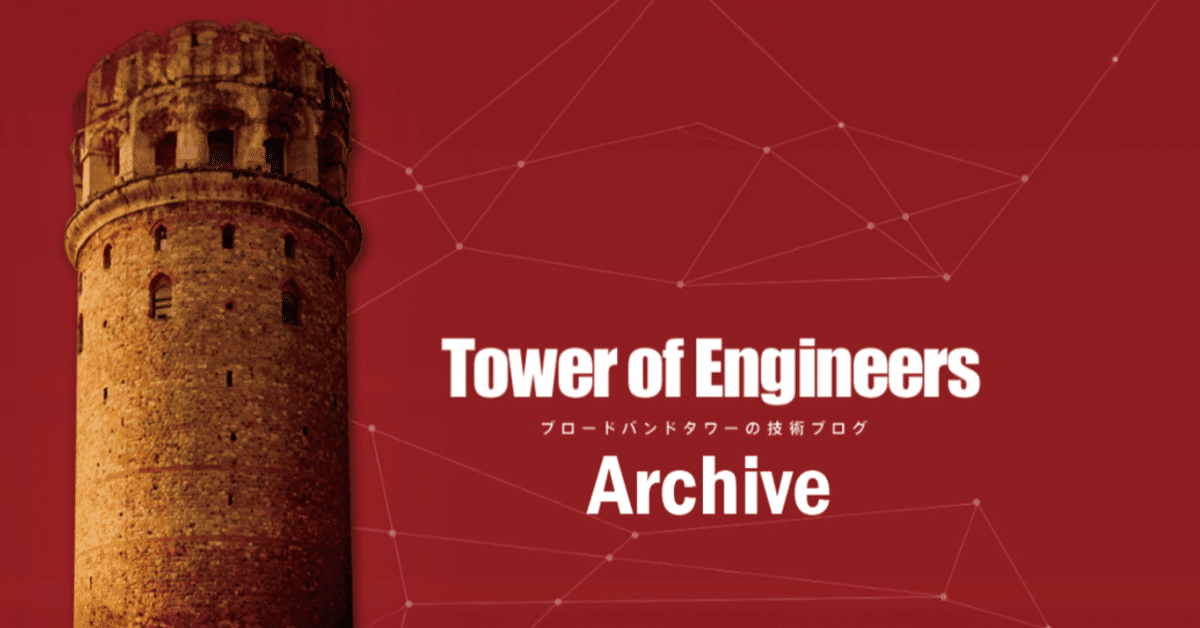
【2020年1月20日掲載】ユーザは見た!光トランシーバ製造工場訪問記
ご無沙汰しています、佐伯です。
今回は、株式会社マクニカさんと、FINISAR Japanさんのご厚意により、FINISAR(フィニサー)社の光トランシーバの製造工場を見学することが出来ました。写真及び詳細担当:研究所加藤、文面担当:佐伯で訪問記をお送りします。
1. はじめに
皆さん、光のトランシーバは使ってらっしゃいますか?スイッチやサーバを接続するとき、機器側にぽっかり空いている孔に差し込む金属のモジュールです(図1参照)。
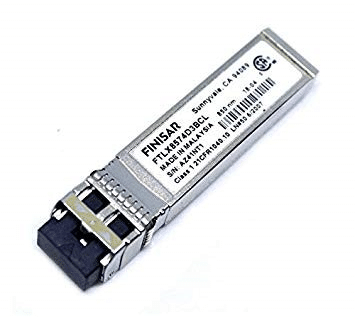
速度や形状に基づいてそれぞれ名前がついており、図1で示す光トランシーバは、10Gbps用の「SFP+(エスエフピープラス)」です。ほとんどの光トランシーバは、MSA (Multi-Source Agreement) やSNIA (Storage Networking Industry Association) に従って、詳細が取り決められており、私たちはこれらの規格に則ったものを使っています。
では、具体的にこの光トランシーバの中身はどうなっているのでしょう?図2に光トランシーバの中身について概要を示します。実際には、もっといろいろあるのですが、この3つの部品がキーポイントになります。
TOSA Transmitter Optical Sub-Assembly
ROSA Receive Optical Sub-Assembly
送受信回路
1-(1) TOSA
