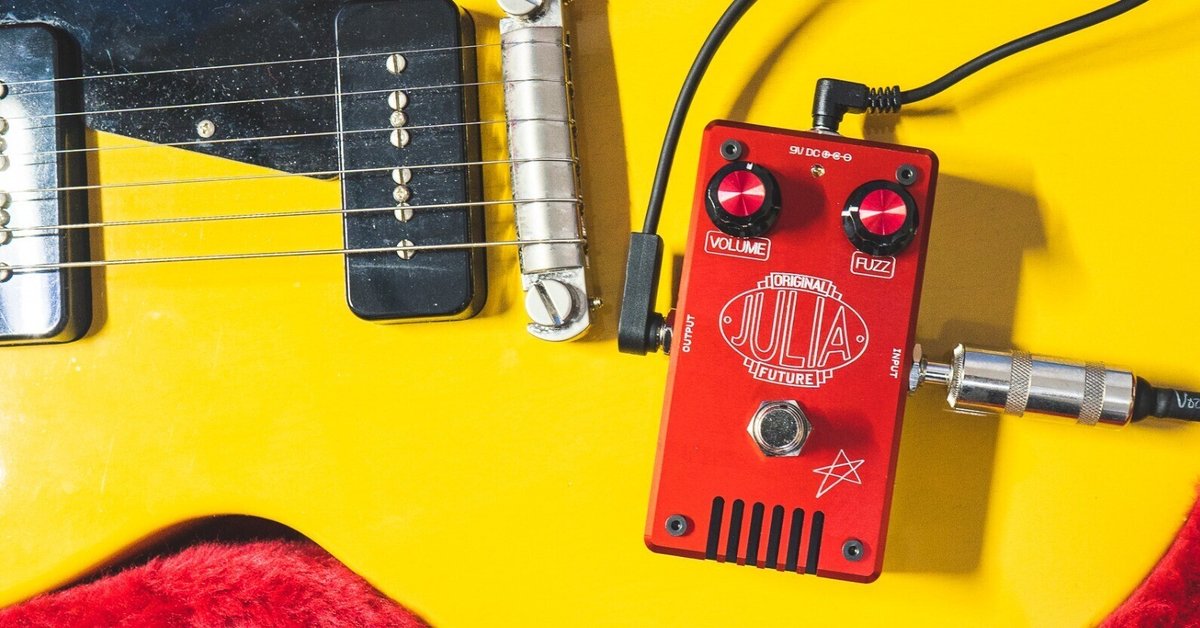
担当をイメージしたエフェクタを作った話
TL;DR
ミリオンライブのジュリアをイメージしたエフェクタを作りました!
エフェクタケースの設計、アルミ削り出し、アルマイトと部品の実装まで全部自分でやりました!
ISF10で展示予定です。
注意:以下作業内容について説明が続きますが、金属切削、アルマイトについては先月から独学で得た知識を元に初めて行ったものであり、文章は完全に経験日数1ヶ月未満の素人が書いています。したがって内容については正しくない部分があるかもしれませんので、万が一実行される際は自己責任でお願い致します。
以下散文
「ある日、僕は研究用の材料を揃えに秋葉原を歩いていた。買い物もとりあえず終わり、ラジオデパートの中にある店をなんとなく眺めているとカラフルなものが目に入った。それはアルミダイカストの自作用エフェクタケースだった。」
エフェクタというのは、ギターとアンプの間に挟んで、音の調子を変えたりノイズを取ったり載せたりするような機器のことです。たまたま見つけたお店は、そんなエフェクタを自分で作りたい人向けの部品やキットを販売しているお店でした。面白そうと思ってケースを2つほど買って、色々と試してみました(下記ツイートの左下と中央下)。基本的にはケースにノブやジャック用の穴を開けて(最初から穴の空いてるケースもありました)、エフェクタキット(基板、ポット、トランジスター、ダイオード、抵抗、コンデンサー等)の部品を組み込み、はんだ付けして配線するだけで自作できます。
試行錯誤中… pic.twitter.com/pbyM0Cd1jR
— じりおん@ISF10 G-34 (@zillione) March 30, 2023
そこでひらめいた。
最近、卓上 CNCフライスを導入したので、アルミケースまるごと自作は無理でも、ケースの上面を装飾するプレートくらいなら削り出せるのでは、と。手順としては設計→切削→アルマイト→彫刻という順番です。まず設計はFusion360というソフトを使って3DCADの図面を作成し、その後CAMデータを作成してGコードを出力します。CAMデータとは3D CADのモデルに対して工具の移動パスなどの切削手順を定めたものです。Gコードは、実際にCNCを動かすコントローラに入力されるプログラムです。次のツイートは、Fusion360のCAD作成画面です。
ふむふむ pic.twitter.com/2wW3nxPXzl
— じりおん@ISF10 G-34 (@zillione) March 30, 2023
続いては切削です。切削というのは、専用の刃物で金属を削って加工することです。CNCフライスは、エンドミルという刃物を回転さえて被削材(ワークとも言います)を削り出す機械です。
今回の被削材は板厚t2mmのA5052(アルミ合金の一種)です。アルミ合金としては他に、A2017(ジュラルミン)やA6063(押出用材料)、A7075(超超ジュラルミン)などたくさん種類がありますが、A5052はアルマイト施工時の剥離剤(後述)でスマットが出なかったり、耐食性と強度のバランスがよいなどの利点があります。
