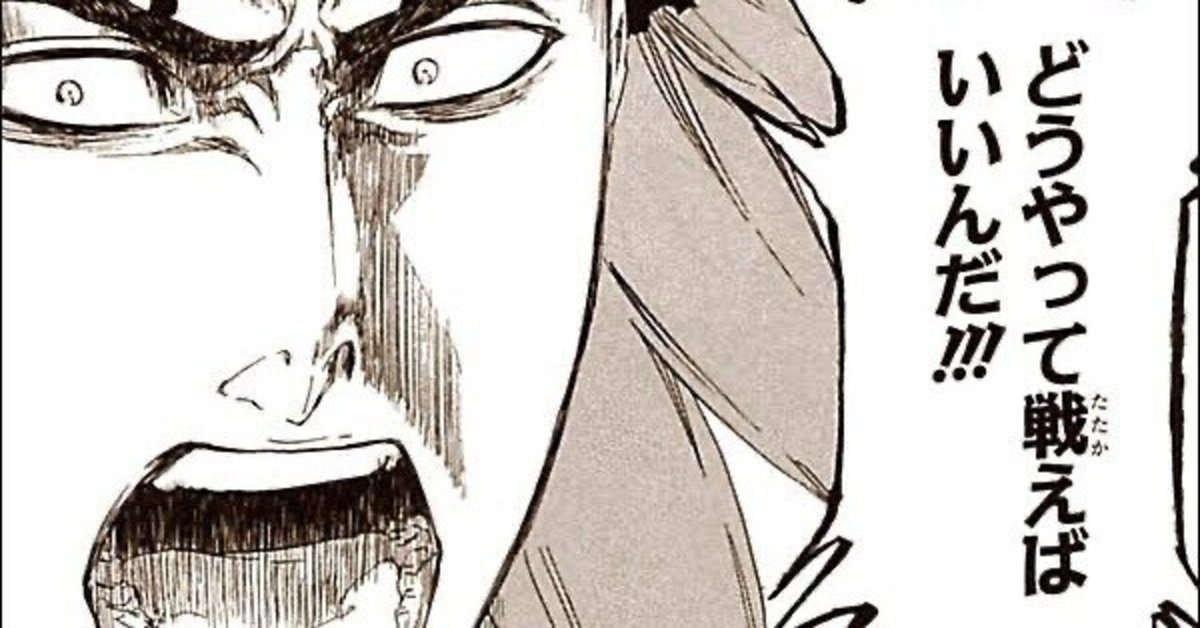
原価計算って何が正解なの?!
はじめに
この記事は「会計系 Advent Calendar 2023」の一部を構成する12月17日担当の招き猫.mdbの記事となります。
昨日はましゃ.net🍹さんで、明日はケイバリュエーション☻ (鈴木健治)さんの記事になります~!後半戦も盛り上がっていきましょう!
初めまして、招き猫.mdbと申します。
メーカーでSAPを使った原価計算を担当しています。
飽きるぐらい長く原価計算の実務に携わると、組織再編で他社の原価計算に触れる機会も増えます。
その時「こんな原価計算もあるんだ」、
「一から原価計算するなら自分ならこうする」などと考えることも多々あります。
またSAPの運用保守をサポートしてくれるベンダーさん、社内SEさんや会計士さんからも「原価計算実務は詳細が分かりにくい。」との声も聞きます。
原価計算基準が下記のように基本的な枠組みを示しているだけなので、実務では様々な原価計算が行われていると思われます。
この基準は、個々の企業の原価計算手続を画一に規定するものではなく、個々の企業が有効な原価計算手続を規定し実施するための基本的なわくを明らかにしたものである。
そこで、これから自社の原価計算を見直したい人、新たに原価計算システムを構築したい人向けに、私の実体験も含めたよりベターな原価計算の運用をできるだけ紹介していこうと思います。
原価計算のプロセスに沿って網羅的な解説を試みたところ、かなりの長文(約30,000字)となってしまいました。(すみません。。)
あまりに長いので、まず序章として各章の構成と概要について下記のように記載いたしました。興味のある章だけでも読んでもらえると嬉しいです!
全体構成
費目別計算→部門別計算→製品別計算の原価計算プロセスの順に実務上のポイントやSAPでの原価計算実務に触れています。
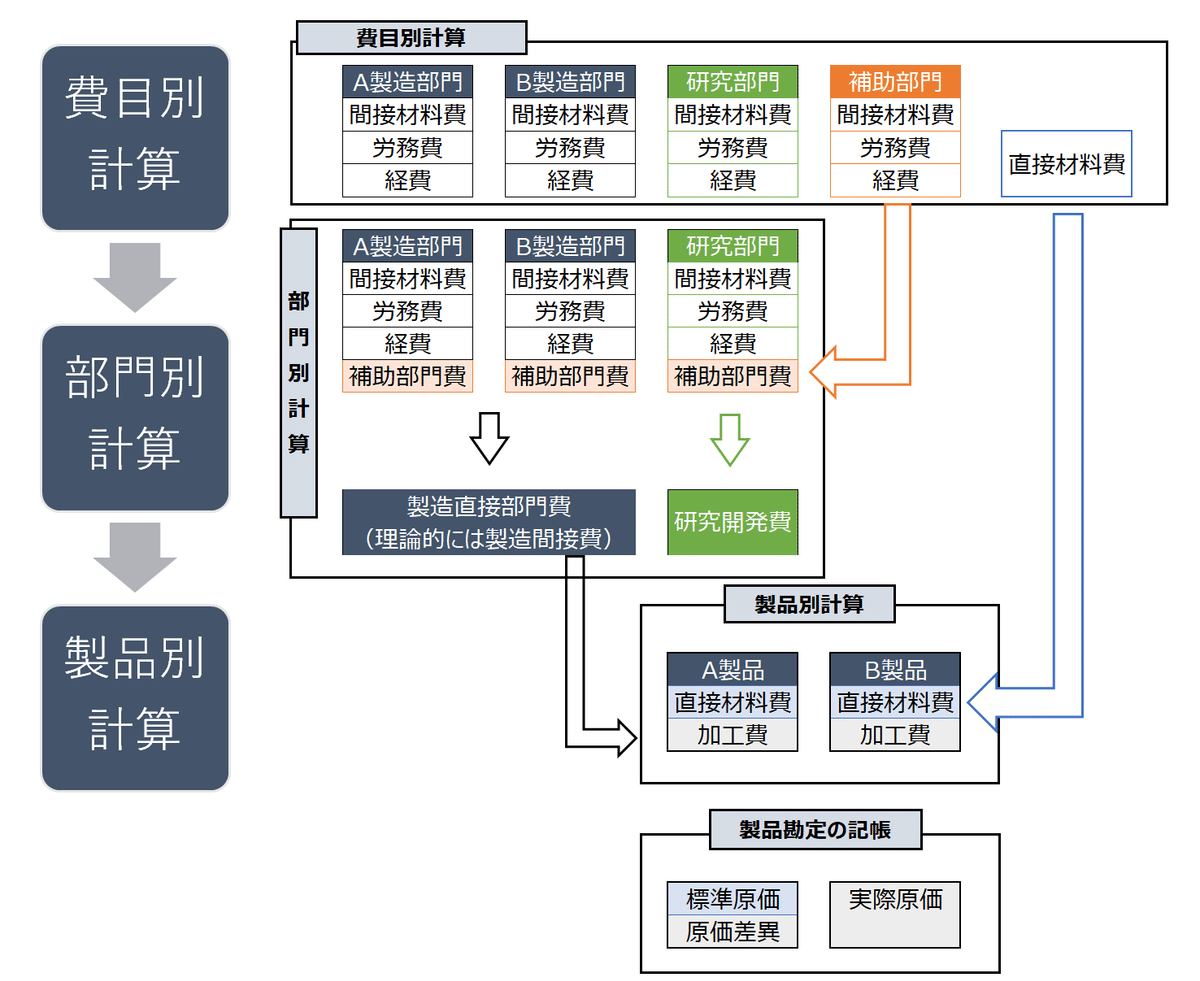
1 費目別計算
一般経費仕訳の入力方法や科目マスタ管理を中心にまとめています。その他、原料の棚卸管理や労務費管理についても触れています。
2 部門別計算
原価センタ(部門コード)の管理方法、配賦方法の種類と実務上の問題点、
よく使う配賦手法(SAPでの実務を含む)についてまとめています。
3 製品別計算
製品別計算の種類と事業特性から考えた選択の基準についてまとめています。
4 実際原価と標準原価
実際原価と標準原価の理論上の相違を記載した上で、標準原価計算実務についてまとめています。その後に実際原価と標準原価の選択の方針についても触れています。
また記事の随所に原価計算についての企業調査結果を記載していますが、下記よりの引用です。とてもよい本なのでご一読をおススメします。
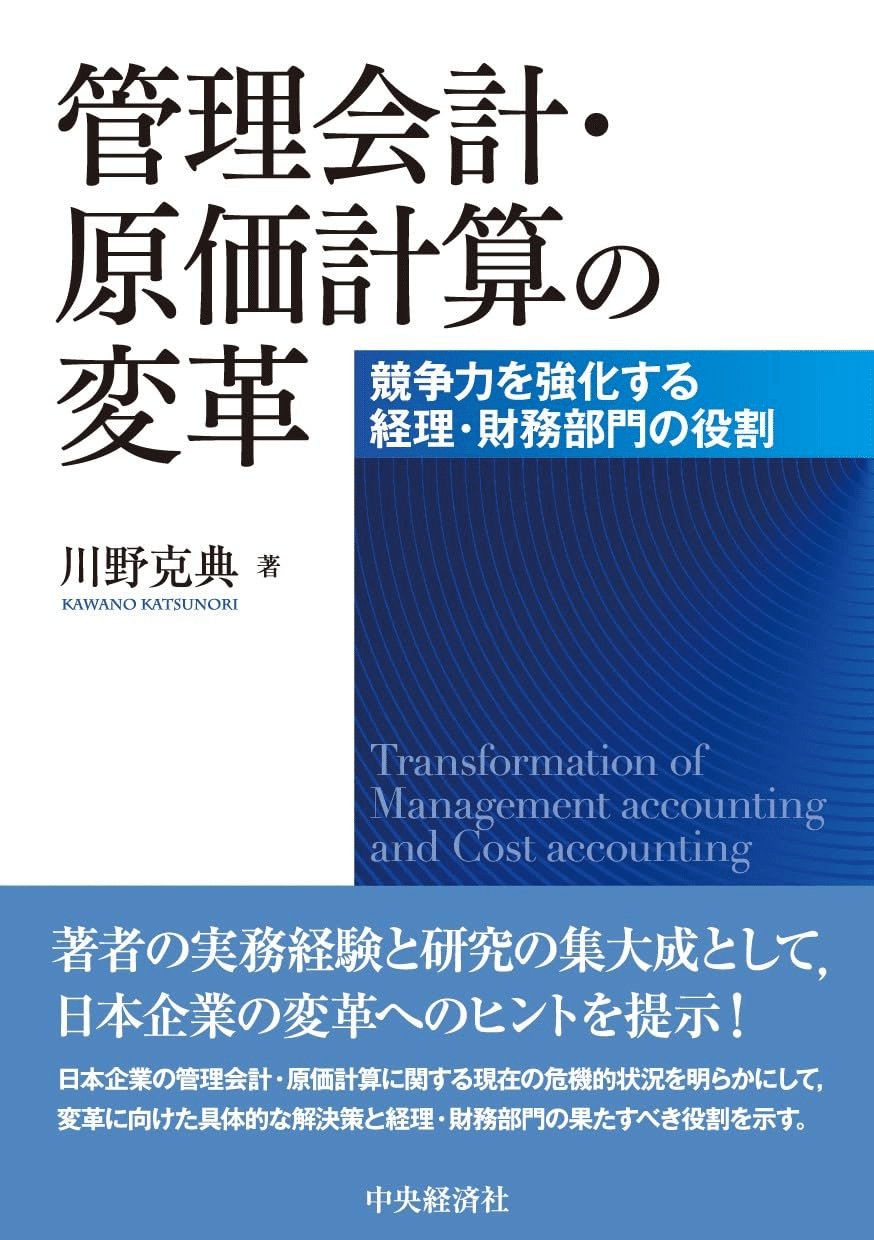
川野 克典
では、以下より本格的にスタートです!
1 費目別計算
1-1 費目別計算の重要性
まず、費目別計算です。
現代の会計システムにおける直接材料費、労務費を除く一般経費の費目別計算の仕訳は、経費精算システムでの伝票起票時に入力される科目コードと部門コード(以下原価センタと呼びます)で表現されることが一般的だと思います。
正直、ここが一番大事と言っても過言じゃないです。なぜなら、このデータが財務会計・管理会計両面の基礎となるからです。
原価計算基準でも下記のように記述があります。
原価要素の形態別分類は、財務会計における費用の発生を基礎とする分類であるから、原価計算は、財務会計から原価に関するこの形態別分類による基礎資料を受け取り、これに基づいて原価を計算する。この意味でこの分類は、原価に関する基礎的分類であり、原価計算と財務会計との関連上重要である。
八 製造原価要素の分類基準(一)
形態別分類
後ほど部門別計算の項でも書きますが、原価計算は配賦との戦いです!
