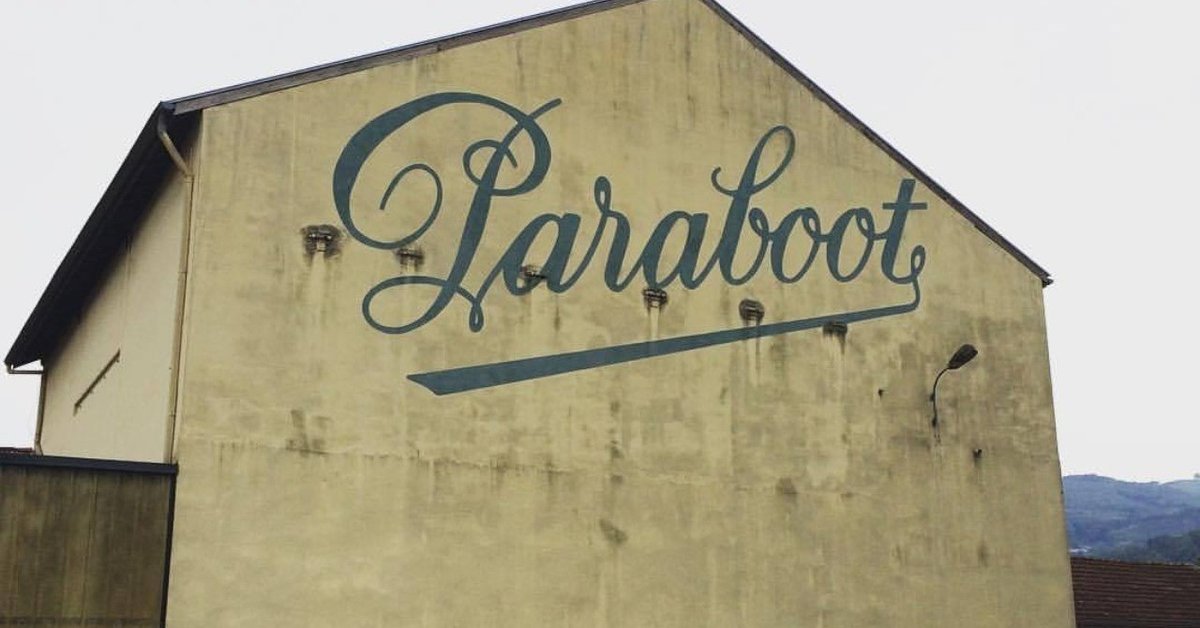
Paraboot Factory / Les chaussures Paraboot, une réussite "made in France"
Paraboot, 111 years of Made in France know-how
Paraboot marks their return to the spotlight to celebrate 111 years of existence. This independent and family business, which defends its Made in France know-how, put aside money in 2017 to expand with a new 11,000 square metre factory in Saint-Jean-de-Moirans, Isere, the ancestral birthplace of the label, whilst continuing to rely on its speciality, hand sewn rubber soles. With today’s more urban style and top quality materials with the majority of the leather coming from French tanneries. Paraboot sells over 120,000 pairs annually and has over 800 points of sale worldwide. It takes no less than 150 operations to make a pair of Michael or Morzine, emblematic models that are characterised by the Norwegian stitch.Models that are becoming more popular again, with the rise of the power of unisex fashion and the desire of a high quality historical product. With interview from Pierre Colin:The name ‘Paraboot’ comes from the combination of the words ‘para’, which is a port in Brazil where the hevea period comes from and therefore the raw rubber material, and also the word ‘boot’. Americans called ‘boots’ their ‘rubber overshoes’ to protect their shoes which, at the time, had a leather, or even rubber, sole. And when Rémy Richard, the founder of the firm saw that, he said why not directly make a shoe with a leather top and a rubber sole.We are right next to the mountains and there is demand from the country folk, farmers and mountain people to have shoes with crampons to help them walk on rocks. So, he started to work on the crampons on the sole and that’s what started the style of the Paraboot that we all know now and is still used.Once we received our skin, we had to cut it to make our shoes and all the pieces of the shoe are cut from the same skin.The famous Norwegian stitching was the origin of Paraboot. The big seam is so recognisable with Paraboot. It has to attach the bottom of the shoe to the welt, and then we can attach the sole at that point. So there you have a production form that gives a complete guarantee of waterproofness. The day that we have to resole the shoe, for example, we just have to unstitch the second seam, take off the sole, put on another one and sew it back on. Without touching the body of the shoe.As I always say, when you have a car, you change the tyres, you don’t change the whole car, and it’s the same thing for a sewn Paraboot shoe.For the 111 year anniversary, we did a lot. We chose four symbolic models for the brand in a capsule collection with 111 copies and that allowed us to celebrate 111 years in quite a special way. When we talk about Paraboot in general, we’re talking about a puncture-proof shoe, these are the elements that we have tried to maintain for our customers.Music free to take : Starlight by Duce Williams (Duce Haus) Artlist
世界中の靴の歴史を研究をしています。ご協力いただければ嬉しいです。よろしくお願いいたします。