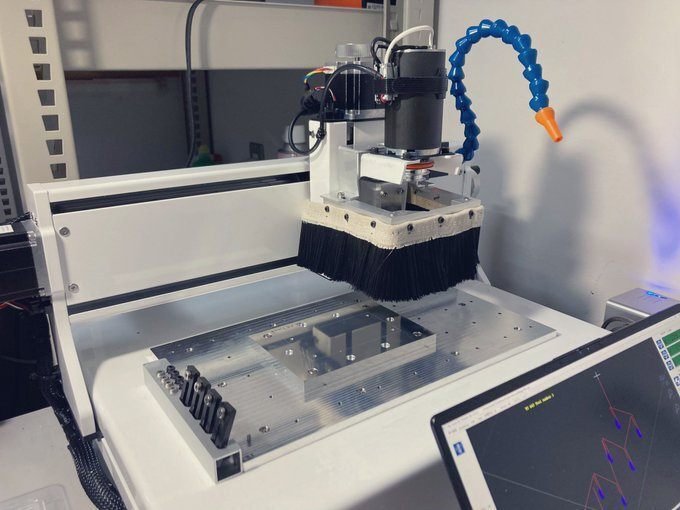
↓は削ってる様子。
これがこうなってこうじゃ pic.twitter.com/ShzBnSwDFf
— じりおん@ISF10 G-34 (@zillione) March 31, 2023
切削が終わったらアルマイト(陽極酸化処理)をかけます。なんとアルマイトは自宅でできます(自分は休みの日に職場でやりました)。
アルマイト中の画像はないんですが、手順はざっくりと次のとおりです。
「表面剥離」剥離剤(強塩基性)にワークを浸けて、アルミ表面を溶かし、素の材料を露出させます。マスク必須。
「電解研磨」アルミ材料を陰極、鉛板を陽極に接続して希硫酸を入れた容器に浸けて直流電流を流し、アルミ表面を電解研磨します。目的は表面剥離と同じで、地の材料を露出させます。マスク必須。
「陽極酸化処理」これがアルマイトです。電解研磨とは逆にアルミ材料を陽極として電気分解して陽極酸化皮膜というものを作ります。マスク必須。
「染色」陽極酸化処理が終わったら、55℃前後に温めた染色液に浸けてアルマイトに色を乗せていきます。陽極酸化皮膜が生成できている部分にだけ色が入るので、ここが一番のドキドキポイントです(うまく行かなかったら最初からやり直し)。
「封孔処理」酢酸ニッケル(沸騰水でも可らしい)で煮沸して、酸化被膜の細かい穴を塞ぎます。マスク必須。
アルマイトの方法は、なん重さんの動画(https://www.youtube.com/watch?v=JncglZ3RRuw)を参考にしました。剥離剤の工程を入れると失敗が少なく、また万が一失敗しても剥離剤でアルマイトを剥がせばやり直せます。
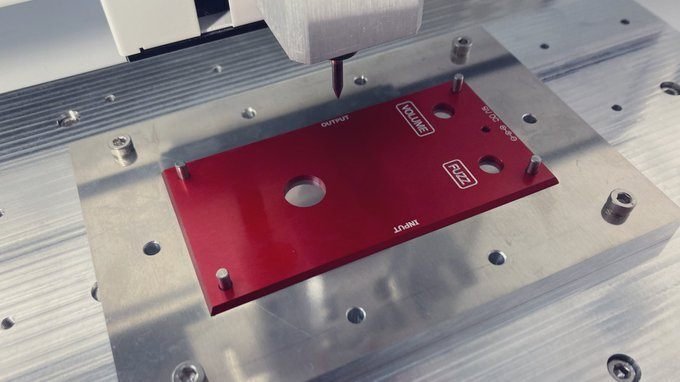
アルマイトが終わったら最後に彫刻です。コントールの文字やデザインを彫り込みます。これ、実は全工程の中でもアルマイトに並んで非常に難易度が高い作業です。まず彫刻は下のような先の尖った三角形の彫刻用エンドミルを用います(下記画像)。
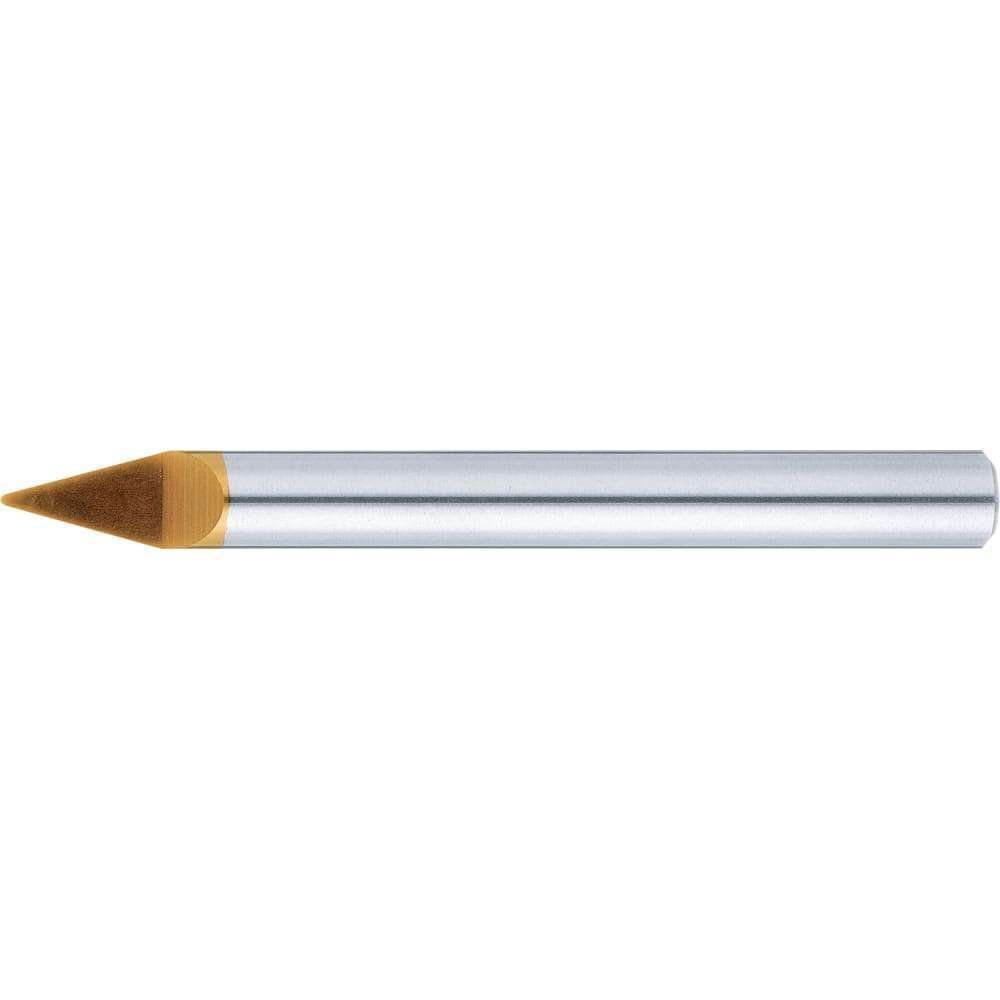
通常はこれでいいのですが、今回の切削は非常に小さい文字を切削します。削る線の幅は細いところで0.05~0.1mm程度(推定)になるのですが、一般的な彫刻用エンドミルは先端の欠けを防ぐためにR(円形状)を設けています。この直径はたいてい0.1mm程度あるため、今回の場合は太すぎます。ここでは、非常に細い線を彫り込むために、フランスのmagafor社の彫刻用マイクロエンドミル MF8540(先端径Φ0.05、角度40度)を選定しました。
