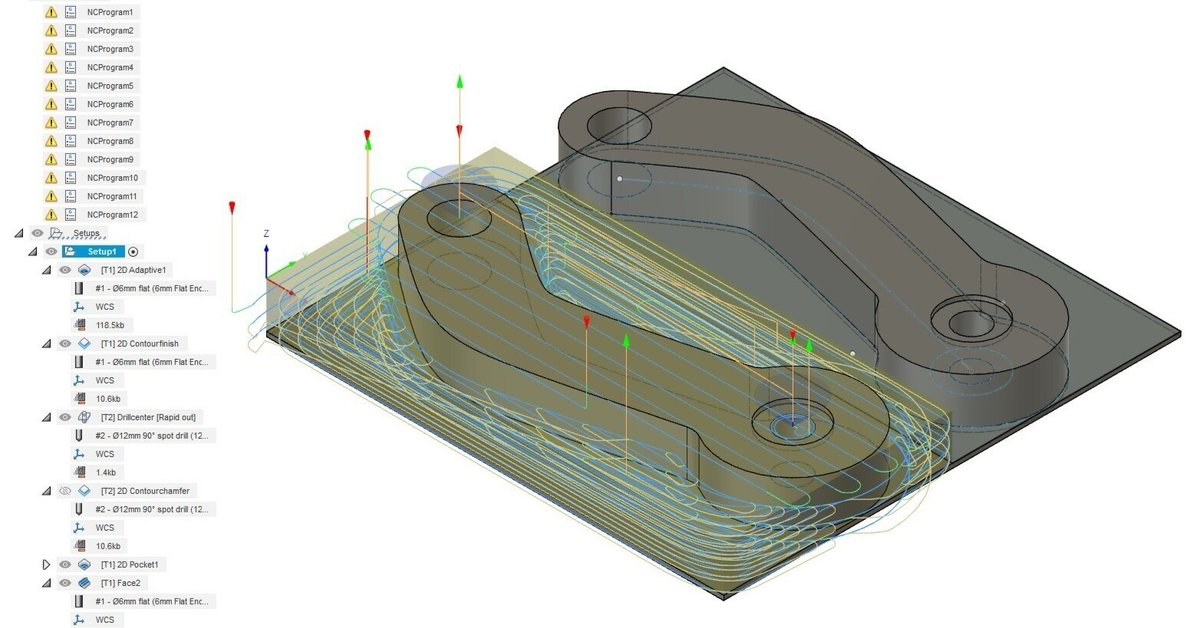
FUSION 360でのCAMを実践で使い方を習得する
バイクのミラーブラケットをつくりました。
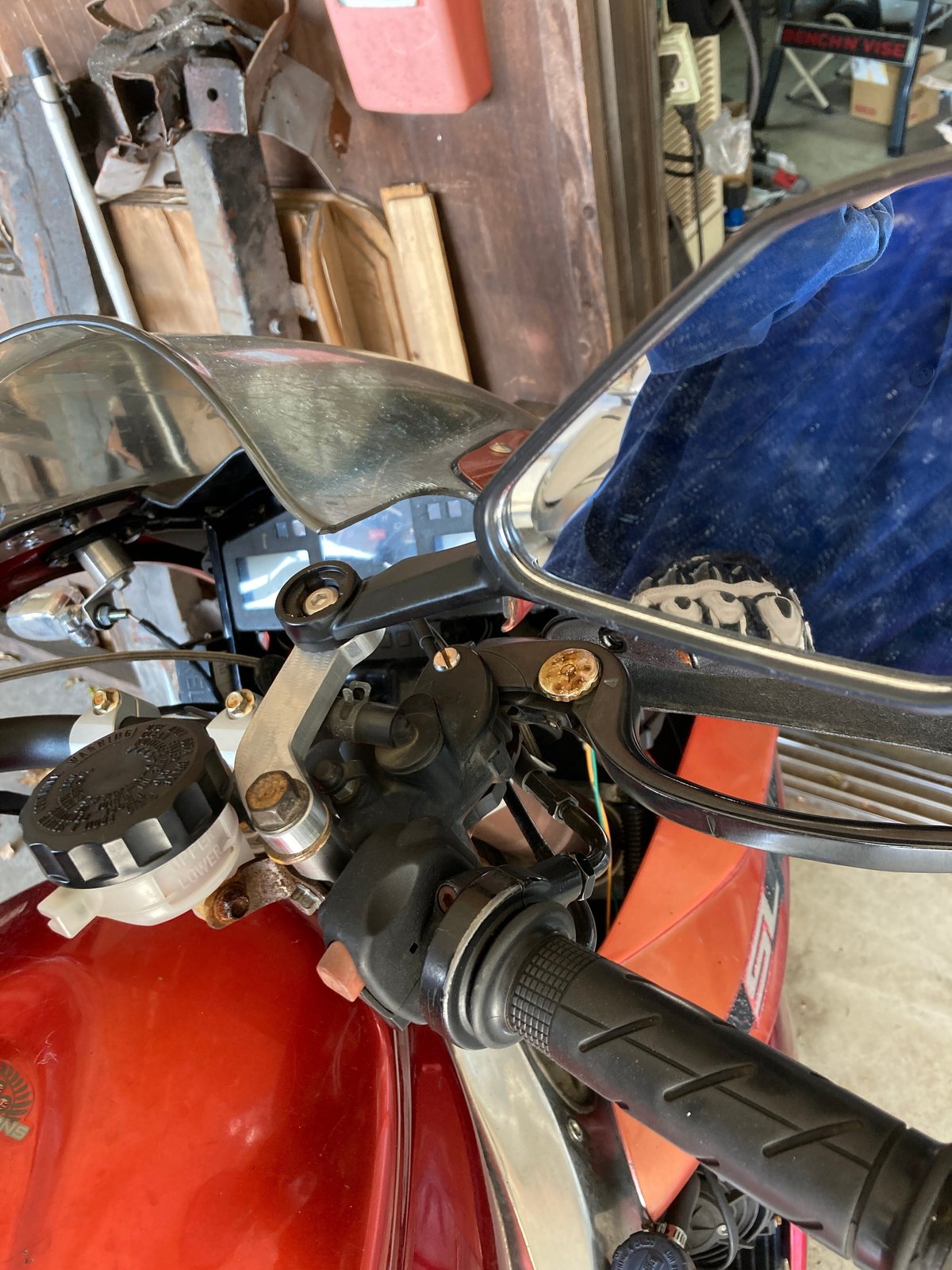
ツールパス生成のやり方は削ってみるとよくわかりました。負荷制御はほんとうまいこと計算していて、切削負荷が大きくなって主軸モーター回転数が落ちる現象がほとんどなかったです。
このサイズのミニフライスは6ミリエンドミルを12,000rpm回しつつ、送りモーターを手で回せない速度で回してざくざく削り落とすのが正解。