具体的には、直課出来ないものを合理的な配賦でどこまで実体(直課)に近づけられるかの計算手続になります。
そのため現場に伝票起票してもらい、仕訳された一次データを集める費目別計算は最も重要な手続きとなります。
1-2 経費仕訳の入力手続き
直接材や人件費を除いた現場からの起票データから会計仕訳を起こす方法は、下記2パターンに分かれるものと考えています。
① 現場の起票データから会計仕訳を自動起票
② 現場の起票データを確認して経理担当者が会計システムへ伝送する仕訳を直接入力
①現場の起票データから会計仕訳を自動起票する方法
現在の主流となっている方法かと思います。
支払の内容・商材とその用途から会計科目への誘導を図るマスタを作成して、現場の伝票入力から仕訳を自動で起こす手法です。
入力の主体を現場に移すことで、予実管理意識の醸成と経理側の入力負荷の軽減が両立できる方法となっています。
反面、現場には入力内容がどの費目に誘導されるかの教育が必要となり、営業事務や工場総務などの現場担当者の事務負担は増えることになります。
②現場の起票データを見て、経理担当者が会計システムへ伝送する仕訳を入力する方法
伝統的な仕訳入力方法となります。
経理側で経費精算システムデータに対して仕訳入力するので、入力内容を経理でコントロールできる反面、入力要員を恒常的に確保する必要があります。さらに入力要員は会社規模(伝票数)に比例して必要となります。
また現場側にとっては、経費精算についての会計科目設定プロセスがブラックボックス化するので、予算統制の面ではやや不十分な運用となります。
どちらの運用でも重要なことは科目マスタを分かりやすく整理することです。
1-3 科目マスタの整備
勘定科目のマスタは、最初は体系的な設計がされていたにも関わらず、時間の経過とともに設定の趣旨やルールが継承されずに、新しい科目が無秩序に追加されてしまい、どんどん崩れていくパターンになりがちです。
一度設定して使用してしまった不要なマスタは、過去データとの結びつきからデータベースから物理的な削除ができず、幽霊のように残ってしまいます。(削除すると過去データ諸共消えるリスクがあるためです。)
特に、機能別分類や政策費・運営費といった管理会計的な概念を一つの勘定科目体系で表現しようとした時に設定ルールが曖昧になるケースが見受けられます。
1-4 機能別分類について
原価計算基準には、形態別分類に加えて機能別分類を行うと書いてあります。
機能別分類とは、原価が経営上のいかなる機能のために発生したかによる分類であり、原価要素は、この分類基準によってこれを機能別に分類する。この分類基準によれば、たとえば、材料費は、主要材料費、および修繕材料費、試験研究材料費等の補助材料費、ならびに工場消耗品費等に、賃金は、作業種類別直接賃金、間接作業賃金、手待賃金等に、経費は、各部門の機能別経費に分類する。
八 製造原価要素の分類基準
(二) 機能別分類
機能別分類は端的に言えば、会計科目に使用目的の色を持たせて、分析性を高めるアプローチとなります。
しかし、実務上は単に分析性を高めるという目的以上に組織上どの機能で使用された費用かを識別する方が重要な意味を持ってきます。
具体的に言うと、工場では製造以外にも、研究部門、品質保証部門、物流部門など販管費として計上すべき部門の費用が発生します。
特に研究部門については、税務上の試験研究費の観点からもPL上で明確に区分する必要があるため、製造経費と区別した科目体系が必要になります。
原価センタとの組み合わせでもそれは実現出来るじゃないか!という声もあるかと思うのですが、財務会計上のPLは、あくまで科目別で表記することになるので、販管費として表示する科目体系が必要です。
1-5 機能別分類の表現
システム的に機能別分類を実現するためには、組織の機能に応じて科目を順次追加する方法が考えられます。
例えば、間接材料費であれば、工場消耗品費、事務用消耗品費、修繕材料費、試験用材料費といった複合補助科目をどんどん増やす方法です。
…いきなりですが、この教科書的な方法は下記の理由からおススメしません。
どの科目をどの場面で使用するかあいまいになっていく。
PLがいたずらに細かく表示され、逆に分かりにくい。
特定の組織機能に対してのみの科目が生じるなど網羅的な設定が難しい。
私が、今までで一番合理的な設定と感じたのは下記の方法です。
1-6 マイベスト科目体系
材料費、労務費、経費の基本的な大科目は同一で各機能に対して同じ体系を使います。ただし、機能別分類の表現は原価センタとの組み合わせで実現します。
どういうことか説明します。
SAPの原価センタ機能で原価センタカテゴリーという区分が設定できます。
これは、原価センタに「製造」、「販売」、「研究」などのカテゴリーを割り当てることができる設定です。
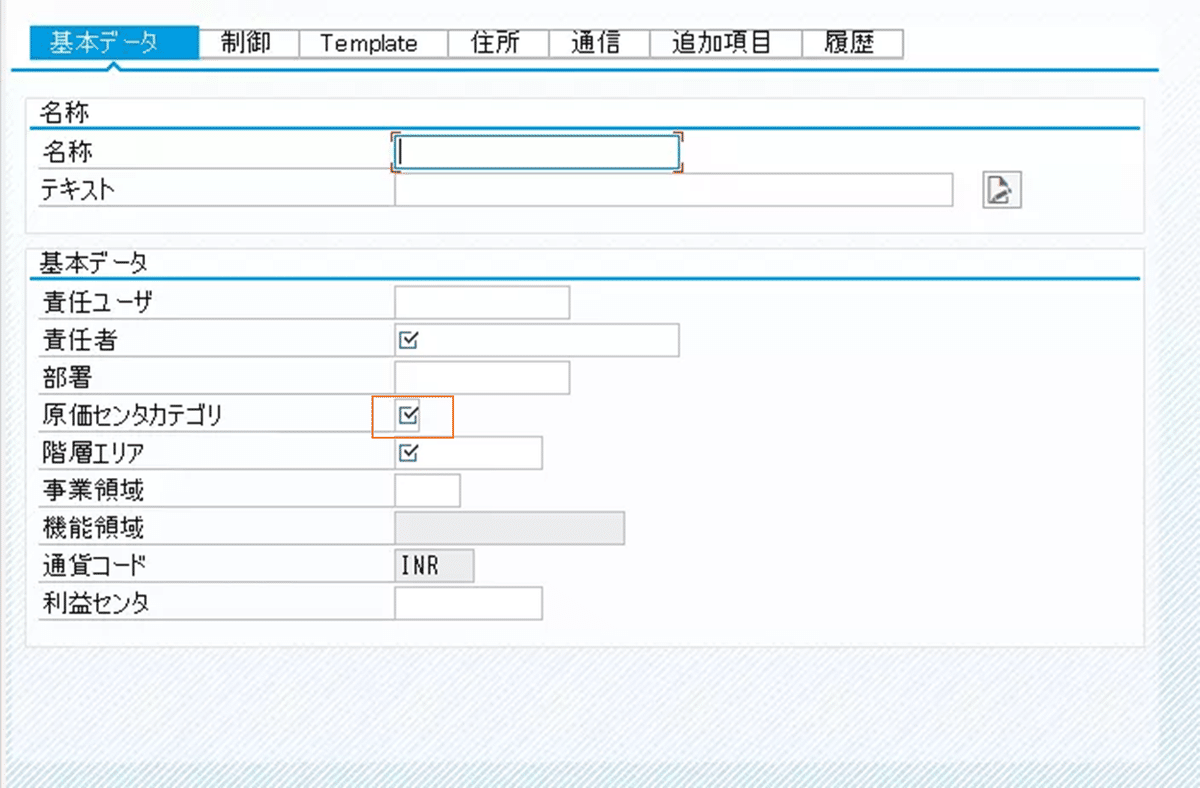
この機能を利用することで、現場で経費精算システムから起票された伝票の原価センタのカテゴリーに応じて会計科目を自動決定します。
例えば、「製造なら製造材料費」、「研究なら研究材料費」といった感じで、、
科目体系は機能ごと持つことになりますが、コード体系や名称は簡単な組み換えで設定できるように実装します。
例えば、5211が消耗品費の科目コードであれば、製造はS5211、販管はH5211、研究はK5211といったように、基本体系に何らかの区分コードを加えることで、機能別科目体系を表現するのです。
この方法であれば、実質的な科目体系は基本体系の一つとなるため、機能ごとに異なる科目体系を覚える必要はありません。また全ての体系に同一科目を設定することになるため、網羅性の問題は生じません。さらにPLの表記も製造、研究、販売などでまとまったものを作りやすいので勘定科目のグループも作成しやすいです。
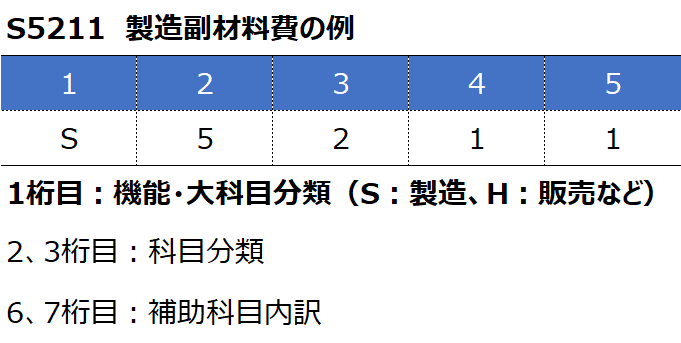
1-7 余談_SAPの科目設定
なお、SAPの勘定科目設定はとても複雑で、FIの財務会計科目を設定しても、COの原価要素科目も設定しないと、原価センタ会計としての仕訳が入力できません。
組み込めば色んな処理ができる複雑なDBであるがゆえに、要求されるマスタ設定も非常に細かいユーザー泣かせのシステムとなっています。。
1-8 材料費計算と棚卸管理
材料費計算では、原料費を製品に直接賦課する直接原料費と間接部門の経費となる間接原料費に分ける必要があります。
この区分を明確にするために、実務では直接用原料に原料コードを採番して、在庫管理システムで管理する手法を使います。
生産システムでの原料投入情報や購買システムの原料入荷情報を在庫管理システムと会計システムにタイムリーに連携することで、棚卸帳簿を適切に管理するためです。
間接原料の場合は、通常は在庫管理システムでの管理を行いません。製造部門の原料コード管理と採番が煩雑になるからです。
研究用原料などは、購買時点で研究部門原価センタの試験材料費として費用化してから期末棚卸で未使用となっているものを未使用原料として、棚卸勘定に振替計上する処理が一般的だと思います。
なお、棚卸管理という点では、コード管理をして在庫管理システムに載せる方法が一番です。
金額や購入目的を基準に、製造部門や購買部門による注文時点でのコード管理を促す運用に内部統制を整備すべきです。
1-8-1 SAPの原料支給管理
SAPでは原料を仕入先に無償支給する場合、BOMを用いて、元支給原料と外注加工費、完成原料を管理することができます。
但し、製品、半製品と異なり原料全てにBOMが必要な訳ではないので、BOMの変更が必要な場合、設定がモレることが多いです。
1-9 労務費計算と兼務
労務費は給与計算システムで計算した実際労務費を、人事システムの個人別所属原価センタ情報をもとに部門別に集計する方法が一般的だと思います。
しかし、実務では以下の例外パターンが発生します。
個人が複数部門を兼務する場合
スポット的な作業応援による労務費振替を行う場合
個人が複数部門を兼務する場合
部門別の兼務割合を人事システムの個人コードに設定することで、労務費計算を行うことが多いです。
この場合、兼務割合の設定を現場に依頼すると、異様に細かい割合を提示されることもあるため、重要性の観点から方針を示すべきです。
作業応援費
実務では、他部門への応援作業の時間情報を受け取り、時間当たりの労務費単価をかけることで、労務費の付替を行うとことが多いです。
応援労務費レートの定期的な見直しや現場から作業時間情報を入手する運用の整備が重要となります。
次に部門別計算にいきたいと思います。
2 部門別計算
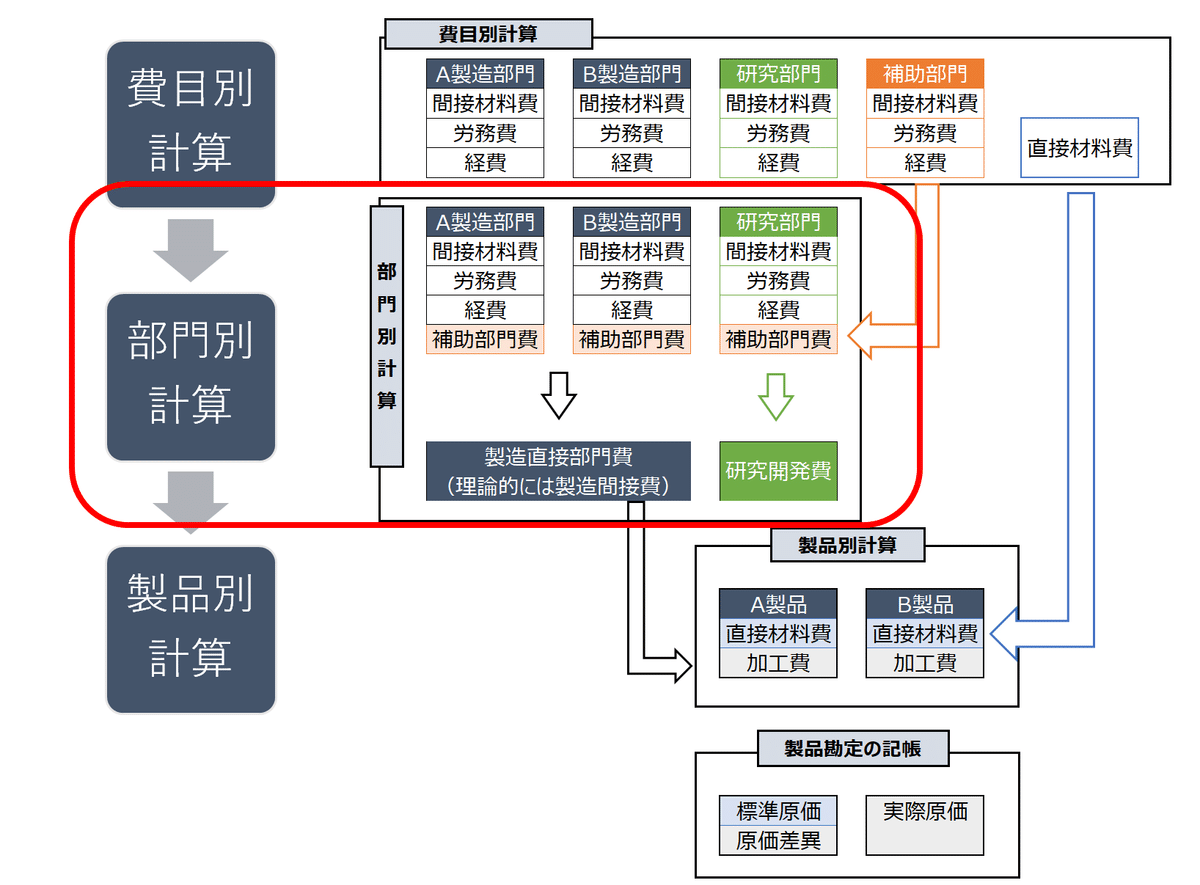
2-1 そもそも部門別計算って何?
