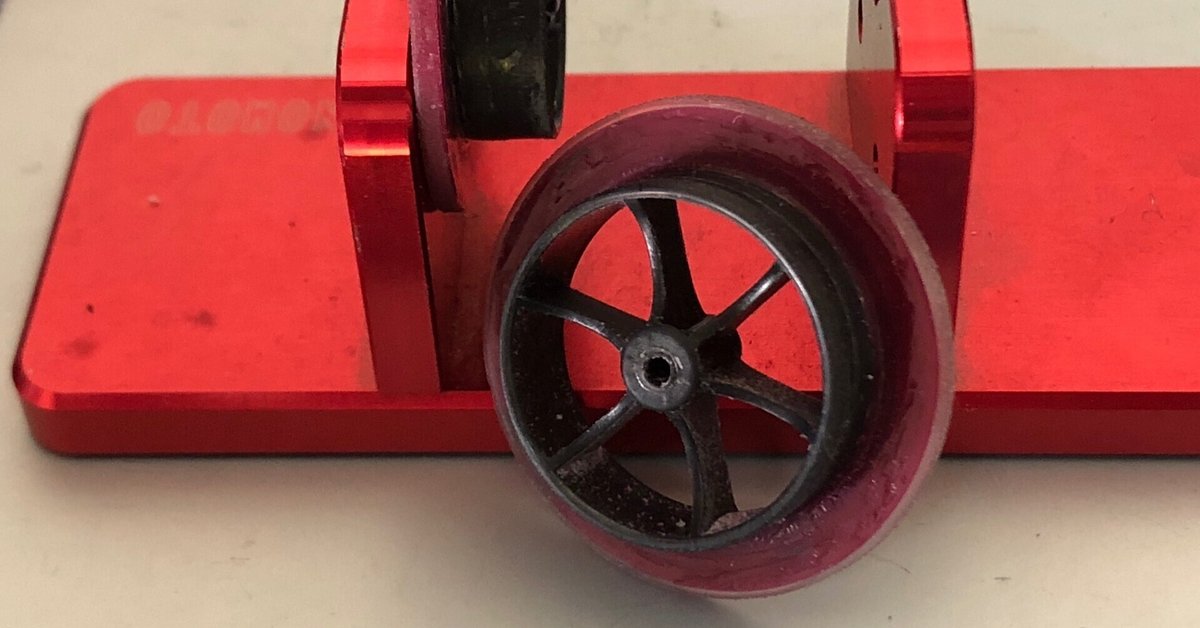
タイヤ加工の精度を出す!後編
【はじめに】
皆さんこんばんは。現場猫で学ぶミニ四駆チャンネル管理人?のミヤです。
今回はタイヤの成形後編になります。まだ前編を読んでいない方は前編を読んでみてね!
【タイヤの選定】
①素材の違いについて
現在、ミニ四駆で使われているタイヤ素材は熱可塑性エラストマー(TPE)という素材が使用されています。昔のタイヤはゴムだったので、天日干しするとグリップが落ち、干しタイヤと呼ばれるツルツルのタイヤになりました。
熱可塑性エラストマーは「軽量」「着色が容易」「加工が簡単」「熱可塑性を持つ」「耐候性が高い」「リサイクルしやすい」性質を持ちます。非常に扱いやすい素材でゴムのような性質を持つため、ゴムの代わりにかなりの分野で熱可塑性エラストマーが利用されています。
分子構造の特性により、熱可塑性エラストマーは高い弾性を示します。すべての熱可塑性エラストマーは、拘束相と非拘束相で構成されています。拘束相となる結晶性ポリマーと、非拘束相となる柔軟な非晶性ポリマーの組み合わせがある構造や、ひとつのポリマー鎖に拘束相ブロック(ハードブロック)と非晶性ブロック(ソフトブロック)を持つブロック共重合体が例として挙げられます。