データを送出するための光源等が入っています。10Gbpsまでは1つの光源を収容するだけで済んでいましたが、40Gbps・100Gbps時代に突入し、ここに4つの波長の光源が収容されるケースも増えました。
1-(2) ROSA
データを受光するためのPD (Photodiode) 等が入っています。TOSA側の光源が複数になった場合は、受光側のPDも複数波を感知し、回路に情報を送る必要があります。
1-(3) 送受信回路
機器から送られてきたデータをTOSAに送信する、若しくはROSAから来た光信号を機器に戻す部分になります。
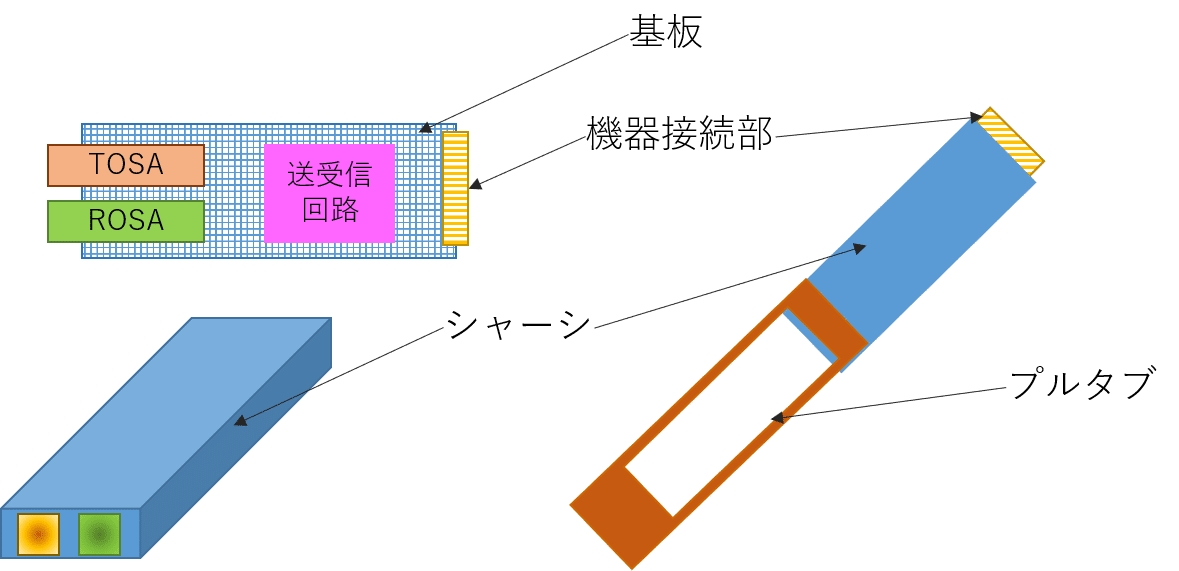
これらの部品を決められた寸法のシャーシに納め、十分な光学及び電気特性を提供することが、光トランシーバに求められています。
2. FINISAR社概要
今回、見学したFINISAR社は、光トランシーバメーカとして30年以上に渡り豊富な実績を誇る会社です。実は2019年9月にII-VI(ツーシックス)社と合併しました。光学部品を扱うメーカ同士の大型合併ということで、業界は大騒ぎでしたが、両社の強みを生かした合併が行われ、今後益々この技術力が世界市場で優位に立ち続けると私は信じています。
今回の訪問記は、II-VI社と表記するよりFINISAR社の名前の方が、私だけでなく皆さんにも通りが良いと思いますので、以下FINISAR社と表記します。
2-(1) 市場での位置づけ
2016年と少し古いデータですが、図3に光トランシーバ市場のシェアについて示します(既にいくつかの会社は合併して会社名が残っていないものもあります)。当時からFINISAR社は世界市場で第1位のシェアを誇っていたことが分かります。この傾向は、昨今の中国勢の振興の中、現在に引き継がれているようです。
