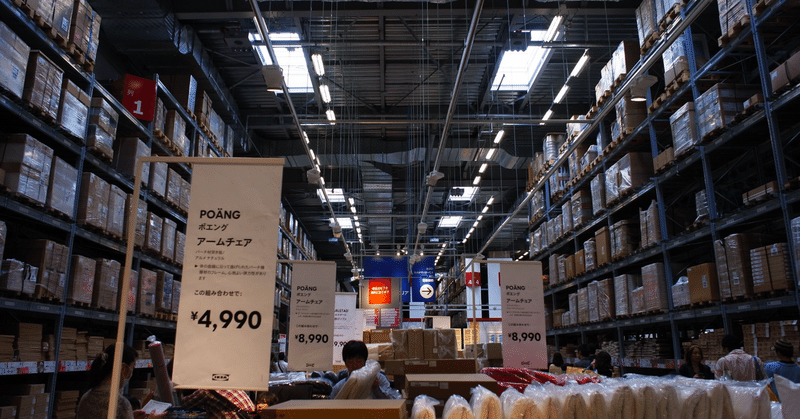
サプライチェーン最適化とデカップリング・ポイント:季節性商品のバッファ在庫戦略
Supply Chain Optimization and Decoupling Points: Buffer Stock Strategy for Seasonal Products
2023年9月15日追記:
【はじめに】
本記事は、以前に投稿したglobal weekly supply chain planの記事の続きです。
今回は、ご紹介してきたglobal weekly supply chain plannerの機能を拡張して、サプライチェーンの需要計画(PULL)と供給計画(PUSH)を生成した後に、デカップリング・ポイントにおけるバッファ在庫の推移を可視化する機能を追加しました。
試作レベルのサプライチェーン・シミュレーション・ツールですが、徐々にサプライチェーン全体を俯瞰する仕組みに近づいてきました。今回の成果物となるバッファ在庫の推移グラフ(「参考図. バッファ在庫の推移グラフ」を参照)は、サプライチェーン上にデカップリングポイントを配置する問題を検討する際に役に立つと思います。
なお、pythonのソースコードは、以下のgithub URLに公開しています。少しきれいにしてから、以前の記事と同様にgithubに公開したいと思います。
Yasushi-Osugi/PySI_E2E_decoupling: decoupling point and its buffer inventory analysis with global weekly supply chain planning and simulation (github.com)
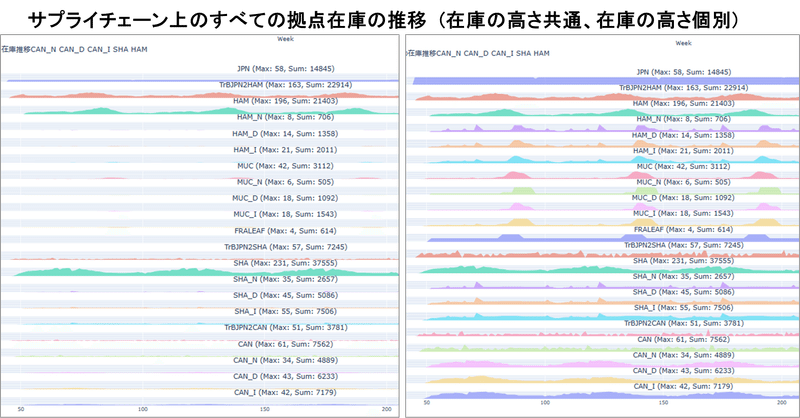
需要変動を吸収するバッファ在庫について検討する観点から、今回は、季節性の強い商品、例えば、アパレルの秋冬物の需要、あるいは夏シーズンに入る頃のエアコン空調機器の需要、クリスマス需要など、需要のピークが2~3週間に集中的に高まる需要特性を持つ商品を対象としたサプライチェーンについて考えてみたいと思います。
季節性の強い商品の需要特性は、需要ピーク期の数週間に年間需要の大半を占めており、市場からの要求需要量と生産制約による供給可能量との間に大きな乖離が発生しています。
以下では、デカップリング機能を持つglobal weekly supply chain plannerからの出力結果を見ながら、季節性の強い商品のサプライチェーン計画におけるデカップリング・ポイントの設定と評価についてご紹介します。
季節性の強い商品において、需給ギャップが発生する様子は、「図1-1. グローバル生産拠点にデカップリング・ポイントを置いた場合」を見ると分かりやすいと思います。
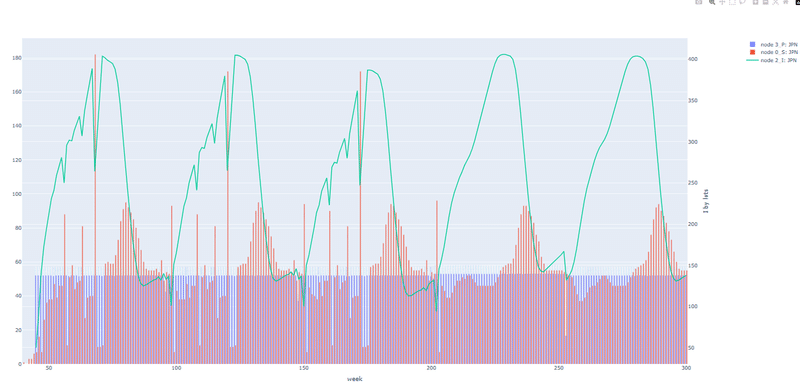
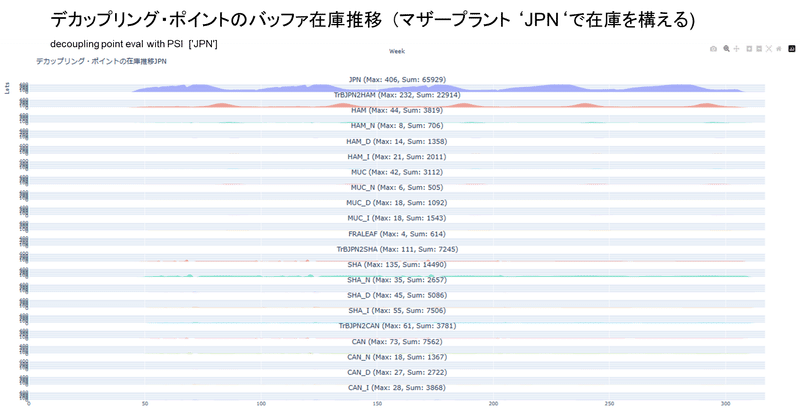
