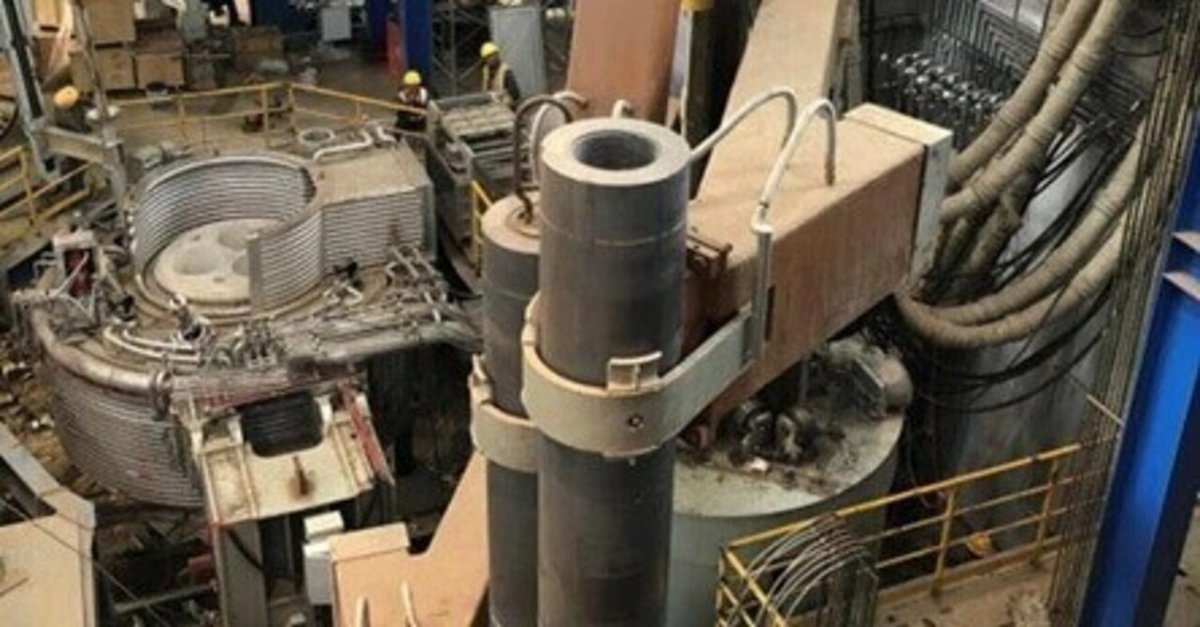
Secondary Refining Furnace
The steel refining process by secondary refining furnace can be divided into two categories: primary refining, aimed at removing carbon from pig iron, and additional refining processes conducted after primary refining, collectively referred to as secondary refining. Secondary refining furnace process involves the removal of impurities and adjustment of elements. The secondary refining usually takes place in a ladle (a transport container for molten steel) and is crucial for producing high-quality steel. The primary role of secondary refining is ultimate desulfurization, the elimination of oxygen, nitrogen, hydrogen, and other impurities, as well as the final decarburization of ultra-low carbon steel.
A steel melting and secondary refining method comprising the steps of melting steel manufacture raw materials while the molten steel is subjected to oxidation and decarburization so that the oxidation and decarburization are substantially completed before melt-down; after melt-down, heating the molten steel to a temperature above a liquidus line temperature and below 50℃. in temperature increment from the liquidus line temperature, and thereafter tapping the molten steel into a primary ladle; teeming the molten steel from the primary ladle into a secondary refining furnace; allowing the molten steel to be effluent into a secondary ladle at a lower portion of the secondary refining furnace while the temperature of the molten steel is raised; and continuously performing gas bubbling in the secondary ladle in a vacuum under existence of slag simultaneously with the effluence of the molten steel into the secondary ladle.
TYPES OF SECONDARY REFINING FURNACE
In the realm of steel production, the Secondary Refining Furnace stands as a pivotal player in achieving exceptional steel purity and quality. This crucial phase of the secondary metallurgy steelmaking process encompasses various techniques aimed at fine-tuning the composition of the molten metal, eliminating impurities, and ensuring the final product meets the stringent demands of modern industries.
ESR Electroslag Remelting Furnace
CHNZBTECH's ESR Electroslag Remelting Furnace is a cornerstone of the secondary refining process, refining metals with unparalleled precision. Utilizing advanced cupellation furnace technology, it ensures superior quality and purity in specialty alloys and superalloys. With precise control over composition and impurity levels, CHNZBTECH's ESR furnaces meet the highest industry standards, making them essential for producing materials in demanding applications.