原価の部門別計算とは、費目別計算においては握された原価要素を、原価部門別に分類集計する手続をいい、原価計算における第二次の計算段階である。
原価部門とは、原価の発生を機能別、責任区分別に管理するとともに、製品原価の計算を正確にするために、原価要素を分類集計する計算組織上の区分をいい、これを諸製造部門と諸補助部門とに分ける。製造および補助の諸部門は、次の基準により、かつ、経営の特質に応じて適当にこれを区分設定する。
第三節 原価の部門別計算
原価計算基準の定義では、原価センタ別に集計された経費を製品原価の計算を正確にするために分類集計すると記載されていますが、
単なる製品原価への配賦に留まらず、販管費の間接部門から直接営業部門への部門費配賦も含めた広い概念で捉えてもらえたらと思います。
例えば、複数事業セグメントを持つ企業においては本社管理部門費などの販管費も本社費として各セグメントに配賦していると思います。
そういった意味で部門費配賦は、メーカーのみならず、複数事業を経営する多くの企業にとって身近なテーマであり、悩みの種だと考えています。
まず、本格的な部門別配賦の話に入る前に配賦の前提となる原価センタについて書こうと思います。
2-2 原価センタ管理の難しさ
原価センタは言わずもがな組織・部門を管理するコードです。
どんなに成熟した企業でも活動の変化に応じた組織の改編は避けられません。その意味で、原価センタは科目コード以上に管理が難しいマスタと言えます。
以前使用していたが現在は使っていないマスタ
予算のみ使用したマスタ
…そういった幽霊のようなマスタが溜まっていき、事情を知らない後任者を苦しめることになります。
そもそも、原価センタは組織図に沿った形でHR-SAPなどの人事管理システムの階層に合わせて設定されるべきモノです。そのため、経理側で管理すべきなのかと考える人もいるかと思います。
そこで、原価センタの決定主体について考えてみようと思います。
2-3 原価センタは誰のもの??
まず、原価センタはある部門にとって予算実績管理ができる単位で決定される必要があります。その意味で部門の管理単位を決める主体は、活動内容を決定する事業部門となります。
また人事部門は、予算編成時に各事業部から要員計画を取りまとめ、組織図を決定します。全社的な要員管理・組織管理という点では、人事部門が原価センタ決定の主体とも言えます。
さらに、経理部(経営企画部)は、各原価センタの経費を会計システムで集計し、会計報告として取りまとめしています。
原価センタ別経費を予実管理し、適切な事業セグメントへ集計できるように管理するという、会計データ管理という視点では、経理部が原価センタの決定主体となります。
このように、原価センタは決定主体が曖昧になる傾向が強いです。
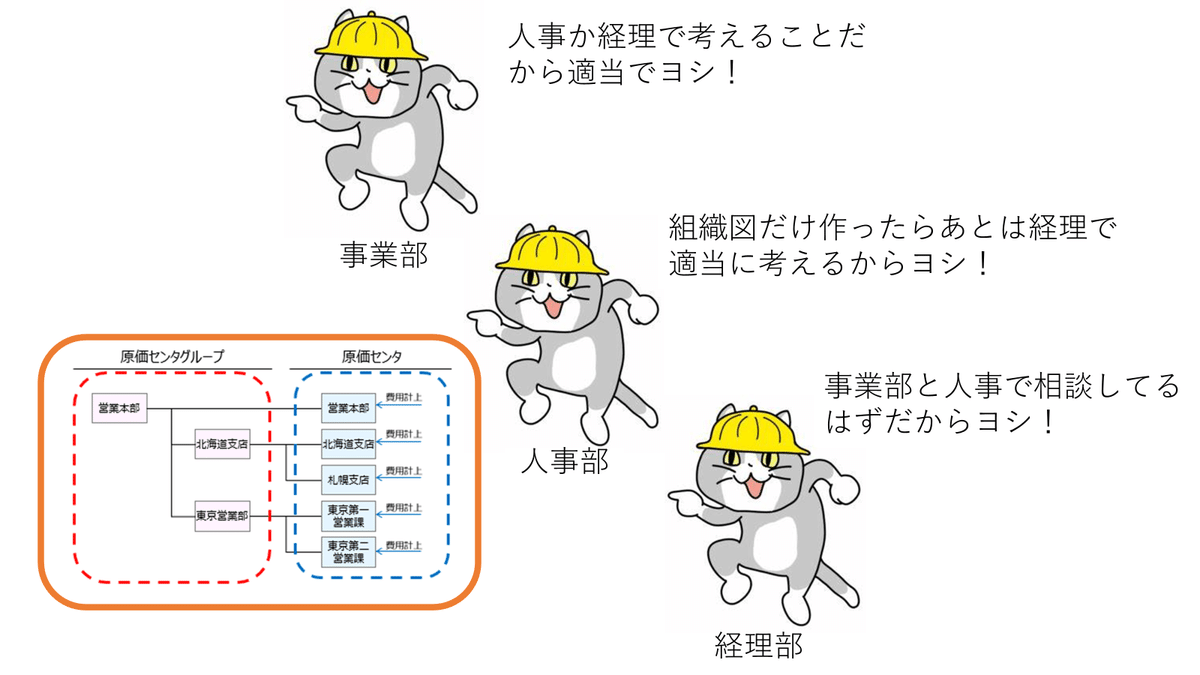
ある時点で設定された原価センタが何のために作られたのか、不明なまま運用されていくことも多いです。組織再編のたびに新マスタが作成され、管理が煩雑になる傾向が見られます。
また原価センタが増える事は単純に部門経費の管理で混乱を招くだけでなく、後述の配賦設定の複雑化も招きます。
原価センタ✖️配賦設定✖️配賦率と、掛け算でどんどん設定が複雑になるため、費用の流れも当然分かりにくいものになっていきます。
じゃあ、どういう設定がベストなの?って話をしていこうと思います。
2-4 ベターな原価センタの管理
端的にまとめると下記のようになると思います。
設定の主体は事業部門
申請ルートの整備
過去マスタの使い回しはNG
原価センタは予実管理のための集計単位として考えると、どういう事業展開を行い、それを計測したいかを理解している事業部門が設定の起点になるはずです。
経理、人事はそのニーズを汲み取って、組織設定上のアドバイスを行うという流れが基本です。
但し、申請ルートを整備して、予算編成時などに人事と経理に事前に連絡がいく運用は必須です。事業部制の組織は、時に経営のスピード感を建前に管理系への連絡を怠りがちです。
無茶で無意味な組織再編を牽制するためにも、管理系への事前申請ルールは必須です。
人事と事業は新組織を知ってるが、経理は人事発令の直前(直後…😭)まで知らされない
事業部門が勝手に決めた原価センタの粒度がとても細かい
このような情報連携不足でマスタメンテやその後の予実管理が悲惨なことになる例も多々あります。
またシステム面では、過去マスタを使用すると後述する配賦の設定など、既存マスタに対する設定が思わぬ形で影響を及ぼすことで、事故に繋がることがあります。
単なる名称変更の場合以外は、面倒ですが、新マスタを作った方が無難です。
さらに、人事管理で使用するマスタと会計で使うマスタは組織グループも含めて極力粒度を合わせるべきです。
設備管理専用の原価センタやプロジェクト専用原価センタなど、会計側のみ使用するマスタを設定する場合があったりもしますが、、
例外が多くなると、経費精算システムなど、社内システムで現場の方が原価センタを入力するルールが複雑化します。
どちらか片方のシステムにのみ存在するようなマスタは極力少なくした方がいいです。
次に部門別配賦の方法について紹介していこうと思います。
2-5 1次配賦と2次配賦
配賦計算は、他部門への配賦する際の科目が元発生科目か、部門費科目かどうかで大別されます。
本記事では前者(元発生科目で配賦)を1次配賦と呼びます。
下記のイメージ図のように、あたかも配賦先部門で発生した費用であるかのように記帳できるところが1次配賦の特徴です。
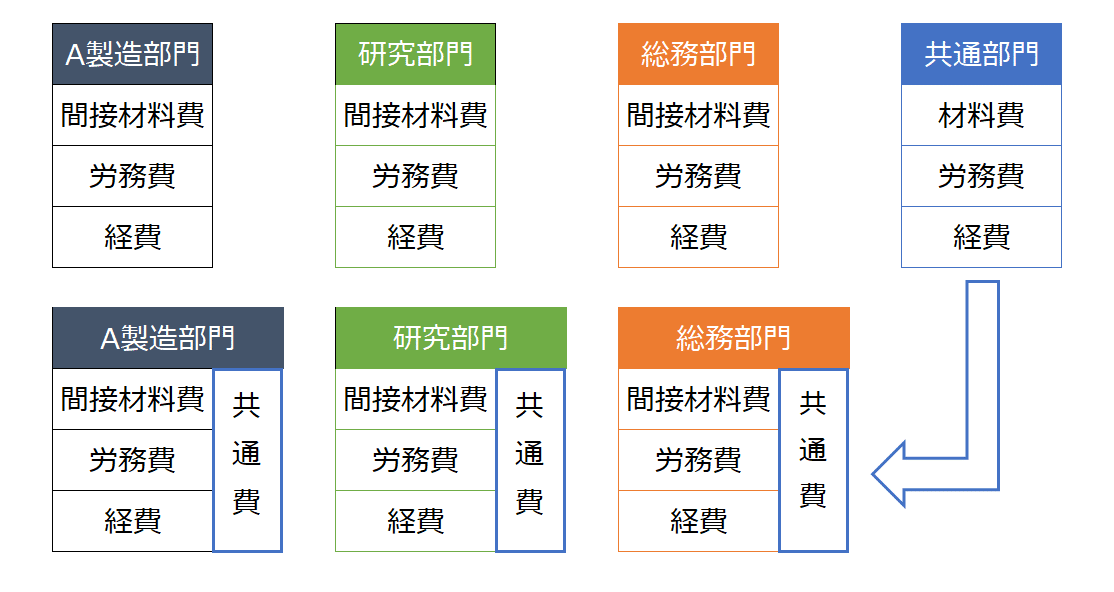
次に1次配賦の具体的な適用場面について書いていきます。
2-6 1次配賦ってどういう時に使うの??
上述の通り、1次配賦した場合は元部課の費用が0になり、配賦先部課の科目別経費として配賦されることになります。
予算実績管理上は、配賦先部課の経費として考慮する必要があるが、運用上は直課が難しい場合に使用します。
例えば、動力費や固定資産税、事業所税などの共通経費です。配賦基準は動力費の場合は、毎月の建屋別の使用量実績比や稼働時間比などで配賦する場合が多いです。
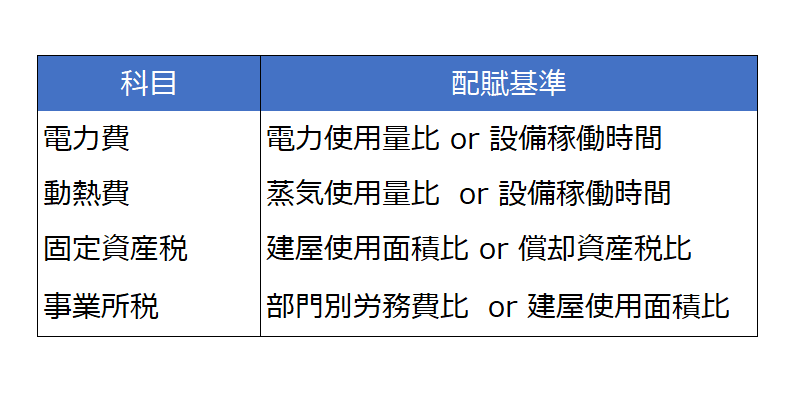
共通費は、現場の伝票起票時点で部課別に直課することが煩雑な場合に、配賦率の設定のみで振り分けできるため、仕訳入力の負荷軽減という観点から見ると便利ですが、あまりにも細かい共通費の配賦設定を作ってしまうと、、
下記のような弊害が発生します。
突然、工場担当者が変更になり、配賦基準を入手できなくなる
配賦そのものが忘れられ、ずっと固定率で配賦
どの配賦基準がどの費目に関係しているか分からない
直課できるものは仕訳で直課するのが鉄則です。
現代会計システムでは、500件ぐらいの単純な振替伝票ならテキストやCSV取込で簡単に転記できる仕組みがあることが普通かと思います。(なければすぐに仕組みを作った方がいいです。)
平均年齢の高い職場だと、昔の慣習から仕訳ではなく、すぐ配賦を使いたがるおじさんがたまにいますが、配賦がブラックボックス化するリスクを考えるべきです。
また配賦のブラックボックス化を防ぐために、配賦基準の管理表は作成すべきでしょう。
次は2次配賦(補助部門費の配賦)についてです。
2-7 そもそも補助部門って何??