大きなフライス盤のように12ミリより太いエンドミルでゴリゴリやるには総合的に剛性が不足しているし補強してもたかが知れています。回し加工するにも回転台を載せるとフトコロ高さが無くなりますし、主軸高速化とNC化で6ミリエンドミルで速・深削りするという一つの解にたどりつきました。現状では6000rpmしか回せてなくて、Vベルトプーリーからタイミングベルト一式に変更予定です。
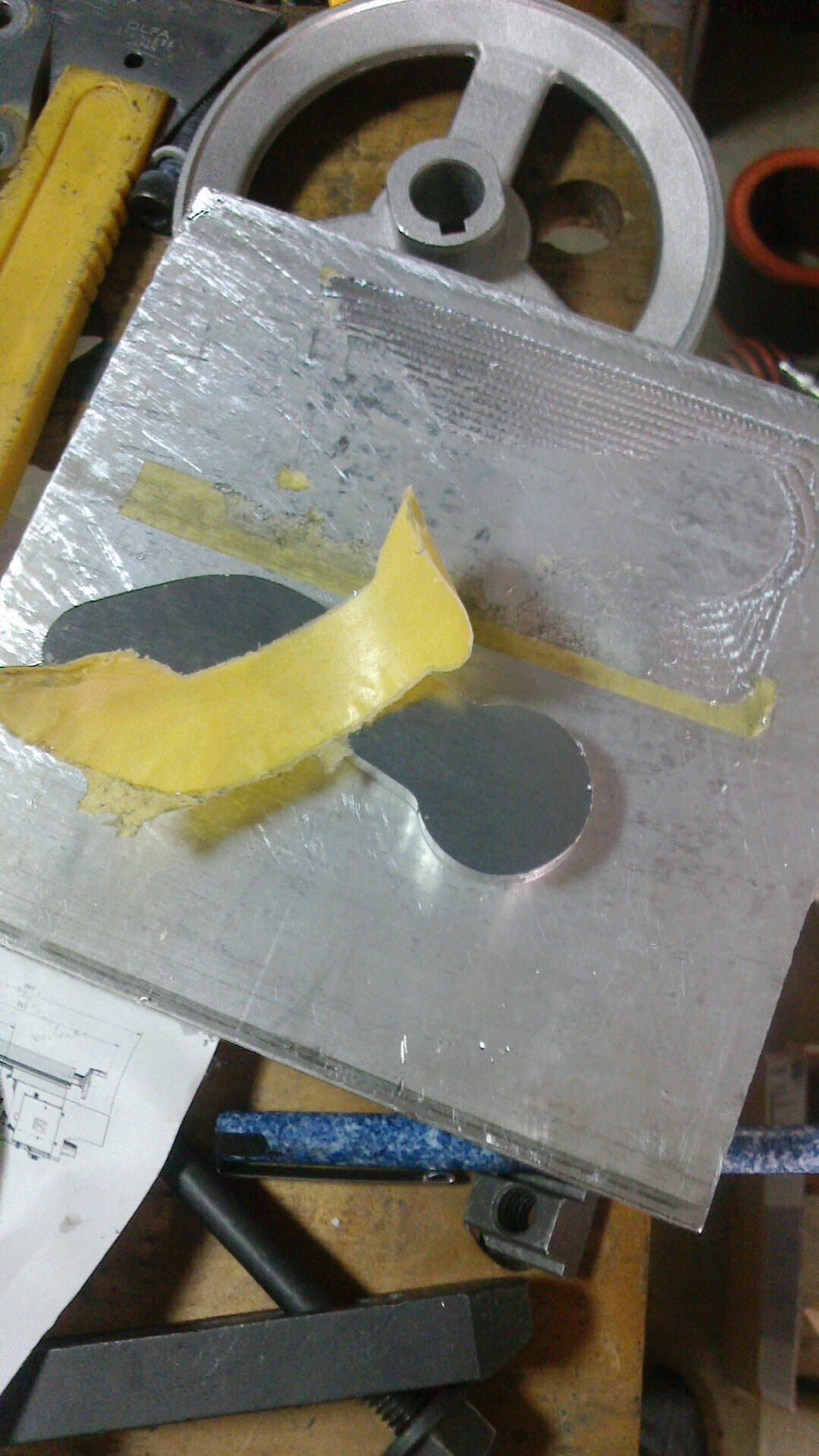