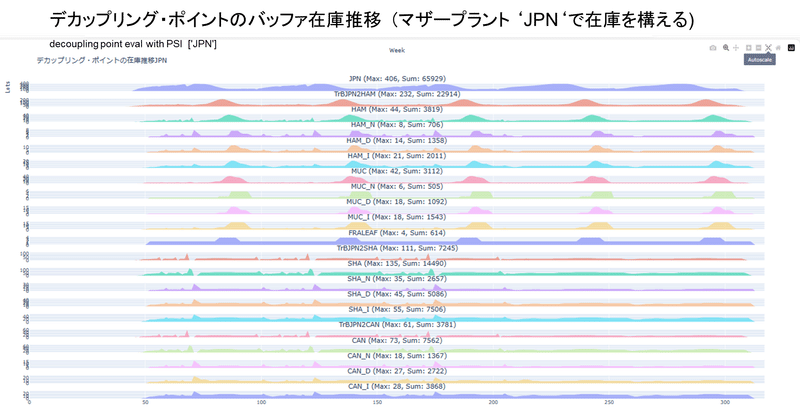
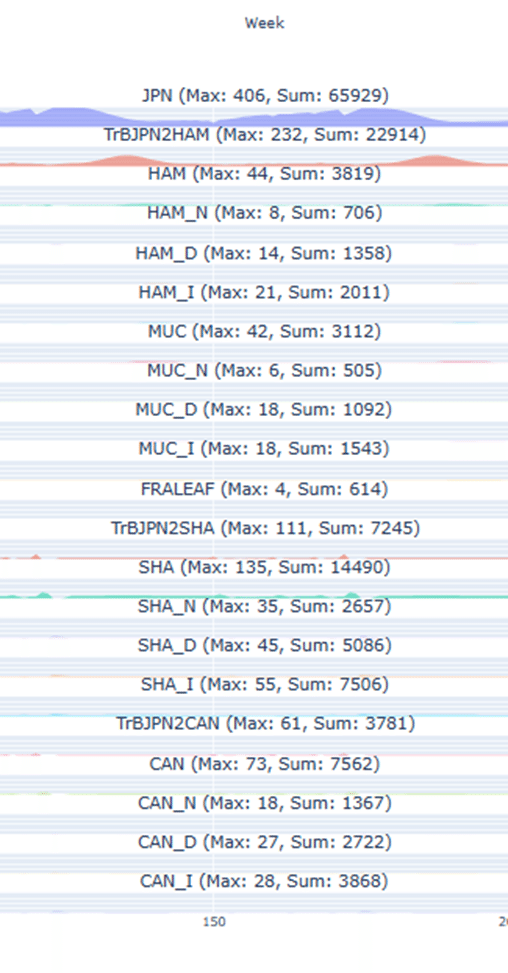
図1-1の青色の棒グラフは、生産側の供給量を示しています。ここで、生産会社は安定した生産供給体制で生産コストを抑えるという生産供給方針を取っています。
一方、赤色の棒グラフは、市場からの需要量を示しており、最終市場から生産側へ、リードタイムオフセットして伝播してきた需要の総量を集約した出荷要求ポジションを示しています。
緑色の折れ線グラフは、在庫の推移を示しています。
安定供給により生産コストを抑えたい生産会社と、ピーク需要に合わせて商品を確保して売上につなげていきたい販売会社、という立場の異なる事業会社間の要求に応えるために、ここでは、マザープラントの完成品倉庫あるいは出荷ヤードをバッファ在庫として、需給ギャップを調整することを想定しています。
次に、「図1-2. グローバル生産拠点にデカップリング・ポイントを置いた場合」は、サプライチェーンのすべての拠点の在庫推移を表示しています。ここでは、デカップリング・ポイントをグローバル生産拠点(マザープラント)に指定したことで、需要変動を吸収するバッファ在庫をマザープラントの完成品倉庫に設置しているというオペレーションをイメージすると全体の在庫推移の様子が分かりやすいと思います。そして、図1-2の末端市場の各国の販売チャネル上では、ほとんど在庫が発生していないように見えます。
ここで、「販売チャネル上に、ほとんど在庫が発生していないように見える」のは、在庫推移グラフの縦Y軸をサプライチェーン上の最大在庫に合わせているからで、「図1-3. サプライチェーン全拠点の在庫推移 (拠点毎の個別表示)」のように、各在庫拠点毎の在庫の高さでグラフの縦軸を調整して個別に表示すると、それぞれの拠点の在庫推移が判別できます。
なお、図1-1の在庫推移のグラフの横軸は、ISO Weekで、事業計画の5ヵ年分の期間をシミュレーションしています。
縦軸は、サプライチェーン上のすべての事業拠点に共通する「共通ロット単位」で、生産・出荷・在庫の数量を表しています。
「図1-4. 拡大図 サプライチェーン全拠点の在庫推移 (在庫の最大値と期間内の総量)」は、各在庫拠点の最大在庫量、期間内の在庫総量を示します。
バッファ在庫の配置パターンをすべて列挙して、それぞれの配置パターンに対してバッファ在庫の推移を表示するので、サプライチェーン上のどこの拠点に、どの程度のバッファ在庫を配置すれば良いかが一目で分かり、需要変動を吸収する仕組みを検討する上で有効な手段となります。
【バッファ在庫の評価方法】
評価方法については、当初、線形計画や機械学習のアプローチも検討していましたが、以下の「表1. サプライチェーン上のデカップリングポイントの検索・抽出結果」のとおり、デカップリング・ポイントとなるバッファ在庫の配置パターンの数は限られていることが分かりました。
したがって、すべてのバッファ在庫配置パターンを対象に、総当たりで在庫保管費用を評価、算定して、グローバル在庫保管コストが最小になる配置パターンを特定するアプローチでよいのではないかと思います。