原価計算基準では下記の通り定義しています。
補助部門とは、製造部門に対して補助的関係にある部門をいい、これを補助経営部門と工場管理部門とに分け、さらに機能の種類別等にしたがって、これを各種の部門に分ける。
補助経営部門とは、その事業の目的とする製品の生産に直接関与しないで、自己の製品又は用役を製造部門に提供する諸部門をいい、たとえば動力部、修繕部、運搬部、工具製作部、検査部等がそれである。
工具製作、修繕、動力等の補助経営部門が相当の規模となった場合には、これを独立の経営単位とし、計算上製造部門として取り扱う。
工場管理部門とは、管理的機能を行なう諸部門をいい、たとえば材料部、労務部、企画部、試験研究部、工場事務部等がそれである。
一六 原価部門の設定 (二) 補助部門
製造直接部門など製品の計算にダイレクトに関係する部門の費用と違い、補助部門は製品や事業セグメントと直接の繋がりを持ちません。
そのため、いったん直接部門に部門費として配賦することで、結果的に製品別計算や事業セグメントへの経費集約ができるようにするのです。
なお、本記事では研究部門費など事業セグメントに直接賦課される販管部門についても広い意味で直接部門としています。
補助部門はその部門特性に応じて、異なった部門費科目として直接部門に配賦します。
実務上は、保全部門、試験部門などについては補助経営部門として設定し、総務、工場経理、生産計画部門などは工場管理部門として設定することが多いです。
但し、間接部門の原価センタ設定が増えれば増えるほど、補助部門費の設定も必要になります。
単純に考えると部門費設定が多くなればなるほど、間接部門の用役を正しく配賦できそうなものですが、そうはならないのが原価計算の難しいところです。
原価センタを細分化して、そのすべてについて現場から用役提供率(配賦率)をもらう場合、現場の負荷も高まるので、逆に正しい用役提供率を入手することは難しくなります。(後述するSAPなど会計システムの配賦設定をミスる可能性も著しく高まる。)
ある程度グループ化して用役提供率(配賦率)を設定するように現場と協議すべきです。
また原価計算基準では工場一般部門の設定についても触れています。
部門共通費であって工場全般に関して発生し、適当な配賦基準の得がたいものは、これを一般費とし、補助部門費として処理することができる。
一七 部門個別費と部門共通費
例えば、工場長の労務費など多額で工場全体に影響する間接経費については、工場一般部門費として直接部門に配賦します。
実務的には各部門の発生経費にできないような工場全体に影響する経費を集計して一括して配賦したい場合に使用することが多いです。
但し、工場一般部門の経費は、ルールを決めないとゴミ箱のように工場内のいろいろな経費が仕訳される傾向があります。予算実績管理の過程で工場一般部門の経費で他部門へ直課できる経費を見つけた時は、振替計上すべきです。
2-8 補助部門費の配賦(2次配賦)
次に具体的な配賦の方法について記載していこうと思います。
1次配賦と違い、下記イメージ図のように配賦先部課に1次配賦も含めた経費合計を部門費として配賦する方法が補助部門費の配賦となります。本記事では、これを2次配賦と呼ぶことにします。

2次配賦は、理論的に補助部門間の相互の用役の授受をどう考慮するかで下記3つの方法に分かれます。
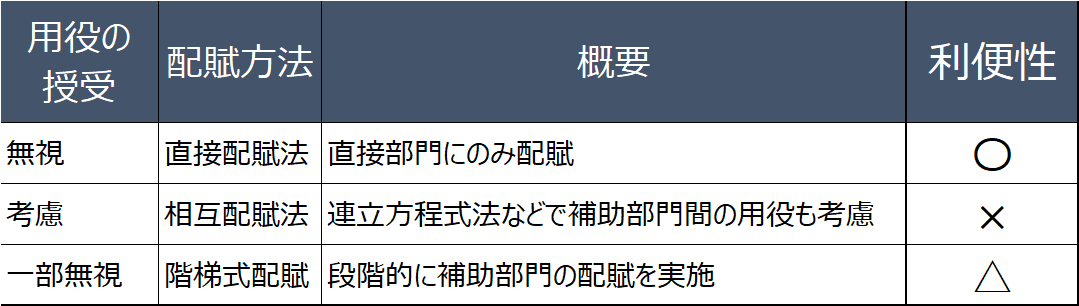
2-9 配賦を考える上で重要な視点
実務的には、直接配賦法が第一優先です。
間違っても、「補助部門間の配賦も考慮した適切で精緻な計算が〜」などという耳障りのいい言説に惑わされて相互配賦法を選択してはいけません。
理由は、配賦処理が複雑化するためです。
例えば、予算編成時に各事業セグメントごとの製造間接費を集計するとき、まず経理担当者以外は試算できなくなります。(ひどい時は、経理担当もその配賦方法の合理性が分からず、計算式の説明しか出来ない。)
原価計算は正確性も重要ですが、計算方法を全社的に共有しないと、PLの改善に繋がりません。
補助部門間の配賦を行った方が、相互配賦も含めたトータルの管理コストが高い補助部門を把握することも可能でしょうが、、
実際は、各部門の発生経費の予算差異すらまともに把握出来てない会社も多いのではないでしょうか。
発生費用についてのコストダウンの前に、配賦基準の話をしても全社的なコストダウンには繋がらないのです。
発生費用の構成が把握出来ていない状態で、配賦基準の妥当性だけをどれだけ論じても、部門間の費用の押し付け合いにしかなりません。
なお、階梯式配賦については、実務上で使用する場面があります。
本社費を各工場にばら撒いたあとで、各工場の直接部門に再度配賦するような場面です。ただ、このような多段階配賦も設定が複雑になるため、多用は禁物です。
2-10 複数基準か単一基準か、実際配賦か予定配賦か
また配賦方法については、経費の観点と用役使用量の観点から下記4パターンに分かれます。
理論上は、複数基準×予定配賦が一番優れているとされていますが…
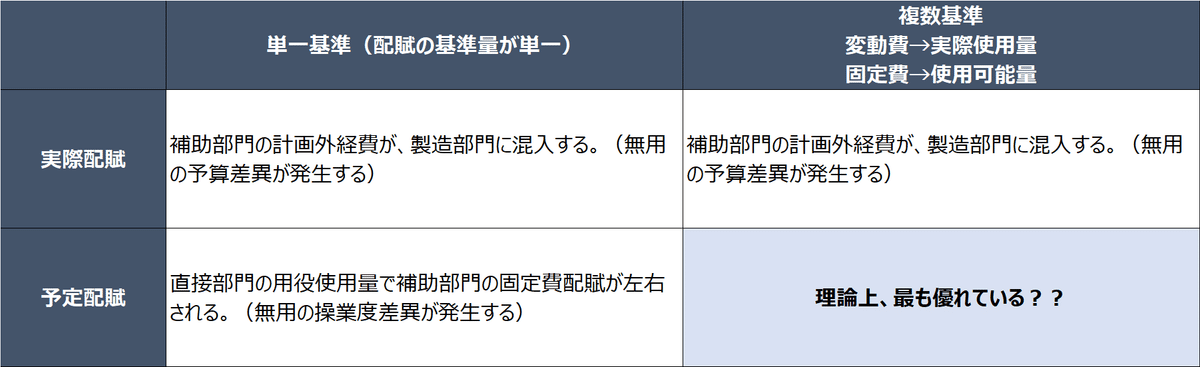
実務上の観点から私はこの説に異論を唱えたいと思います。(…すみません。)まずは予定配賦の問題についてです。
2-11 予定配賦の問題点
理論上の予定配賦の計算式は下記の通りです。
予算レート(予算経費÷予算用役量)×実際用役量
理論的には、責任会計の観点からは予定配賦が合理的とされています。
計画外で発生した実際経費の影響が直接部門に流れない配賦ができるためです。実績発生との差異は配賦差異として補助部門側で把握されるため、責任の所在が明確になるとされています。
実務的にも定常的に決まったレートで配賦するので、配賦先部門も予測が立てやすく、予実管理がしやすいというメリットもあります。
確かにそうなのですが、私はあえて声を大にして言います。
予定配賦は単純に実務で使うには重大な欠点を抱えています。
例えば、予算で大規模設備投資を計画していた補助部門の費用を実績で配賦するとしましょう。
当然、設備稼働に伴う多額の償却費や修繕を前提とした予算による予定配賦率を設定することになります。
その後、実績で予定通り設備計画が遂行されれば、何の問題もないのですが、実務では投資の実施時期が後ろにズレることがよくあります。
その場合、実際は発生していない予算の経費を予定配賦率で配賦することになるため、直接部門にありもしない負担を強いることになるのです。
酷い時は、補助部門の配賦後費用がマイナス残高になる時もあります。
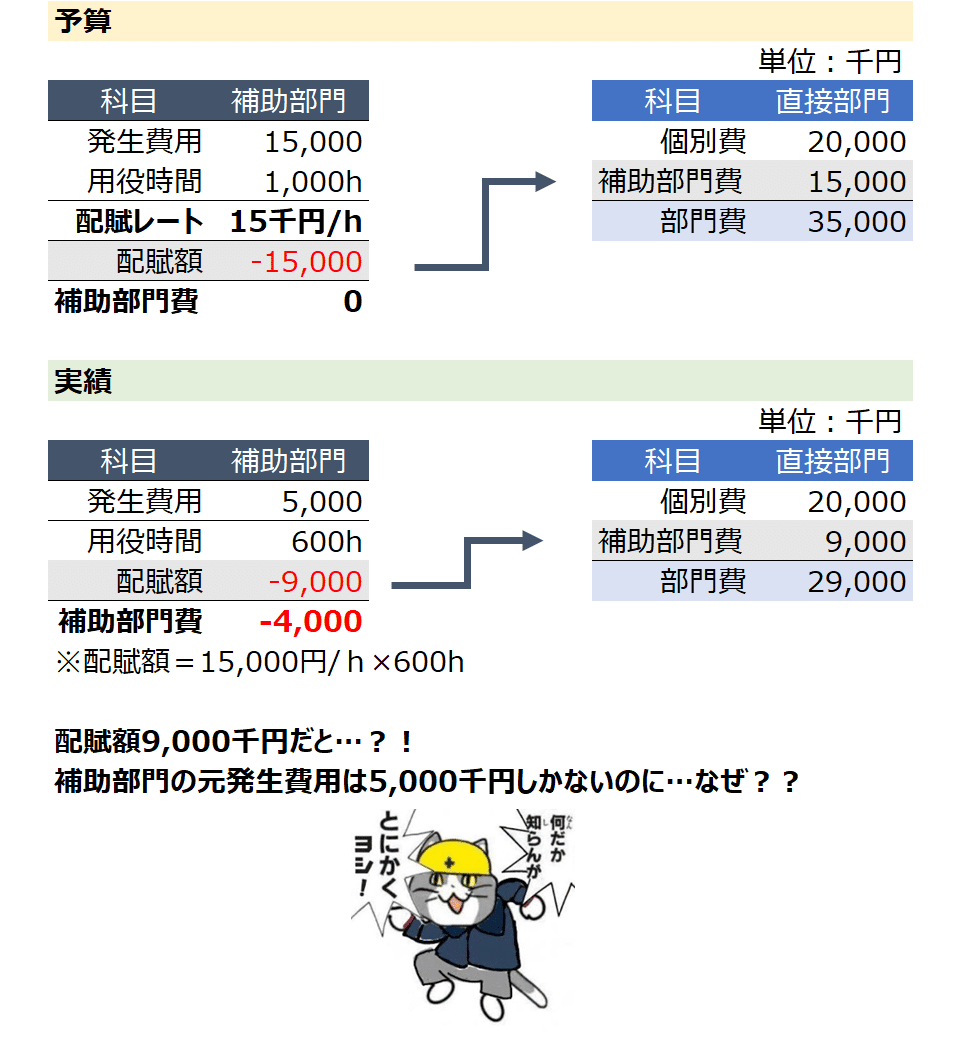
このような費用の入り方をした時に、
「補助部門は予定配賦による差異が多額に出た結果、マイナス残高になっております(ヨシッ!)」と事業側に説明できる勇気があなたにあるでしょうか?
…私は、勇気がなくても説明を求められた事があります😭
元々、補助部門で予定配賦を用いる場合は、製造直接の役割も担うカメレオン型補助部門の場合が多いです。
例えば、生産技術部門や試験部門の場合、入荷時点の原料試験や工程管理といった間接部門としての業務と直接製品の製造にかかわる業務を同時に行っています。
製品に直課できない作業にかかる時間分は、補助部門として他部門に配賦して、残った時間分を直接製品にかかる費用として、製品計算に直課する計算を行う場合があるのです。
このような部門の配賦後経費がマイナス残高になると説明が大変です。(というか納得してもらうのは諦めた方がいい。。)
事業が安定して経費の規模が予算と実績でそれほど変わらない場合は有効ですが、変革期にある組織の配賦方法としては正直使いにくい方法です。またSAPの標準機能では配賦レート(固定単価)を用いた予定配賦は実装が難しいです。
2-12 複数基準の問題点
複数基準は補助部門費を固定費と変動費に分けて、固定費については関係部門の消費能力の割合、変動費については、実際消費量で配賦する方法です。
一見、正しいやり方のように思えますが、ある補助部門の配賦基準が複数に分かれる方法というのは、想像以上に管理が難しいです。
配賦先は、どの費用がどの基準で配賦されたかについて理解していないと正確な予算差異の分析ができないので、取り敢えず配賦された経費を受け入れるしかないという状況に陥ります。
活動基準原価計算のように科目や活動特性に応じた配賦基準を持たせて配賦を精緻化しようとしたケースもありますが、導入時は管理できても数年後に後任者が苦しむ例を見てきたので、同一部門で複数の配賦基準を持つことはあまりおすすめしません。
2-13 実務でよく使う2次配賦の方法
結局、実務で使うには、直接配賦かつ単一基準・実際配賦が一番使いやすいということになります。また「管理会計・原価計算の変革」の調査でも同様の基準を採用する企業が一番多いようです。
よく見るのは、各部門の予算で入手した補助部門の用役提供率表(配賦率)を元に実績経費を配賦する方法です。
予算と実績で同一の配賦率を用いて実際発生経費を配賦する形になるので、補助部門費の配賦による操業度差異は発生せず、補助部門の予算差異のみが影響する形となります。
配賦率の差異が出ないので、直接部門側から見た場合、補助部門の管理者に予算差異の内容を問い合わせすれば差異分析が可能となります。
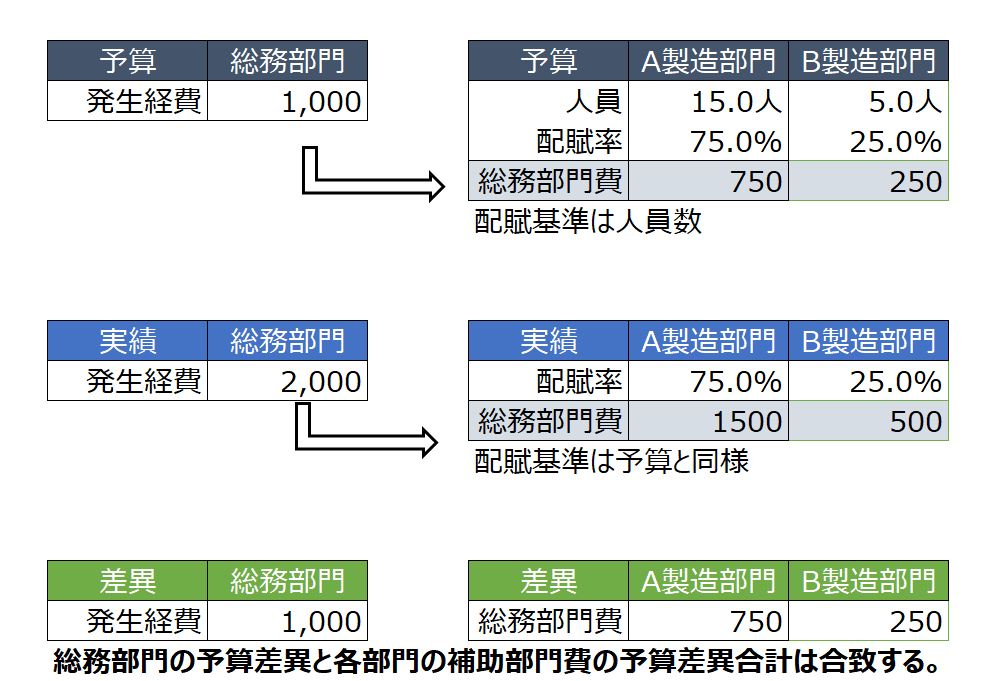
この方法の場合でも、期中で組織再編など前提が大きく変われば、実績の用役提供率を再度入手して、配賦率を変更することになります。
なお、上記はあくまで補助部門費の直接部門への配賦の話であって、製品別計算で集計した直接部門費を各製品へ配賦する話とは分けて考えて下さい。
2-14 配賦基準の決定について
つらつらと配賦方法について書いてきましたが、ここで一番大事なことを書きます。
それは、具体的な配賦基準(例えば総務の費用であれば各部門の人数比で分けるなど)を製造部門や事業部門と協議して、どのように決定していくかということです。
基本的に活動内容を決めるのは工場なので、工場が用役率を決定するのですが、工場だけでは事業側が納得する用役率を設定できないことも多いです。
原価計算は正確性も重要ですが、計算方法を全社的に共有しないと、改善に繋がりません。
昔、ある工場の保全課の課長さんが、「工場内の機械装置の簡易修繕を各部門が依頼しまくるせいで、保全課の残業が常態化している。保全の大変さを各部門に知らしめるために用役提供率を修繕依頼伝票の件数にしたい」と経理に頼み込んできました。
ここで経理担当者が、保全課の経費実績を見たところ、費用構成比率で高いのは労務費(残業代)よりも、むしろ保全部門が管理しているキュービクルやボイラーなど、工場全体の動力設備の管理費(定期修繕費や償却費)でした。現状は、各部門の動力使用量を基準に用役率を決定しているので、変更は不要と課長さんに伝えたところ…
保全課の課長さんは、「それなら費用に応じて用役を分けられる方法を教えてよ!」と言ってきました。
実務上、読者の皆さんはどのように対応しますか?
