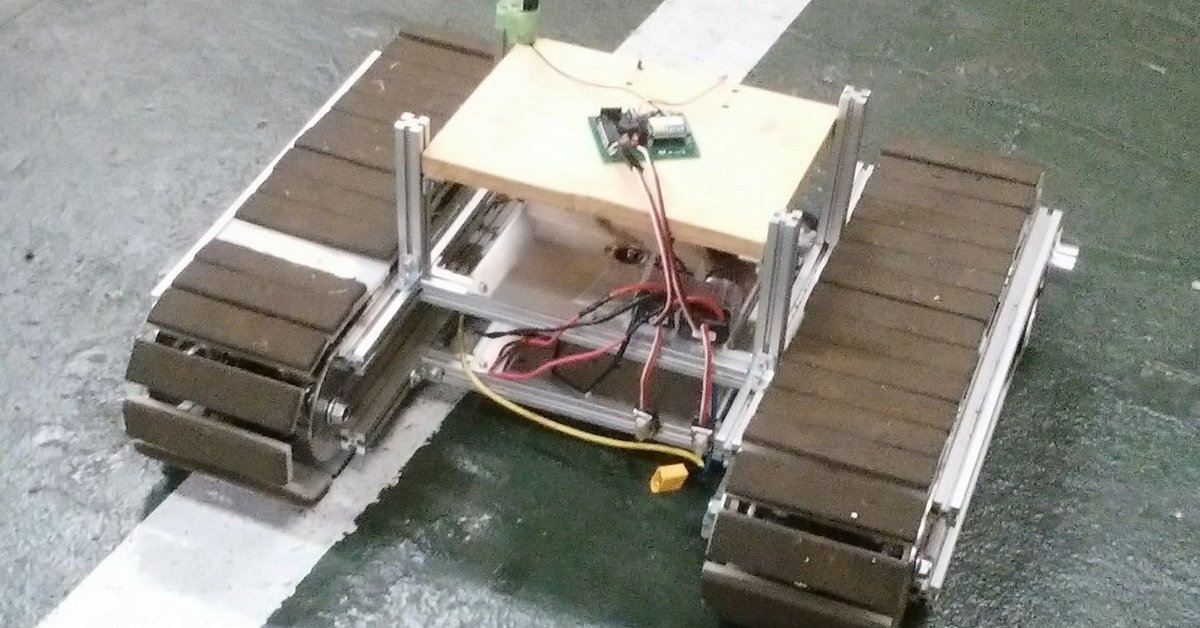
CuGoの開発に至るまでの経験 ~大学への進学とベンチャー修行編~
本記事では汎用クローラユニット「CuBase」に関する開発に至るまでの経験について記載する.ここでは下記の高専での経験に引き続き大学進学後の開発とベンチャーでの修行について記載する.いよいよこの記事でCuBaseの原型ができあがるところまで話がすすむ.
※クローラユニットの呼称が2020年10月よりCuBaseからCuGoに名称変更しています
私は2014年に長岡技術科学大学に進学した.大学でも引き続きクローラ関連の研究開発がしたく長岡技術科学大学の工作センターの使用願いを出したが研究室の許認可及び研究費からの費用の捻出がないと利用できないとの打診を頂くことになった。そこで私が所属していた長岡技術科学大学のロボコンプロジェクトの工作設備を利用してクローラロボットの開発を継続することにした.
このときは2014年9月にあった長岡技術科学大学の技大祭に間に合わせることを念頭において開発を行い,なんとか無事技大祭にまにあわせることができた.この場をかりて手伝ってくれたロボコンプロジェクトのみんなに感謝をのべたい.下記の映像は長岡技術科学大学の放送技術研究会に所属する友人に協力してもらって作成したCubo ver2の紹介映像である.製作の過程もあるのでぜひクローラロボットを開発したい方は参考にしてほしい
また2015年8月には東京ビッグサイトで開催されたメイカーフェア東京に島風技研の名前で出展し,下記の輪投げを行った.
大学の4年では今後のものづくりの拠点として学外にあるものづくり総合支援施設「匠の駅」の設立と運営も開始した.2015年8月以降はこちらでの活動を主軸にすえて行っていった.
http://takumi-no-eki.rgr.jp/blog/
匠の駅の記事は準備中
大学の4年の7月にリバネスのテックプランターに出場しそれの縁で株式会社ホープフィールドに研究員及び技術員として参加することになった.また同じ2016年10月から長岡技大の実務訓練もはじまった.これらの詳細については下記の大学時代をみてほしい.
11月ごろ匠の駅での工作環境の構築を実施しながらホープフィールドでの活動とOM製作所での実務訓練を行った.ぶっちゃけ色々やりすぎだとは思ったが割と夢中になってやれてて楽しかったように感じる.
新しく買ったCNCフライスのセッティング中 pic.twitter.com/jicTKAoDV8
— 寺嶋瑞仁 @南千住 (@simakaze01) November 8, 2015
ホープフィールドに所属してから東京農工大学から問い合わせがありクローラ型の小型草刈り機を作って欲しいとの要望があった.一例としてはみかん農家でのバイトなど
そこで私がその仕事を担当することになった.これまでバイト的なので仕事を行うことはあったがプロジェクト単位で自分がこれまで学んできた工学分野における知見をもちいて仕事をするのはこれが初めてである.寺嶋としては自分の技術が通用するのかどうか分からずかなり不安と期待でドッキドキだったのを覚えている.