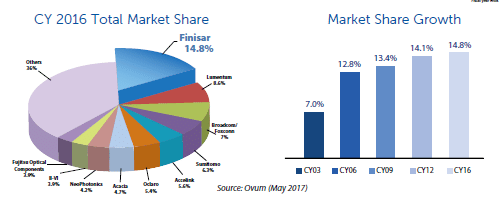
この世界最大級のシェアを誇る光トランシーバメーカであることから、その製造規模から製造される製品の品質に至るまで、大変興味がありました。ですので、今回の工場訪問は非常にワクワクしていました。
2-(2) 工場へGO
クアラルンプール国際空港から、クアラルンプール市街を抜けてイポーまで車で移動です。道中激しいスコールかと思えば、いきなり日差しが照り付けるなど、とてもにぎやかな天候でした。
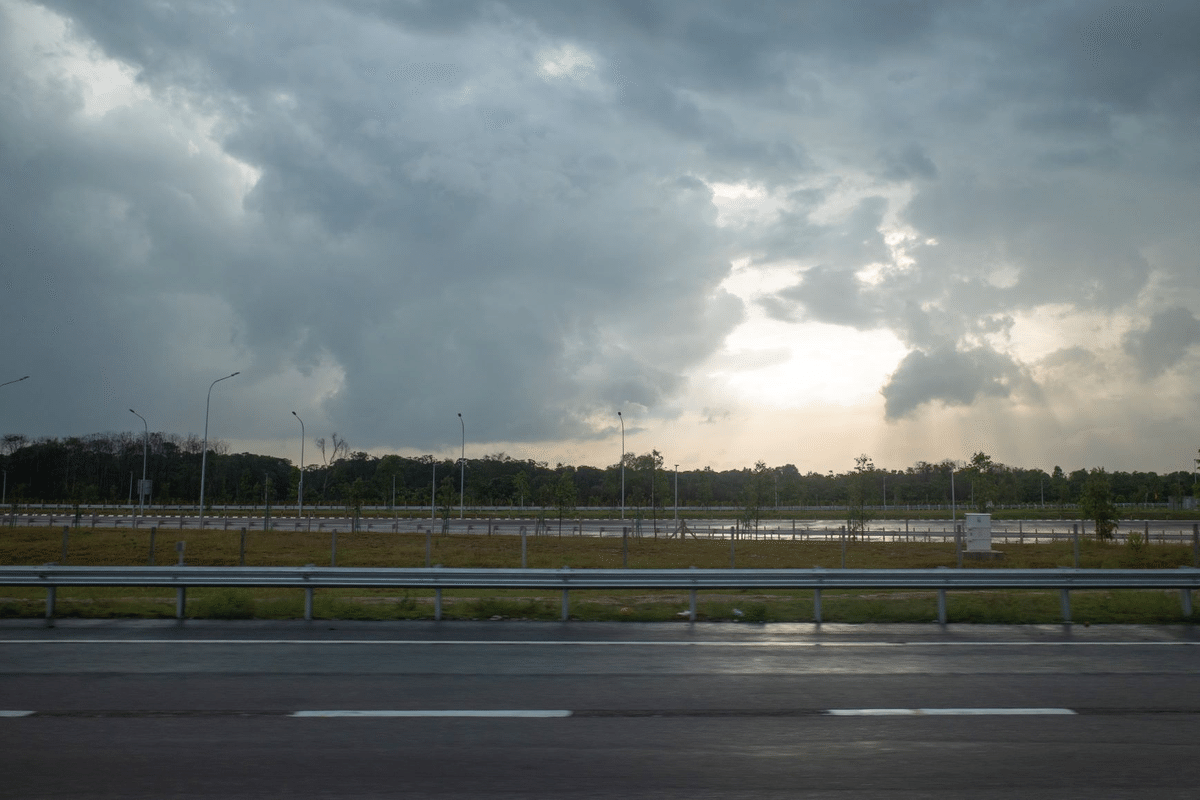
日本にたとえると、成田空港から高速道路を利用して約200km、ちょうど空港から都心を抜けて浜松あたりの距離に位置しています。さて、見えてきたマレーシア工場ですが、ロゴが現在より1世代程度前のもののようです。古くから知っているものとしては、何とも懐かしい気持ちになりました。この場所は、他にも有名な企業の工場が幾つも並ぶ工業団地の一角にあります。
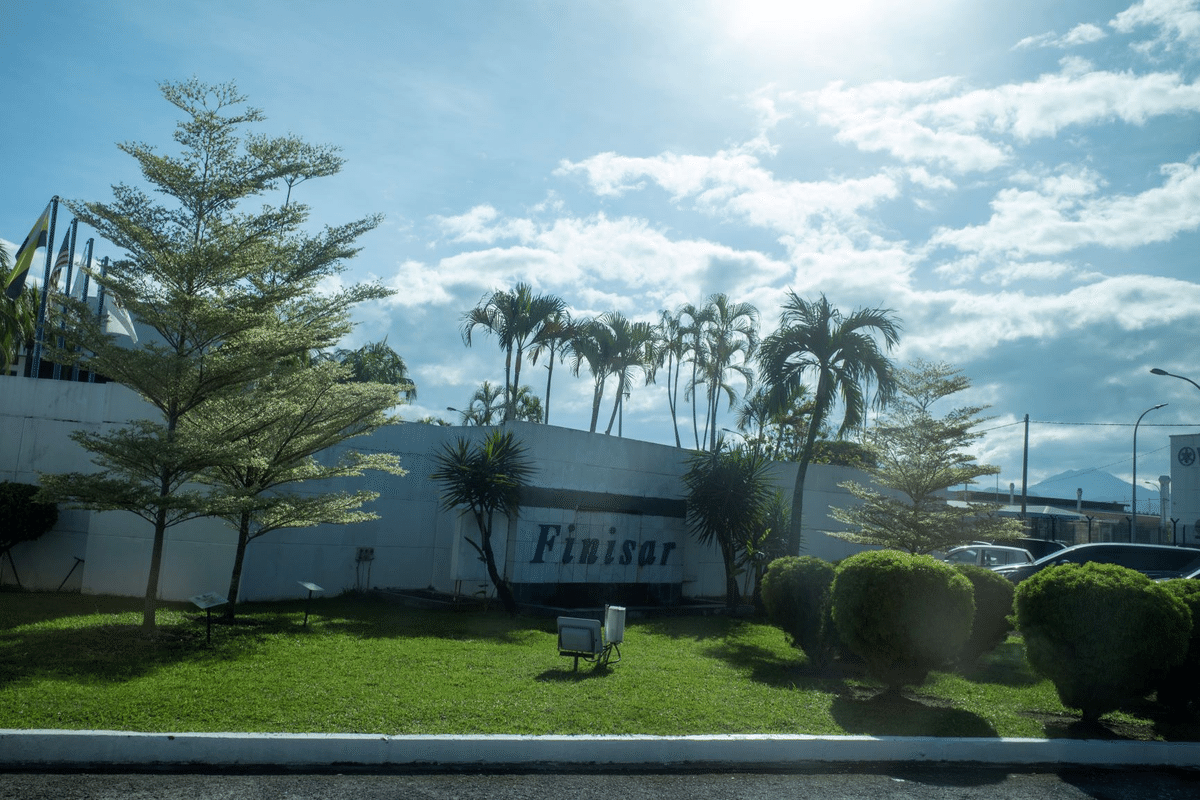
工場正面は、こんな感じです。白い外観がとても印象的でした。

図4に示すように、現在FINISAR社は北米/中国/マレーシアの3か所にそれぞれ異なる役割の工場があります。北米/中国それぞれの工場で作られた部品をマレーシアで組み立て・検査・出荷しています(※一部例外有り)。約1個/2秒に製品を製造する工場とはどのような工場なのか、とても期待が膨らみます。
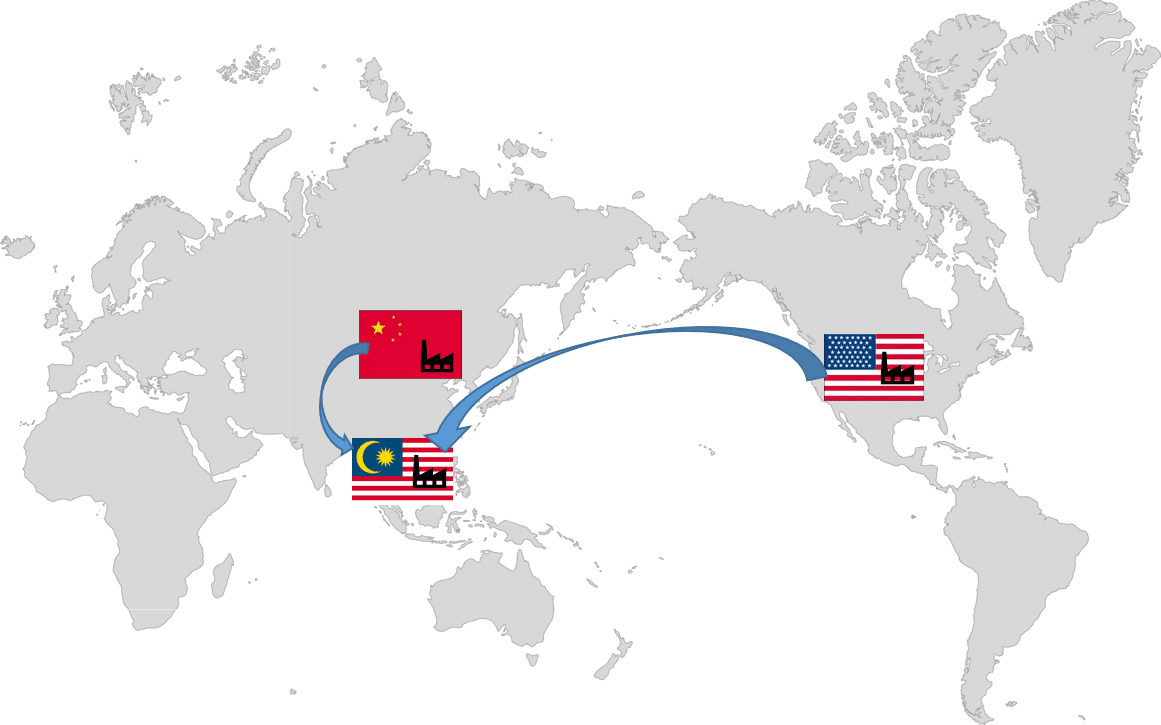
3. 工場見学