私の場合は、保全課が記録していた各部門への簡易修繕にかかる台帳の作業時間を元に保全課の労務費を各部門へ応援労務費として振替する運用変更を行いました。
配賦ではなく、発生費用を適正にする手段を取ったのです。
このように、配賦に頼らずとも納得性の高い費用管理はできるのです。
まずは、配賦方法の巧拙にこだわることではなく、各部門の費用を丁寧に分析して、直課できる費用を適切に反映するべきです。
配賦はしょせん発生費用を割り振る道具に過ぎません。各事業セグメントごとに原価を集計した時に事業部長が補助部門費を見て一番納得できるのは、配賦元部門で自分のセグメントに関連する費用が発生しているとはっきり分かる時だけです。
元発生費用として把握されているものが一番強いのです。その意味で最初の費目別計算はやはり一番重要です。
配賦率は、発生している経費を分析した後で、その費用構成から経理&現場で一緒に考えるべきです。
もし用役率を変更する場合は、事業側に影響額を試算して承認を得ないと原価改善の土台は整いません。
2-15 SAPによる部門費配賦の実装
なお、SAPで上記のような1次配賦、2次配賦の実装のためには科目マスタと原価センタ以外に下記のマスタを整備する必要があります。
配賦周期
統計キー
配賦周期とは、配賦元部門(センダ)のどの科目を先部門(レシーバー)に対して何の科目で、どのような基準で配賦する、いわば配賦基準をマスタ化する設定です。
センダやレシーバ、科目はグループ単位でまとめて設定できます。
また配賦率は、売上基準など科目値を利用した配賦率も設定できますが、任意の率で各部課に配賦することも可能です。
その配賦率設定をSAPでは統計キーと呼びます。
このように、SAPで配賦を実装するには、補助部門の原価センタ(またはグループ)ごとに、配賦周期と統計キーの設定が必要になるので、原価センタ数が多いと管理が非常に煩雑です。
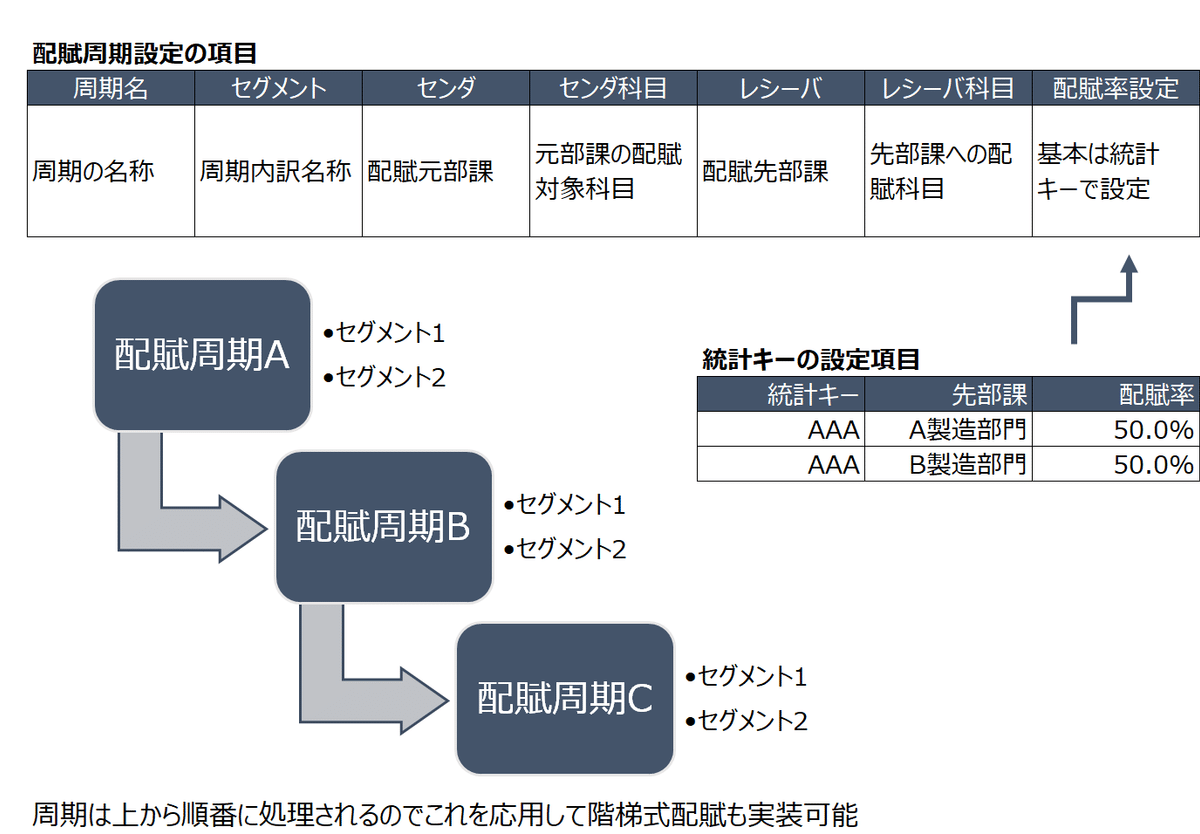
設定を工夫すれば、複数基準や相互配賦なども設定できますが、熟練の技が必要です。
ちなみにSAPの配賦用トランザクション(処理画面)は、付替 or 定期再転記(1次配賦用)、配賦(2次配賦)、利益センタへの配賦など多岐に分かれており、それぞれの画面で設定が必要です。さらに予算と実績でもトランザクションが分かれてします。
…ここまで説明をした時点で、大体の後輩社員は配賦のことが嫌いになります。
なお、万が一配賦をミスった場合、通常の振替伝票で配賦データ(2次原価要素)を修正することは出来ません。配賦という呪力を帯びたものは、同じく呪力を持ったものでしか対抗が出来ないのです。
そのため、修正のための一度きりの原価センタ、配賦周期、統計キーを設定する強者もいます。
なお余談ですが、SAPで配賦処理でエラーが出る原因の第1位が、統計キー(配賦率)の設定漏れです。
統計キーは、年度、各月、予算、実績の粒度で毎回設定が必要なので、忘れる人が絶えません。
その場合のエラーメッセージは、「レシーバがありません」とだけ表示されるので、テスト実行後にctrl+Fで「レシーバ」と検索して確認する事は基本動作となります。
澱みなく周期の流れを把握できる者だけが一級SAP術師として、運用保守を任されるのです😭
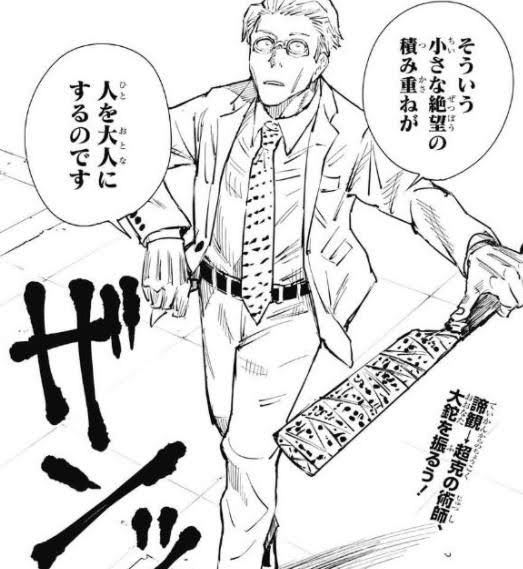
3 製品別計算
やっと製品別計算まで来ました…
ここまで読んでいただいてありがとうございます。
ここまでで全体のうち6合目ぐらいだと思います。
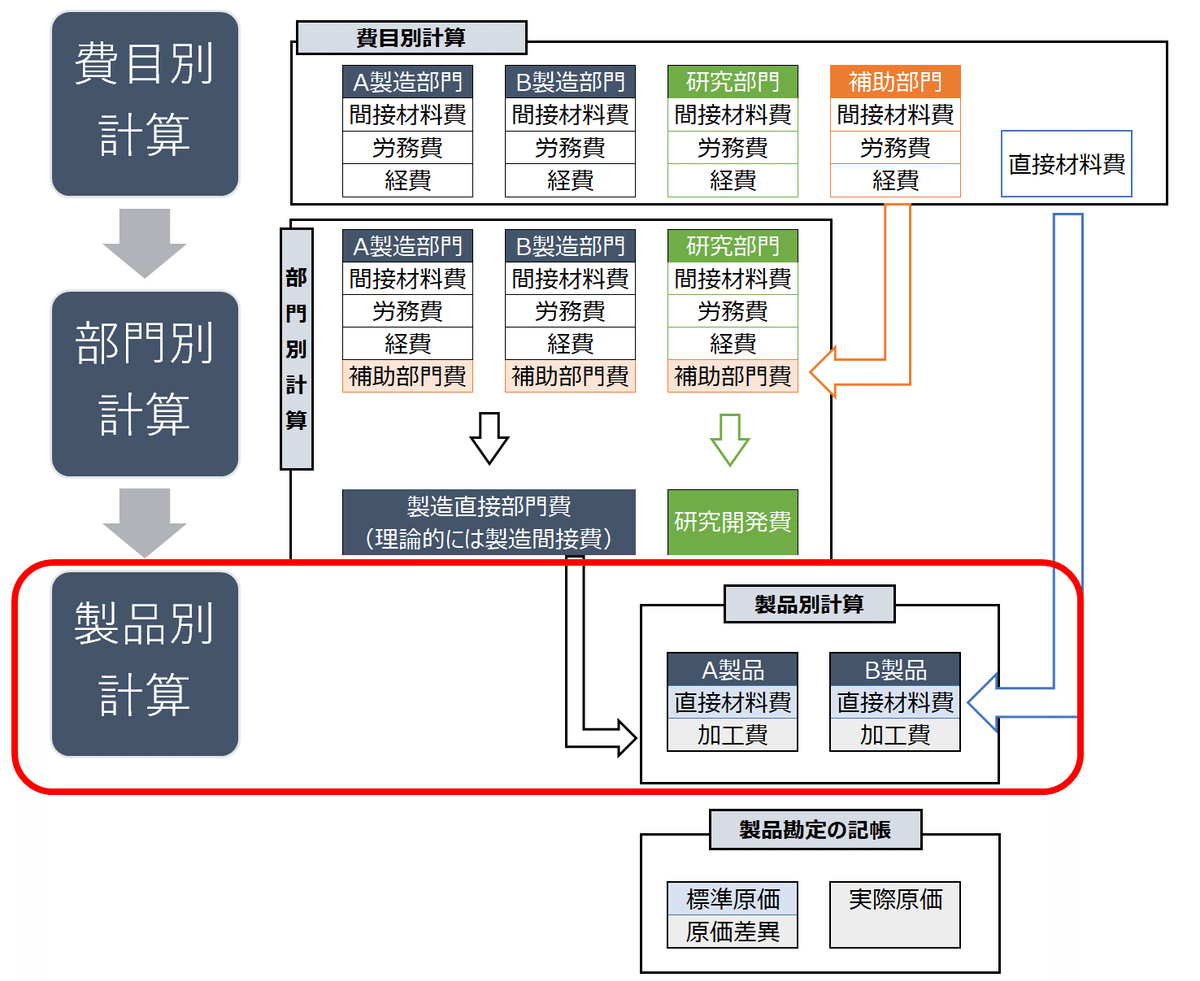
メーカー以外の方は、ここからがよく分からないところだと思います。
原価計算基準で記載されている教科書的な計算と実務の乖離が大きい分野でもあります。
実務的な話に入る前に一般論としての製品別計算の類型についてご紹介したいと思います。(知ってる人は飛ばしてもらって大丈夫です。)
3-1 そもそも製品別計算って何??