東京でのホープフィールドのメンバー及び農工大学教授との打ち合わせを終え仕事に取り掛かった.幸いこれまでで十分に匠の駅が今回の開発に耐えれる水準まで施設の稼働レベルがあがっていたので一部の部品製作を除いて問題なくとりおこなえた.
今回のロボット開発では高速型のCubo ver2と比較した場合に動作や耐久面での信頼性,コストがなにより重要視され,反面速度や軽量化は重要視されなかった.なので耐久面やコスト面で不安視された僕の特許出願技術(当時)は採用を見送られた.下図がその技術内容である.詳細は下記の記事をみてほしい
かわりにアタッチメントチェーンを利用して耐久面で高い性能をもてるベルトで開発を実施することにした.
このFEIGO-D
— 寺嶋瑞仁 @南千住 (@simakaze01) January 23, 2016
FEIGO-D
っていうクローラ移動ロボットにつかわれてる接地パーツの入手先知ってる方居ましたら連絡お願いします
あなたの情報が島風技研の設計を救う。
因みに10年近く前のマシンです pic.twitter.com/kgPlkCumOo
そういったことから最終的な図面が完成した.コンセプトとしては
・確実な動作
・組み換え自由な汎用性
・可能な限り既存の機械部品での構築
が求められた.結果生まれたのが下記のものである.これまでのロボットや装置開発は機構部品は買って使うことはあっても車体のフレームや歯車系などはかなりの割合を削り出しのフルスクラッチでつくることが多かった.またそれ自体の製作工程を楽しんでいた.しかし今回は今後の再現性と開発時間の短縮という側面で既存部品を多く使うことを前提とした.今更ながら設計した図面を公開させてくれたホープフィールドの上司に感謝.
量産型キューボの設計図
— 寺嶋瑞仁 @南千住 (@simakaze01) February 1, 2016
会社から掲載許可を頂いたのでここに張り付けときます
前回と比べかなり汎用性がたかくなってます pic.twitter.com/TKlRIZfQ1q
下図は履帯の間にはいる草刈り部である.
そうして完成した設計図をもとにクローラロボットを作成していくことになった.色々問題はありつつも大学の仲間と一緒に作業してなんとか完成にこぎつけることができた.
黒染め楽しい
— 寺嶋瑞仁 @南千住 (@simakaze01) February 23, 2016
色がドンドン黒くなっていく 最初かなり不思議に思った。
てかそれよりもなぜ 匠の駅には黒染めセットまで完備なんでしょう
いや超有り難いんですけどね pic.twitter.com/8GFeR6Rcyz
うおーーーーーーーーーーーー!!!!
— 寺嶋瑞仁 @南千住 (@simakaze01) February 24, 2016
ついに ついに 夢にまで見た・・・・(企業秘密につき消去されました)ができた
これはクローラ業界に扇風を巻き起こすぞ
つか つぶやけないのが辛すぎる
俺のこの熱い想いをどこにぶつければいいんだ
取り敢えず会社のタイムラインを埋めよ
そうしてできたのが下記のモジュールとクローラロボットである.
今回,希望するスペックのものを実現するためにミスミやモノタロウ,アリエクスプレスなどの機械部品を取り扱っているネットショップをこれまでの人生で最も使い倒してマシンの開発を行った.その過程で必要な部品をみつけるための学びを多くえることができた.
またこれまでの部品の加工を外注することは経験したことがなかったがホープフィールドやリバネスと縁が深い浜野製作所にてステンレス材の板金部品を発注するなど部品を外注するということをはじめて経験できた.3DCADが製造企業側でも実装されて極論3Dの部品データを渡していくらかの情報を補足するだけで部品の発注が可能なのはほんとうに便利である.
また既存部品を購入して使うことと外注企業に部品の加工をお願いして作ってもらった部品を比較してわかったこととしていかにオリジナルの部品が高いかを痛烈に実感することができた.機械部品とフレーム部品とでは役割がことなるので正確に比べることはできないが桁が一つまたは二つ違うコスト感である.こういったコスト感覚についても学べたのは大きかった.
そういった学びを経て.開発業務と実務訓練を終え匠の駅の開発環境を一旦とりはらった.素晴らしい開発環境を提供してくれた匠の駅と同施設の会長にはとても感謝をしている.
よおし 開発業務と実務訓練が終わったので 一気に掃除おわらした
— 寺嶋瑞仁 @南千住 (@simakaze01) February 29, 2016
ビフォーは色々載せれないものであふれかえってるので掲載できず
1ヶ月半ほど匠の駅の一室(最高の立地&環境)借り切り状態でもうしわけなかったっす pic.twitter.com/M3B0kxQP3N
以上の内容が
汎用クローラユニットCuBaseの開発に関わる大学とベンチャー企業での修行の経験である.現在株式会社CuboRexが販売しているCuBaseのコンセプトや形状をみてもらえばわかると思うがこのときに基本的な開発過程の約8~9割は完了していたため製品化を迅速に行えた.
今後も「ほしい者が欲しい物を生み出し試せる社会の実現」にむけ道なき未知を切り拓いていく
著者ツイッター
この記事が気に入ったらサポートをしてみませんか?