を抑えつつ生産能力の拡大を実現した典型例と言えます。この戦略は、他の製造業においても参考になるモデルとして評価されています。
引用:2024/06/07 日本経済新聞 朝刊 14ページ
この記事が気に入ったらサポートをしてみませんか?