原価計算基準では下記の通り定義されています。
一九 原価の製品別計算および原価単位
原価の製品別計算とは、原価要素を一定の製品単位に集計し、単位製品の製造原価を算定する手続をいい、原価計算における第三次の計算段階である。
製品別計算のためには、原価を集計する一定の製品単位すなわち原価単位を定める。原価単位は、これを個数、時間数、度量衡単位等をもって示し、業種の特質に応じて適当に定める。
第四節 原価の製品別計算
端的に言うと、製品別計算は、部門別計算まで行った後の直接製造部門の費用を各製品に配賦するための計算ということになります。
また、その計算方法の類型として下記の通り記述されています。
二〇 製品別計算の形態
製品別計算は、経営における生産形態の種類別に対応して、これを次のような類型に区分する。
(一) 単純総合原価計算
(二) 等級別総合原価計算
(三) 組別総合原価計算
(四) 個別原価計算
第四節 原価の製品別計算
おそらく、部門別計算まではどの会社も似たような計算を行っていると思いますが、製品別計算は業態や製品の特性で大きく変わることになります。
例えば、造船を行っている企業とポッキーなどを生産する製菓メーカーの原価計算は同じでしょうか。
船の製造は、海運会社などから依頼を受けた長期間のプロジェクトとなるはずです。受注後に生産計画書に基づいた製造が実施され、個別受注案件ごとにその原価を集約して採算性を把握する必要があると考えられます。
一方、ポッキーの方はどうでしょうか。季節的な需要変動に応じた生産量の調整はあるものの、おそらく絶え間なく見込み生産が実施されているはずです。
さらに、大量生産されるポッキー1本に対する原価を個別に把握するニーズよりも、ある一定期間に稼働したポッキー生産ラインのトータルコストをまず把握したいはずです。
このように、どのような事業活動を行うかで、当然、原価管理のポイントも変わります。
原価計算基準は、企業の業態に応じた製品別計算の例を示してくれているのです。
3-2 製品別計算の種類と選択
製品別計算は、大きく個別原価計算と総合原価計算に分かれます。
3-2-1 個別原価計算
先程の造船企業の例のように、個別の受注(指図)単位で原価を集計する手法です。製造部門費や直接原料費を指図単位で配賦する形になるので、個々の製品単位の細かい原価管理が可能となります。また案件ごとの生産ステータスに応じて製品出来高計上か、仕掛品計上かを判断します。
反面、適切な管理を行うためには、指図ごとの生産データが必須となります。
案件別の仕掛品勘定を沢山作るイメージです。
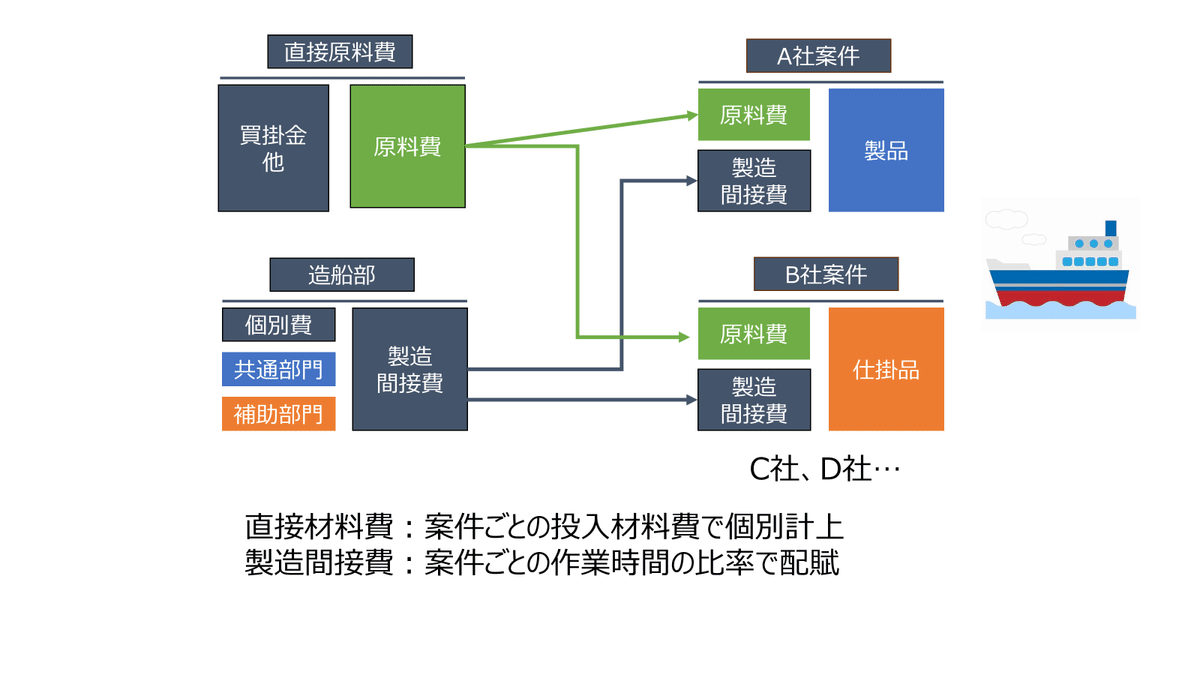
3-2-2 単純総合原価計算
総合原価計算はポッキーの例のように会計期間の内の製造費用を完成品数量と仕掛品数量の比に応じて按分して期末仕掛品在庫と製品出来高を算出する手法です。平均的に投入している原料費や加工費(製造間接費)に関しては、仕掛品に対して、どれぐらいコストがかかったのかハッキリ分からないため、進捗度を考慮してざっくり計算します。
いわば個別原価計算に対して、トータルコストを按分する簡易的な計算なので、製品の単位当たり原価は全て同じになります。
大きい仕掛品勘定をざっくり製品と仕掛品在庫に按分するイメージです。
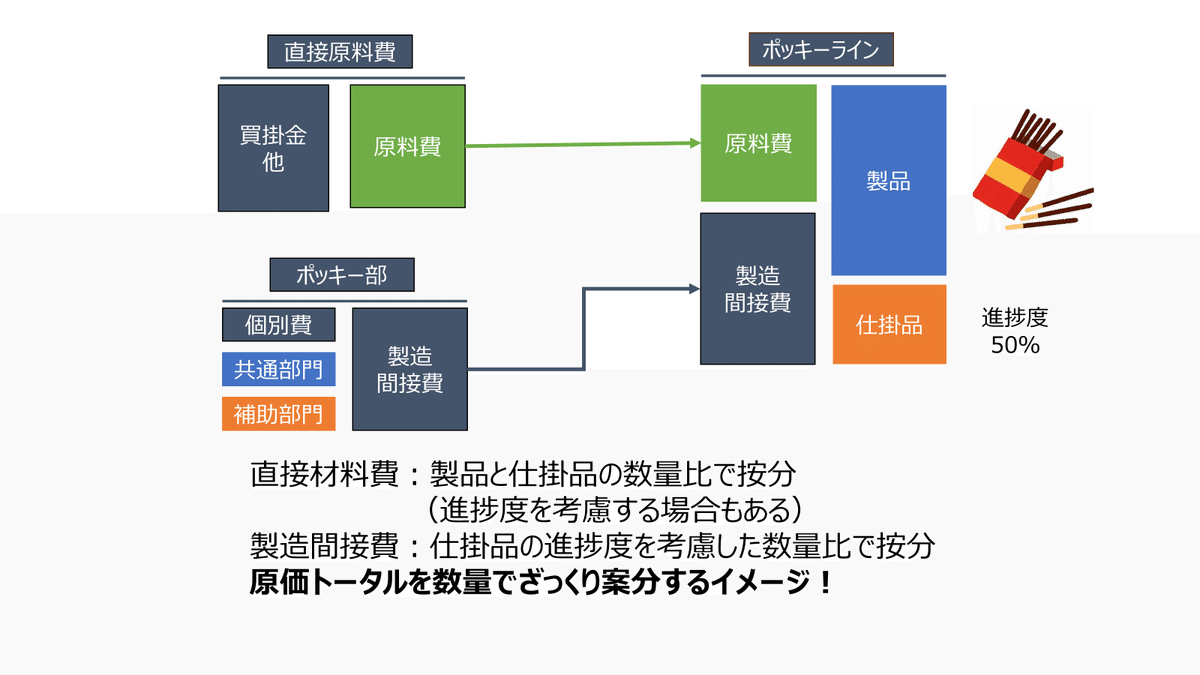
ある製菓メーカーがポッキーだけを生産しているなら、単純な総合原価計算だけでもいいのですが、ポッキー以外も作る場合にはどのような計算になるでしょうか。
原価管理を行うために、総合原価計算には複数のオプションが用意されています。
3-2-3 組別総合原価計算
例えば、ポッキーに加えて、別ラインでカプリコも新たに生産する場合、事業管理者ならカプリコの採算性を把握するために製造費は別管理したいと考える事が普通じゃないでしょうか。
そういう場合は、もともとの部門費、直接原料費の発生段階で費用を分けます。ポッキー部門とカプリコ部門を分けて原価センタを設定し、直接原料費もポッキーラインとカプリコライン別に投入を管理します。
その後、それぞれのラインの進捗度と数量に応じて、期末仕掛品在庫と製品出来高に按分します。
いわば、元の部門費や直接材料費をポッキーとカプリコの組に分けて、総合原価を別計算する方法です。
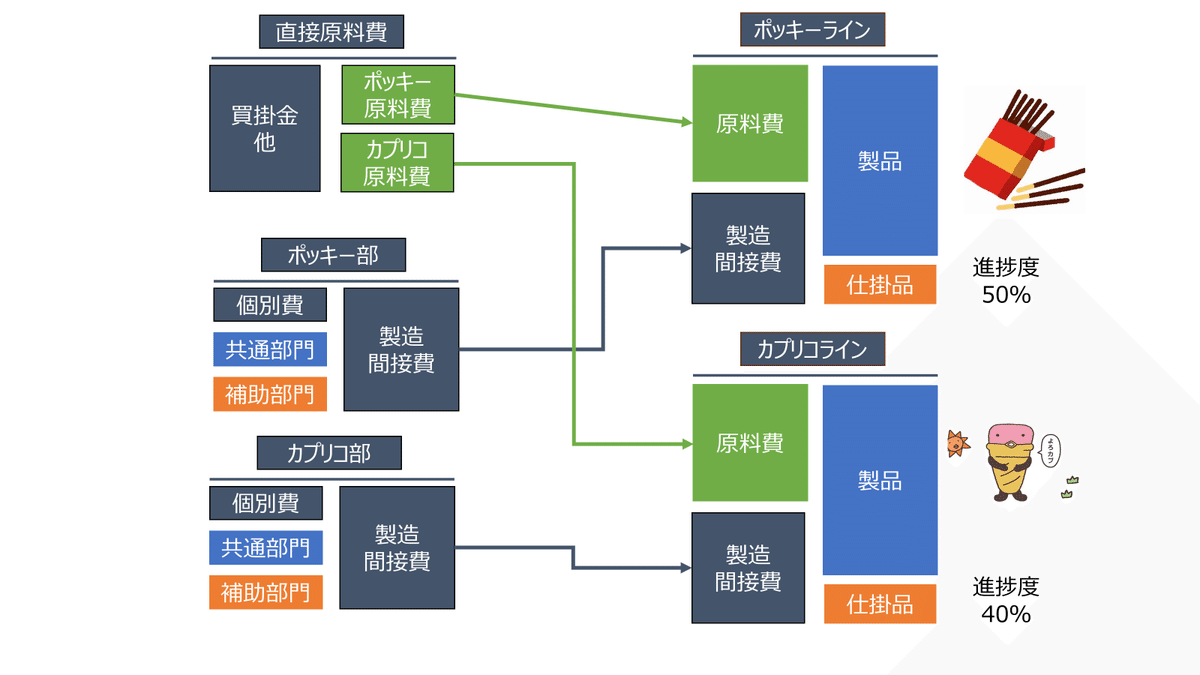
次にポッキーラインで極細版の新製品も作ることになった場合は、どういう計算がいいでしょうか。
3-2-4 等級別原価計算
ポッキーラインの中で、極細ポッキーも作る場合は、ポッキーラインの製造費用を通常ポッキーと極細ポッキーに分ける形で原価計算する方が効率的でしょう。
同じラインで同種の製品を作るので、組別総合原価計算のように大元の直接費と部門費から分ける必要はありません。
このような同一ラインで作る同種の製品の原価をそれぞれ計算する場合、総合原価で計算した結果を物量基準(等価係数)で按分します。
例えば、通常ポッキーと極細ポッキーの原料投入比率などを元に按分係数を作成して、それぞれの製品出来高数量にかけることで分割するのです。
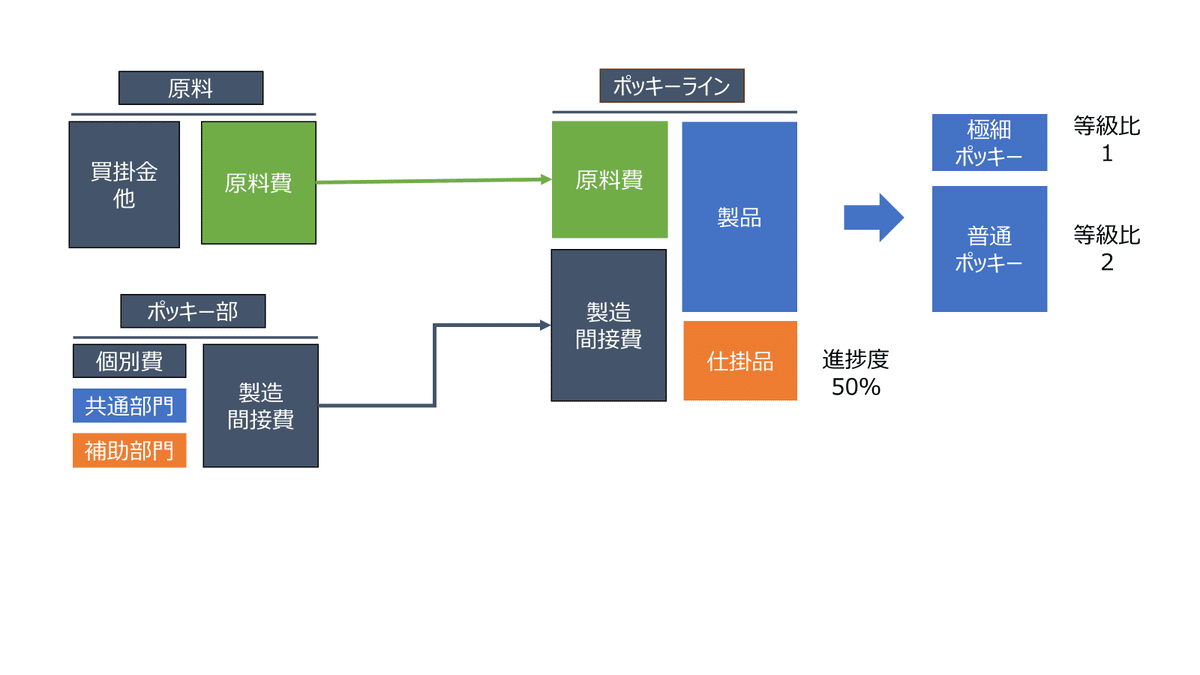
元データを分けないので、組別総合原価計算よりも計算が容易になります。
ちなみに等級別原価計算と似た計算方法として、連産品というものもあります。
端的に言うと、同一工程で異種の製品が必然的に出来てしまうため、重量や比率などの等価係数でも分けられないものなのですが、、
これがどのようなものかについて、かの原価計算の大家 岡本清先生はこのように述べておられます。
豚を1頭仕入れてきて, これを殺すと,豚肉の上肉,中肉,並肉,ラードがとれ,また豚皮や豚の毛がとれる。豚肉はさらに加工をすれば,ロースハム,ベーコン,ソーセージなどの食品がえられる。
…なんと、端的でストイックなお答え!
岡本先生、かっけぇぇ!