しかし、エンドミルだけでは加工の精度は出せません。エンドミルの先端半径が0.05mmでも先端形状は三角形なので、深く切り込んでしまうと線の幅が太くなります。つまり、高さ方向の精度も10μm(0.01mm)程度のオーダーで出す必要があります。エンドミル先端のZ軸原点(高さ方向)を目と手で調整するのはなかなかに難しく、さらにフェイスプレートは薄いので材料のたわみや浮きも発生するため加工難易度は跳ね上がります。Z軸原点については、後ほど救世主が登場しますが、この時点では、少し上から削り初めて、加工深さを10μm刻みで増やしていくことでなんとか削り出せましたが、品質は安定しませんでした。
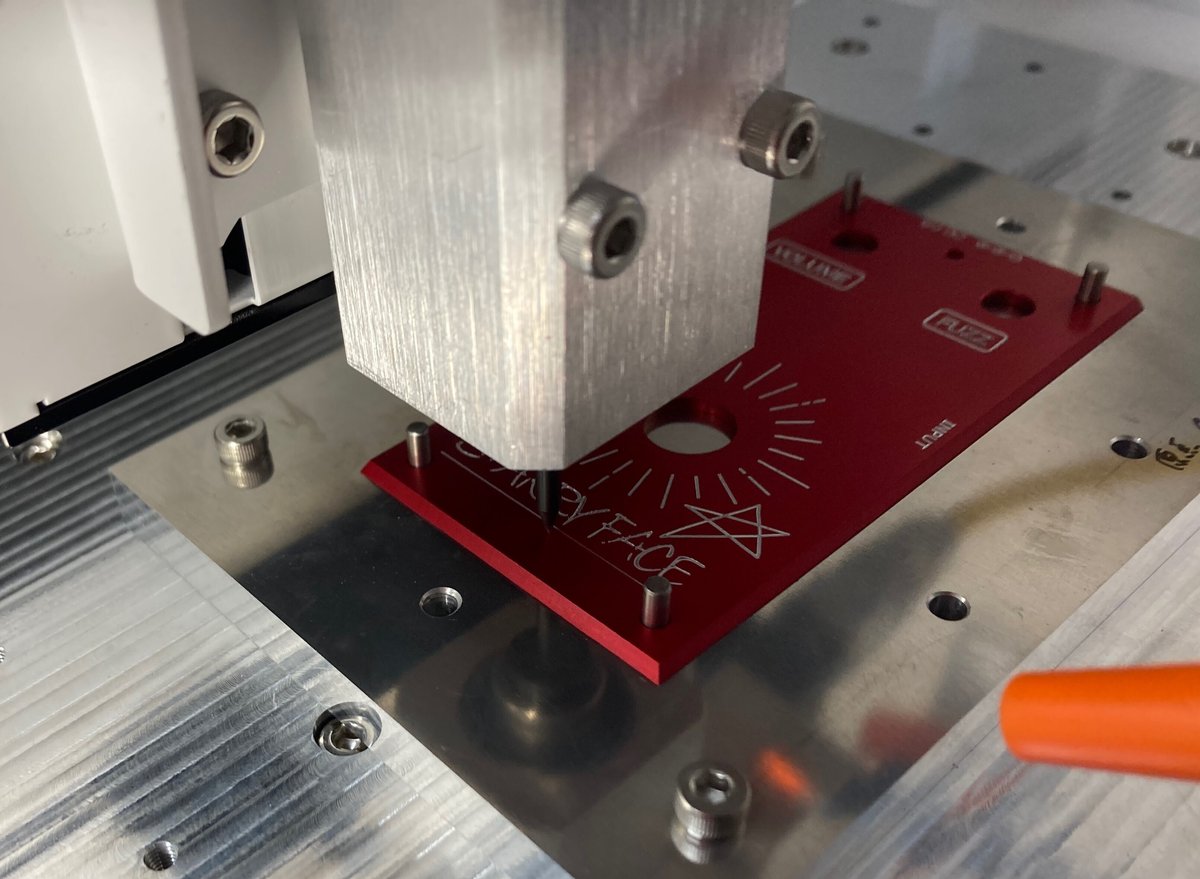
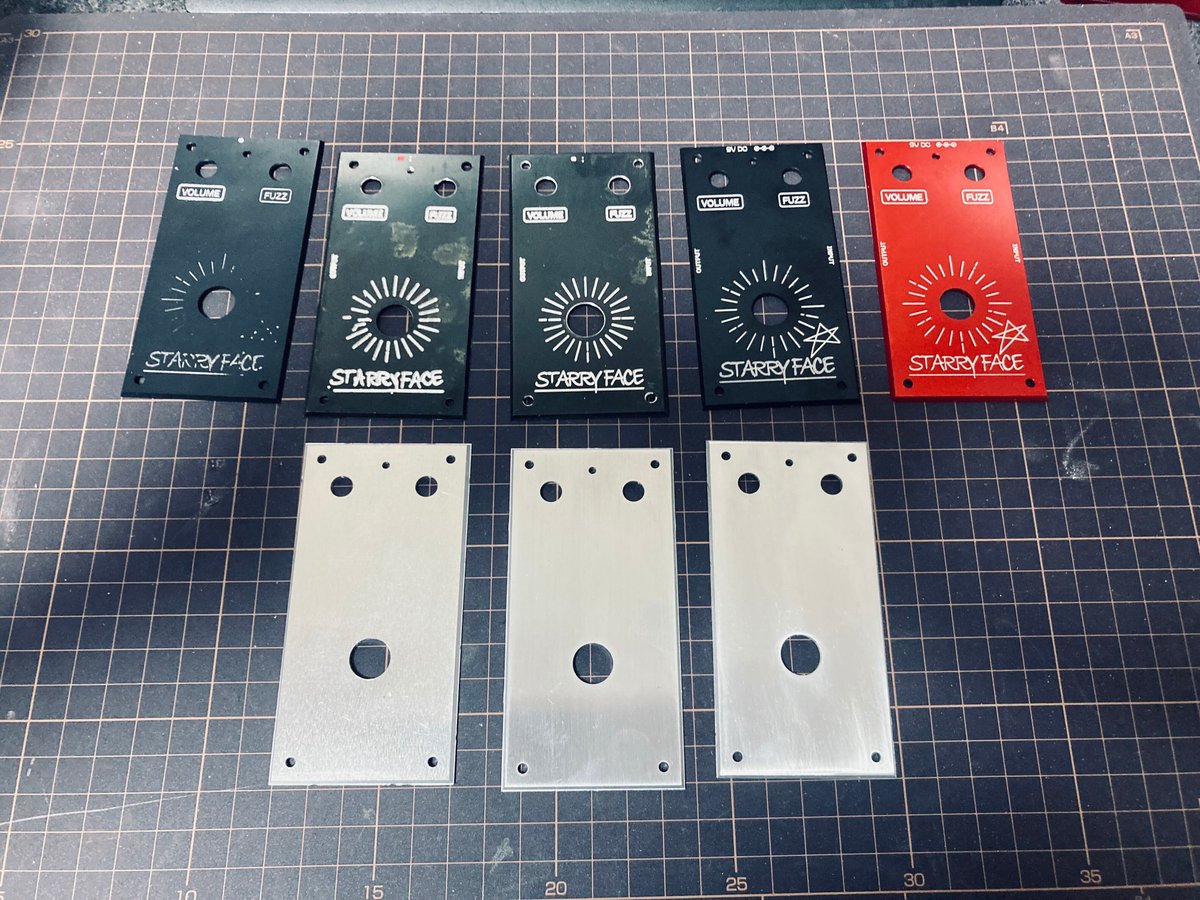
とりあえず、雰囲気を確かめるためにアルミケースにフェイスプレートを組み付けて雰囲気を確認しました。悪くなさそうです。
フェイスプレート(失敗作)を仮組 pic.twitter.com/vJkFGcO9av
— じりおん@ISF10 G-34 (@zillione) April 6, 2023
ここでデザインについてですが、「Starry Face」というのはジュリアの「星」とFuzz Face(キットの内容がFuzz Faceというエフェクタのクローン)を組み合わせた造語です。ペダルスイッチ(エフェクタ中央)の周りには星の光をイメージした光線を彫り込んでいます。四隅は低頭ネジで止めましたが、これはVOXのVALVENERGY COPPERHEAD DRIVEというエフェクタのデザインを参考にしました。余談ですが、このエフェクタはKORGが新開発したNutubeという真空管を搭載し、OLEDによる波形表示機能を有した変態素晴らしい機種です。
とりあえず設計から彫刻まで終わり、あとは本番の部品を作成して配線すれば完成だ!と思っていた矢先、Twitterでエゴサしていたらこんなつぶやきを見つけてしまいました。
「エフェクタケースを自作してるのかと思ったけど、ケースと言うかガワだった。」(特定を避けるため発言内容はだいぶ意訳、改変。念のため言っておくと発言自体を悪く言う意図はありません)
ふーーーーん🤔
最近卓上の CNCフライスを導入したので、アルミケースまるごと自作は無理でも、ケースの上面を装飾するプレートくらいなら削り出せるのでは、と。
・・・だれが無理って言いました?
冗談です。でも、たしかにフェイスプレートだけって中途半端ですよね。やっぱケースを全削り出ししたいですよね。・・・作りますか。。
・・・とはいえ、現在運用しているオリジナルマインドのKitMill CL200という機種のスピンドルモータの定格出力は30W。最近のもう少し能力のある卓上のCNCのスピンドルモータが1000W以上の出力を持っていることを踏まえると圧倒的に能力が低いので、エフェクタケースまるごとの切削は色々と工夫の必要があるのは事実です。
クリアランスがギリ pic.twitter.com/K5PPddNNyd
— じりおん@ISF10 G-34 (@zillione) April 30, 2023
ケースはざっくりと箱と蓋の2つのパーツで構成されます。CNCの工程としては、箱パーツ