ここでは、デカップリング・ポイントの制約として、「デカップリング・ポイントは、特定の製品が通過するサプライチェーン上に1か所のみ存在するという制約」を前提として、バッファ在庫の配置パターンをリスト・アップしています。
各在庫拠点の最大在庫量、期間内の在庫総量は、「図1-4. 拡大図 サプライチェーン全拠点の在庫推移 (在庫の最大値と期間内の総量)」に示すとおりです。
在庫の保管スペースの評価方法、コスト計算式を、例えば、
在庫保管コスト = バッファ在庫の年間ロット数(ピーク時maxまたは、年間総量、年間平均) X 在庫拠点の単位ロット当たり保管費用
とすることで、すべてのバッファ在庫の配置パターンを評価して、在庫保管コスト最小となる在庫配置、デカップリング・ポイントの位置を特定することは比較的容易であると思います。
ただし、各国の通貨、関税などのコスト増への対策として、保税倉庫を利用するケースや、極端なケースでは、地元の学校の利用されていない体育館を借りて在庫保管することで保管コストを抑える事例など、様々な在庫保管コストの抑制策が想定される部分で、各在庫拠点の実態に合わせたコスト評価が必要になることもあります。
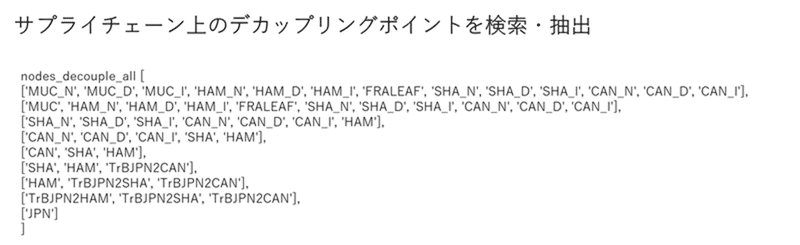
ところで、図1-2では、デカップリング・ポイントをグローバル生産拠点に設置した場合、グローバル全体の需要変動を一か所で吸収する様子を示していますが、このようにグローバル需給の変動を1か所のバッファ在庫で集中管理するケースでは、在庫の保管スペースが大きく膨らむため、事前にバッファ在庫の変動をシミュレーションから、最大在庫量、期間内の在庫総量を算定し、十分な保管スペースを確保することは非常に重要です。
在庫シミュレーションを行わずに、経験と感のみでバッファ在庫を設置して、いざ先行生産を進めるうちに想定した在庫保管スペースがパンクして、生産ライン横の仕掛品の通路にまで在庫が溢れ、先行生産を断念するといった事例、バッファ在庫の経営効果を享受できないまま、バッファ在庫の設置を諦めてしまうケースも実際にあります。
説明が前後しますが、「図6-2-1. デカップリング・ポイント(すべての販売チャネルで在庫を構える)」、「図6-2-2. デカップリング・ポイント(中間の’CAN’, ‘SHA’, ‘HAM’で在庫を構える)」に示すとおり、実際のデカップリング・ポイントの位置は、サプライチェーン上のより市場に近い流通拠点にバッファ在庫として分散設置するケースが多いと思われます。
「図2. サプライチェーンのツリー構造」は、今回のデモ用に定義したサプライチェーンの各事業拠点の需給関係 (ツリー構造の親子関係) を示しています。
この需給関係を前提として、「図3. バッファ在庫を中間事業拠点と販売チャネルに併設した場合」では、バッファ在庫が流通側の物流拠点に移動、設置されている様子が分かります。
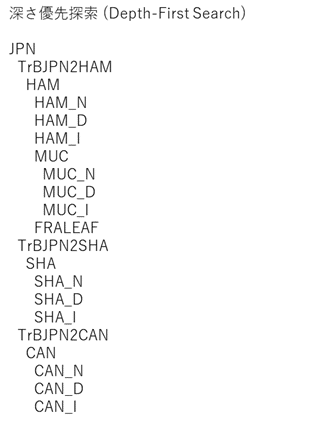