ハードブロックは、熱可塑性エラストマーやそのコンパウンドにおいて、最終製品の熱可塑性 を担うもので、易加工性や耐熱・耐寒性、耐薬品性などの材料特性を有します。接着性もこれらの特性により左右されます。ソフトブロックはゴム弾性を担い、硬度や柔軟性などの材料特性を左右します。引き裂き強度や引張強度、永久変形の程度 は、ハードブロック、ソフトブロックのどちらからも影響を受けます。
ここで厄介なのは耐候性が上がってしまい紫外線を当ててもなかなかグリップが落ちてくれません(UV材でも混ざってるの?)。ミニ四駆的には非常に困ります。そこでパーツクリーナ(ヘキサン)に浸すとソフトブロック側の特性が変質し、柔軟性が失われていきます。結果としてノーマルな状態よりはグリップが抜けた状態になります。ただ、これは浸す時間の問題なのか色の違いなのか抜け具合が結構違ったりします。
2000年代後半から徐々にTPEに切り替わっているみたいなのでのでゴムタイヤを干したい方は、昔のキットを狙ってみましょう。ノーマルタイヤでの見分け方は、タイヤの内側に規則性のあるフローマークがあるものはTPEと言えます(光の当て具合でわかります)。触感はTPEのほうが柔らかいです。