マレーシア工場は約7000名(2014年) の従業員の方が働いています。これらの中には、製造の現場で働く人の他、納期管理や、品質保証部門があります。更に不具合品の解析を行うエンジニア、独自の製造機器の設計や工程をブラッシュアップするエンジニアなどが含まれます。先ずはマレーシア工場の製造工程について、図5に示します。
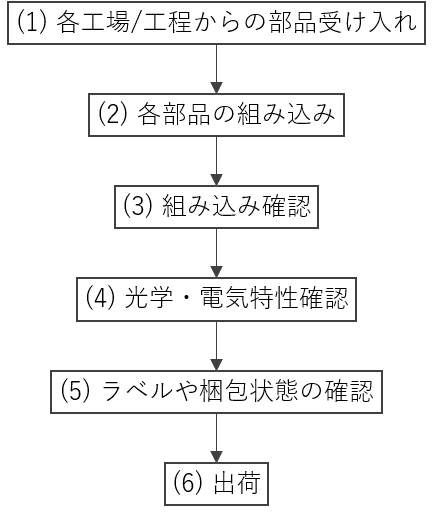
3-(1) 各工場/工程からの部品受け入れ
各工場から完璧な状態で出荷されていても、必ず受け入れ試験を行っています。また、受け入れ後の製品の保管/次工程へ送るための流れも十分管理されていました。
3-(2) 各部品の組み込み
先ほどの図2で示した「TOSA」「ROSA」「送受信回路」を接続し、シャーシに組み込む作業です。人手を介するため、工程も多く作業内容も複雑でした。それをスマートにこなしていく作業者の皆さんはとても格好良かったです。
3-(3) 組み込み確認
図2の下の図のようになります。シャーシの各寸法を測定するなど地味な工程ですが、マイクロメータなどの数値の読み取り及び判定は全て自動で行っていました。作業者が目で数値を確認し手で数値を記載、合否判定することがありませんでした。難しい光学的/電気的な測定値だけでなく、全てのデータが、電子的に処理されているのはすごいと思いました。
3-(4) 光学・電気特性確認
外観で問題なければ、次に光学・電気特性についてのチェックになります。ここでは、高温や低温での光トランシーバの動作確認などを行います。これも各小工程とも、自動/手動の作業が複雑に絡み合っていました。
また、Ethernetの光トランシーバの場合は、1Gbps時代には不要であっても10Gbps以上の速度では、必ず「Stressed receiver sensitivity」試験を実施する必要があるなど、Ethernetの進化に合わせて、製造ラインの追加、更に新たな測定装置が必要になることを知りました。1Tbps時代には更に新たな測定試験が追加されるかも知れませんが、きっとこの生産体制であれば、スムーズに工程に取り込めることが出来るのだろうと、頼もしく感じました。
