【カーボンニュートラル推進企業紹介㉗】アスカ工業株式会社~真剣作業で削れるCO2~
カーボンニュートラル―。脱炭素への取り組みは国際レベルのものから個人での活動まで様々です。
厚木市内で脱炭素の取り組みを進めている企業に、どのように「脱炭素への挑戦」をしているかをインタビューしました。取り組み理由や具体的な進め方、これから取り組む企業へのメッセージなど、1社ずつご紹介します。取り組みを始める一歩に、また活動を促進させるヒントにしてはいかがでしょうか。
27社目は厚木市上依知のアスカ工業株式会社。作っているのは様々な「歯車」です。長年にわたり精密な歯車の製作を追求する地元の企業が、地道にCO2削減に取り組んでいます。社内での様子を加藤洋一郎社長に案内してもらいました。
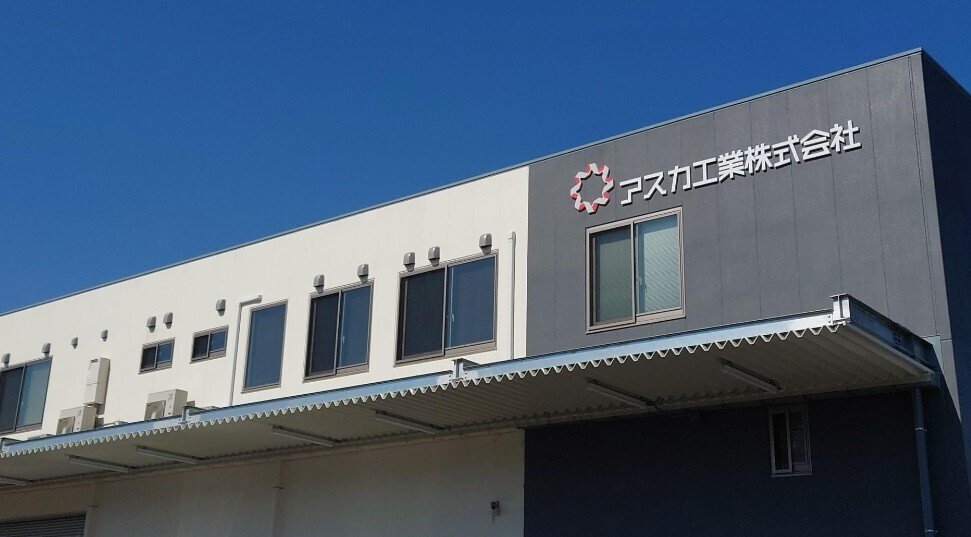
