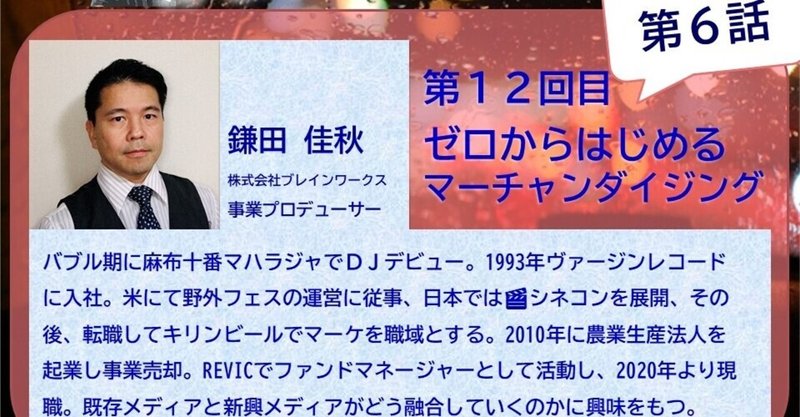
第12回「ゼロからはじめるマーチャンダイジング」第6話
さて、第12回「かまちゃんねる」を始めたいと思います。今回はゼロからはじめるマーチャンダイジング第6話で、このシリーズもいよいよラストとなります。
前回に予告していたように、このシリーズのラストは、タクト数について必要数で決める理由を解説します。後半では総括してアグリハックの導入事例などを紹介していきたいと思います。
その前に、このシリーズを振り返っておきたいと思います。シリーズの最初は農産物流通において、取引最小化の原理というマーケティング理論を用いて仲卸の果たす役割や、マーケティングにおける定義を農業に対して、どのように移転していくか解説させていただきました。
これは日本が誇れる食品流通システムですし、食品ロスにも一定の寄与していることから仲卸不要論などと、ここ数十年程ささやかれていますが、なくなるどころか、ますます、その存在感を浮き彫りにしています。
また、アメリカでインダストリー・エンジニアリング理論が生まれて、生産性の向上へのあくなき欲求が高まって、これを応用したのがトヨタのカンバン方式でした。日本独自の商習慣や文化に合わせて、世界でも生産性向上へのお手本ともなりました。
これを農業にフィットさせたアグリハックの紹介では、ジャストインタイムの考え方を中心にお届けしながら、後工程が必要になったものを前工程へ指示することによって、保冷設備などの倉庫は要らないという話をさせていただきました。
そして生産活動の中で、ロスが起こる構造を明らかにしたうえで、具体的にどのような対策をするのかについて提案させていただきました。
今回はその対策についてノウハウを移転するために、さらに実際に使用した資料などを掲示しながら話を進めていきます。
生産性を上げていくためには全体最適化を考えないといけないわけですが、アグリハックの対象範囲について解説して、受注から出荷までのプロセスを分解しました。そして段階的に、どのようにアグリハックを適用するのかについて論じました。
結果的には、出荷までがアグリハックの適応範囲で、販売店に荷物が着いた時点で責任が移転すると考えるわけです。このあたり輸出入の仕事をされたことがある方にはインコタームズと呼ばれる貿易条件と照らし合わせて考えれば理解が早いと思います。
そういたことで得られるメリットがこのように、アグリハックを導入すると多品種少量の生産でも、生産能力を高めることで、一見効率がよさそうな大ロットで大雑把に処理するよりも収益性をあげて、付加価値を生み出せるということを説明しました。
また商品を大雑把に作るって結局、生産工程を突き詰めないですし、課題感そのものがありません。だから勝手な閾値を設けて、ついつい作りすぎて食品ロスを生んでいるという側面も無視できないですね。
そこで出荷規格ごとに農作物を選別する手間を考えて、そもそも加工品用途の作物を作った場合のメリットや事例の紹介や農産物の出荷のポートフォリオを描いて、さらに収益構造にインパクトを与えるアグリハックもご紹介してきたところでございます。
しかし、加工用農産物の栽培となると基本的には、経営農地拡大となる傾向があるわけですけども、そうなると次の課題が「雇用」になります。そこで食品加工によって雇用の平準化を図る方法や、これとは逆に食品加工に乗り出さずに経営農地の拡大によって管理農地を増やしながらも雇用の平準化を実現した事例もご紹介させていただきました。
具体的には水稲栽培における直接、農地にモミをまく直播という方法で、省力化を実現させる方法を解説してきました。移植栽培と組み合わせることで機械の年間稼働率を向上させることもできますし、農地の拡大も容易になるので是非、取り組んでいただきたい栽培方法となっております。
投資に関しても管理農地が飛び地であれば移動のためにユニック車の導入程度で周辺分野で資金需要はありませんので取り組みやすいのも大きなメリットだと思います。
そもそも水稲栽培における課題というのは、農業就業人口の減少や、高齢化などを背景とした労働力不足が大きな課題になっていますし、だったらということで、こうした取り組みによって、どんどん管理農地を増やすとコストメリットを創出できることをお伝えしました。