図3では、以下のように地域によって流通経路上の異なる事業拠点にバッファ在庫を設定しています。
1. バッファ在庫の一部をサプライチェーンの中間事業拠点に設定
例えば、欧州域内在庫をハンブルグ(HAM)に、中国の域内在庫を上海(SHA)に設定
2. バッファ在庫の一部を販売チャネル上に在庫設定
CAN(中国の広州)に対して、販売チャネル上に在庫設定
図3からは「中間拠点の在庫推移」と「最終販売チャネルの在庫推移」との違いがよく分かります。ここでは、域内(HAMハンブルグ, SHA上海)のバッファ在庫の推移と、販売チャネル(CAN_D,CAN_I,CAN_N: 広州の直販、間接販売、ネット販売)上のバッファ在庫の推移を示しています。
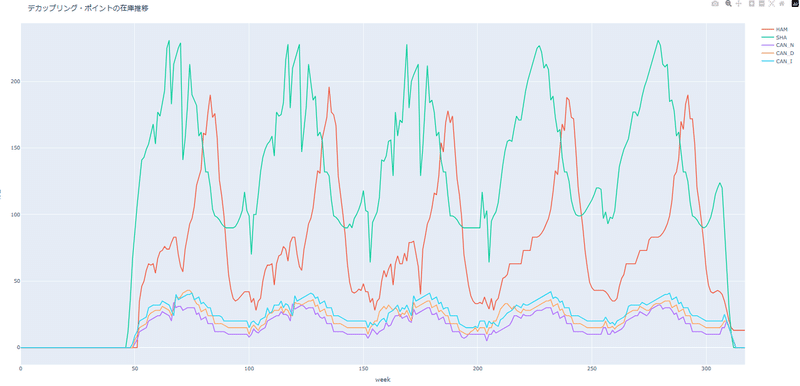
ところで、デカップリング・ポイントの位置が、マザープラントからサプライチェーンの流通サイドに移動した時、先ほどの図1のグローバル生産拠点の在庫推移はどのように変化しているのでしようか?
「図4. グローバル生産拠点の在庫推移(デカップリング・ポイントが流通側にある場合)」に示すとおり、グローバル生産拠点におけるバッファ在庫の大きな変動が解消して、安定的に操業しています。
図4のグラフからは、プラントの保守点検などで長期休暇の非稼働週が年間に1~2回発生する以外は、生産・即出荷していることが分かります。
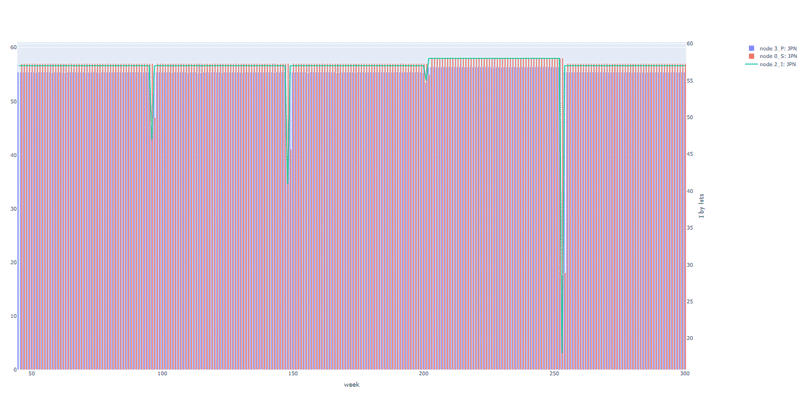
なお、今回の生産平準化のシミュレーションでは、需要変動を吸収するために「先行生産」で対応する方針をとっており、生産能力は一定にしています。
市場からの総需要量と総供給量とのバランスを取りながら、先行生産の期間(例えば13週先行など)をパラメータ指定することで、生産拠点側の確定出荷計画を生成しています。
【共通ロット単位を粒度とするPSI計画の操作】
いままで見てきた在庫推移グラフの縦軸は「共通ロット単位」にロット数を示しています。
「図5-1. 拠点毎、週毎にロットIDを積上げた結果 (拡大図1)」のとおり、グラフを拡大表示すると、サプライチェーンの各拠点の各週の中には、共通ロット単位のロットIDが在庫として積み上がっている様子が分かります。
つまり、「ロット積上げ方式のPSI操作」によって生成された共通ロット単位の在庫推移グラフであることが分かります。
【ロットIDの生成とロット積上げ方式によるロット操作】
以下では、サプライチェーン計画の処理において、ロットIDとロット操作がどのように行われているか、簡単にご紹介します。
ここで、ロットIDの付番は、最終市場の販売チャネル毎、ISO Week毎に自動付番されています。
生成されたロットIDは、最終市場から流通経路を遡り、リードタイム・オフセットされて生産拠点に集計され、共通ロット単位の需要計画情報として、グローバル生産拠点にself.psi4demandという名称でセットされます。