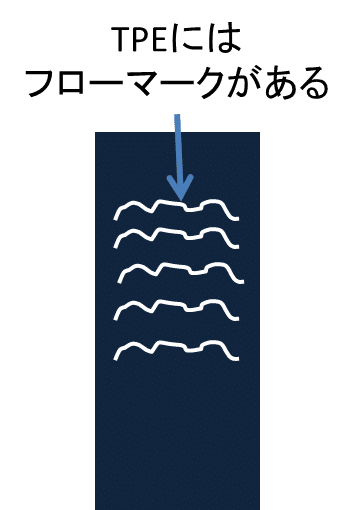
カラータイヤのほとんどはTPEですが、一部、昔の材料で作られていたものもあります。リンゴジャムの赤タイヤや復刻版前のウイニングバードなどは同じ材料で作られているそうです。
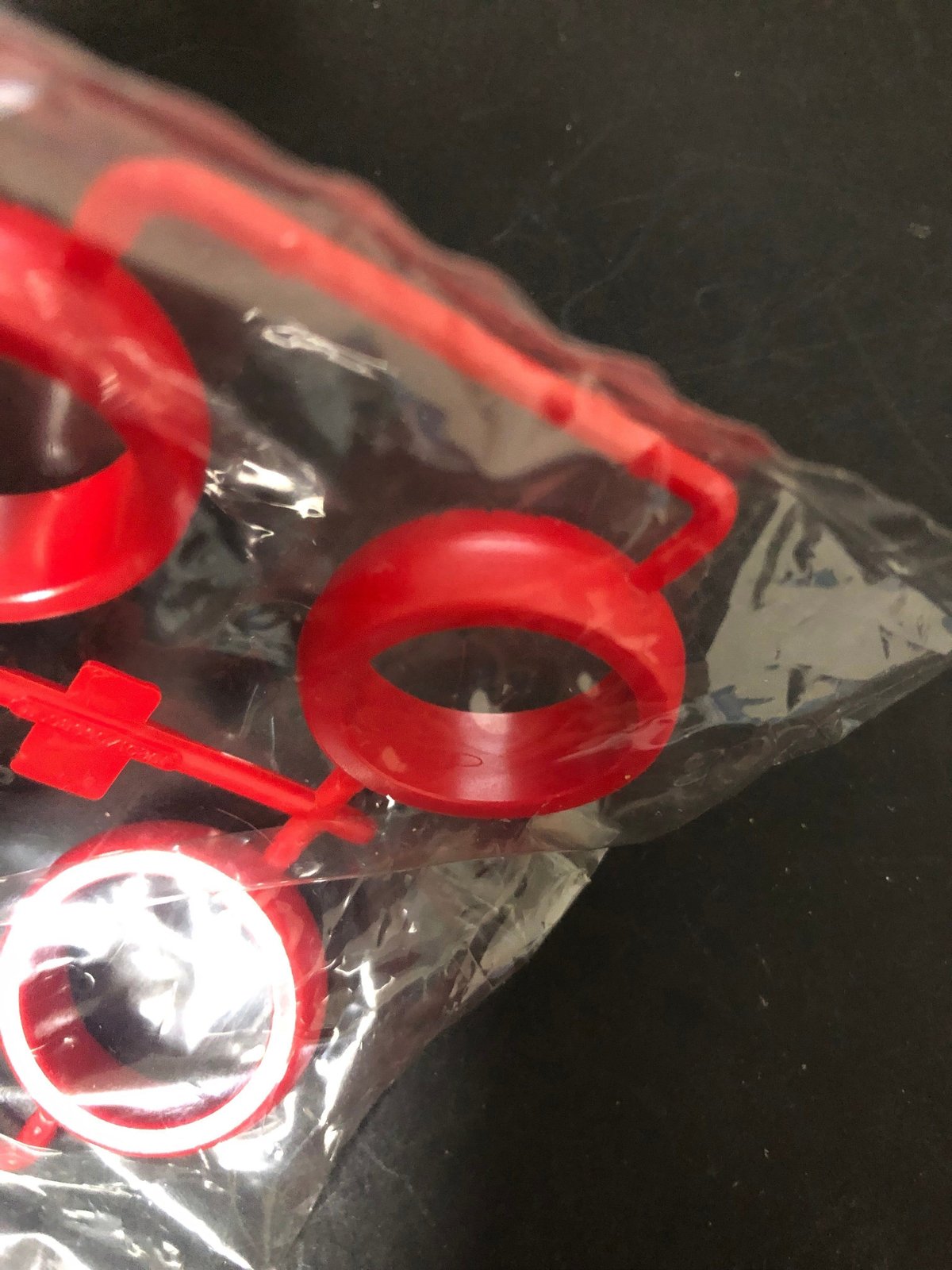
初期の大径ハードスリックタイヤホワイトはTPEなのかよくわかりませんが、今のスーパーハード並みの固さです。当時、自分はインナーにしか使っておらず、アウターとして使っていなかったのですがどうやら干せるらしいです(知らんかった)。ちなみにこのタイヤは普通に伸ばして接着剤で付けようとするとタイヤがちぎれます。発泡スチロールに接着剤を垂らした感じみたいにちぎれます。
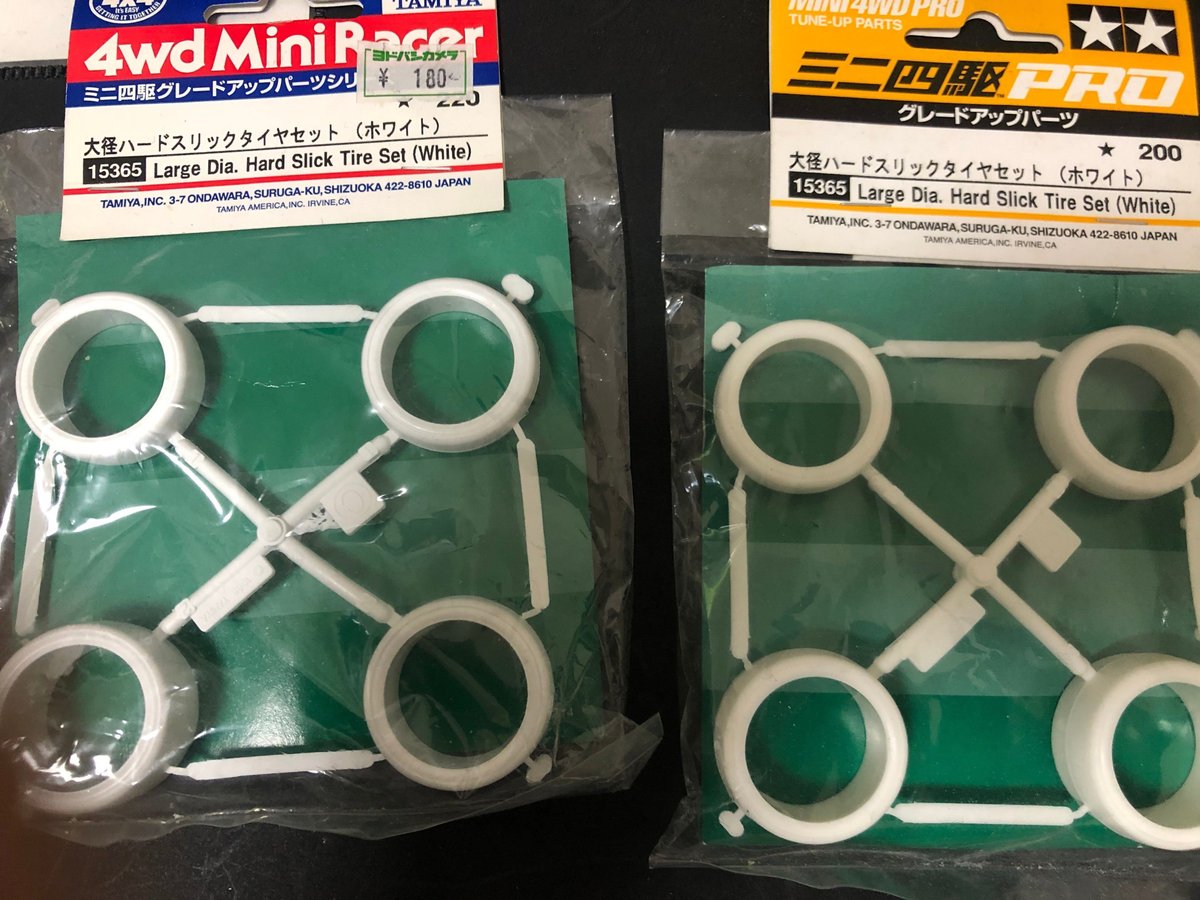
このタイヤ自体はPROタグ時代に販売されたものですが、途中から千切れない材料に切り替わっています。その後、価格改定(200→220円)で青タグになるのですが、一部、初期のタイヤが混入してたりします。中古屋さんで見つけた際は確認してみると良いです。