が、「固定用の穴あけ→ひっくり返して輪郭の荒加工(120x70mmの材料から110x60mmまでざっくり外形を削り出し)→外形の2D 輪郭仕上げ加工→ボールエンドミルで角のフィレットの3D仕上げ加工→ひっくり返してポケット加工用のエンドミル侵入穴用の穴あけ(ヘリカル加工)、内側のポケット加工(荒加工のみ、104x54x17mmの領域を全削り)→蓋固定用のネジ部分の下穴あけ」となります。
1つ目の問題は、CNCの能力不足です。特に深さのある厚い材料の切削は大変です。例えば箱パーツは、厚さが20mmあります。使用しているCNCだと、メーカ推奨値だと一度に削れる量は深さ方向が0.1~0.2mm程度が上限です。径方向の切込み量は、刃径の0.1倍程度(刃径Φ6mmのエンドミルなら0.6mm)になります。削れる量が少ないと加工時間だけでなく、CAMプログラムも行数が膨れ上がってしまい、CNCで扱える上限に引っかかります。
他の問題としてワークの固定方法があります。たとえば外形の削り出しをするためにはワークを固定する必要がありますが、上から下まで削る関係でバイスで掴む場所がないので、固定用の治具も作成しなければなりません。また、ひっくり返して、両面から加工しないといけないので、位置合わせ用のワークストッパも作成する必要があります。バイスでつかもうとすると、小さな卓上機では、20mmの材料は高さ方向の大きさもギリギリです。
・・・不可能な気がしてきた。
なんにせよ、まずは加工条件をなんとか緩和すべく、一度に削れる量を増やす必要があります。完全に非推奨でおすすめはできませんが、今回CNCに限界を超えてもらうためにCNCのモーターコントローラの過負荷制限の閾値を上げて設定しました。過負荷制限というのは、またエンドミルで切削中にトルク不足で刃物が食い込んでしまったり、無理な力がかかったときに軸移動用のステッピングモータやスピンドルモータが焼ききれないように安全に機械を停止するための機構です。通常は少しでも負荷がかかると止まるような値がメーカから推奨されていますが、今回はこれを少し上げて無理をしてもらいました。加工の条件出しは、メーカの推奨条件も参考にしつつ、エンドミルの回転数(CL200は3段階プーリで5600~10000rpm)、送り速度(最大10000rpm)、切削速度(刃径と回転数により決定)、切込み量(軸方向ap,径方向ae等)の条件に加えてCAMのツールパス等も含めて調整(溝加工しない、急激な工具の移動を減らす、ランピング加工の不使用など)していき、最後は切削加工中の音と勘が頼りに探っていきます。何度か試し削りをして、Φ6のアルミ用スクエアエンドミルで一度の切削の切削深さapを0.6mm→4mmまで条件を上げることができました。結果的に加工時間は、内部のポケット加工だけで35時間から5時間まで短縮できました。まだまだ長いですが、極小の卓上機だとこれが限界です。とはいえ、だいぶCNCに無理させているので、加工中はヒヤヒヤものです。
5時間とか出てる・・・削れるのか? pic.twitter.com/Gf01AG7BG7