また、ご視聴いただいた方からの質問に答える形で、同期化によってリードタイムの短縮や在庫削減する方法についても具体的な事例を挙げながら、ご紹介させていただきました。
このように1個流しを実現させることによって、生産の同期化とその必要性については工程を流れるように配置して、生産工程を徹底的に短縮することがジャストインタイムの考え方の軸になる基本的構想の1つになっていることがお判りいただけたと思います。
そのために、いろいろな設備を操作可能にするよう作業訓練が出来てないといけないわけで、多工程待ちのできる多能工を育てるためには、それなりの教育について、ジョブローテーションを取り入れて、各作業者を順次移動させて、どのような仕事でもこなせるように訓練する方法について、作業訓練票を用いて説明させていただきました。
その結果、QCDにおける問題意識向上と改善提案の増加につなげるために工程間の仕掛けをなくして、工程の流れ化を実現するためには工程順に設備を配置し1個流しを徹底することが、結果としてリードタイム短縮につながっていたという結論でした。
さらに作業者の無駄な動きや動線を排除して、出荷までに必要な設備を加工順にU字型に並べて、初回工程と最終工程を近づけるようにすることで効率化を図る方法を紹介しました。
そこで今回の本題に移るわけですが、取引先へジャストインタイムに納品するために重要な基本的な考え方は、これまでの「かまちゃんねる」でお伝えしてきた、工程の流れ化と、今回、お話しする「必要数でタクト決めする」ということになります。
そして、もう1つが、後ほど説明しますけども、「後工程の引き取り」になります。
タクトタイムの物流では、お客様の要求した時にタイミングよく商品を発送できれば、商品在庫を持たずに運用できますよね。
しかし、中には売れる速さにマッチング、つまり同期化させることが困難で、在庫を持った運用になる商品も1部にはあります。これまで保冷設備なんかは要らないよという話をしてきたわけですけども、これはコールドチェーンが整った日本だから運用できるテクニックなんです。
これが例えば、サツマイモだったらキュアリングという工程が必要で、一定の温度で保管しなければならないわけです。これはこれで、在庫を持つことで、農閑期でも売上を上げられる加工品のような立ち位置で運用できるので、キロ単価は安いんですけど、生産原価も安いのでお勧めの作物の一つです。
アグリハックでは、在庫を持たないジャストインタイム。つまり、必要な時に、必要なだけの生産を行うという話をしてきました。
例えば、野菜の包装ラインが3.6秒に1袋の封入をするときには、この野菜を袋詰めする袋も3.6秒に一枚ずつサプライすると同期化されるということになります。
つまり、工程の流れがスムーズに行くわけですよね。そこで各設備や工程で、色々な野菜が混在して流れるラインのタクトタイムをここに表した式に基づいて決定します。
ここでのポイントは、タクトタイムはお客様が決めるものであって、タクトタイムは日々変化するということだけ、ここでは覚えておいて頂ければいいかなと思います。
標準作業といったところでは、その日の生産必要量が決まると、決まった作業手順で訓練された作業者が、安定した生産を行うことが必要になってきます。
そこでアグリハックでは、無駄がない作業方法で効率的な生産を行うために誰もが同じようにできるロールモデルというものを作成しておりまして、これを「一般化」と言っているわけですね。
一般化の3要素として、タクトタイム、作業順序、標準手持ちの、この3つを決められた工程で、必ず作成するようにしているんですね。
この一般化はアグリハックの基本となるもので、一旦決めたらそのまま長期に変更しないというものではなくて、日々見直して改善点が見当たれば、その都度、柔軟に更新して作業者に教育訓練して行くと言うような、どんどん新しい人にも技術やナレッジを移転しているというようにしていきます。
ここでの標準作業とは、工程別能力票、標準作業組み合わせ票、標準作業表の3つの帳票を指していまして、標準表作業の作成とは、これらを作成するということなります。
そのためには、作業工程を充分に観察して、作業の順序や所要時間についての作業を分析して、ストップウォッチなどで時間を計測する必要があります。ここでは基本的な手順として時間の計測から述べたいと思います。