見分け方は簡単で固いです。あと色目も違います。恐らくマスターバッチはグレーっぽいホワイト系だと思われます。
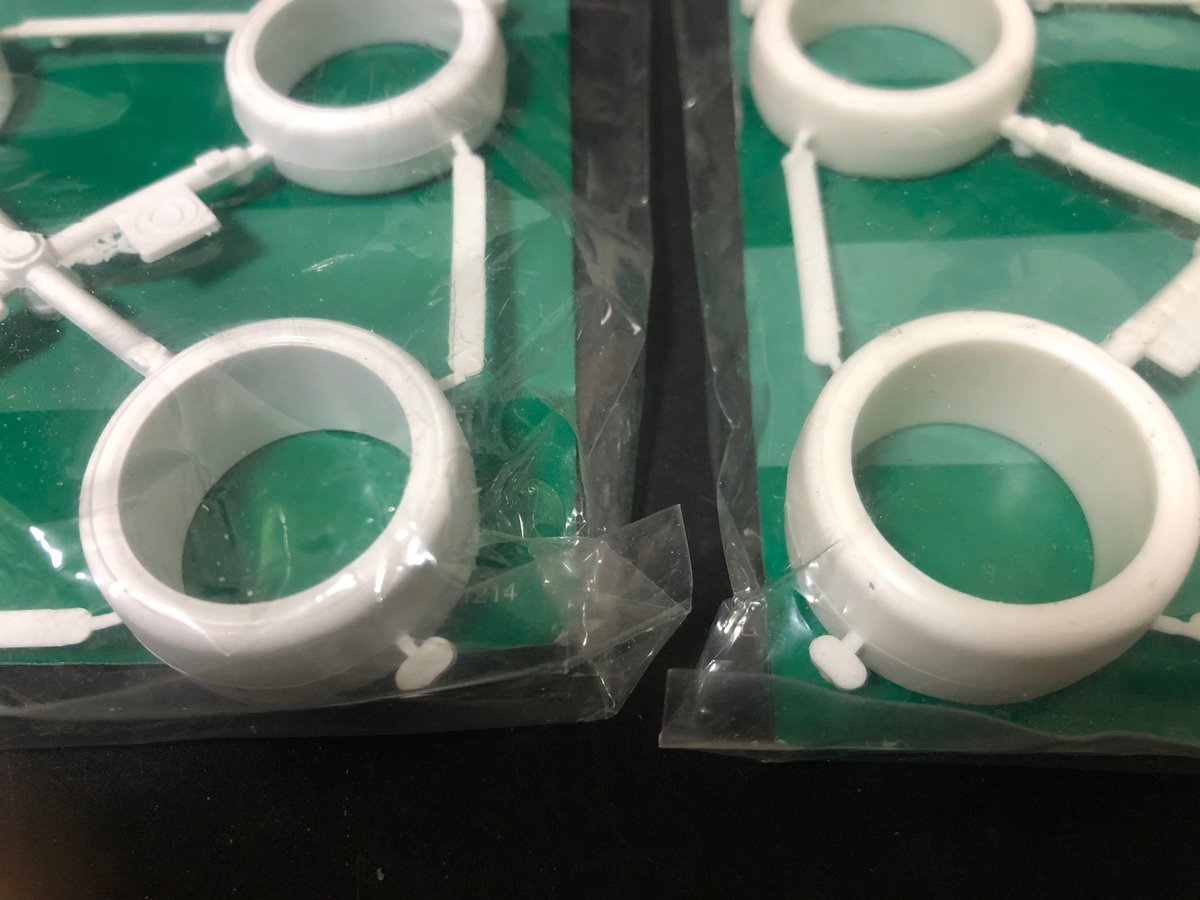
シリコンタイヤもPROタグ以降からから材料が変わっており、柔らかくなっています。
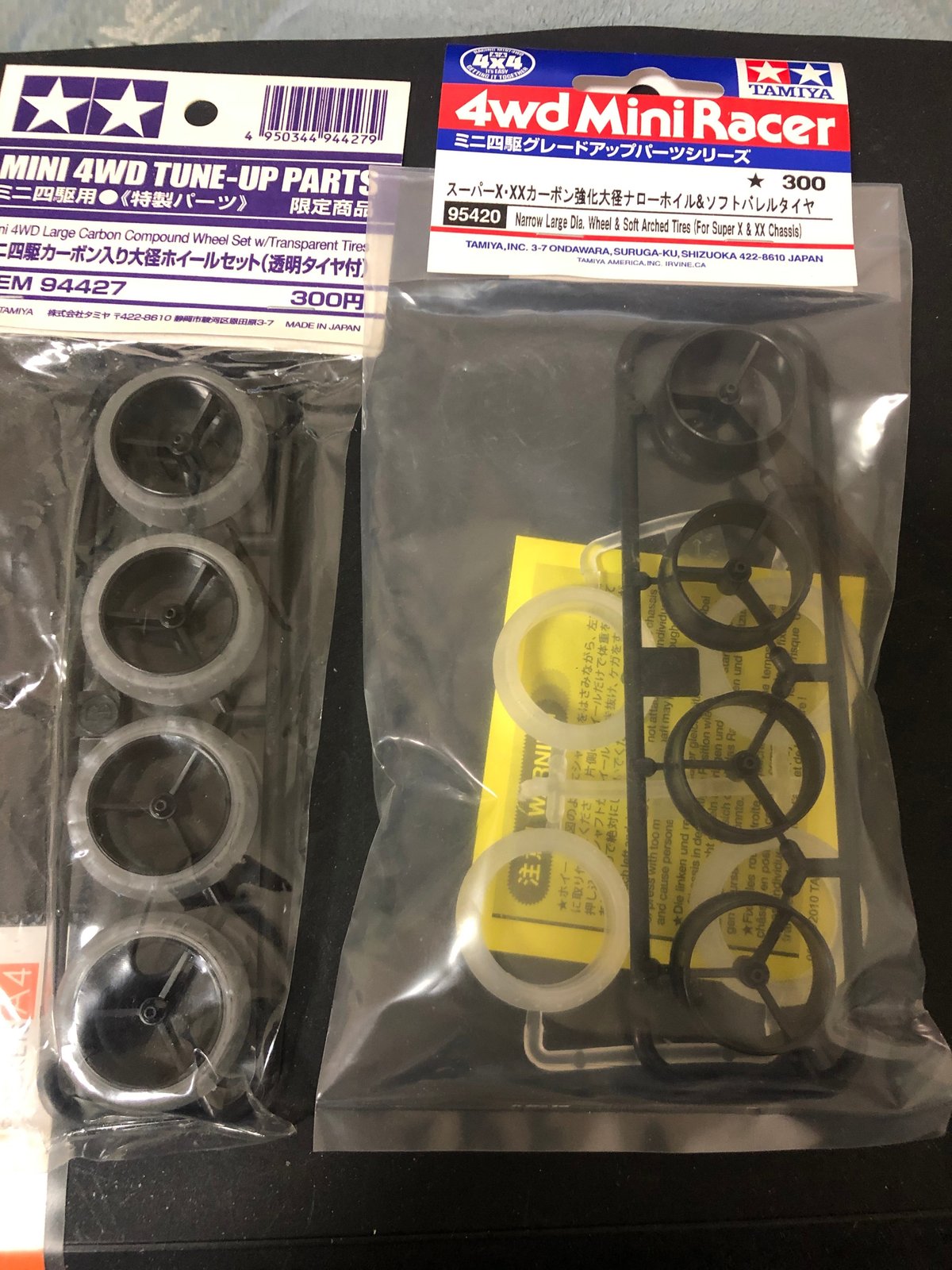
②下準備
使用するタイヤを幅3~4mmにスライスします。デザインナイフに水をつけて切ると綺麗に切れます。
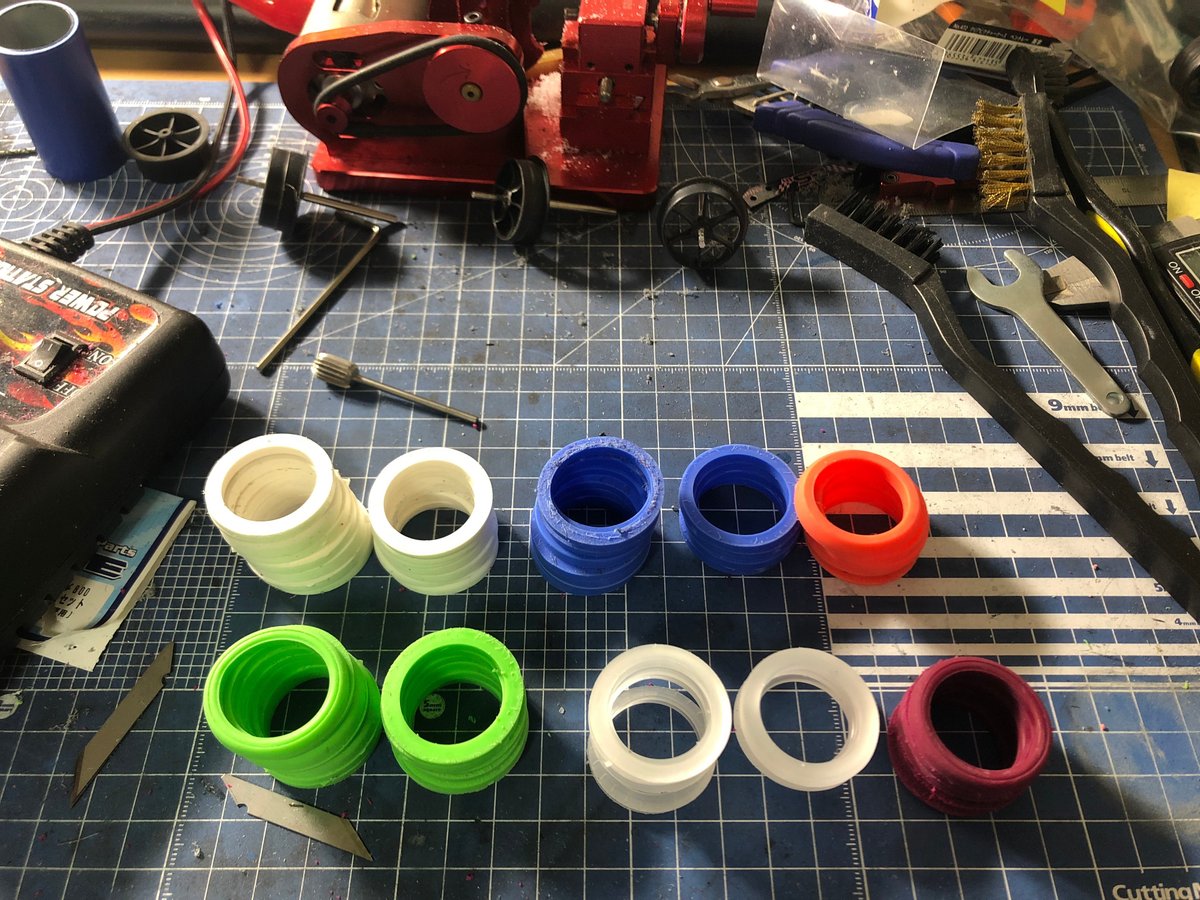
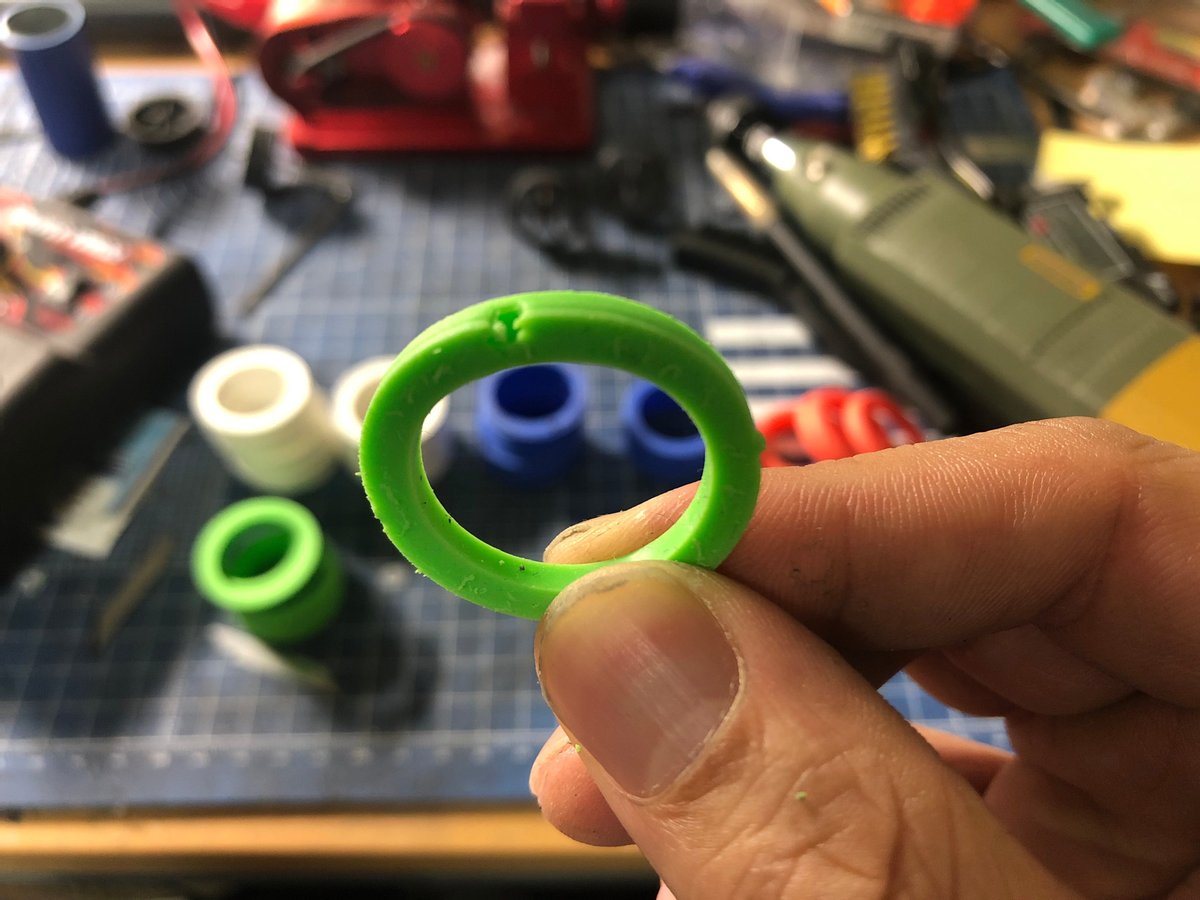
切ったタイヤの一部はパーツクリーナーに漬け込みます。
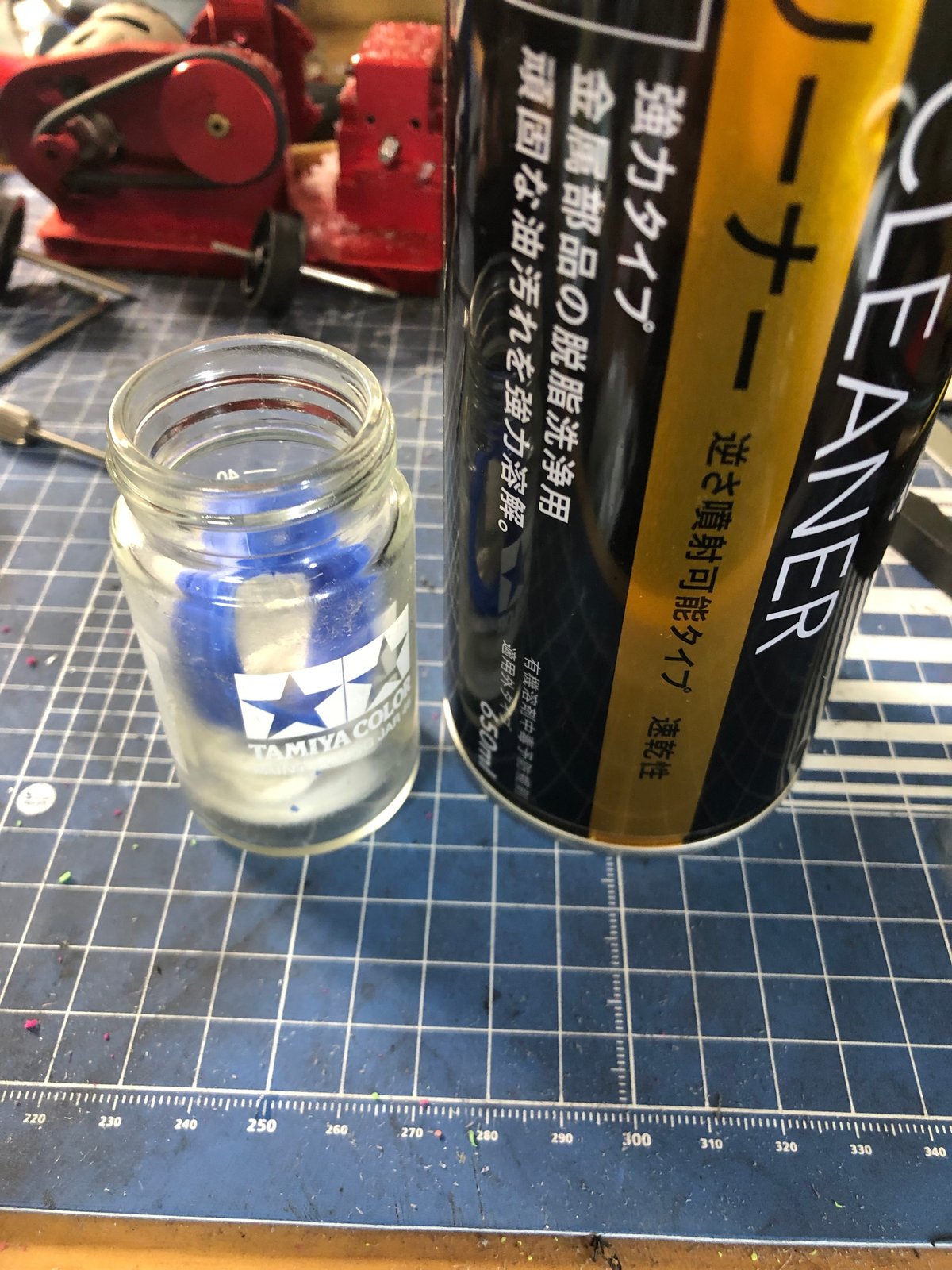
漬け込んだタイヤは超大径の治具(パイプ)に取り付けます。
パイプのサイズは25mmと32mmのパイプを使用しています。他に23mm、27.5mmがあると便利です。