一方、グローバル生産拠点では、生産平準化処理(今回は、先行生産処理)と出荷計画の確定処理を行った後に、ロットID毎に、供給計画として出荷先の市場に向かって展開され、各事業拠点においてself.psi4supplyという名称でセットされます。
確定出荷計画をもとに、各ロットID毎にサプライチェーン上の各流通拠点を経由して、最終市場の販売チャネルの着荷ポジション(着荷週)を計算し、着荷週へのロットIDの積上げ処理を行っています。
言い換えると、生産出荷されたロットを最終市場まで出荷するシミュレーションを行っています。
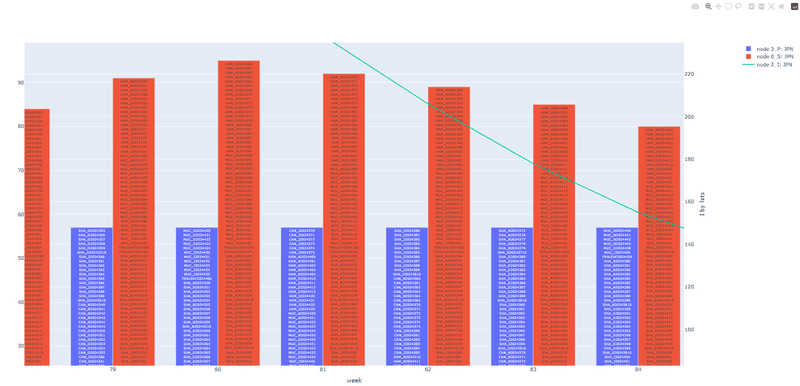
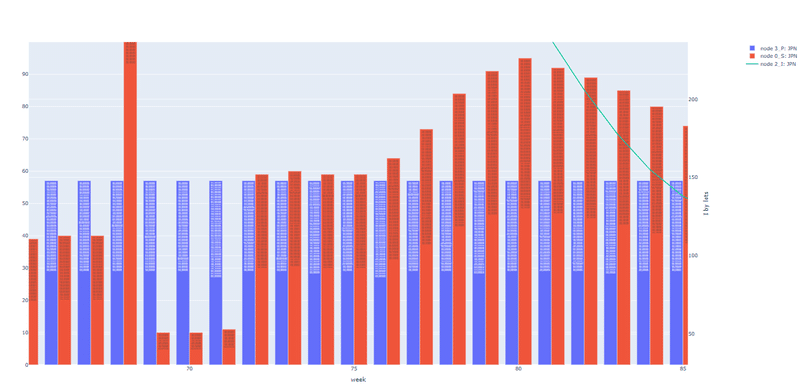
以上、今回は需要変動を吸収するためのデカップリングポイントとバッファ在庫の機能について、ご紹介しました。
【製品特性によるサプライチェーン構成の違い】
以下では、本来、最初に整理してから本記事をスタートするべきであった、いくつかの前提条件について、補足しておきたいと思います。
本記事で取り扱っている商品の特性は、比較的、重量のある素材商品や機械設備、家電製品、輸送機器などを40フィート・コンテナに入れて、船便でゆっくり搬送するビジネスを想定しています。
筆者の経験からは、1トン近い重量物を取り扱う製品のサプライチェーンにおいて、需給調整に失敗すると、年間に数回、本来は船便で輸送すべき製品を航空便で緊急搬送する、といったコスト増オペレーションが発生してするという問題が、様々な業界で共通の経営課題になっているように思います。
このようなコスト増を抑止するためにも、需要変動を吸収するサプライチェーンの仕組みを慎重に分析・設計する必要があります。
この問題を解決するためには、サプライチェーン上の「在庫の構え方」あるいは「生産計画への引当て方」といった業務の仕組みをどのように設計するかという点に注目して、検討を進める必要があります。
同時に、全世界に製品を供給販売するグローバル・オペレーションの全体像を俯瞰的に見渡すためには、グローバル・サプライチェーン全体を可視化すること、グローバル需給のモデルを定量的に把握する機能が重要になります。
グローバル経営においては、ブランド管理や販売チャネルの整備といった経営テーマと同様に、「サプライチェーンの最適化」の検討は重要な検討テーマの一つであるといえます。
例えば、アパレル業界で有名なZARAモデルでは、生産と販売をグローバル・レベルで直結して、時間差を無くしています。
ZARAモデルの場合は、需要変動に対応するために、需要変動を吸収するというよりも、実際の需要に俊敏に対応するビジネス・モデルといえます。
ここで、ZARAモデルのようなグローバル生販の直結型サプライチェーンを可能にしているのは、その商品の特徴として、
●付加価値の高い商品であること 輸送コストを高く設定できること
●商品の重量が軽いこと パッキングして航空便輸送が容易であること
にあります。