— じりおん@ISF10 G-34 (@zillione) May 1, 2023
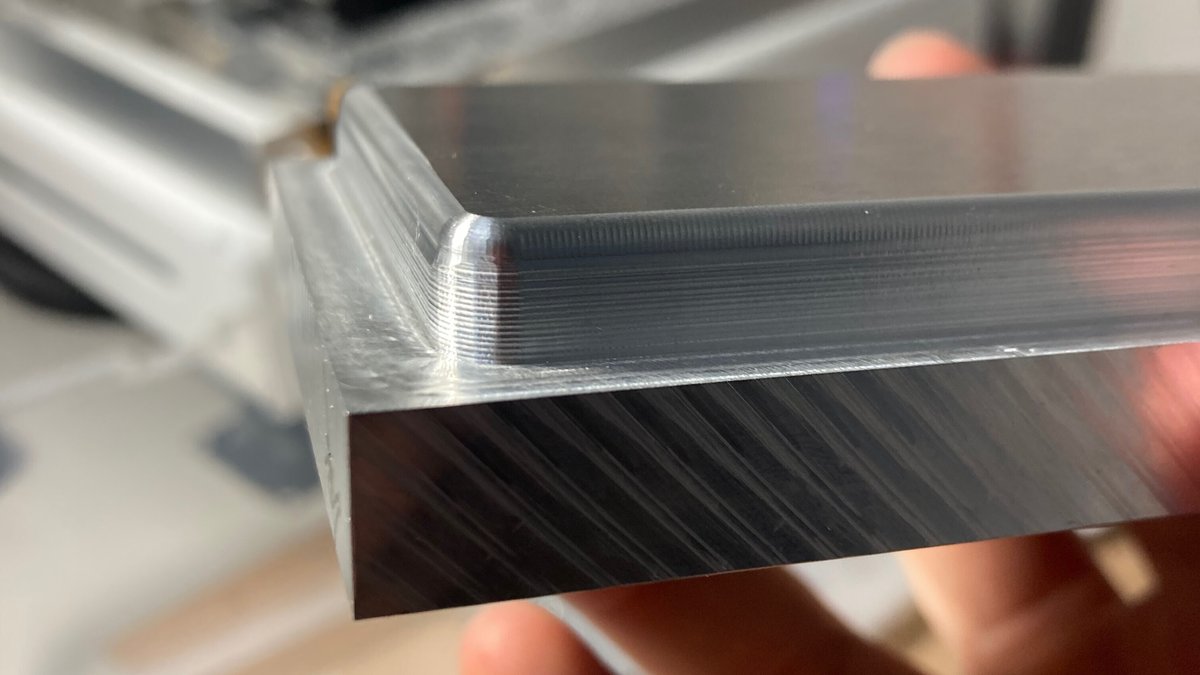
CAMの設定ミスって面が荒れてるけど、削れることは分かった pic.twitter.com/AUoupJPvzT
— じりおん@ISF10 G-34 (@zillione) May 10, 2023
この頃、世間はGWに突入し、ISFの同人誌の原稿に忙殺され始めます(取り掛かりが遅い)。そんな中、ミリシタにジュリアと所恵美のデュエット曲「エスケープ」が追加され、筆者は頭が悪いのでTPRを取りにいってしまいます(原稿と平行して作業して死ぬかと思いました)。
— じりおん@ISF10 G-34 (@zillione) May 10, 2023
閑話休題。原稿を終えたタイミングで後回しにしていたエフェクタケースの上蓋部分を含めて全体の形状設計を完成させました。上蓋のデザインにあるスリット部分は、海外の自作キーボードであるRAMA WORKS®のThermal keyboard (https://ramaworks.store/products/thermal-seq2)のデザインを参考にしています。このデザインを実現するために蓋と箱部分の間に敷板を入れるようにして3つの部品で構成する形に変更しました。
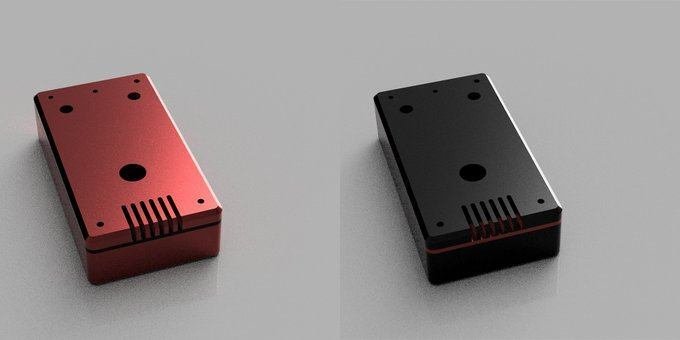
また、加工時間を減らすために極力各部材の厚みを減らして形状を単純化しました(特に中の見えない部分)。また、上蓋は目立つので、綺麗に面取り(角の切り落とし)を行うために、イワタツール社のトグロン®シャープSPを導入しました。1枚刃という微妙に不安を感じる見た目に反して、非力な卓上機でも一発でさくさくとC2(45度の2mm幅)の面取りをしてくれる非常に能力の高いエンドミルです。

まずは上蓋を削り出しアルマイトしました。箱パーツに比べると上蓋は厚さが5mmなので、加工はラクです。治具作成の手間をなくすために、外形を下から厚さ2mmだけ残して削り出し、C面取り、穴・スリット部分の加工を済ませてから、最後に残った2mmの外周を削ります。うまく段取りを工夫することで、工数を減らせました。
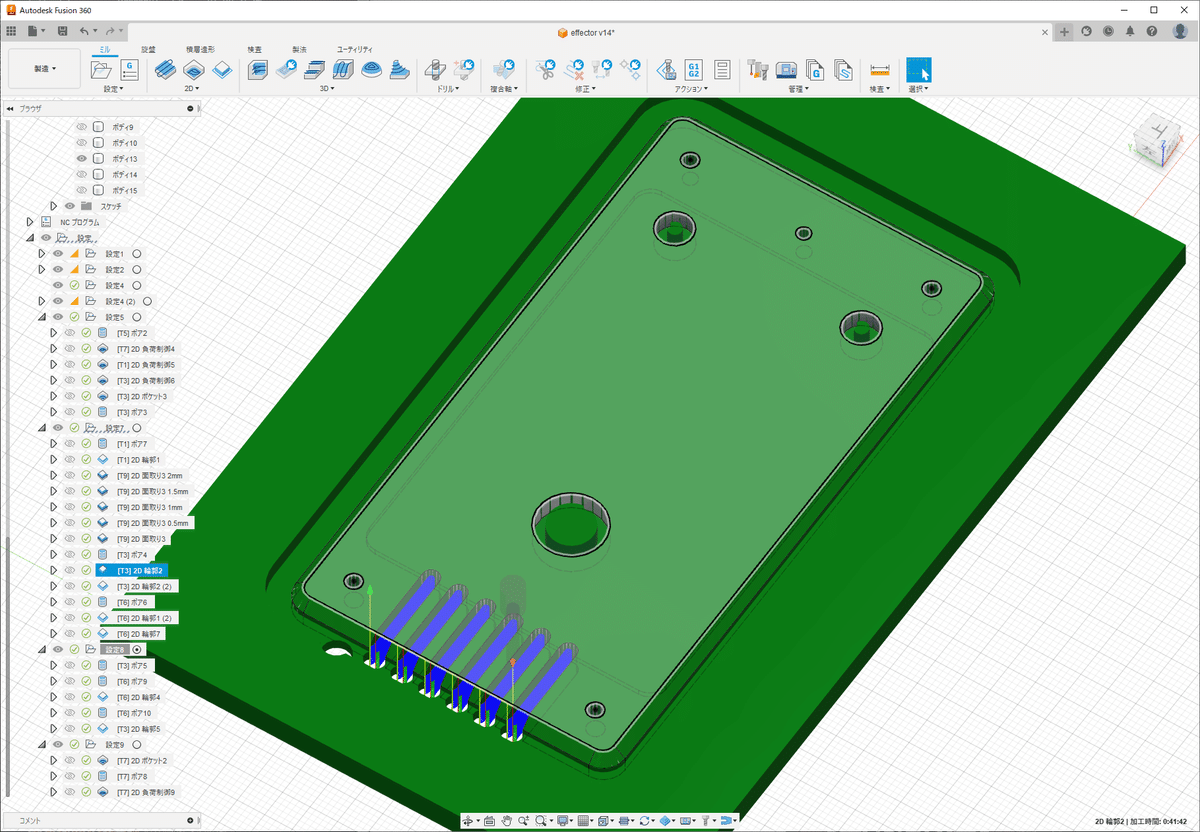
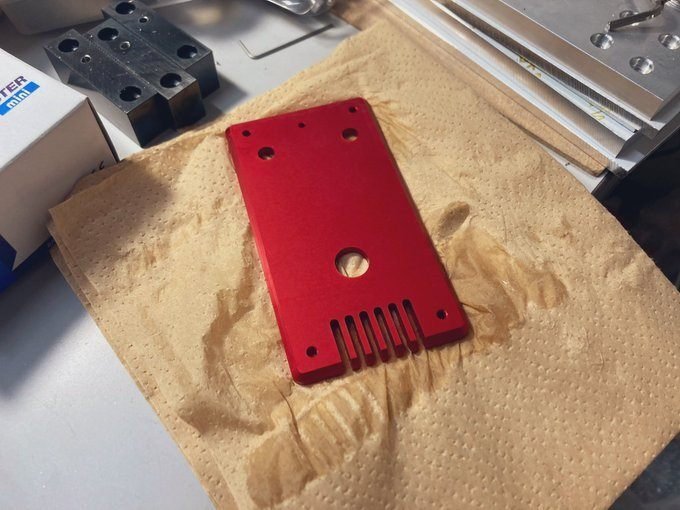
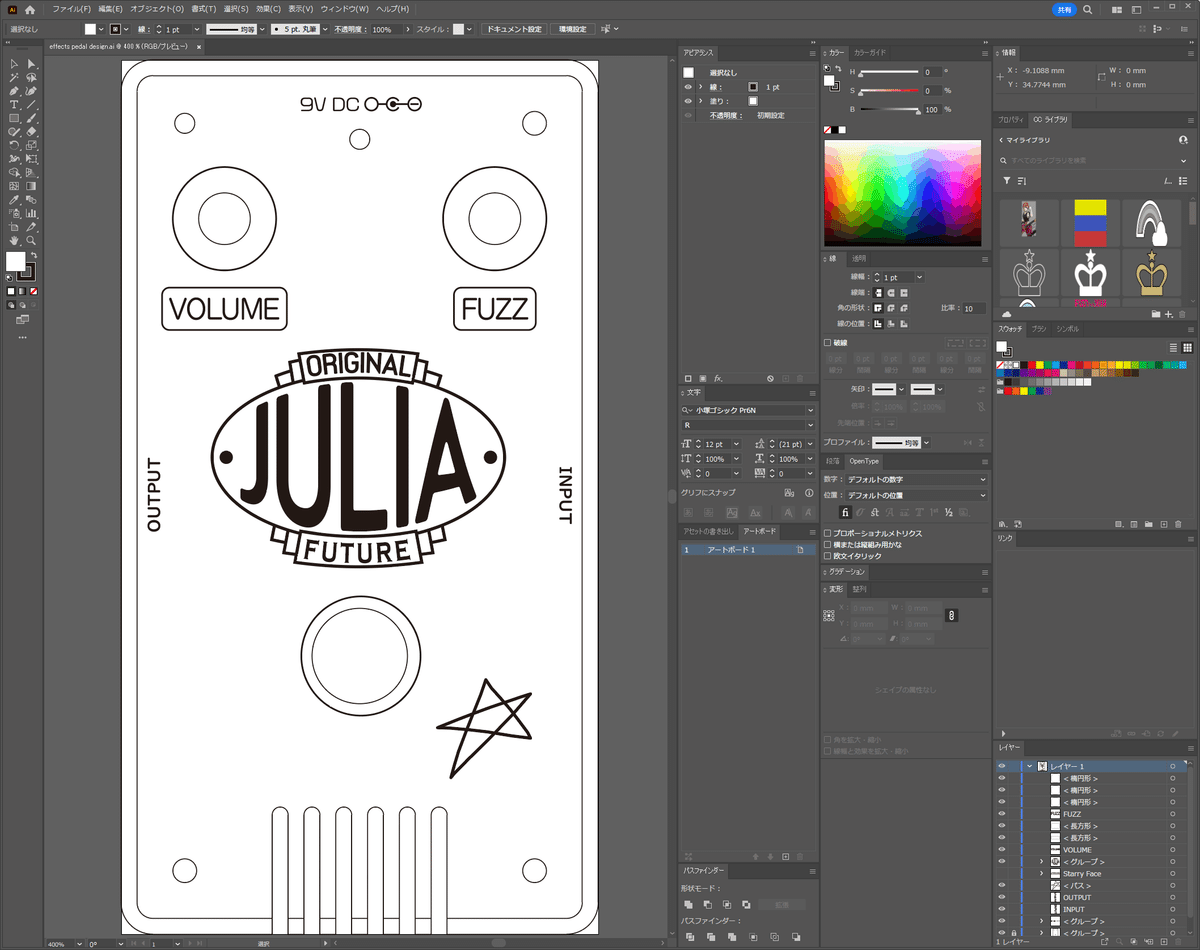
続いては、上蓋と箱パーツの間に挟む板パーツの作成です。このパーツは側面と上蓋のスリット部分から除く差し色的な役割を果たします。ここまでの切削作業に比べれば、板パーツの加工について難しい部分はありません。
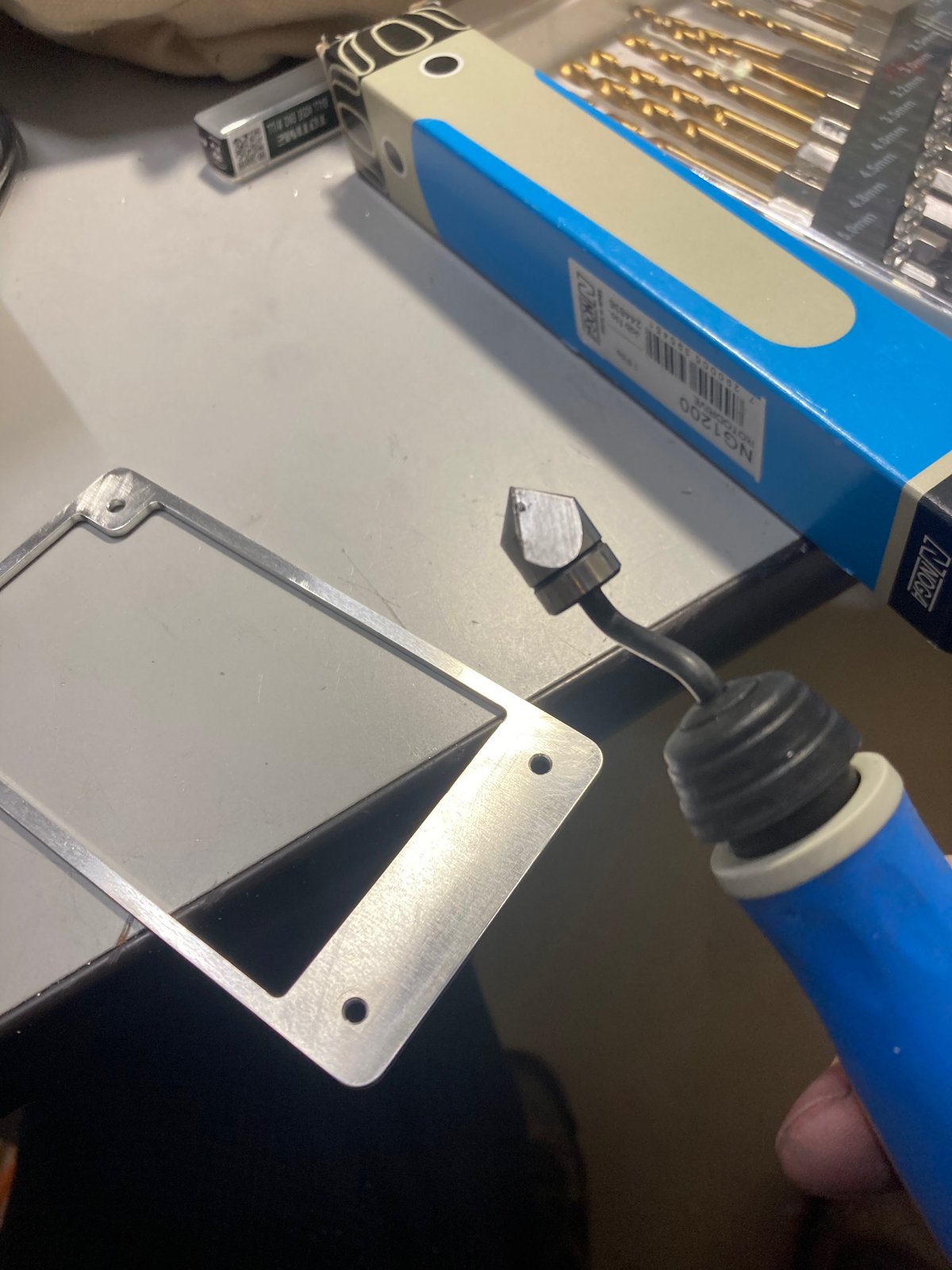
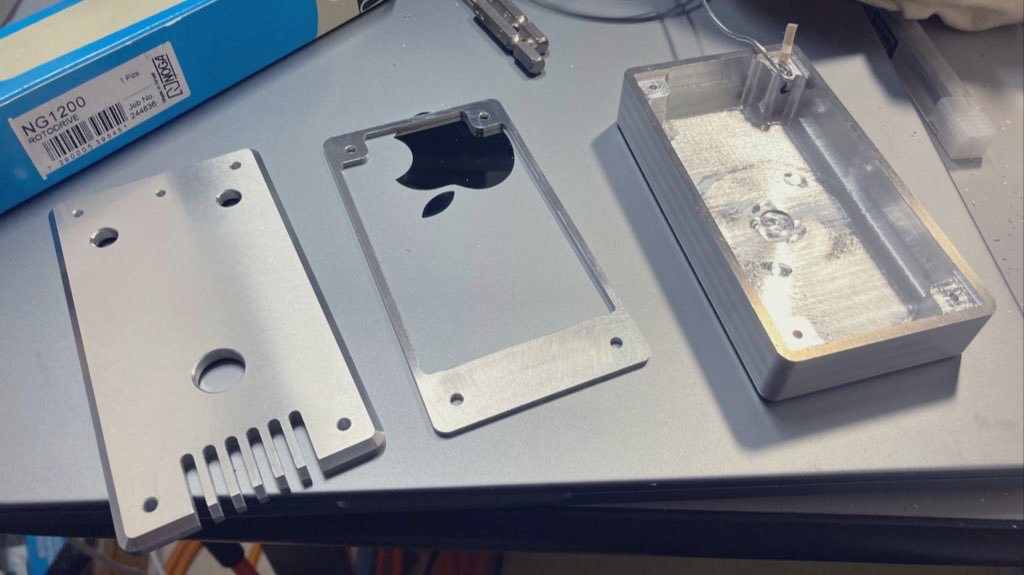