普段の暮らしで「歯車」に直接手に触れる機会は少ないでしょう。しかし実は同社が試作した製品の数々は、私たちの身近なものの内部で動き続け、暮らしを支えてくれているのです。クルマのトランスミッションもそのひとつ。さらにコピー機(複合機)の内部の歯車、ブルドーザーなど建設機械や、防衛車両の部品まで手掛けています。
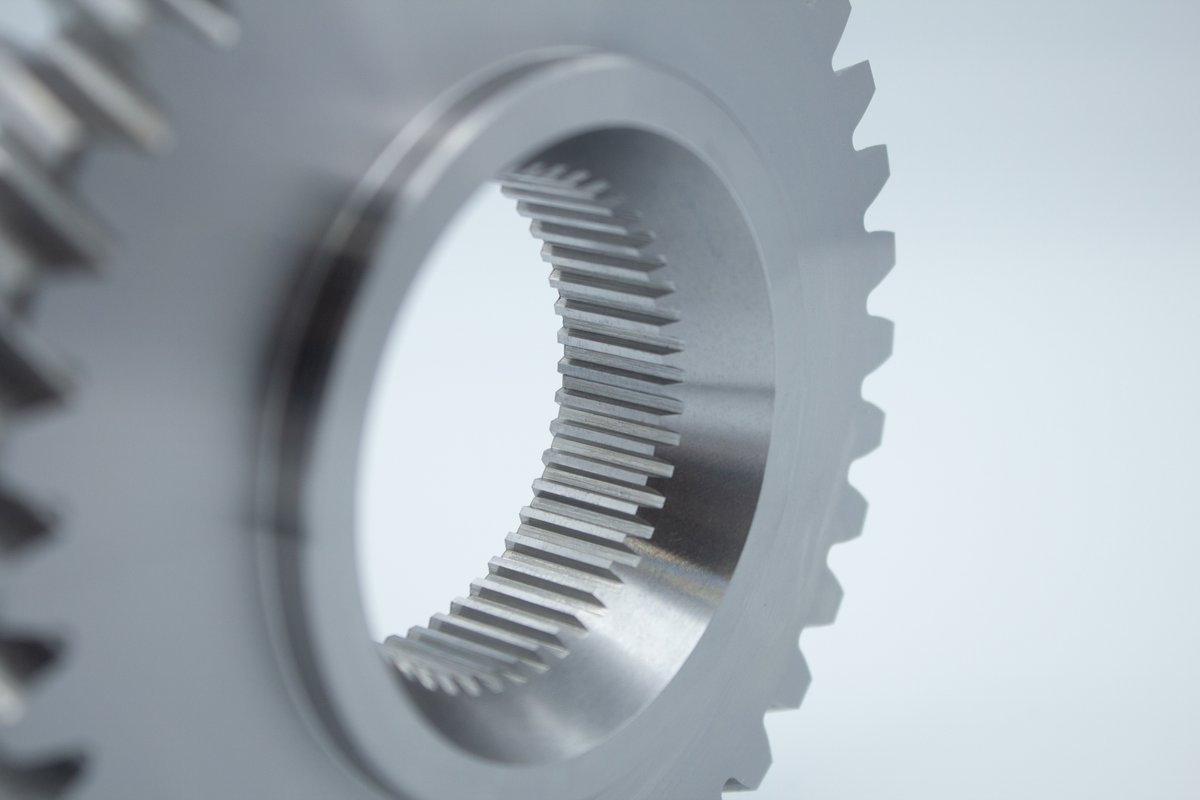
精密さを追求する同社は、コスト削減とCO2削減を兼ねて、2024年初旬に第3工場の屋根に太陽光発電を設置しました。年間で720,000円の電気代がかかっていましたが、太陽光パネルの設置により、月々の設備費用を差し引いた約480,000円に減らすことができました。現在第3工場で必要な電力はすべてまかなっている状況です(全てはまかなえていないので、削除)これからの目標は、さらに売電をして6000円ほどまで電気代を低減すること(これも現実的ではないので削除)。加藤社長は「この取り組みを見て、本社工場などにも太陽光が導入できるか検討したい」と見据えています。