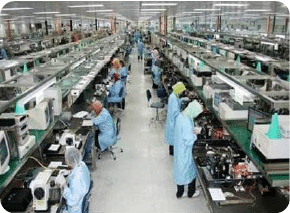
3-(5) ラベルや梱包状態の確認
寸法や光学・電気特性が合格した後は、外観・ラベリングの工程に入ります。光トランシーバの外側に指定色のプルタブを付けたり、一元管理のためのバーコードシールの貼り付けを中心に、光トランシーバ内のEEROMに書き込まれている内容と、バーコードの示す内容が合致しているか?など、細かいチェックの連続でした。また、ラベルも自社ブランドのラベルだけでなく、機器メーカの名前の場合もあり、ラベルが曲がっていないか?印字は鮮明か?など、目視以上の細かいチェックが行われていました。
3-(6) 出荷
こうして、長い工程を経て最後に出荷となります。ここに来るまでには、何回も全数検査/抜き取り検査が行われており「もうこのタイミングで不良品は出ないだろう」と、思うような工程で「いや、ゼロでは無いのです。だから全工程、1つも外す訳にはいかないのです」という説明を受けた時には「日本の製造メーカで、ここまでやっているところがどれくらいあるのか(ここまで厳しいところは、なかなか無いのでは)?」と思いました。
また全体を通して、製造装置のメンテナンスや、測定装置の校正だけでなく、測定に使われる光コードなども利用する回数が厳しく決められていました。また作業者が「うっかり新しい光コードに代えそびれた」が無いような工夫も施されており、決めたことを守るしくみが徹底されていることが、とても良く分かりました。