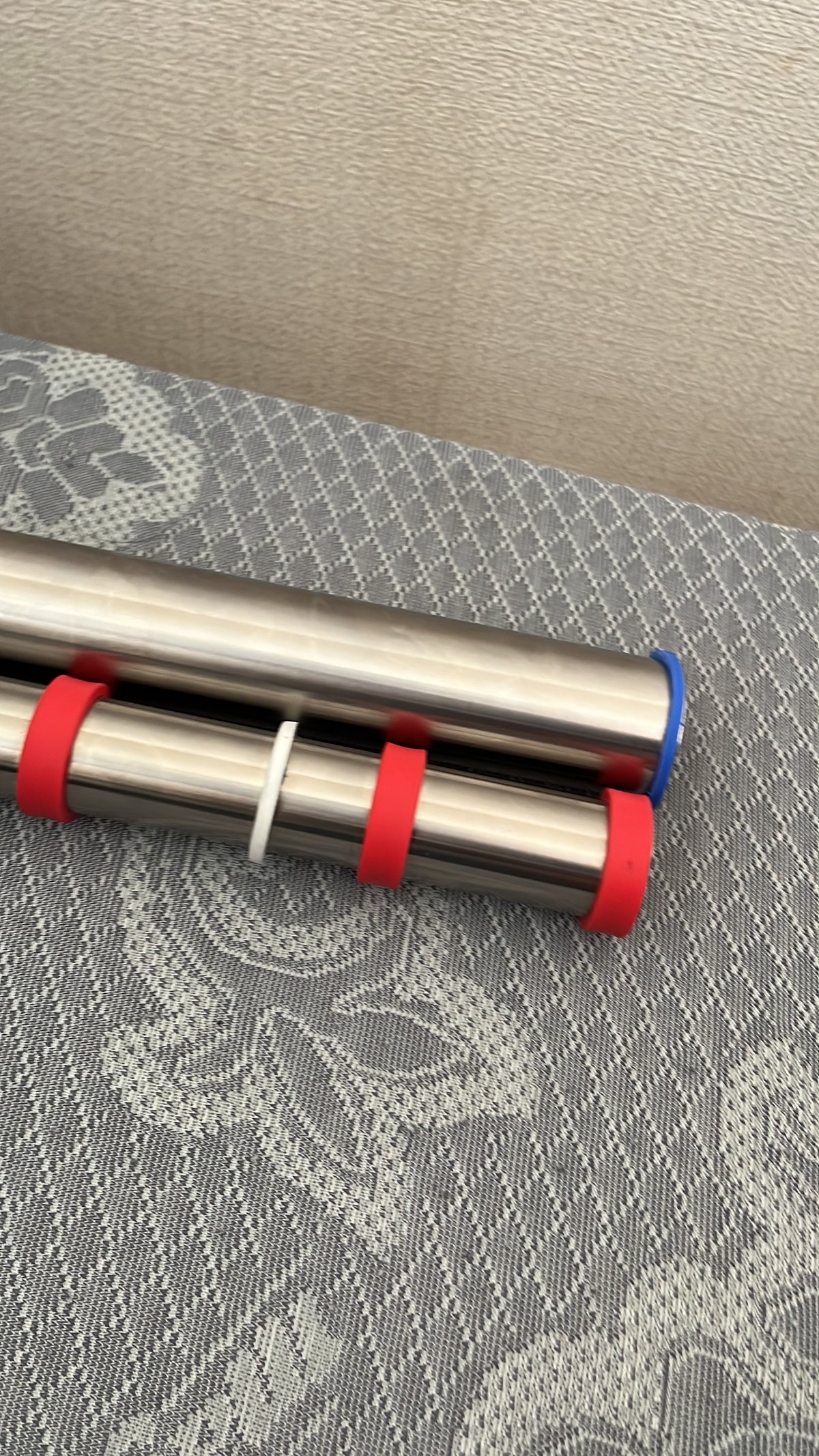
③インナー・アウター
私の場合はインナー2or3層アウター1層タイプの超大径を作ります。
縮みタイヤを使うと必然的に層が増えていきますが、マルーンだとインナー2層で出来ます(ホイール径による)。タイヤを接着する接着剤はお好きなものを使用してください。自分はヨコモの接着剤を使用しています。
(低粘度なら何でもいいです)
PPホイールを使用する際はPP対応の接着剤を使用します。
瞬着硬化スプレーもあると作業性があがります。
硬化剤を使用しない場合は、接着剤が乾燥するまでは回転させないように注意してください。ムスカさんになります。
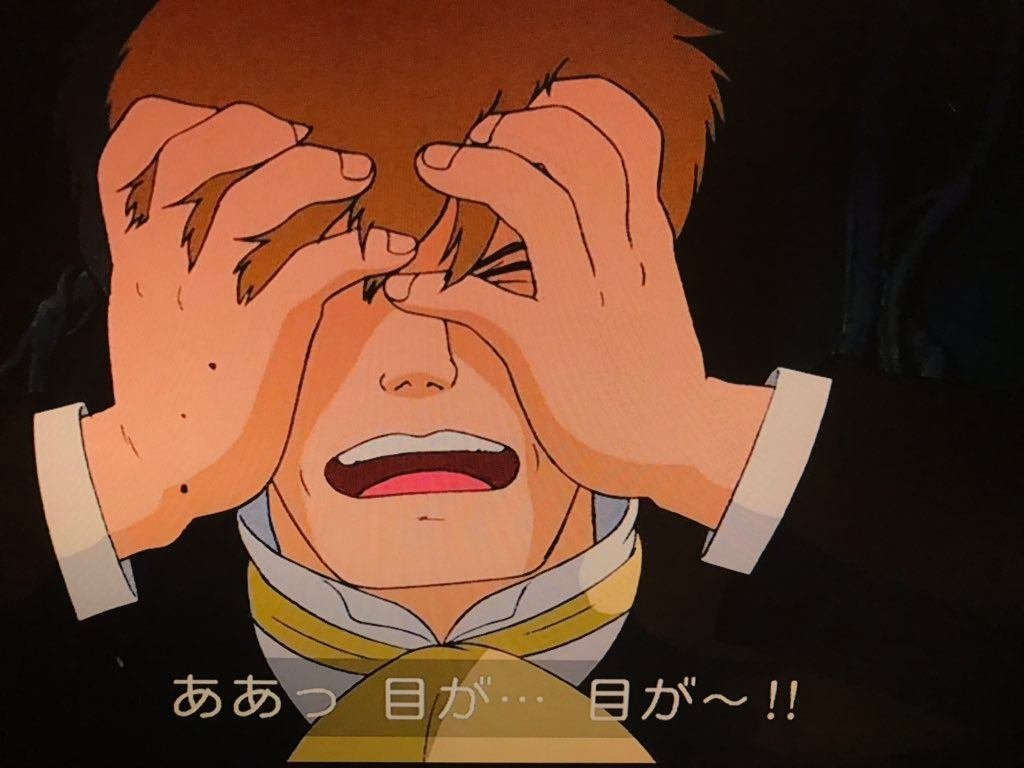
1層目はリムの高さに合わせて削っていきます。まず、リューターとデザインナイフで大まかに削ります。そのあとタイヤセッターに取り付けて削っていきます。切削する道具は汐見板金から出ている誉ヤスリ加工アーム EXを使用しています。
2層目を被せて削るのですが、このときにリム側を少しはみ出した状態でくっつけます。