最後はいよいよ刻印です。アルマイトと違うのはやり直しができないことです。フェイスプレートのときは、目と手で工具のZ軸(高さ方向)の原点を合わせていたため、ワークの上面とエンドミルの刃先の位置に0.1mm~0.2mm以下の誤差がありました。高さ原点が0.1mmもずれると細かい字や記号は最悪潰れます。誤差が発生する原因は、マニアックなので詳細は割愛しますが、Z軸の駆動が台形ねじであることによるバックラッシの発生と、手動でステッピングモーターで高さを出す際に、ハンドルで手動調整後にコントローラから制御を開始した際(ステッピングモーターに通電して回転させたとき)に微小なズレが発生することの2点があると予想しています(素人なのでズレてるかもしれないです)。PCからパルスを送ってステッピングモータを操作しZ軸原点を調整する方法もありますが、彫刻用エンドミルは先が細くて欠けやすいので、ワーク上面ちょうどを狙って軸を下げていくのはエンドミル先端がワークに突っ込んでしまうリスクがあり避けたいです。また、ワーク表面の傷も避けたいところです。
ちなみに、太さが気になるのであれば超微細加工用の細いスクエアエンドミルやボールエンドミル等の先端の太さが変わらないエンドミルを使えればよいのですが、先端径が0.05mmのものは自分が探した範囲で見つかりませんでした。また、線の太さが一定でないため、0.05mmより太い線を描きたい場合は、より太いエンドミルを用意するか、オフセットしたパスを彫刻して(要するに何本か線をずらして彫って)いく必要があること、先端が細い棒の形状になるため、折れやすいという問題点もあります。
前置きが長くなりましたが、ここで登場するのが刃先位置測定器です。今回は大昭和精機のBMN-20Hという機種を購入しました。円筒部分の中央にボタンのようなものがついており、ここにエンドミルの刃先が当たるとLEDが光るという仕組みです。動作は単純ですが、計測の繰り返し精度が±1μm(0.001mm)と卓上機にはオーバースペックなほどの超高精度測定器です(お値段もオーバースペックです)。実は半分の高さのBMM-10Hという機種も所有していましたが、ボタン部分のストローク量が小さく、一度操作を間違ってエンドミルを下げすぎてしまった結果壊してしました。BMM-20Hは、ボタン部分のストロークが2mmあるので多少雑に扱っても壊れないという長所があります。ただ、測定可能な最小工具径がΦ0.1mm(これでも十分な低測定圧)なため、先端径Φ0.05mmの彫刻用エンドミルMF8540が測定できるか微妙なところです。これよりさらに低速低圧の機種(測定可能な最小工具径がΦ0.05mm!)もありますが、測定器の高さが倍以上あり断念しました。
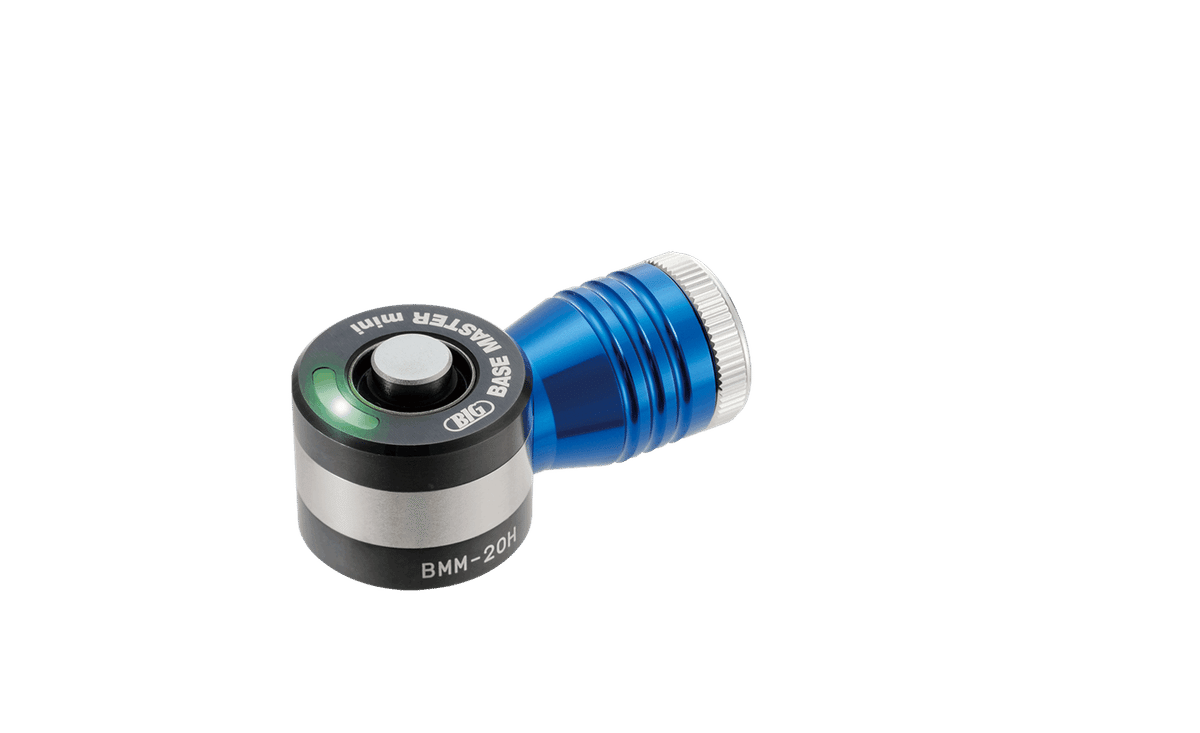
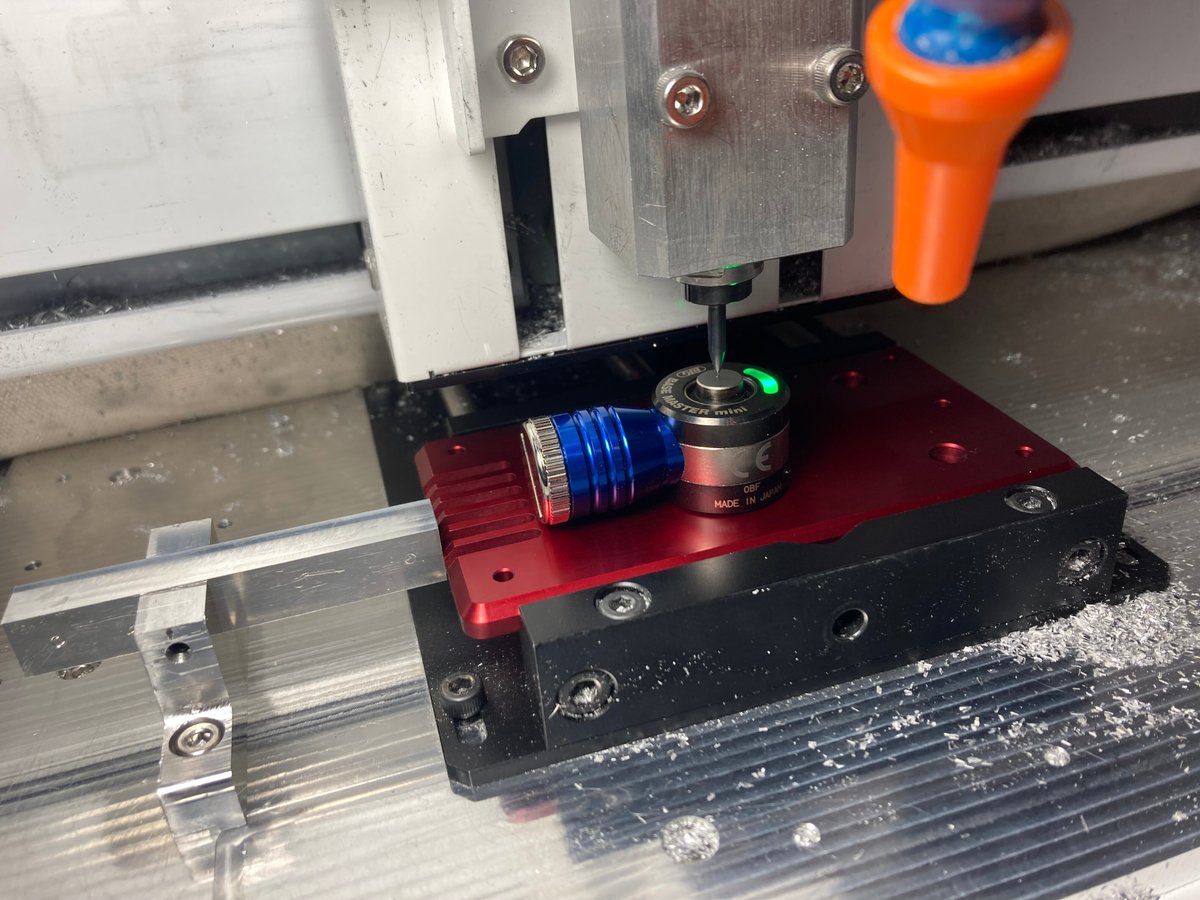