4. 高品質な製品を安定供給するための工夫
FINISAR社が高品質な製品を安定して供給するためには、ISO9001やISO14000などの継続監査以外にも、沢山の項目を挙げていました。中には「5S」という説明もあり、とっさに日本語で全部出てこなかった自分が、ちょっと恥ずかしかったです。その中でも、彼ら独自に挙げていたポイントを3つ紹介します。
不具合品は徹底解明する
人手を介す作業は、治具等を用いて品質の均一化を図る
オールFINISARとして、製品を一元管理する
4-(1) 不具合品は徹底解明する
出荷した後に発生した不具合品の戻入だけでなく、各工程で発生した不具合品も全てラボに持ち込まれ、不具合が発生した原因について、徹底解明します。そして、その原因を製造工程にフィードバックしています。
製造に必要な装置類も全てFINISARのエンジニアの手が入っています。必要に応じて製造装置の改良を行い、その工程を製造するのに最適化を行っています。各工程の歩留まりを常にチェックし、品質を担保しながらコストの低減を図っていることが良く分かりました。
4-(2) 品質の均一化のための取り組み
製造工程では手動の工程も存在しています。人手を介すると、どうしても品質のばらつきが発生してしまいます。そこで、作業者の誰が実施しても均一になるよう、専用の治具を内製し用いていました。ちょっとした作業であっても、必ず治具が用意されていることは、本当に微細な工程まで知り尽くしているエンジニアたちの目が行き届いていると感心しました。
更に作業者全員への教育も充実しています。入場前教育は、単に教えられるだけでなく、テストを行い、一定の水準以上のスキルを取得した方のみ、現場で作業することが出来ます。また作業者の皆さんも、定期的にスキルテストがあり、それに合格しないと作業を続けることが出来ません。この仕組みを作っているのも、FINISARのエンジニアたちです。こうして人的な取り組みも行うことで、品質が維持・向上されていることがよく分かりました。