ちなみに、連産品は東ソーなどの石油化学製品を扱う企業ではよく使用される概念です。
連産品は、重量など原価と関連する按分基準(価値移転的な按分基準)が算出できないので、仕方なく正常市価(要するに売価)で按分します。
負担能力主義という考え方です。
この方法は結局は売上で按分する事に等しいので、追加加工がない場合は、按分後はどの製品も同じ利益率になります。
そのため、収益管理には全く意味をなさない、棚卸管理のために使う原価計算方法となります。
みなさんもセグメント別按分基準が見出せないものに売上基準を使った事はないですか?
例えば、無形資産の按分とか。
3-3 製品別計算の類型
上記の内容を端的にまとめると下記の表の通りとなります。
原価計算基準は、一番計算精度が高く手間がかかる個別原価計算の採用が、難しい業種もあるため、総合原価計算を工夫して、いかに個別計算に近づけるかについて重点をおいて記載されているとも考えられます。
組別総合原価計算や等級別総合原価計算が中間的な計算と言えるでしょう。
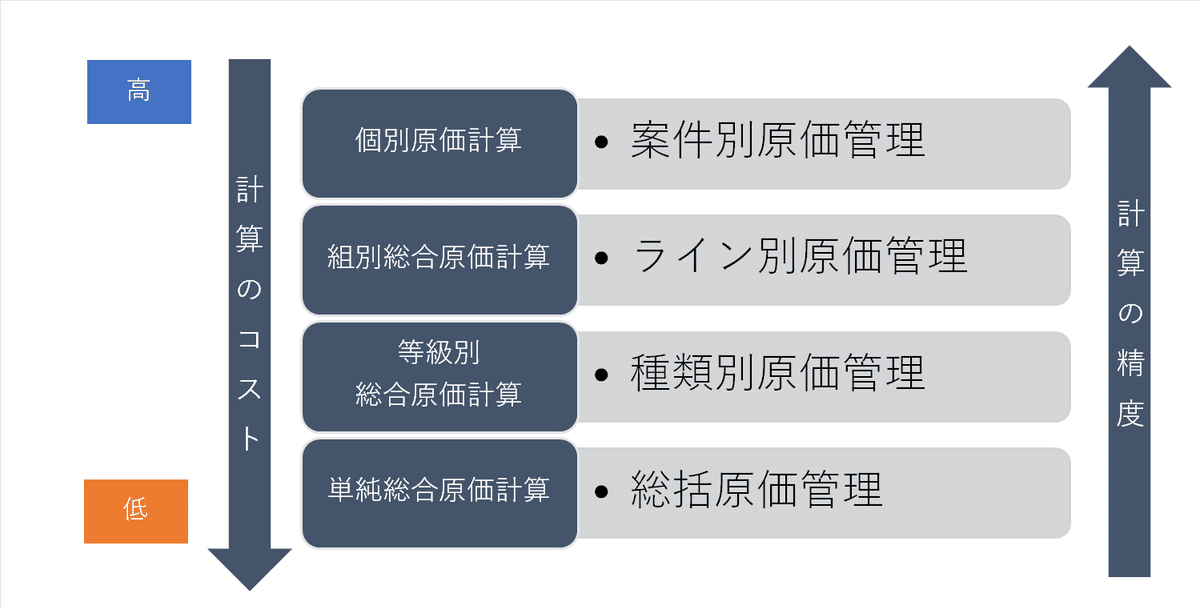
3-4 工程別計算
なお、総合原価計算と個別原価計算の両方で必要な計算方法として、工程別計算があります。
原価計算基準には工程別”総合原価計算”としか記載されていませんが、実務的には個別原価で計算したものを次工程で使用する計算が必要な場面もあるため、総合原価、個別原価の両方で必要な計算方法です。
二五 工程別総合原価計算
総合原価計算において、製造工程が二以上の連続する工程に分けられ、工程ごとにその工程製品の総合原価を計算する場合(この方法を「工程別総合原価計算」という。)には、一工程から次工程へ振り替えられた工程製品の総合原価を、前工程費又は原料費として次工程の製造費用に加算する。この場合、工程間に振り替えられる工程製品の計算は、予定原価又は正常原価によることができる。
第四節 原価の製品別計算
これは、一つの工程で製品が完成しない場合、中間工程の出来高を半製品として計上して、次工程の原価に賦課する計算手法です。
先程のポッキーの例では、チョコレートを作る工程が事前にある場合、そこで生産したチョコをポッキーの工程に流すといった場合に使用します。
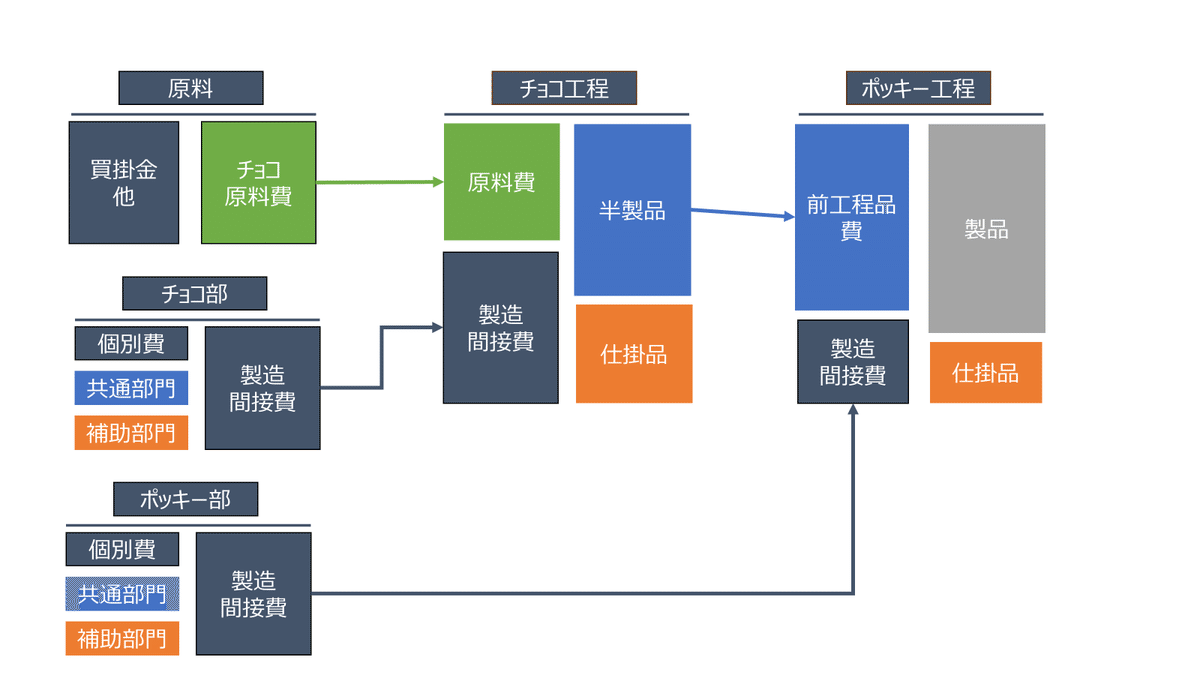
実務上は、ほとんどのメーカーでこの工程別計算が使用されていると思われます。
工程別計算は、前工程の費用を元の原価要素別に次工程に賦課する非累加法と前工程費として流す累加法の二つに大別されます。
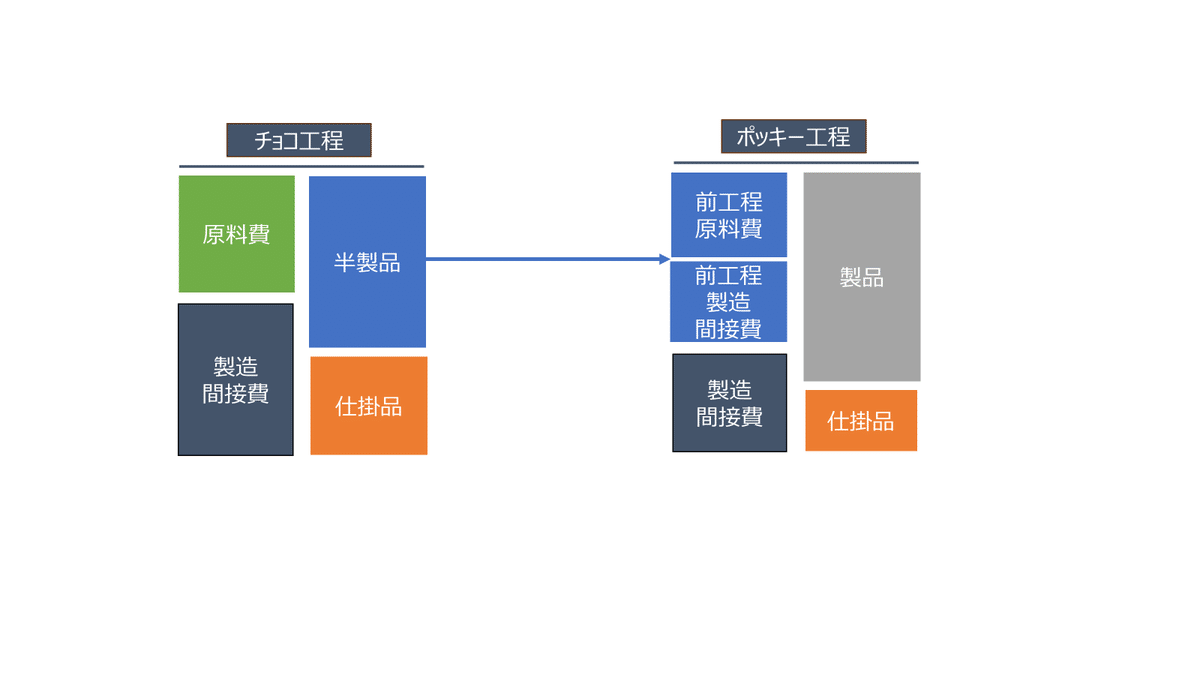
一見、それほど違いはないように見えますが、実務的には重要な意味を持ちます。
例えば、チョコ部門がポッキー部門とカプリコ部門の両方にチョコを提供していたとしましょう。
その記帳を累加法で行った場合、それぞれの部門から見て、直接材料費と加工費(製造間接費)の区別がつきません。
機械装置や化学薬品のような製造工程が長い製品の場合、当然工程も増えるので、最終製品から見た工程間を串刺しにした原価要素別の原価把握が難しくなります。
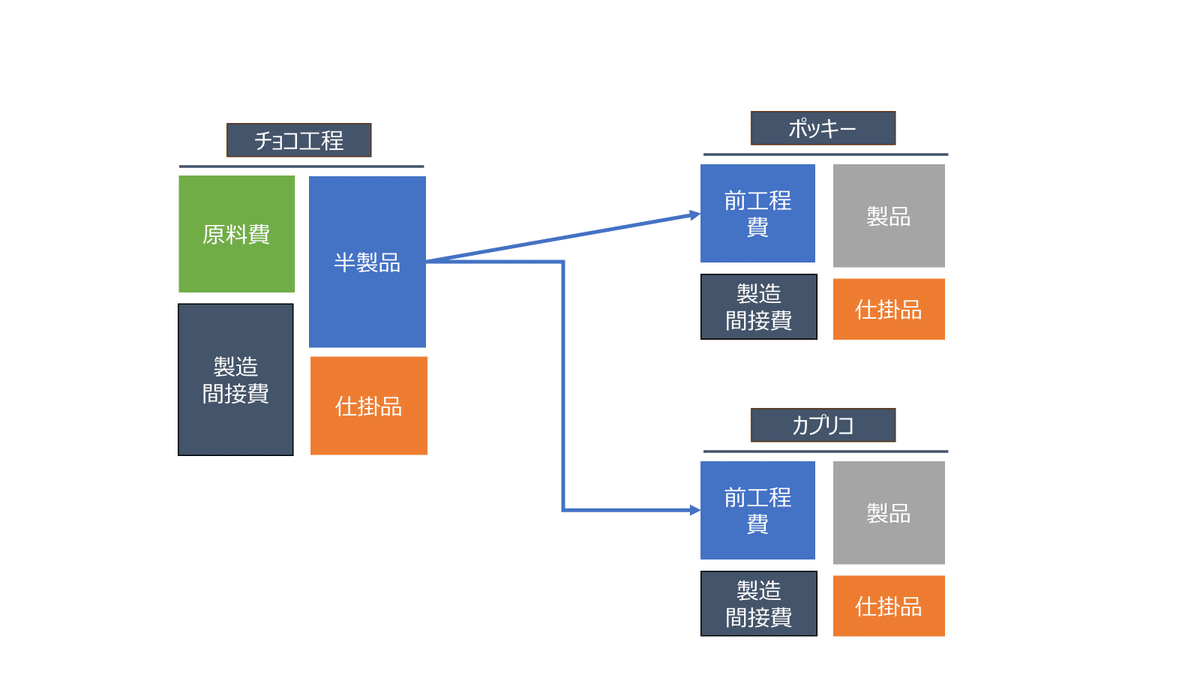
では非累加法が良いかというと、非累加法は記帳が複雑になるので、実務ではあまり採用されていません。
記帳は累加法で行い、製品マスタレシピ(BOM)を使って、工程を串刺しにした原価要素内訳を計算をするサブシステムを構築している企業もあります。
3-5 実務の計算は類型にハマらない?