道具は揃ったので早速刻印ですが、まだ問題があります。普通、精度を求めるような材料の場合は、目的の加工をする前に4F(フライス), 6F加工と呼ばれる面だしを行います。この加工を行うことで、単に面を平らにするだけではなく、向かい合う面が平行度、隣り合う面が直角度を出すことができます。逆に6F加工されていない材料は、一見直方体に見えて寸法意外に平面度や直角度等の精度は保証されません。材料屋さんから素材を購入する際に、6F指定すれば出荷時点でフライス加工したものが手に入りますが、加工賃が乗るため価格は上がります。今回は材料代をケチったので、フライス加工されていない材料を使っています。そのため、上面が平らではありません。さらに言うと、アルマイト加工をすることにより厚さが0.01~0.02mm程度厚くなります。また、剥離材につけることで表面材料が1~2μmほど減ります。結果的にアルマイト後のワーク表面は、0.01mmのオーダーで荒れていると考えれます。
以上を踏まえて、実際に同じワークで、刃先のZ軸の高さを変えて彫刻した例が下の画像です。画像中央の曲線(エンブレム部分の一部)を見てください。全然、太さが違いますよね?基準高さでは、線が彫れていない部分もあります。ここで変えた高さは、たったの0.025mm(25μm)です。このような状況のため、結局は、少しずつ刃先位置を変えて様子を見ながら線を描いていく必要があります。では、刃先位置測定器がいらないかというとそんなことはなく、今回、刃先を下ろしていく間隔は0.025mmなので、目標の高さから1mmずれるだけで、40回も刃先を変えて様子を見なくてはいけません。彫る位置や線の太さにより、高さ方向は都度調整の必要があるため、さらに調整回数は増えます。刃先位置測定器のお陰で、これらの刃先高さを調整する回数を減らすことができます。0.025mmという数字は、0.05mmで下ろしてしまうと線が太くなりすぎる場合があるのと、これ以上細かくすると刃先を調整する回数が増えてしまい手動で加工する時間がかかりすぎるところからバランスを見て決めました。より細かく調整すれば、さらにきれいな線を彫ることも(技術的には)可能です。
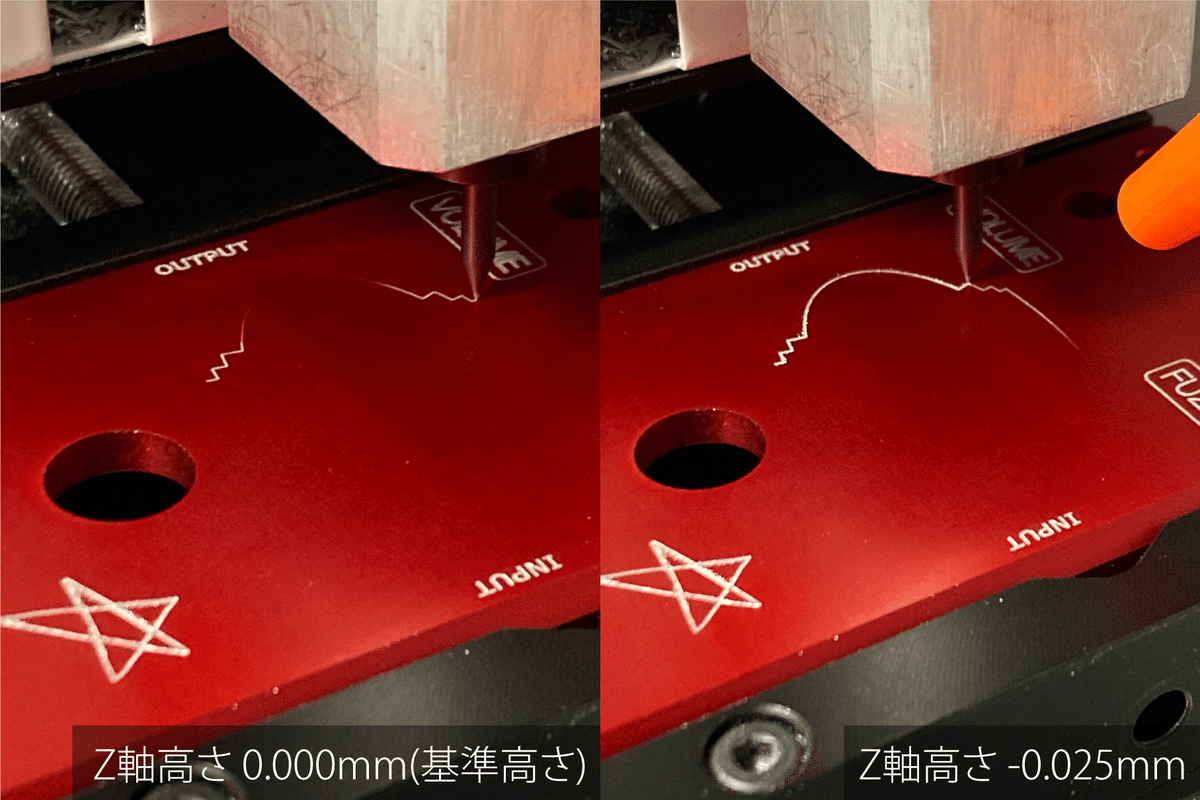
加えて、今回彫刻は、Fusion 360の彫り込みコマンドを使ってCAMを生成します。彫り込みコマンドは、彫刻する溝の深さに応じて自動的に刃先の高さを変更します。これにより例えば「はらい」があるような明朝体の文字であっても、太さを変えて一発で彫刻することができます。これも問題で、あまり深く彫りすぎてしまうと文字が太く、またバリが発生して見栄えが悪くなります。彫り込みコマンドの標準の設定では、最大で-3mm程度までのツールパス(工具の移動経路)を生成してしまうためワーク上面から-0.2mm以上は深く彫らないように制限をかけてツールパスを生成します。
これまで説明したように彫刻加工はなかなかに難しいので、本番の加工の前に、感覚をつかむために練習用のパーツで刃先位置の調整間隔等を探っていきました。材料は勿体ないですが、目的の精度を出すためにはこれも必要な作業です。
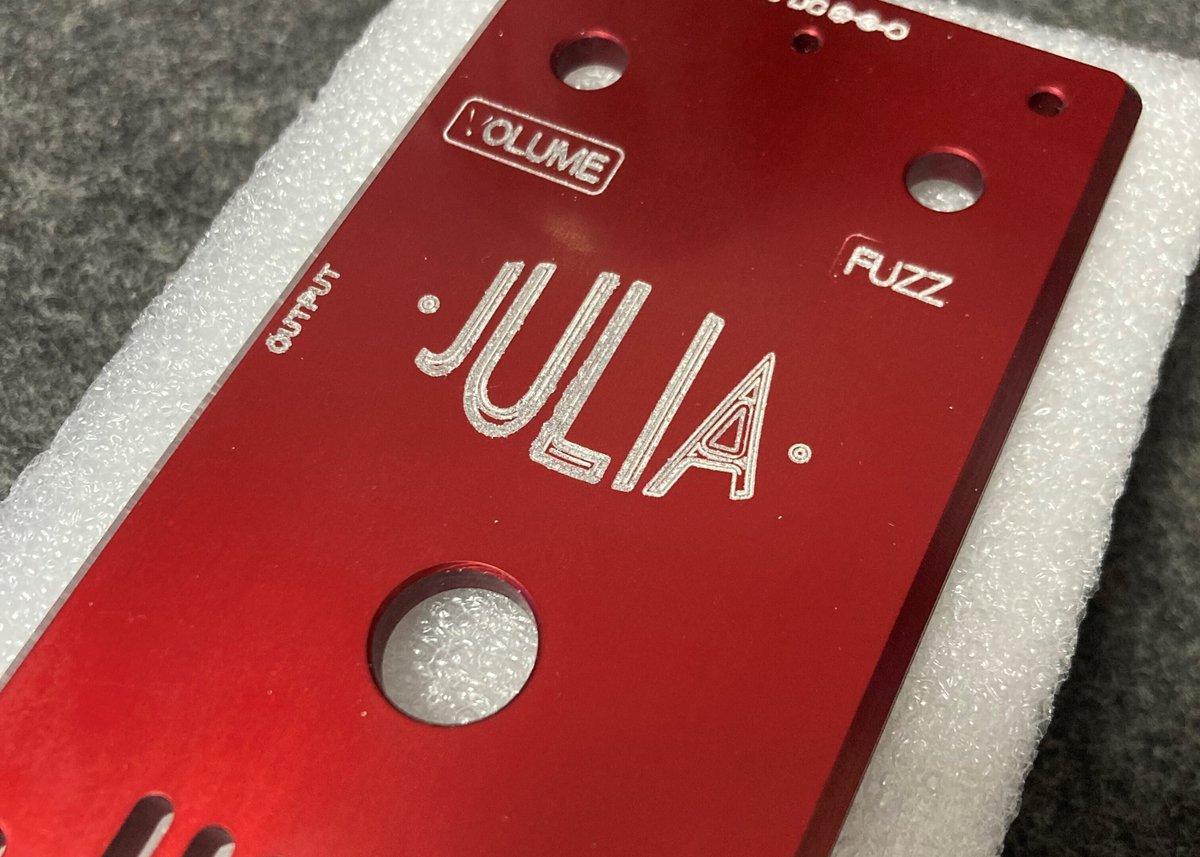