今回ご紹介しているglobal weekly supply chain plannerで、ZARAモデルをweekly supply chainとしてモデル表現することも可能ですが、生産と販売が直結するZARAモデルは、今回の中心テーマであるバッファ在庫の構え方というテーマの本題から外れるので、ZARAモデルに対する検討は別の機会にしたいと思います。
なお、筆者の経験からは、ZARAモデルの場合であれば、モデルを形成している最終アセンブリ工程、つまり縫製工場よりもさらに上流の供給サイド、素材生産に注目することで、例えば原反や染色といった工程において、今回の需給調整のシミュレーション機能、統合的なバッファ在庫の考え方が役に立つ場面があるのではないか、サプライチェーン全体において、さらなるコストダウンの余地があると思います。
【サプライチェーンの最適化の問題点】
サプライチェーンの最適化の検討が進まない理由として、サプライチェーン・シミュレーションの観点からは、以下のような問題点が挙げられます。
●グローバル・サプライチェーンの各事業会社の実態把握、現状分析に時間がかかる
●定量把握するためのサプライチェーン・シミュレーションのモデル定義に工数がかかり、さらにシミュレーションの精度を上げることが難しい
●サプライチェーン全体の可視化、全体を俯瞰する仕組みの整備、全体を俯瞰できるグラフィク表示の表現方法が難しい
といった課題があります。
【本サプライチェーン・シミュレーションの特長】
ご紹介しているサプライチェーン・シミュレーションの特長は、以下のとおりです。
1.「週次ロット」を処理の単位、モデルの粒度とすることで、中長期の経営判断に必要なデータ粒度を確保しているという点が重要な特徴です。
2. 取り扱うデータの粒度が大きい分、以下の2種類の入力データを準備すれば、グローバル・サプライチェーンのモデルを定義でき、簡単にシミュレーションがスタートできる事は、データ準備が比較的、容易であり、大きなメリットになります。
サプライチェーン・シミュレーションの入力データ
●最終市場の各販売チャネルにおける月次の需要数 (事業計画の企画台数)
●サプライチェーン上の各拠点の親子(需給)関係と輸送リードタイムと安全在庫(週単位)
3.また、モデルがシンプルであることから、短時間でシミュレーション処理を繰り返し行える点がメリットです。
【バッファ在庫配置パターン毎の在庫推移の可視化と在庫評価】
「図6-1. デカップリング・ポイントとバッファ在庫の在庫推移」は、以下の代表的な3つのバッファ在庫配置パターンについて、それぞれの在庫推移を示しています。
1. 末端市場の流通チャネル上に、すべてのバッファ在庫を設置
生産拠点、中間拠点はディスパッチする機能で保管せず直送する仕組み
2. 中間拠点、例えば、港に着荷した域内の物流倉庫にバッファ在庫を設置
3. マザープラントの出荷ヤードなど、生産拠点にバッファ在庫を設置
「図6-2-1. 6-2-2. 6-2-3.」では、バッファ在庫の配置パターン毎に、サプライチェーン全拠点の在庫推移 と、各在庫拠点の最大在庫量、期間内の在庫総量を示します。
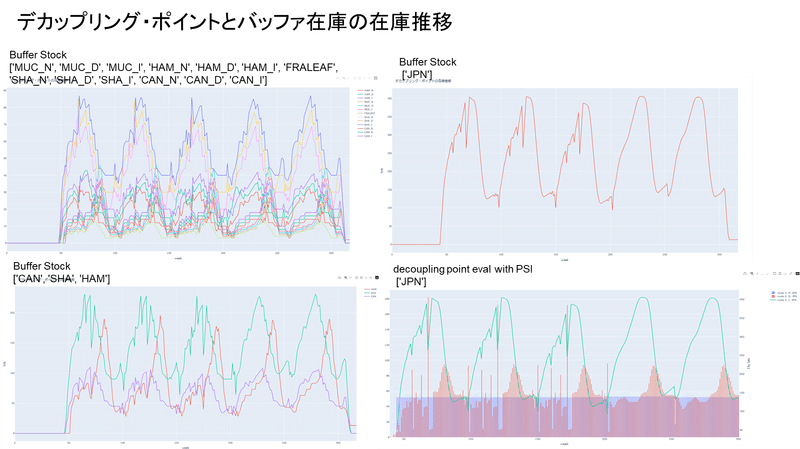