同社は65年前の1959年に東京都大田区で創業、1984年に厚木市に工場を設立し、長年にわたり歯車を作り続けてきました。材料から製品まで一貫で生産でき、取引先から寄せられた図面通りに「試作開発品」を熟練の職人たちが作っています。歴史ある企業ながら、若手も多く明るい雰囲気。短い納期であっても柔軟に対応できるのが同社の強み。完成した品をもとに型が作られるなどして、大量生産されてゆくのです。
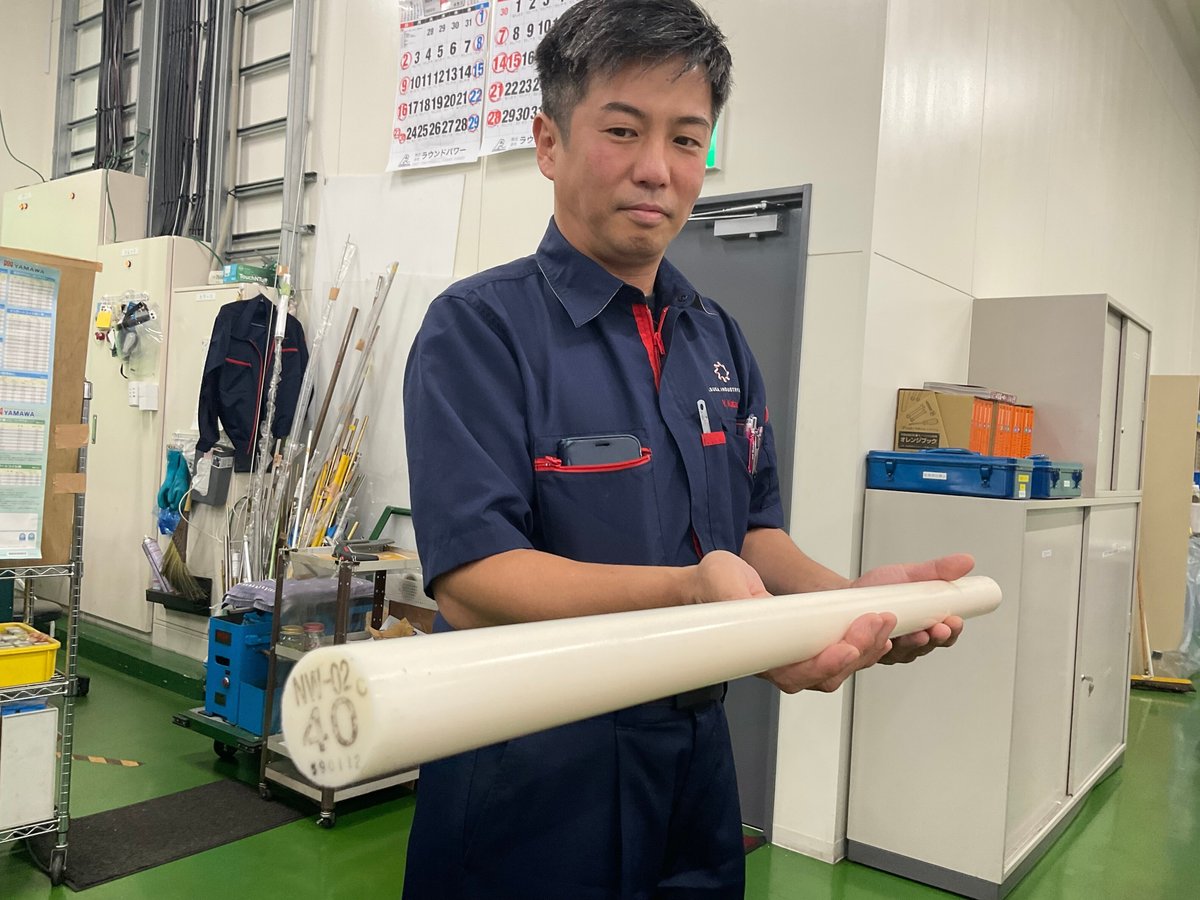
試作開発品の予備数を1つ減らす
品物を削る前には、極力ムダが出ないサイズの素材を選びます。大量生産に直結する重要な品ゆえに、従来はプラスチックの試作開発品については予備を3個作成していました。工程には旋盤やマシニング、歯切りなど複数の工程を経て歯車が生まれるのですが、工程が複数になる分、万が一の失敗を加味して複数が必要でした。