4-(3) 製品の一元管理
それぞれの工場や工程で製造された部品や完成品は、一元管理されているため、製造番号をチェックするだけで、製造から検査結果、出荷まですべての履歴を追うことが可能です。製品の製造工程が複雑であるにも関わらず、仕掛品1つ1つが、どのタイミングであっても、その時点での品質状況がバーコード1つで直ぐに分かる具合は、とても近未来な感じでした。
FINISAR社が製造しているトランシーバは、自社ブランドと機器メーカのOEMの2種類があります。いずれのパターンもラベルが違うだけで、厳密なテストを経た同じ品質であることが、改めて良く分かりました。
5. まとめ
製造工程は、多岐に渡っていましたが、自動化するべきところは自動化し、手動の方が効率よいところはそれとして区別し、工程を組んでいました。それぞれ自動/手動の流れが複雑でしたが、製品を1つずつトレースする仕組みがしっかりしているため、製品の完成までに無駄な工程が全くありませんでした。またそのトレースする仕組みは、各工場内での情報共有に留まらず、オールFINISARのデータベースとして製品の一元管理が可能になっていました。更に、作業者の皆さんが高度なスキルを持ち続ける仕組みが出来ていることもとても素晴らしかったです。
また、自社ブランドと機器メーカOEM製品の製造工程が分け隔て無く作られていることから、自社ブランドを購入しても、問題なく動作する理由がより明確になりました。
6. 最後に
