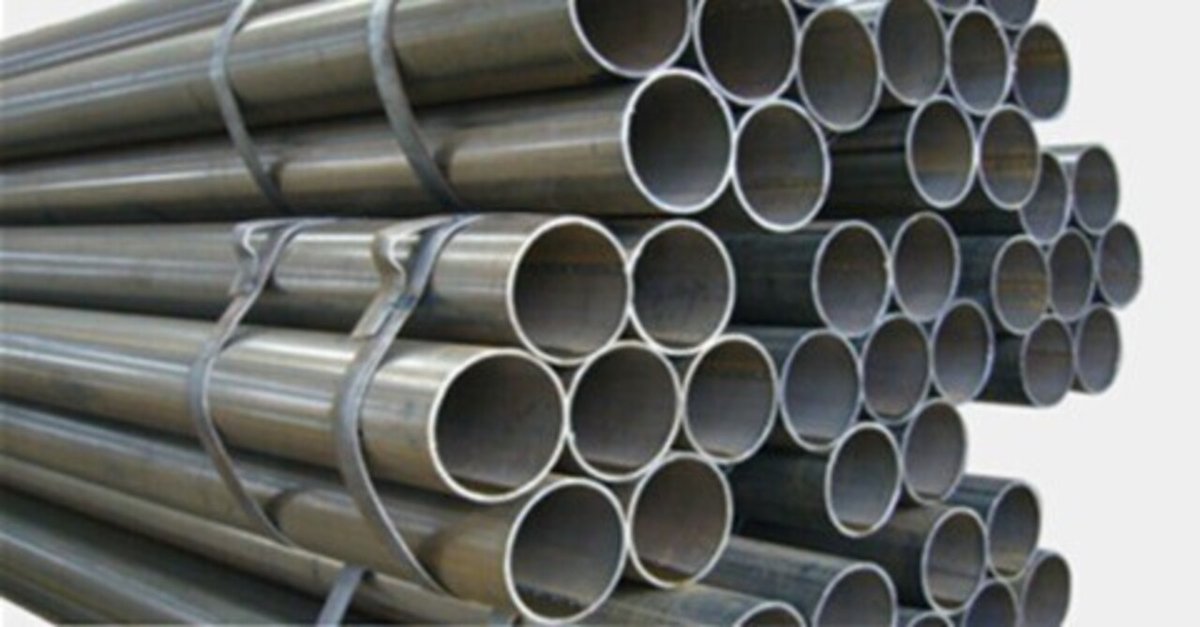
4 Ways To Test the Quality of Longitudinal Welded Pipes
When it comes to longitudinal welded steel pipes, many people are deeply impressed by their broad selection and relatively low cost. And these factors also contribute to its booming market and sufficient supply of goods. However, when faced with a mass of longitudinal welding pipes, whether we are sellers or buyers, we are all worried about one problem – product quality.
Then, how to test the quality of longitudinal welded steel pipes?
Generally, there are many methods for quality inspection of straight seam welded pipes. Among them, physically inspecting is the most commonly used in the market, measuring or testing by using some physical phenomena. It is also called non-destructive testing, which inspects the internal defects or materials of longitudinally welded pipes. The current non-destructive testing includes:
1. Magnetic Inspection
Magnetic inspection is to use the magnetic flux leakage, which is produced by the magnetic field magnetization of ferromagnetic longitudinally welded pipes, to find defects.
It is a simple testing way that can only find defects on the surface and near-surface of longitudinal welded pipes. Moreover, this way only does quantitative analysis of defects, and the nature and depth of those defects need to be estimated based on experience.
According to the different methods of measuring magnetic flux leakage, it is generally divided into magnetic powder method, magnetic induction method, and magnetic recording method. Among them, the magnetic powder method is the most widely used.
2. Penetrating Inspection
Penetration inspection uses the permeability of certain liquids to find and display defects, including color inspection and fluorescent inspection. It can be used to inspect the defects on the surface of ferromagnetic and non-ferromagnetic materials.
3. Radiographic Inspection
Radiographic flaw detection is a method that uses the properties of ray penetrating substances and attenuation in substances to find defects. It is mainly used to inspect the cracks, incomplete penetration, pores, slag inclusions, and other defects in the welding of longitudinal welded pipes.
According to the different rays used in flaw detection, it can be divided into X-ray flaw detection, γ-ray flaw detection, and high-energy ray flaw detection. Besides, due to the different methods of displaying defects, each type of radiographic inspection is divided into ionization method, fluorescent screen observation method, photographic method, and industrial television method.
4. Ultrasonic Inspection
It is known that when the ultrasonic waves are propagated in metals and other homogeneous media, they can be reflected at the interface of different media. Similarly, this idea can be applied to testing steel piping for the inspection of its internal defects.
Usually, ultrasonic can inspect the defects of any welded material in any part and can find the defect location more sensitively. But it is difficult to determine the nature, shape, and size of the defect. So ultrasonic flaw detection is often used in conjunction with a radiographic inspection to test longitudinal welded pipes.
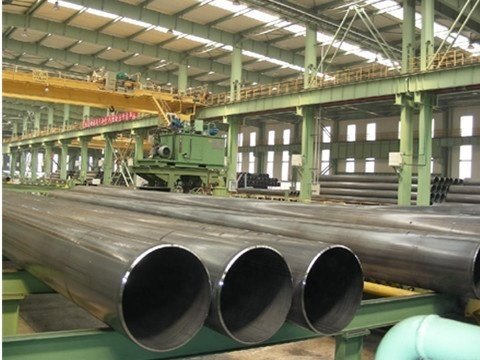
In any way, the longitudinal welded pipe is a very cost-effective solution to many large projects like water supplying, gas & fluid conveying, structure applying, and so on. Therefore, Before using them, product quality inspection is a problem that we all cannot ignore. And when buying, remember to choose a reliable supplier who has strict product quality inspection, for example, Wanzhi Steel.
For more details about longitudinal welded pipe: you can see: spiral welded pipe vs longitudinal welded pipe.
この記事が気に入ったらサポートをしてみませんか?