バイスに精密に咥える段取りをしなくてもワーク裏としっかりした捨て板とにマスキングテープを貼り、それを瞬間接着剤で貼るので十分な保持力がありました。加工熱が入りすぎるとズレやすいかもしれません。瞬間接着剤はマスキングテープ同士を接着しているだけなので切削が終わったあと簡単に剥がせます。
使ったのは耐衝撃瞬間接着剤です。特別なものでなくダイソーにあります。下の嵌めあい勘合用嫌気性接着剤は金属同士の直接なら強力な液体バイスとして使えますが、マスキングテープが介在するとまるで接着できませんでした。直接だと200度くらいに加熱しないと剥がれないから後始末が大変ですしね。
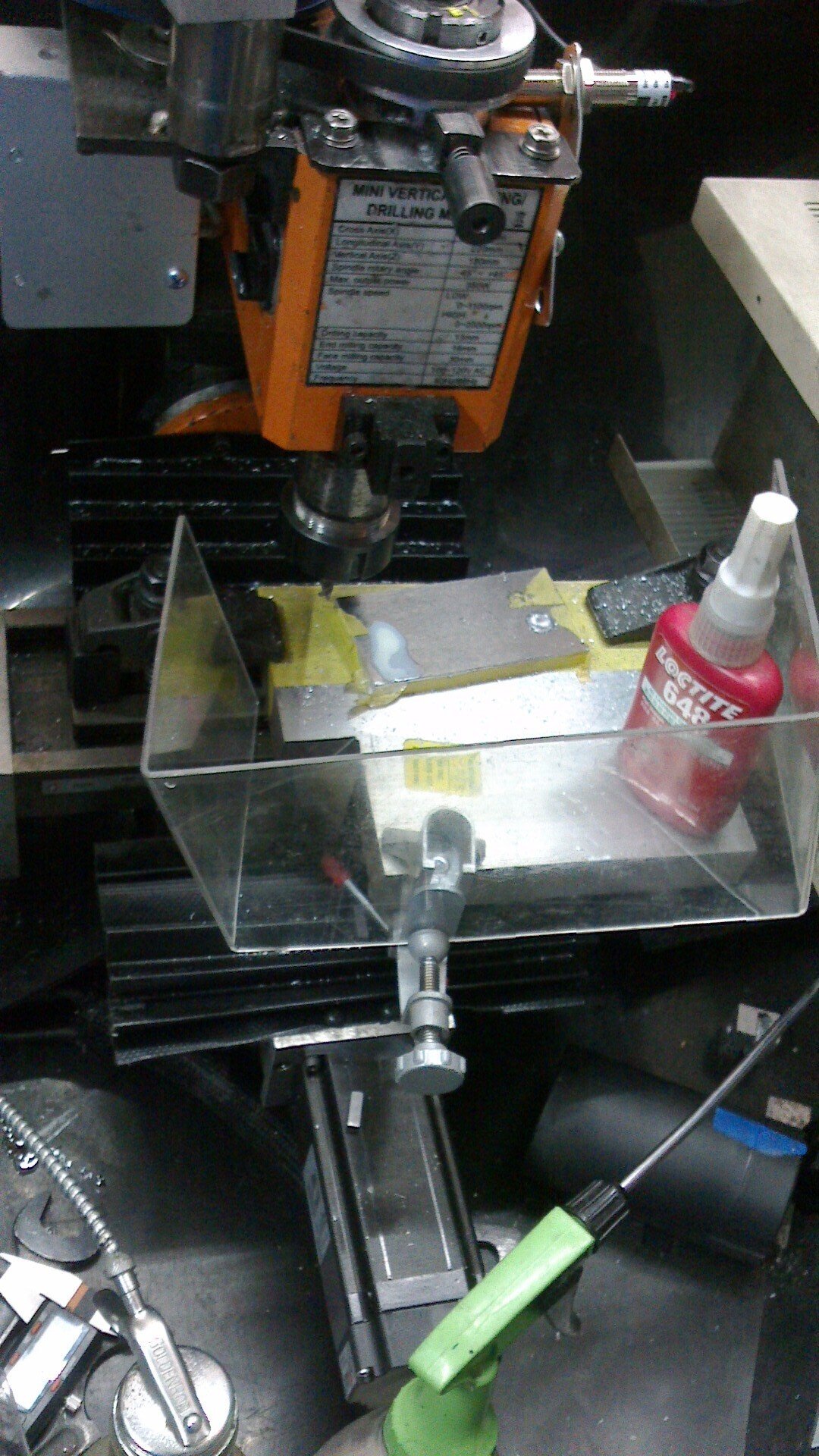
FUSION 360で生成したGコードをスタンドアローンCNCコントローラー(SMC5-5-N-N)で実行すると最初のところで停止してしまう件はコントローラーが受け付けないGコードをファイルから削除することで可能になりました。具体的にはツールオフセットや円弧切削の相対座標等でした。
まとめ
FUSION 360でのGコード生成にて2次元形状のアルミ合金ブラケットをミニフライスのブン回しで作りました。