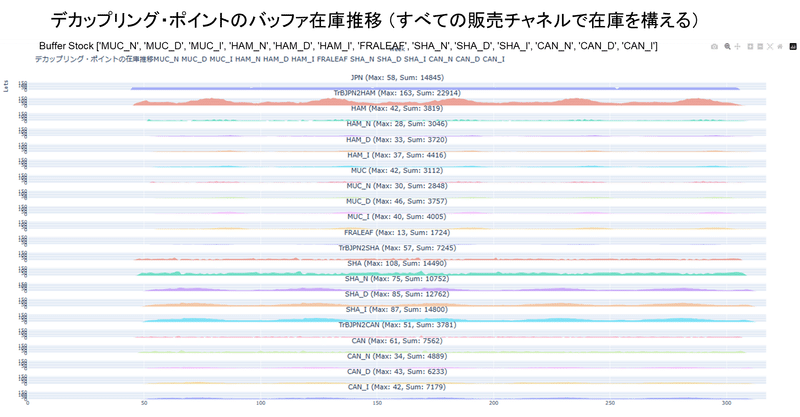
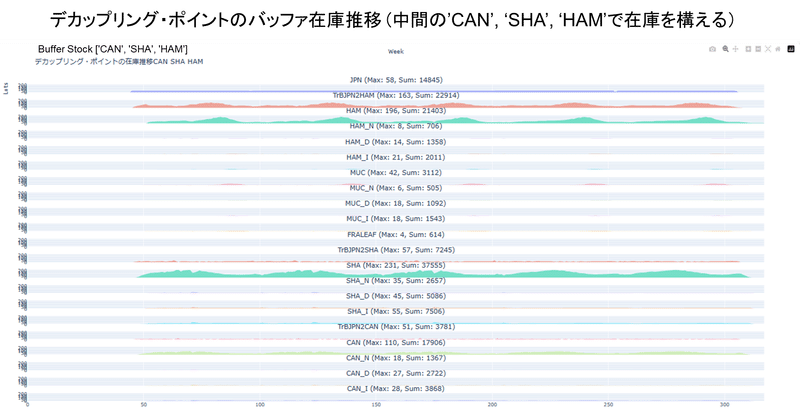
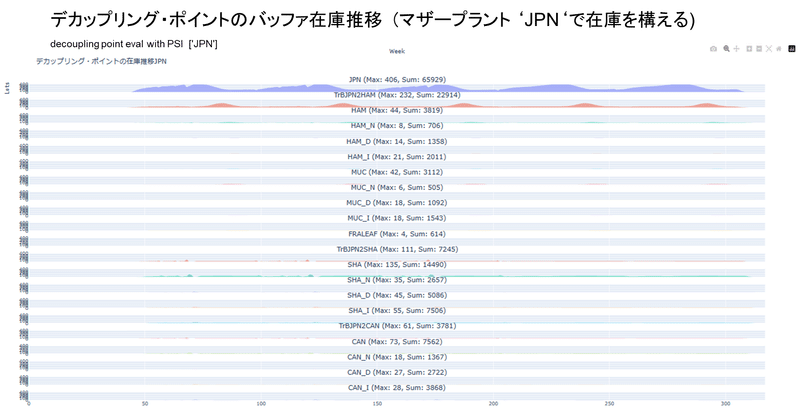
【本シミュレーション機能の処理概要】
以下では、今回のシミュレーション機能の処理概要を示します。
【入力データ】
●最終市場の月次の需要数を入力すると、ISO週の需要数を自動生成する点
●サプライチェーン上の各事業拠点間の搬送リードタイムと安全在庫を週単位で時間指定すると、最終市場から生産拠点までの総需要を計算して、
最終市場
【内部処理】
●最終市場の需要(ロット)をリードタイム・オフセットして需要計画を生成
●生産出荷拠点における生産配分 (今回は、需要変動に「先行生産」で対応)
●確定出荷・確定PO:Purchase Orderを最終市場まで展開と供給計画を生成
●需要計画(PULL情報)と供給計画(PUSH情報)から、バッファ在庫推移を生成
【出力表示】
●サプライチェーンの各拠点の在庫の推移
●デカップリング・ポイント候補となる拠点のバッファ在庫推移
●各拠点の需要計画(PULL)と供給計画(PUSH)のPSI(仕入・販売・在庫)の推移
以上、今回は、サプライチェーンの需要変動を吸収するために、在庫バッファを何処にどのくらいの在庫を設置するべきかというテーマを目標に、pythonで開発中のglobal weekly supply chain plannerにバッファ在庫をモデル定義するとともに、可視化して、動きを検証してみました。
【おわりに】
需要変動の大きい商品、特定の季節に需要ピークを持つ商品に対して、需要変動を吸収するサプライチェーンの仕組みをどのように構築するべきかという問題は、ビジネス業績に直結する問題であり、経営に与えるインパクトは非常に大きいといえます。
本記事では、サプライチェーンの需要変動を吸収するために、在庫バッファを何処にどのくらいの在庫を設置するべきかというテーマで、開発中の計画システムglobal weekly supply chain plannerに、バッファ在庫をモデル定義して、在庫の推移を可視化することで、サプライチェーン・シミュレーションの機能を検証してみました。
シミュレーションの対象とするサプライチェーンの範囲、入力データの量、コンビュータの処理性能に依存するものの、ソフトウェアのモデルの観点からは、適切なデータ粒度を採用し、制約条件のモデル化で高速処理の工夫をすることで、グローバル経営の意思入れに必要十分なレベルでのシミュレーションが可能であると思います。特に、グローバル経営の観点からは、週次の意思入れに使えるか否かという点が重要になると思います。
さらに、もう少しこの問題を広義にとらえると、需要変動にかぎらず、物流経路の変更要請やサプライヤーの生産能力の変動など、内外の環境変化に対して、柔軟にサプライチェーンの制約条件、モデルの構成要素を変化させて、供給手段のバリエーションを評価しながら最適なサプライチェーンを再構成する能力をどのように定義するか、という検討テーマにつながってくると思います。