リム側はリューターで揃えていき、面側はタイヤセッターで仕上げていきます。最終的にはインナーが33.5mmくらいになるように削っていきます。
次にアウターを取り付けて(2層目と同じ感じで)35.5mmくらいまで粗削りします。そのあとタイヤ幅をここで決めます。自分は大体接地面が2.0mmくらいで、形状は垂直タイプです。
削ったら側面を接着剤で薄くコーティングしていき、強度をあげます。使用する接着剤はアロンアルファの耐衝撃用。
その後は、34.95mm近辺を狙って削っていきます。縮みタイヤなどはタイヤセッターで仕上げますが、シリコンタイヤだと綺麗に削れないので、ヤスリを使用します。使っているヤスリは、新潟県燕市製 プラスチックヤスリ ~誉~ 細目を使用しています。
最後にシリコンタイヤ側面を軽く削りラウンド状にします。
【ホイール(タイヤ)バランス】
ザックリ言うと重さが偏っているタイヤの軽いところにタミヤテープを貼って綺麗に回転するようにしていきます。
重さが偏っているとタイヤの回転が速くなるほど遠心力が強くなり振動が発生して細かくピョンピョン跳ねてるような走りをします。
グワングワンって回ってませんか?
大事なのは回転の止まり方です。
回転が右〜、左〜、右、左...で止まりましたか?