4時間くらいCNCに張り付いて切削を行い、ようやく上蓋の彫刻加工がおわりました。あとは、CNCで加工しなかったケース側面のジャック用の穴を開けて長かったケースの加工は一旦終了です。部品の組付けを行ってみて干渉等がないかチェックします(もっと前段階でやっておくべきでは)。今回一応、上蓋とケース本体を黒でアルマイトしたバージョンも作りましたが、彫刻加工は断念しました。また、暇なときにやっておきます。
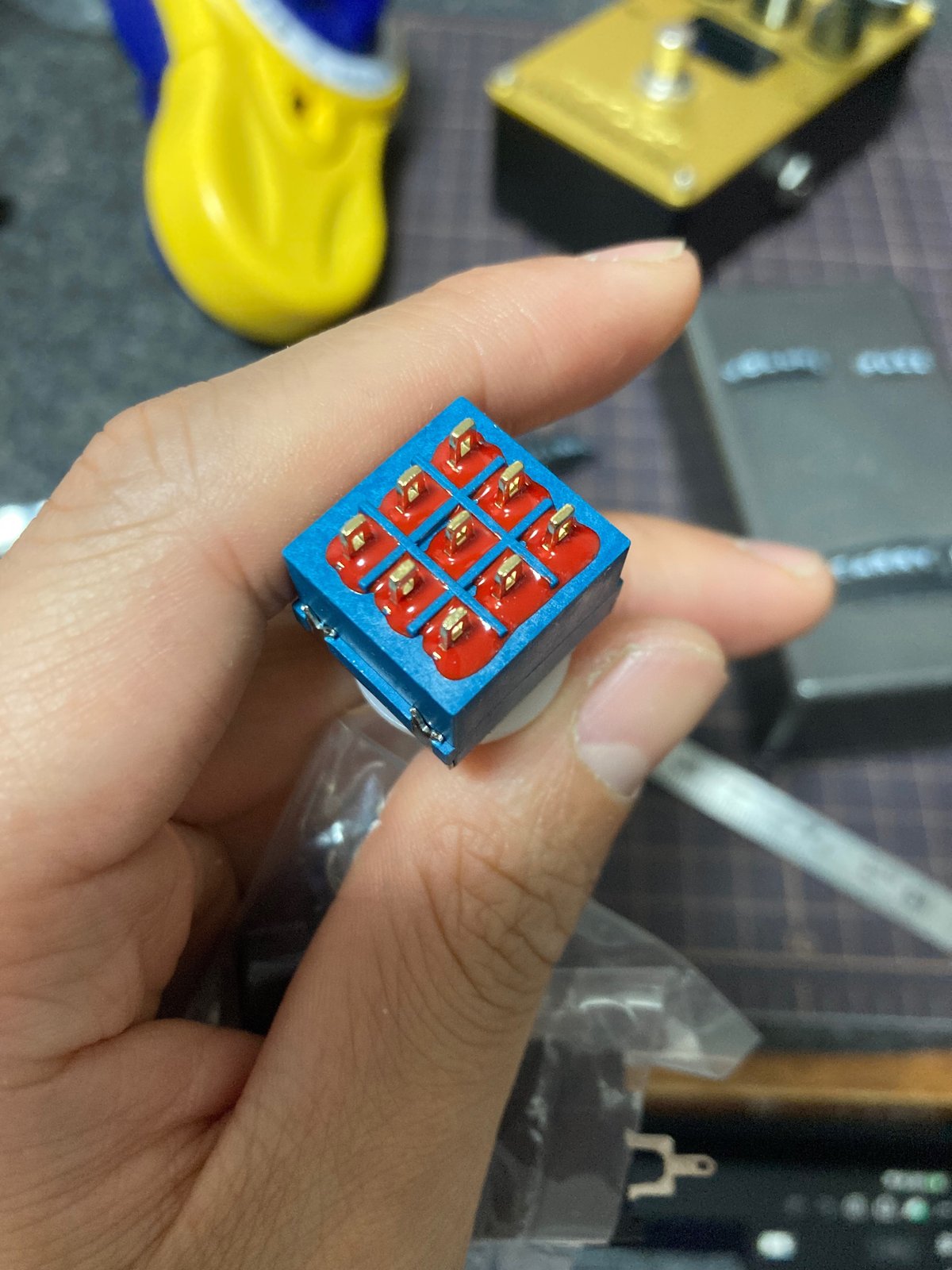
こんなもんでどうだ…? pic.twitter.com/NI2e9bS0Dj
— じりおん@ISF10 G-34 (@zillione) May 25, 2023
部品も配置できたので、残りのパーツを含めてすべて結線・はんだ付けしていきます。実際に、電源に繋いでアンプから音が出ることも確認できました。ファズのキットを購入しましたが、鳴らしてみた音は微妙な感じです。目的はケースを作ることだったので、音のこだわりはあまりなかったのですが、これはあとでパーツを変えるかもしれないです。とはいえ一応動くものができたので一旦完成とします。
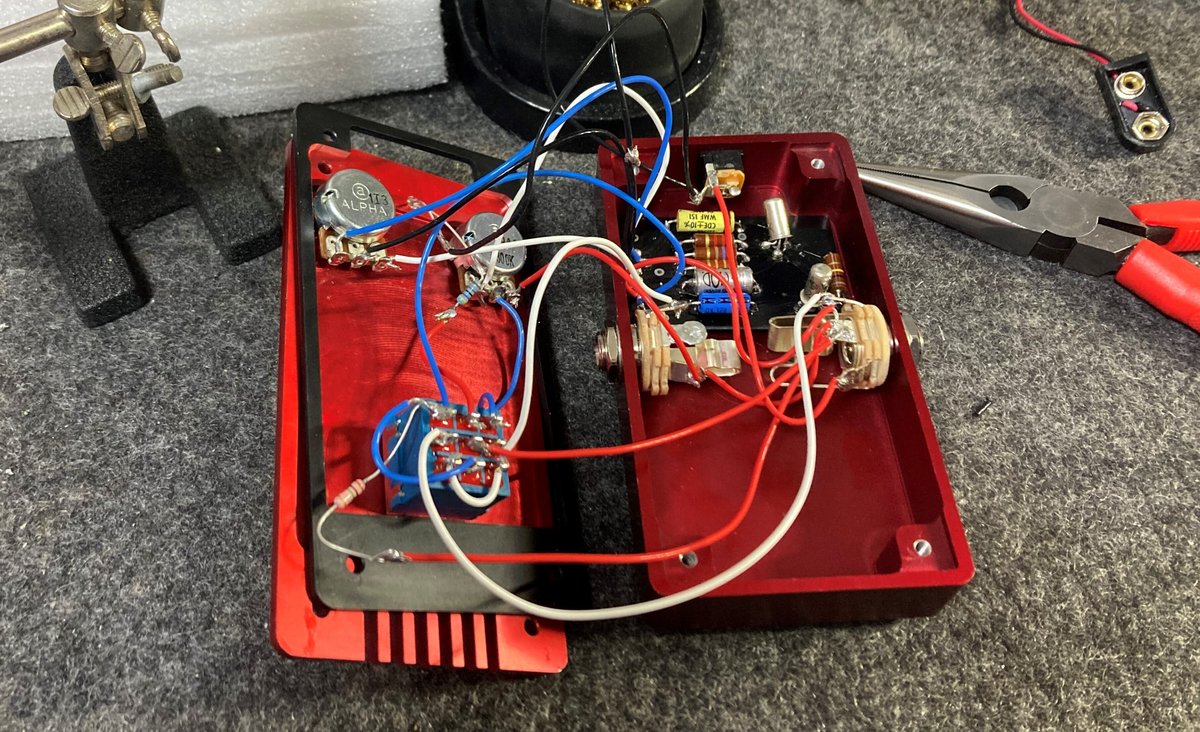
以上が担当のエフェクタを自作したお話でした。CNCもアルマイトも初でしたが、今回の作業でだいぶ経験値がたまりました。音は要調整といったところですが、だいぶ仕組みもわかったのでこれからパーツ探しの旅に出ると思います(本当?)。最初は、スリット部の見え方を重視して、黒を主体としたカラーリングで行こうと思っていました。Twitterにどっちの色がいいかと聞いてみたら100:0で赤が選ばれたので、この色にしましたが、結果的にうまく行ったように思います。
ここで宣伝になりますが、今回作成したエフェクタを、5/28(日)に横浜産貿ホール マリネリアで開催されるアイドルマスターミリオンライブ オンリーイベントのISF10でこのエフェクタを持っていきます。売ってほしいという声もいくつか見かけましたが、完全にワンオフのため今回は展示だけになります。すみません。
新刊やグッズのシールを頒布しますので、是非お立ち寄りください。
#ISF10 のお品書きです。新刊とジュリアのホロシールを頒布します!
— じりおん@ISF10 G-34 (@zillione) May 23, 2023
新刊はジュリアだらけのRock Kitシリーズの第4弾です。今回は短編マンガにオリPが出ます。
グッズのホロシールは20%くらいの割合でバージョン違いを封入予定です。当たったら友達に自慢しよう!
よろしくお願いします! pic.twitter.com/AIeHM09Hqy
最後に作成したエフェクタをジュリアが愛用するギブソンのレスポール スペシャルと並べて"""ノルマ達成"""です。
ここまで長文を読んで頂きありがとうございました。
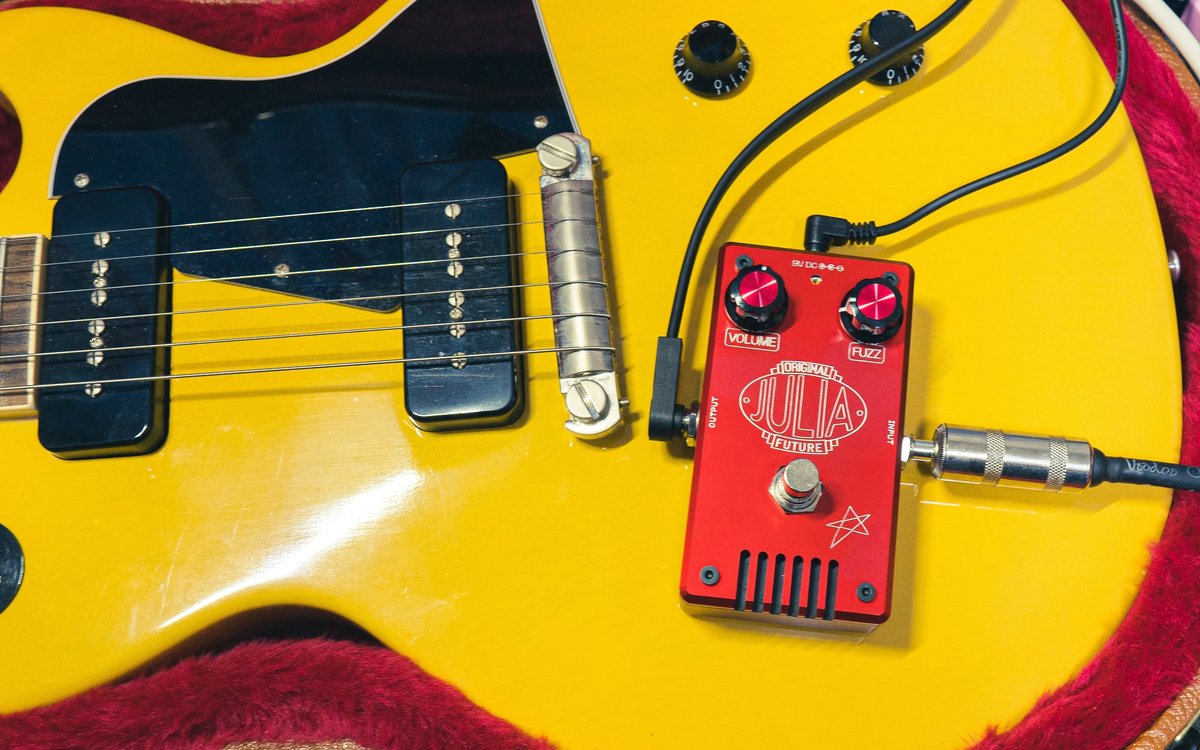
この記事が気に入ったらサポートをしてみませんか?