このような環境変化に順応できるサプライチェーンの柔軟性を確保することは、グローバル経営を進める上で、優先度の高い取り組みテーマであると思います。
2023年8月 猛暑の自宅にて
【補足資料】
以下、本文にまとめきれなかった資料を追記させていただきます。
「図A. サプライチェーン上のバッファ在庫拠点と在庫推移」は、流通サイドのアウトバウンド・サプライチェーン上で、バッファ在庫の位置が変化した時に、どのように在庫が推移するかを示しています。
バッファ在庫を設置拠点として、サプライチェーンの各階層毎に以下の3つのケースを想定し、シミュレーションしています。
ケース1. マザープラントの出荷ヤードにバッファ在庫を新たに設置した場合
ケース2. 中間拠点 域内事業会社にバッファ在庫を設置した場合
ケース3. 最終市場の販売チャネル・実店舗にバッファ在庫を設置した場合
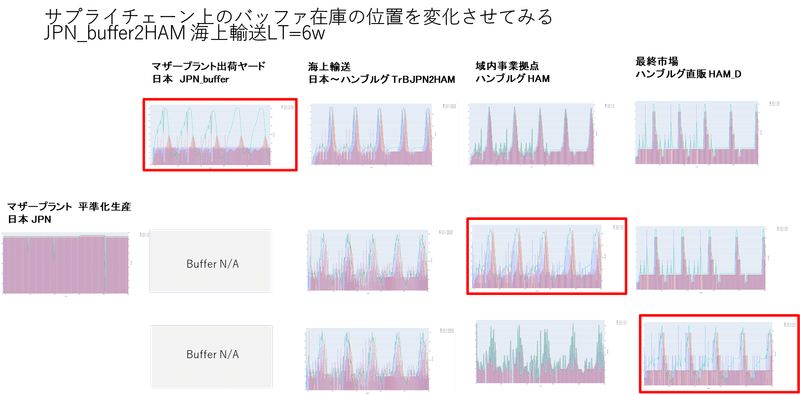
シミュレーション結果からは、「それぞれのケースで、バッファ在庫の高さをシミュレーションから確認することができる」点がメリットになります。
例えば、「図B-1. マザープラントの出荷ヤードにバッファ在庫を持つ場合」は、マザープラント(グローバル生産拠点)の出荷ヤードに、グローバル総需要の年間需要を吸収する在庫バッファーを設定した場合に相当します。
バッファ在庫がどのように推移するかを示しています。
ここで、在庫量はロット単位で示され、ピーク時には最大で350ロット前後の在庫を保管することが必要になることが分かります。
同様に、「図B-2. 域内の中間事業拠点にバッファ在庫を持つ場合」は、最大で270ロット前後のバッファ在庫。
「図B-3. 最終市場の販売チャネルにバッファ在庫を持つ場合」は、最大で33ロット前後のバッファ在庫。
というようにバッファ在庫の容量をシミュレーション結果から読み取ることができます。
ここで、域内の中間事業拠点とは、欧州アフリカ(EMEA)、北米(NA)、南米(S Americas)、東アジア(EA)、南アジア(S Asia)、中国(China)など、グローバルで6州前後のリージョンを定義しており、それぞれに域内在庫拠点の設置が想定されます。
また、末端の販売チャネル上の在庫拠点は、各国の販売会社の先の販売チャネル上の在庫拠点となるので、総拠点数は数百~数千のオーダーになることが想定されます。
一方、バッファ在庫を設定した事業拠点から先、市場の方向へ展開されているサプライチェーン上の各事業拠点では、需要と供給がマッチすることから効率的なオペレーションが計画されています。
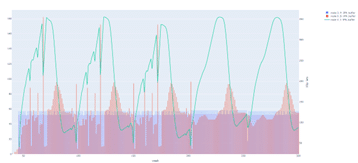
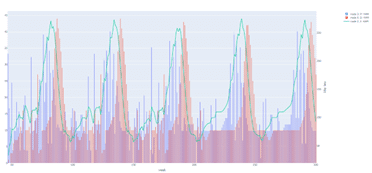
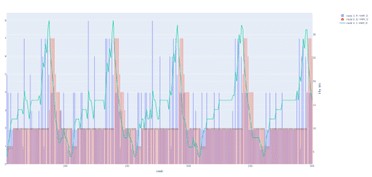
以上
この記事が気に入ったらサポートをしてみませんか?