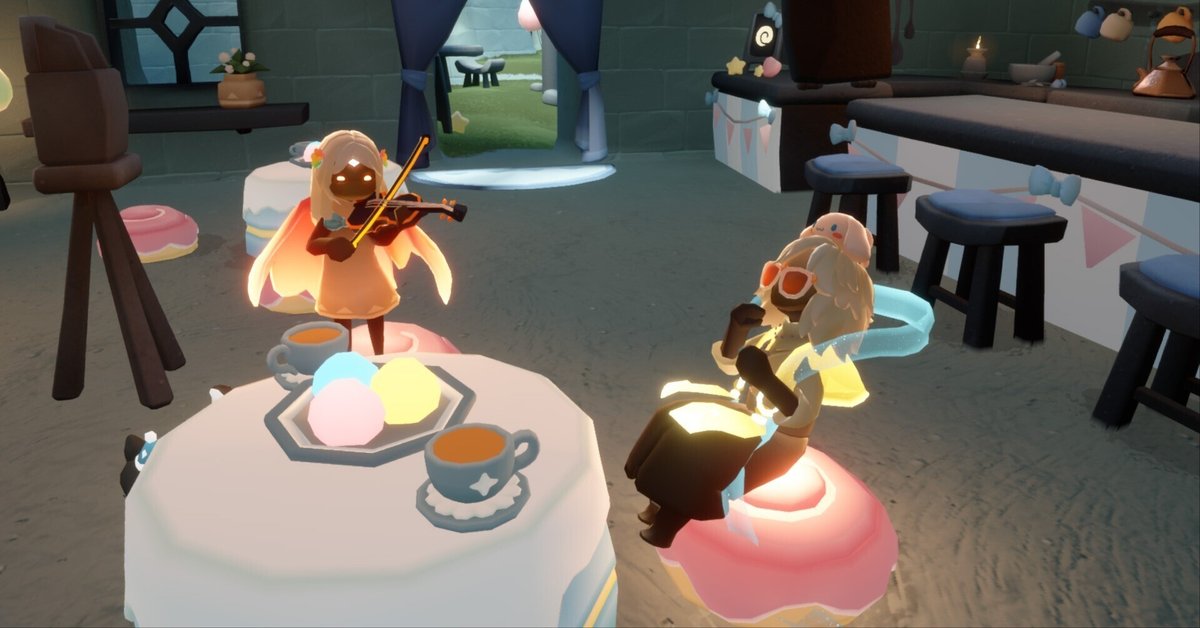
01_製造プロセスの設計
背景
大学内で進めてきた院内製造品について、特定臨床研究で臨床試験を進めるに当たり、より高品質に作製する必要があった。これまでは真空引きしたグローブボックス内で嫌気的に作業してきたため、作業負荷が高く、かつ品質にばらつきがあった。
目的
グローブボックス内での作業よりも容易な製造工程とする
嫌気性を維持した製造工程とする。
メンテナンス性の良い製造工程とする。
手段
仮説立案
まずはこれまでの製造工程の現場での確認や、作業者が想定する理想的な製造工程が描かれた資料を確認した。理想的にはこれまでの工程の作業者に直接ヒアリングをしても良かったかもしれないが、業務委託で即時で結果を出したかったので、現状ベースではなく理想の絵を描くことから開始した。成果物として製造工程をiPadでイラスト作成し、およその工程を描いた。
探索
次に、描いた製造工程を実現する方法を探索した。使い捨ての容器(バッグ)とチューブによって構成される工程を想定していたが、バイオ業界には「シングルユース製品」というのが細胞培養系の製造プロセスで使用されていることを知り、活用することとした。
設計
シングルユース製品を活用した製造工程をざっくりと設計した。
論点整理
おもに以下の比較表を作り、論点整理した。
シングルユース製品を国内で販売しているベンダーの比較(売上高、設立、資本金、従業員数、医療事業への関わり、ラインナップ、メリット、デメリット)
製造工程に登場する各容器やチューブに求められるスペック(数量、用途、容量、滅菌済・洗浄不要、温度耐性、、ハイバリア性(低酸素透過)、低溶出性、物理的耐久性、可視性、脂質・タンパク質低吸着性、低不純物、接続性)
各工程の選択肢
既存設備と新規設備
以上の内容を業務委託開始から2週間程度でまとめ、最終的に選択したベンダーに依頼を持ち込むこととし、打合せを開催した。結果的に、依頼しようと考えていたベンダー上位2社が連携していることが判明したり、インターフェックスジャパンで両社と対話することができるなど幸運もあり、無事に製造工程のFixと試作品の発注に至った。
結果
ベンダーとの良好な関係を築き、試作品を無事に入手することができた。2024年6月現在も、当初私が設計した製造工程を踏襲する形で製造されており、設計としては成功したと考えている。
学び
良かったこと
製造業において機械系エンジニアとして社会人をスタートしたので、製造工程の設計がスムーズにできた。
探索において運良くシングルユース製品にたどり着けた。このときレファレンスとして再生医療等製品の製造方法を模倣しようとサーチしていたのが良かったのかもしれない。
委託先ベンダー、製造工程で取りうる選択肢という重要な論点順に議論を進め、ベンダーを決めた後はコンサルティングのようなことも受けながら一緒に製造工程をFixしていけたこと。
試作品の設計まではできても、その試作品を使った製造実験が上手にできるイメージが無かったが、たまたま2022年2月に入社したCMCエンジニアが得意だったので、スムーズに業務を移管できた。
反省
試作品を作ったが、フィルター容器のメッシュサイズが大きすぎたこと。どんなものも大きく作りすぎる傾向があるのは反省。大は小を兼ねないケースも大きい。
試作品のパラメータを振ることを最初から想定していればよかった。委託先がそのようなことが可能なことに考えが至らなかったかも。
2021.11-2022.02
ここから先は
¥ 1,000
この記事が気に入ったらサポートをしてみませんか?