回転が遅くなったあたりから重さの偏ってる雰囲気を感じられると思います。
この時点でタイヤの上になった部分、ここが一番軽いところです(軽点)
ここにマーキングします。この時点でどのぐらい偏っているかわからないので適当にマルチテープ(重り)を軽点のリムへ貼りつけます。
【バランスがとれたか見極めるポイント】
・マーキングが一番上だけではなく毎回停止する位置が違う
・停止するとき僅かに逆方向へ回る
このへんの感覚はやっていくうちになんとなく掴めると思います。
マーキングした部分が一番上に来ていなくても停止する位置が毎回同じ場合は、重りの貼りかたで軽点が移動しただけなので貼り直すか移動した軽点へ追加で重りを貼ってください。
バランスのとれたタイヤをマシンに装着してスイッチを入れてみると作業前より手に伝わってくる振動が弱くなっているのを実感できると思います!(プラシーボ効果大)
ホイールを選別してタイヤを作るのとは違ったアプローチでタイヤが綺麗に回るようにする作業なのでコレが正解というわけではありません。
重りを追加するのでタイヤの軽さを重視した場合には不向きだと思います。
自分が使っているホイールバランサーはえのもとサーキットの奴に620を装着したものになります。
【干しタイヤの作り方】
縮みタイヤと干しタイヤを比べると干しタイヤのほうが滑るような気がするので(個人の感想です)、殺菌灯で縮みタイヤを干していきます。
※殺菌灯の光は非常に眼に悪いもので絶対に直視及び間接的に視ないでください。
まず、アルミテープをタイヤサイズにカットしていきます。使っている道具はオルファから出ているコンパスカッターです。
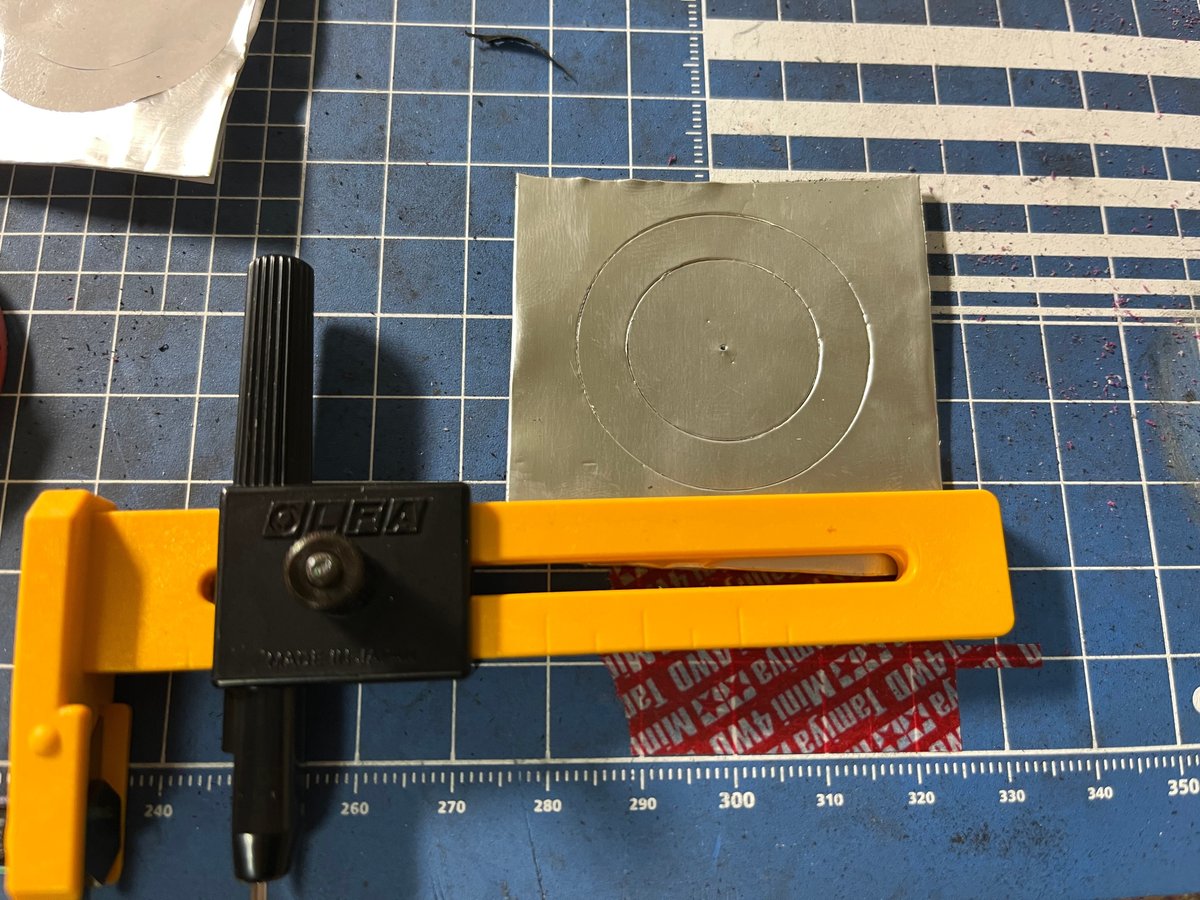
カットしたアルミテープをタイヤに貼り付けていきます。
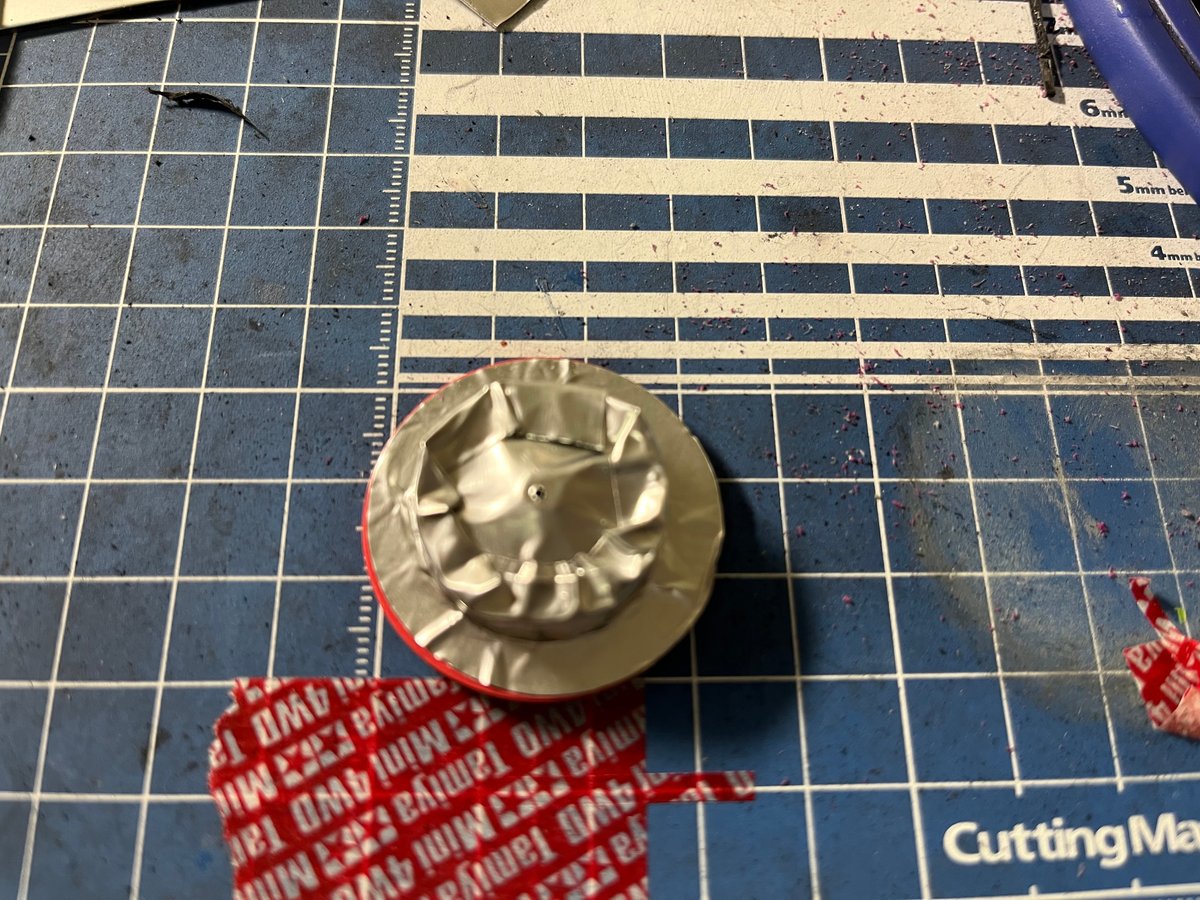
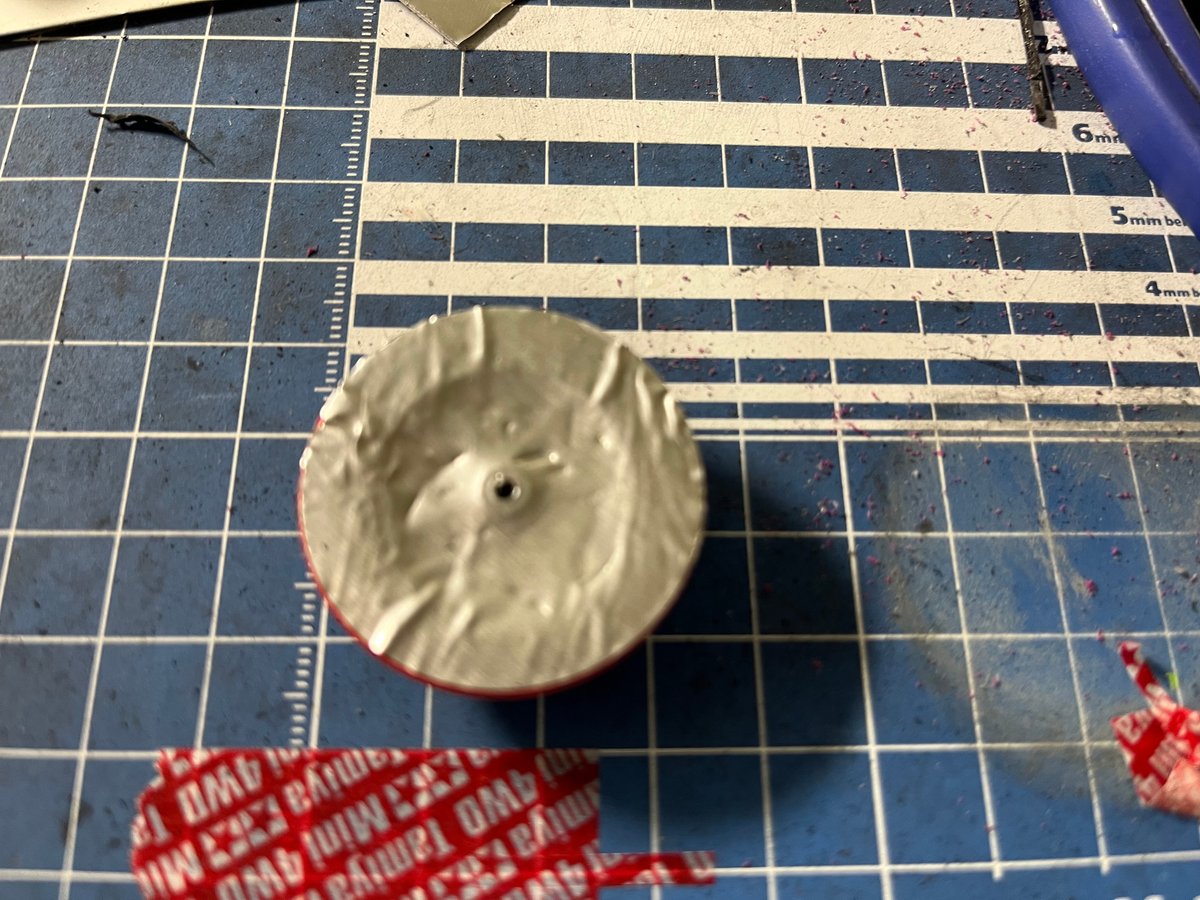
後はダミー電池を入れてお好みのグリップになるまで干します。
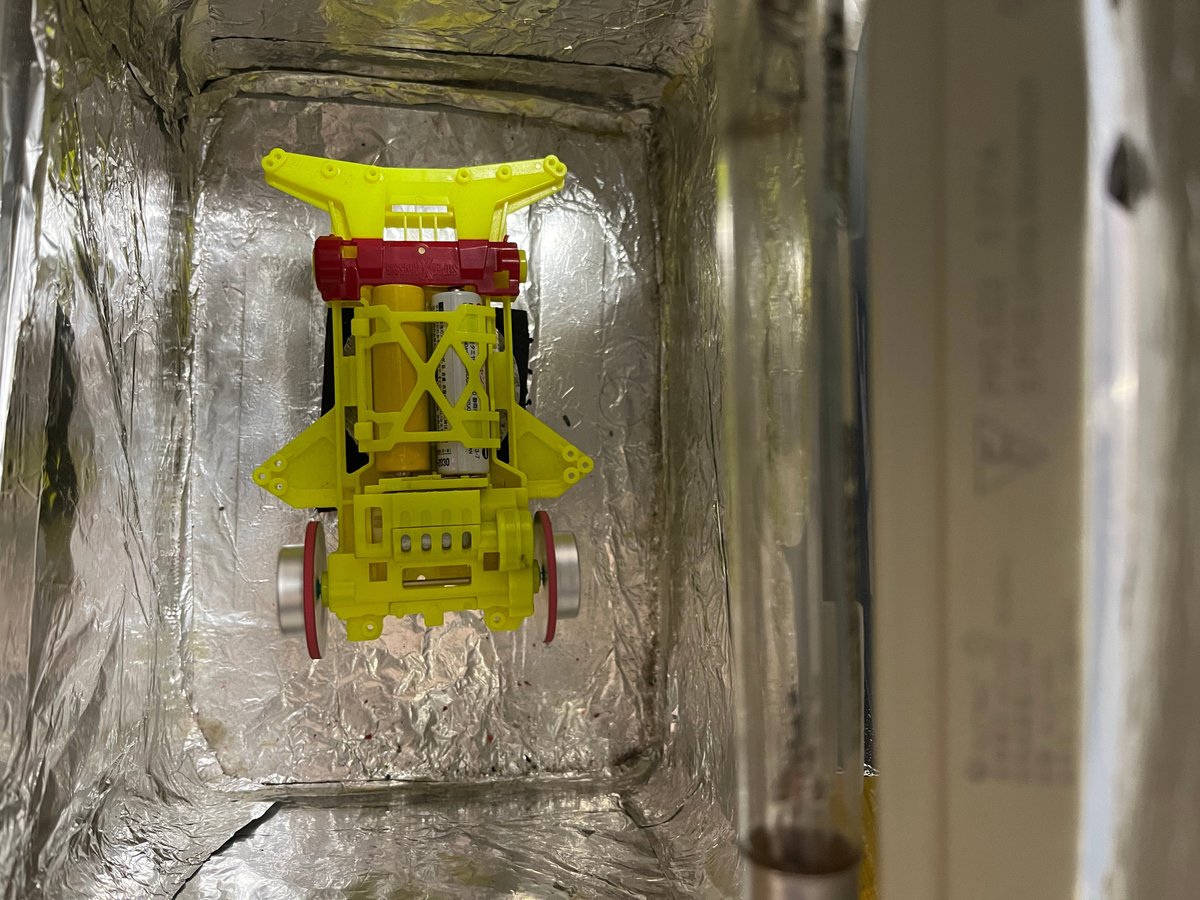
この記事が気に入ったらサポートをしてみませんか?