これは繰り返し作業を前提としていまして、まずは作業手順に沿って作業要素作業基本となる最小単位の作業を記入します。
そして、繰り返し作業を要素作業単位に通し時間を記入します。その際、最低10回は観測するといったようなことが必要だと思います。
次に、測定後の個別時間を記入します。こちらは、前の要素作業時間終了との差を記入していただければ良いです。
そして、個別時間の平均値を算出して、最後に標準作業組み合わせ表に個別作業の最も短い時間を使用します。
次に工程別能力表を説明します。こちらは作物別別能力表とも換言できるものとなっていまして、標準作業を作成するために工程順の各工程での名称ごとに能力を工程別能力表に記入するわけです。
それが、こちらになっていまして、この工程別能力表は標準作業を作成する時の為に必要なものであって、工程におけるネックになる箇所を探して、改善の手がかりを探すために重要なポイントになっています。
画面左側にワンサイクルという記述がありますけど、タクトとサイクルの違いについても説明しておきたいと思います。
タクトタイムとは、一般的に1つの製品の製造にかける時間のことで、このタクトタイムが短ければ短いほど、稼働時間に対して、より多くの商品を生産することができます。
タクトの語源はドイツ語でして、その意味は拍子や指揮棒ということなんですけども、まさに生産のリズムを決める大切な基準値となります。
一方で、サイクルタイムとは、1つの製品の工程開始から完了までの1サイクルに対して実際にかかる時間のことです。こちらは工程にかかる正味時間なので、余裕・損失を考慮しない場合の作業時間といえます。
ここに、それぞれの関係性を示しておりまして、タクトタイムとサイクルタイムは常に同期化できるように最大限の注意を払う必要があります。
それらを踏まえたうえで、標準作業を組み合わせ表の作成と活用といったところなんですが、これは工程別能力表で作成した作業手順と時間をベースに、標準作業を組み合わせ表を作成してタクトタイムを計算します。
この標準作業組み合わせ表は作業の時間的経過が図表で示されておりまして、ボトルネックになっている工程を見える化させることができます。
したがい改善の着眼点を容易に見つけることができるというわけです。プロジェクトリーダー、あるいは管理者は、この標準作業組み合わせ表を基に、実際にその時間通りに作業ができるか自らやってみて、問題の箇所が無いか確認するわけです。
それで問題がなければ、各作業者にタクトタイム内でできるまで技術移転します。要は訓練して教え込むというわけですね。
こういった施策によって、改善の優先度、つまり費用であるとか、その効果、あるいは難易度や改善ニーズなどを付け加えながら、改善していくんですけど、そのポイントは、まず改善ニーズの高い工程を徹底的に改善するということです。
2つ目が、設備の自動化といったところです。例えば自動送りであるとか、自動停止といったところになります。
そして3つ目が、ボトルネックになっている設備の高速化というところになります。
4つ目は、歩行時間の短縮ということになります。
標準作業表の作成と活用といったところなんですけど、こちらの標準作業票というのは、平面の簡易な機械配置を書き出してみて、そこに基本となる項目を書き入れて作業現場に掲示することで、作業者が正しく作業を行っているか確認するものになっています。
こちらの標準作業表の記入項目では、一つ目が設備あるいは工程別の作業順序となってまして、2つ目が標準手持ち数になっています。3つ目にタクトタイムがやってきまして、4つ目が、正味時間になります。5つ目には、品質チェック箇所があって、最後に安全注意箇所ということになります。
※ブレインナビオンでは、この記事の動画を無料でご視聴いただけます。
ここから先は
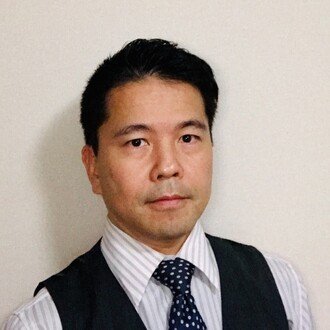
ブレインナビオン「かまちゃんねる」ここだけの話
株式会社ブレインワークスの運営するブレインナビオンで毎週火曜日11:00~11:30にお届けしている「かまちゃんねる」を中心にブレインナビ…
この記事が気に入ったらサポートをしてみませんか?