VOD Vacuum Oxygen Decarburization
CHNZBTECH's VOD Vacuum Oxygen Decarburization Furnace is a cornerstone of the secondary refining process, ensuring high-quality steel production. Employing advanced lead refining furnace technology, it effectively removes impurities and reduces carbon content in molten metal, enhancing its mechanical properties. With precise control over oxygen levels and temperature, CHNZBTECH's VOD furnaces deliver superior metallurgical results, meeting the stringent demands of modern steelmaking.
AOD Argon Oxygen Decarburization
CHNZBTECH's AOD Argon Oxygen Decarburization Furnace plays a vital role in secondary metallurgy steelmaking. As a key component of the secondary refining process, this refining furnace effectively removes impurities and lowers carbon content in molten metal using argon and oxygen. With precise control over parameters, CHNZBTECH's AOD furnaces ensure the production of high-quality steel with improved mechanical properties, meeting the rigorous standards of modern steelmaking.
WHAT ARE THE FUNCTIONS OF VARIOUS SECONDARY REFINING FURNACES?
Advantages of ladle refining furnace in alloy steel secondary refining
Enhancing Steel Quality through ESR Process
Stainless steel refining: AOD and VOD furnace
LRF furnace offers strong heating functions, permits the addition of a large amount of alloys, and enables precise temperature control. The ladle secondary refining furnace also provides outstanding desulfurization by high-temperature treatment with reducing fluxes and the removal of deoxidation products. The ladle refining furnace process is therefore often used for the secondary refining process of alloy steel.
THE PIVOTAL ROLE OF SECONDARY REFINING FURNACES-SHAPING MODERN STEEL EXCELLENCE
Secondary refining aims to fine-tune the steel's properties, ensuring the secondary refining process meets the stringent requirements of various industries, including automotive, construction, aerospace, and more.
Purity Enhancement: Steel produced in primary furnaces can still contain impurities and non-metallic inclusions that might adversely affect its mechanical properties, formability, and overall quality. Secondary refining furnaces, such as ladle furnaces or vacuum degassing units, focus on reducing these impurities to enhance the steel's purity. Through secondary refining processes like desulfurization and deoxidation, excess sulfur and oxygen are removed, leading to cleaner and more refined steel.
Composition Adjustment: Steel's composition can significantly impact its performance in various applications. Secondary refining furnaces provide a controlled environment for adjusting the composition of steel by adding precise amounts of alloying elements. This secondary metallurgy steelmaking process allows steelmakers to achieve specific mechanical properties, corrosion resistance, and other characteristics required for specific applications.
Refining Quality: The secondary refining process involves precise temperature and chemical control, which aids in the removal of undesirable elements and compounds that could compromise the steel's quality. By utilizing techniques like argon or vacuum degassing, hydrogen removal, and slag foaming, steelmakers can achieve higher levels of cleanliness and homogeneity in the final product. This contributes to improved mechanical properties, surface finish, and overall quality.
FAQS ABOUT SECONDARY REFINING FURNACE
HOW DOES A SECONDARY REFINING FURNACE ENHANCE THE PURITY OF STEEL?
Secondary refining furnaces employ various processes to enhance the purity of steel. Through the flow of molten steel, these types of steel making furnaces can remove excess sulfur, oxygen, and other impurities using techniques such as blowing, injection, or vacuum treatment. This treatment significantly reduces the content of non-metallic inclusions and impurities, resulting in cleaner and higher purity steel.
HOW DO SECONDARY REFINING FURNACES CONTRIBUTE TO ENVIRONMENTAL SUSTAINABILITY?
CHNZBTECH, one of the leading steel furnace manufacturers in China, is committed to environment protection and sustainability. Modern secondary refining furnaces also take environmental factors into consideration. They utilize technologies such as slag recycling and waste heat utilization to reduce waste generation, energy consumption, and emissions. These measures contribute to achieving sustainable steel production and reducing the environmental impact.
HOW DO SECONDARY REFINING FURNACES ADJUST THE COMPOSITION OF STEEL TO MEET SPECIFIC REQUIREMENTS?
Secondary refining furnaces adjust the composition of steel by adding alloying elements to meet specific requirements. Steel producers can precisely control the amount of alloying elements added, thus achieving specific properties and characteristics in the steel, such as corrosion resistance, thermal conductivity, hardness, etc. This enables steel to be tailored for various application domains.
If you want to know more types of steel furnace for sale, please visit our website.
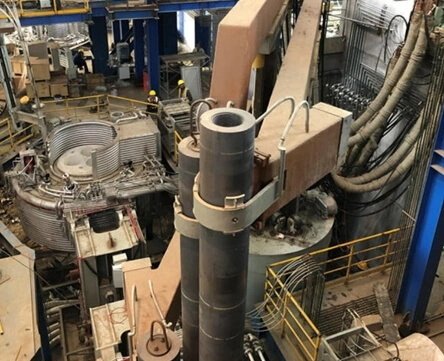
この記事が気に入ったらサポートをしてみませんか?