Made In Malaysiaのラベルから想像していたマレーシア工場は、地図にも掲載されていない秘密の島で、熱帯雨林に囲まれた中にひっそりたたずむ建物で、一度踏み入れたら見学が終わるまで出られない環境かと想像していました。しかし、実際には全くそんなことは無く、オープンで明るい工業団地の一角にあり、とても通い易い環境にありました。もちろんセキュリティやクリーン度は、とても厳しい場所もありますが、その緩急の付け所が整然としており、工場としてとても成熟していると感じました。
日本の場合は、サードパーティ製を利用することについて、そもそもの認知度が低かったり、安価であることが却って「安物買いの銭失い」的な恐れがあるのではないかという、先入観から、購入に踏み切れないケースも見受けられます。しかし、製品の品質的には全く問題ないことを理解するのに十分な見学でした。
改めて、本見学をアレンジして頂いた、株式会社マクニカさん及びFINISARマレーシア工場の皆さん、FINISAR Japanさんに厚くお礼申し上げます。
最後に、工場受付の模様(FINISARさんの許可済)と、ペトロナスツインタワーの車窓をお届けして、今回の訪問記を終わりたいと思います。ありがとうございました。
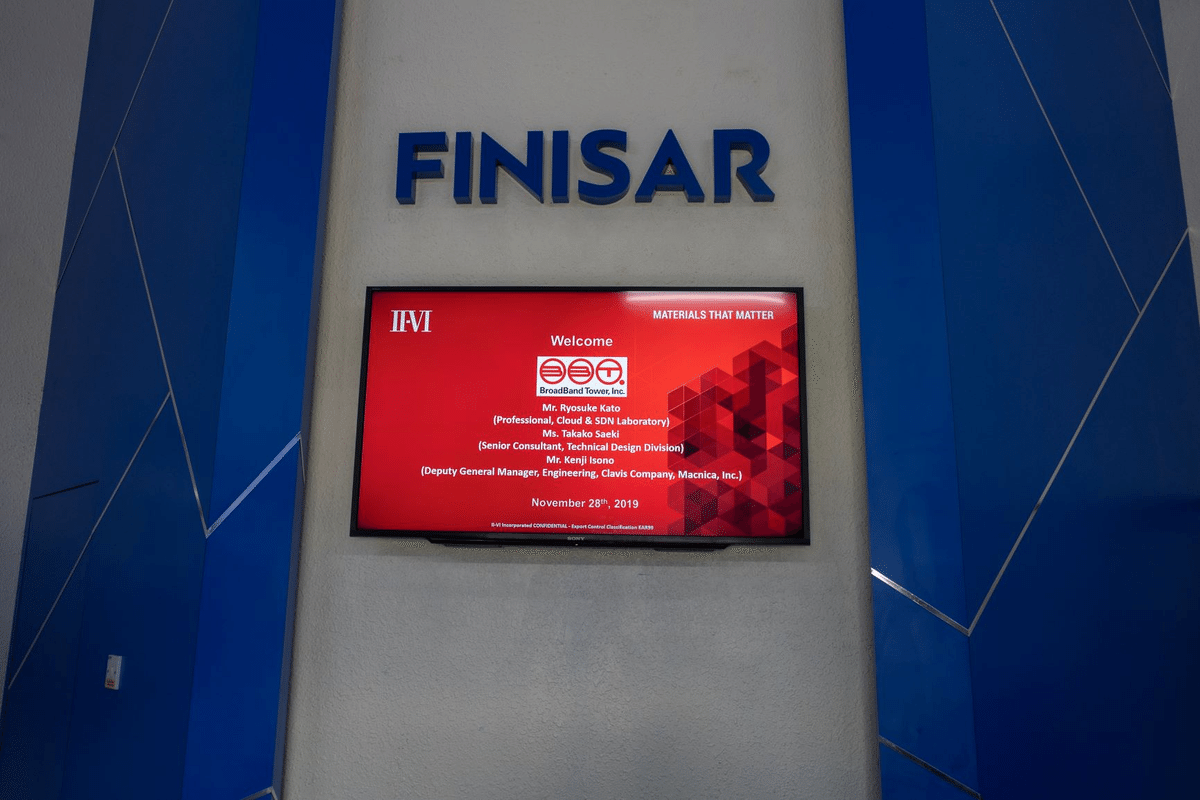
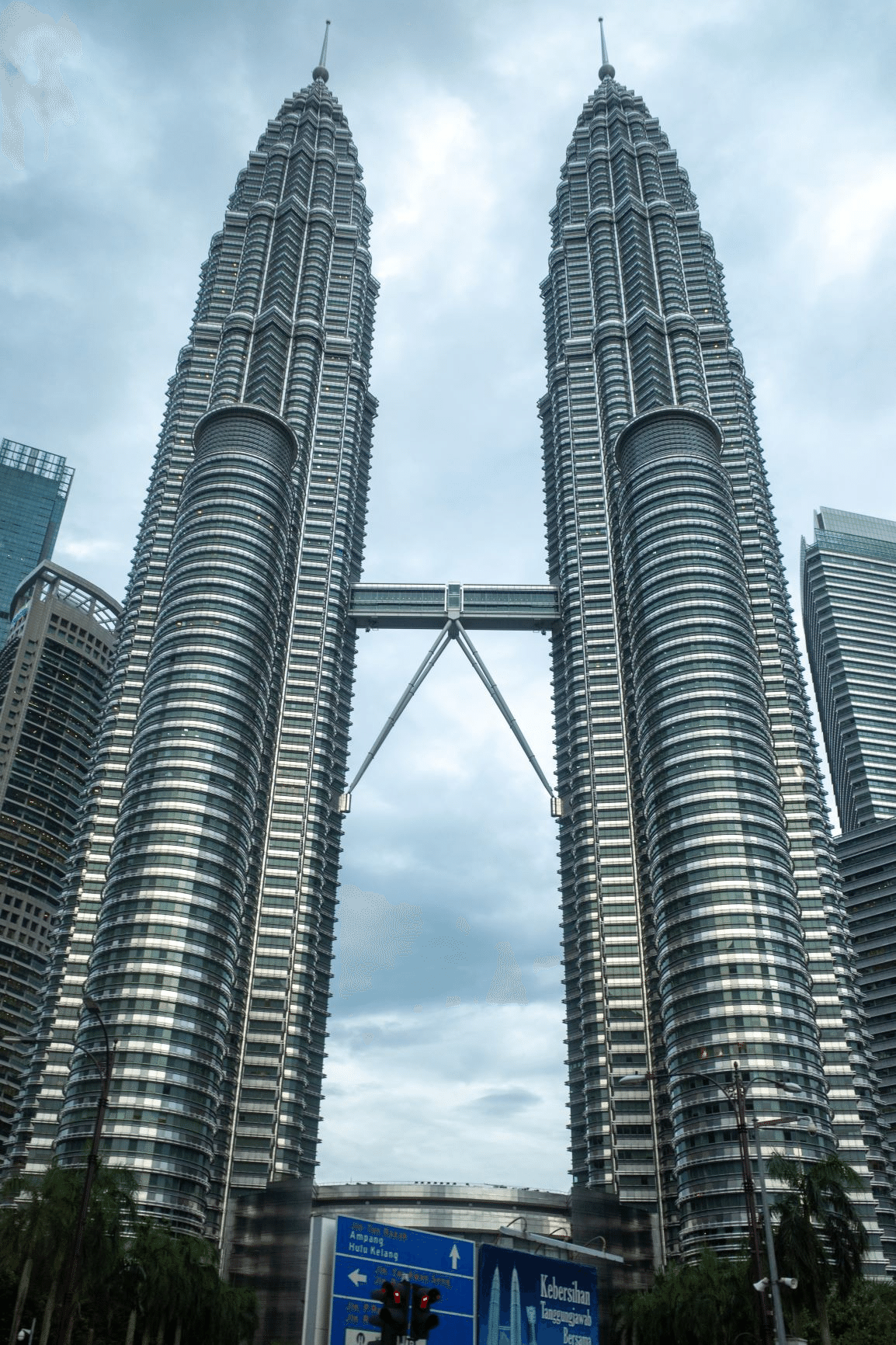
(完)
ブロードバンドタワーのエンジニアブログ『 Tower of Engineers 』で公開されていた記事をnoteに再投稿させていただきました。
過去(2020年1月20日掲載)のものではありますが、皆様に再び楽しんでいただけると嬉しいです。これからも、価値ある記事や興味深い内容を、noteでシェアさせていただく予定です。どうぞ楽しみにお待ちください。