同社ではこれらの予備を従来の3個から2個に減らすことを決めました。同社では毎年約5000もの図面をもとに加工しているので、予備1個分の削減が年間では180000立方センチメートル分に及びます。その結果はCO2削減だけでなく、在庫管理が楽になるというメリットにもつながりました。もちろん予備を減らすぶん、失敗が許されない正確さが求められるわけで、まさに「社員が力を合わせてくれるおかげ」(加藤社長)と言えるでしょう。
無駄な工具を買わない、今手にしている道具を大切に使い続けるというのも、歴史ある同社の気風。たとえばマシニング工程で使われる超硬質の工具があります。これが摩耗して使えなくなっても廃棄はせずに、研いで別の機械の切削工具として活用しています。2020年に新築された工場はすべてLED照明となりました。ごみの分別も徹底し、ペットボトルのキャップから空き缶のプルタブまで分別するほどの徹底ぶり。もちろん金属などの「切り粉」も鉄や真鍮、銅などに分別して業者に引き取され、再生の道に向かいます。
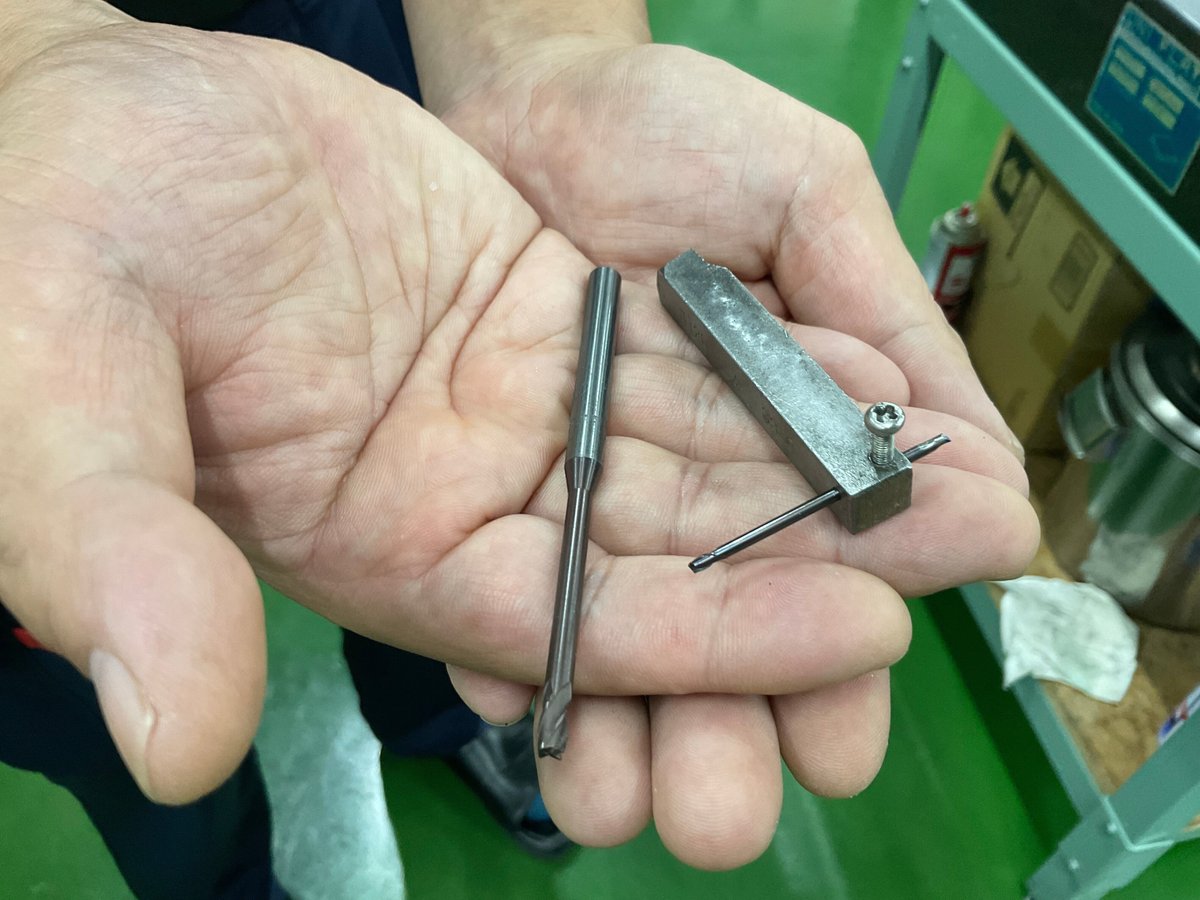
加藤社長は社用車も自家用車もハイブリッド。プライベートでは登山好きということもあり、環境への思いが深まったそう。もちろん、精密な製品を作るためには、機材を正常に動かす必要があり、相応の電力を使わねばなりません。たとえ電力がこれ以上減らせないとしても、別の側面からCO2削減はできるはず――切り口を探し続け、始めたら継続する。工場内を歩きながらそんな気風を感じました。
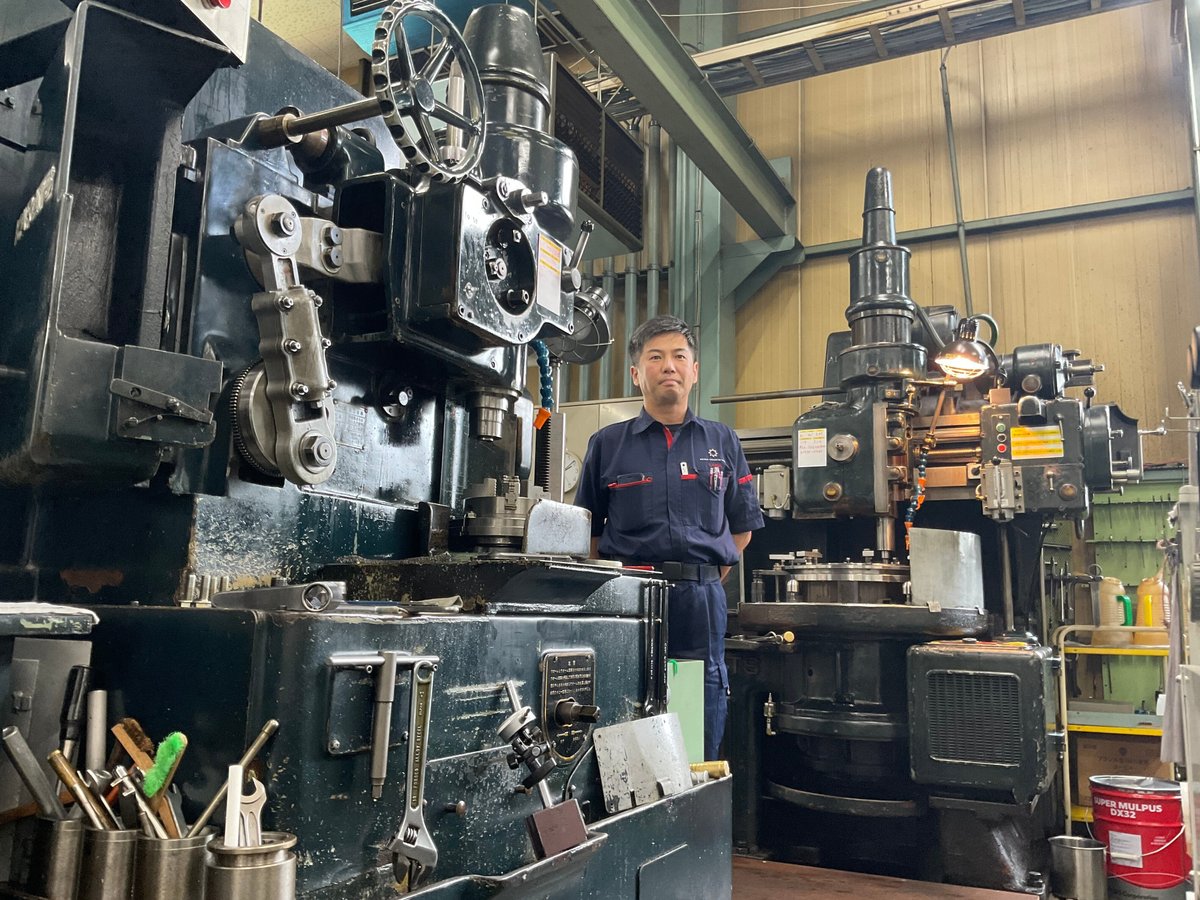
この記事が気に入ったらサポートをしてみませんか?