今までの話を踏まえて、原価計算を行っている会社がこれらの類型にきっちりハマった原価計算をしているかと言うとNOです。
実際は、個別原価計算と総合原価計算を正確に分けられないような計算をしている会社がたくさんあります。
例えば、先ほどポッキーの話を出しましたが、ポッキーは見込み生産を実施しているでしょうが、完全に総合原価計算をしているかというとそうではないと思います。
原価計算基準が示された1962 年から、企業の生産管理のあり方も変化しています。
私が関わっている会社では、見込み生産を行っている製品に個別原価計算を適用しています。
工程数は最大8つくらいのものから、ほぼ単一の工程のものまで様々ですが、とにかく多くの種類の製品を生産しています。得意先も様々に分かれているため、自社のセグメントも細かく分かれています。
細やかな原価管理が必要なため、見込み生産の品目に対しても個別原価計算を採用しています。
上記のような自身の経験も踏まえて、次に製品別計算の選択に必要な観点について述べていきます。
3-5-1 収益管理の観点
どの計算方法を採用するかは、どこまで品目別の収益管理にこだわるかによって変わります。
特定の品目グループ群で原価を一括管理するだけで構わないのであれば、直接製造部門をセグメント単位で分けた組別総合原価計算を実施した後に等級別総合原価計算で容量別などに製品を分割する合わせ技になるかと思います。
但し、共通部品・原料を作る工程など、セグメントをまたがる工程の製造費を組別総合原価計算だけで正確に反映するには無理が生じてきます。
製品ごとの製造時間や投入原料の内容が大きく異なり、品目別の採算性を細かく把握する必要があるのであれば、個別原価計算が必要になります。
3-5-2 生産データ管理の観点
計算方法の決定においては、現場の生産管理データの粒度も重要です。
原価計算において、生産管理システムで管理している以上の細かい管理は不可能です。
在庫管理は、荷姿単位か、kg単位なのか、
作業時間は、時間単位か、日単位か
製品レシピ(BOM)は誰がどのようにメンテするのか
データ入力は、日々入力可能なのか
原価計算システムの設計の段階で製造部門が無理なく管理できる単位を協議して決めておく必要があります。
原価計算基準が出された当時は、製造サイドのデータ管理の負荷を考慮して、細かい生産情報を必要としない総合原価計算を主として、個別原価計算に近づけるアプローチが推奨されたと考えています。
現在はMESなどの製造実行システムでBOMデータやロット別生産データの管理がされており、入力負荷は軽減されています。
そのため、個別原価計算に対応可能なシステム的素地は整ってきていると言えるでしょう。
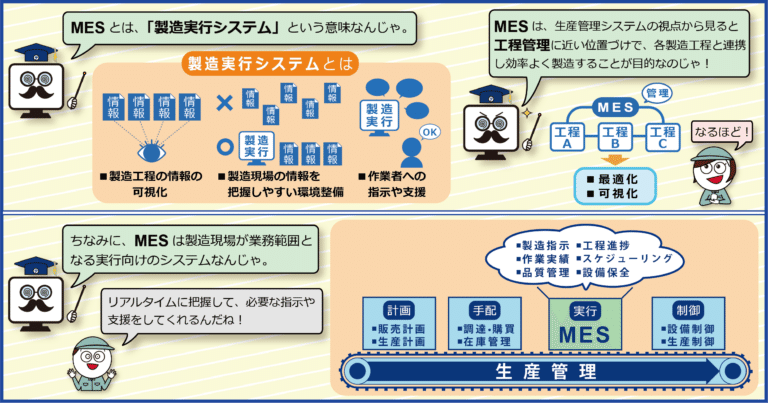
ただ、そうは言っても大量生産データの管理・入力負荷は大きいです。
場合によっては個別原価計算だけでなく、等級別原価計算の合わせ技が必要な場面もあるでしょう。
3-5-3 余談 進捗度に関する疑問
総合原価計算を採用している場合、加工費(製造間接費)や平均的に投入する原料については、進捗度を加味した数量按分が求められます。
この進捗度に関して、簿記の勉強中に「こんなもん、どうやって測るねん!」と思った人はいないでしょうか?
私は、SAPによる個別原価計算で経理のキャリアを積んできたということもあり、この進捗度で仕掛品を計算する方法にあまり馴染めませんでした。
また「管理会計・原価計算の変革」の調査によると仕掛品それぞれに対して実際加工進捗度を測っている企業は調査全体の20.7%であり、教科書通りに細かく進捗度を分けることが難しいと思っている企業が多いようです。
そもそも、現代の生産管理においては、ユーザー監査、許認可…など様々な観点から製造データの管理が求められます。
先程のポッキーにしても、おそらく有効期限、品質の観点から製造ロット単位でデータ管理され、生産計画部門から発注点に基づく生産依頼が製造部門に流れているはずです。
実際の工程管理を原価計算に反映させるという観点からは、「特定の工程を過ぎたかどうか」のようなアバウトな進捗度を測るよりも、下記のような方法でシステム的に進捗管理する方が合理的だと考えています。
工程単位で中間物を管理する半製品コードを設定する
ロット単位でその製造データが完了しているか否かを生産システムから判断する
現代の総合原価計算実務における進捗度の判断は、製造指図単位で判断する個別原価計算に近い手法になっているのではないでしょうか。
3-6 SAPによる製品別計算
SAPの原価計算は、製品の生産ロットサイズ単位で作業時間や直接材料費などの原価要素のBOM情報を設定して、各原価要素の単価情報と掛け合わせることで原価の積み上げを行います。
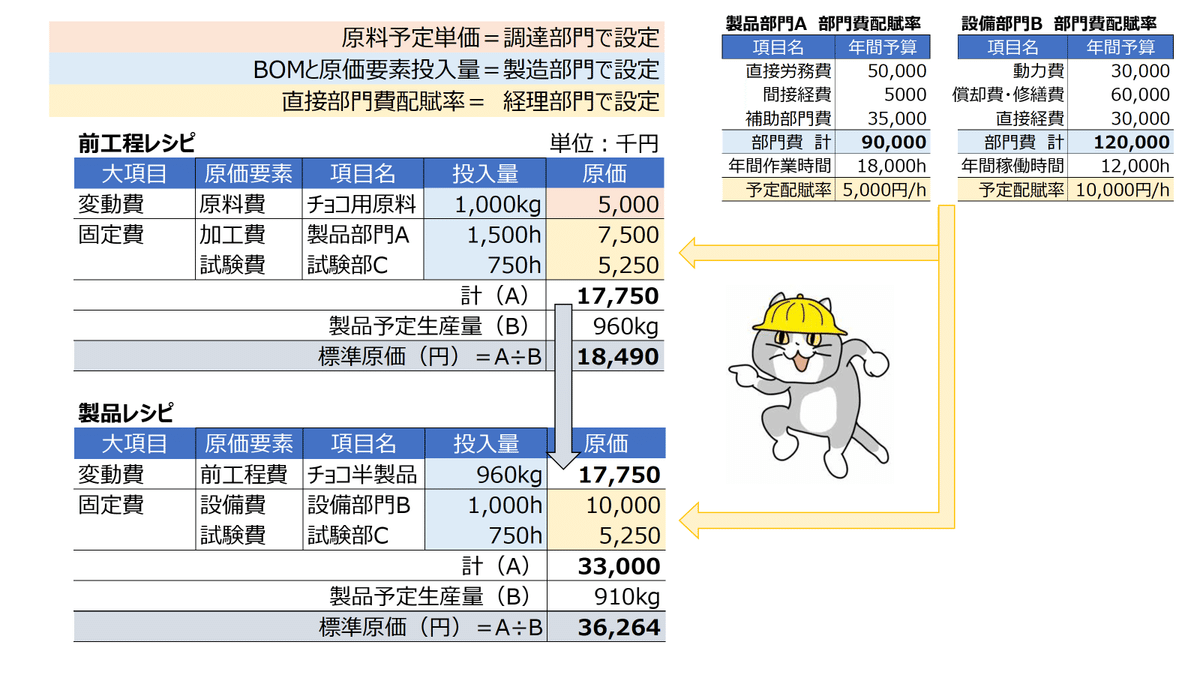
予定単価による標準原価計算が基本です。
SAPでは、原価センタと資源マスタを繋げることで、原価センタに活動タイプという活動量の設定を行うことができるため、原価センタのコストを活動量で製品に配賦する設定が作れるのです。
この設定より作業時間など製造活動に関わる原価要素は、元になる直接部門(原価センタ)のコスト集計を工夫することで、細かく設定することが出来ます。
例えば、専用設備を使った工程に対して作業費と設備費を分けた原価設定をする事もできます。
作業費と設備費を分けた原価センタを設定して、それぞれ異なる配賦基準を設定して、各製品に賦課するのです。
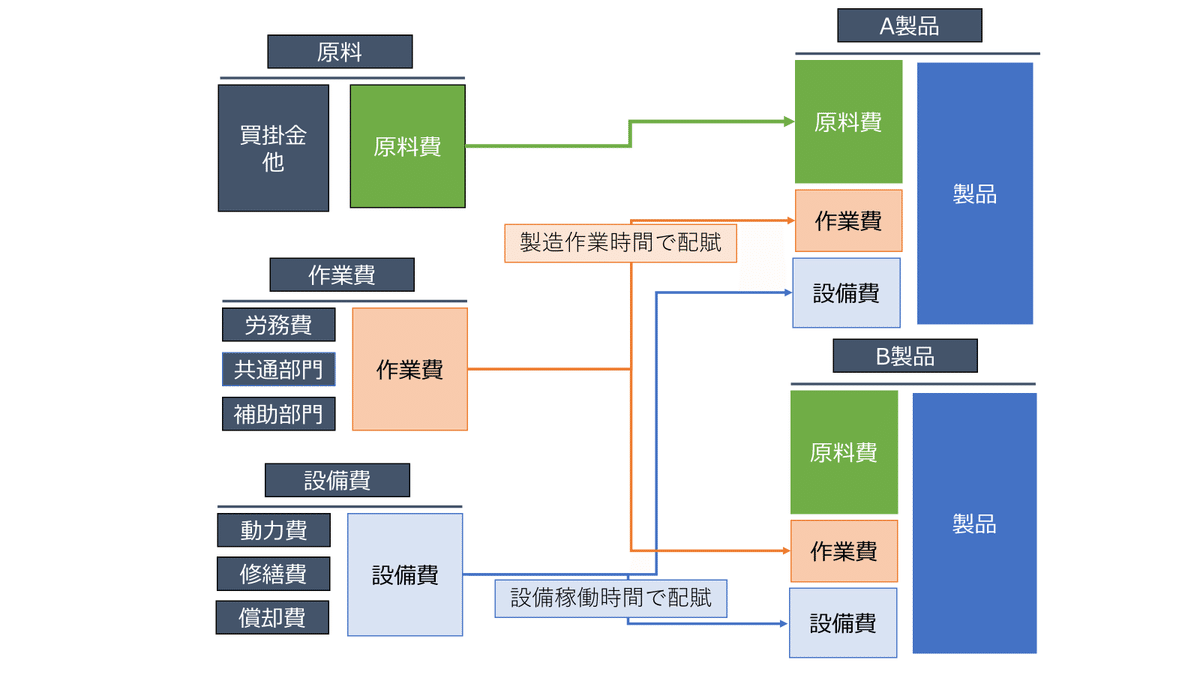
この仕組みを応用して、補助部門のコストをアクティビティ別に製品に直接配賦する活動基準原価計算を行うことも出来ます。
但し、原価要素を分けるという事は、製造部門側で管理する活動(操業度)の基準が増えるということです。
あまりに原価要素を増やしすぎると、標準設定の面でも実際の時間入力管理の面でも現実的ではありません。
作業時間や設備時間など、製造部門で管理出来る原価要素だけに絞るべきです。
3-7 製品別計算の選択に関する考察
製品別計算は、計算方法によって仕掛品の形がコロコロ変わるところが面白いのですが、上手く伝えられたでしょうか。伝わらなかったとすれば、それは私の筆力不足です。(ごめんなさい。。)
ところで、実務上、製品別計算において工程管理やシステム的側面から個別原価計算の素地が固まっている事は説明しましたが、製品別計算を行うためのざっくりした方針を考えてみたいと思います。
前述の収益管理×工程管理能力のマトリクスでいくと下記のような整理になります。
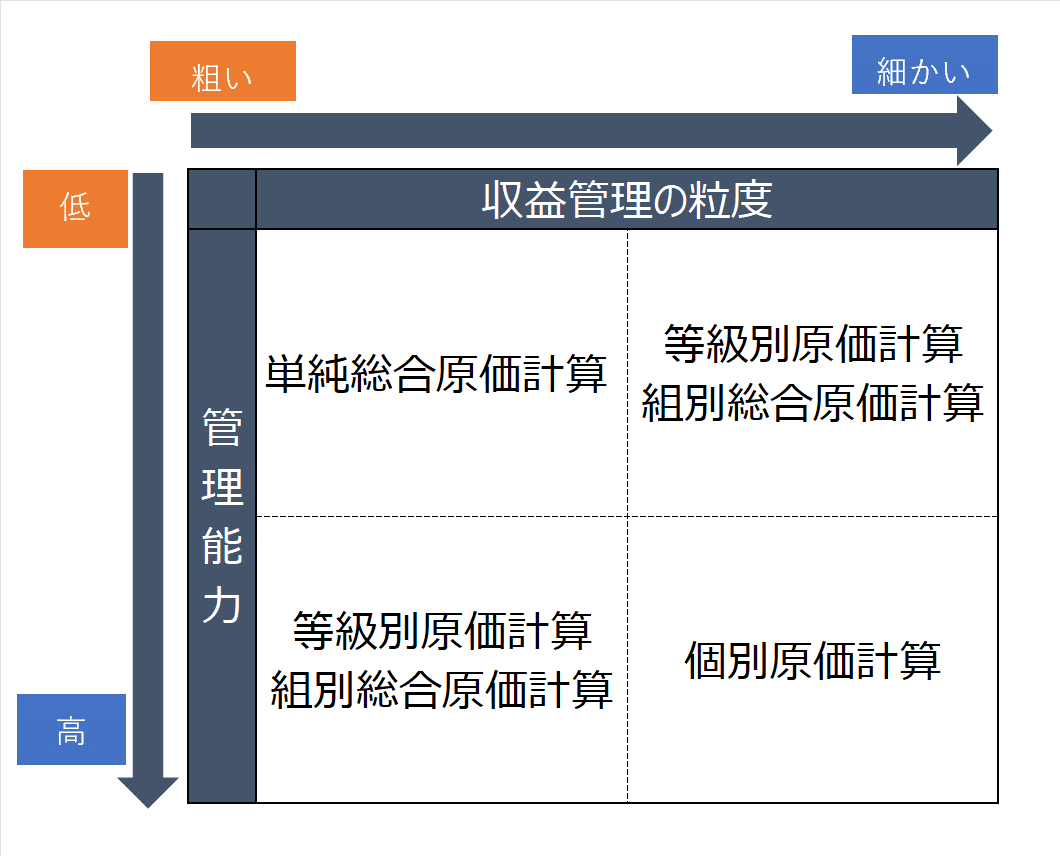
ただ、これはあくまで運用するための判断基準になると思います。
企業として製品別計算がどうあるべきかという観点でいくと、経営戦略との適合も考慮せねばなりません。
そういった観点から、原価計算を決定する場合の基準についても考えてみたいと思います。
下記は、昨年度けいたろうさん(@ClawConciliator)によってまとめられた原価計算についての一連のツイートです。
標準原価計算と実際原価計算の話 - Togetter
ここに企業の原価計算方法の選択について興味深い記述があったために、以下に要約しました。
「実際原価計算 or 標準原価計算の選択は、企業が価格決定力を有するかどうかで決まる。」
自社が自由に売価を決められる
→あるべき原価の計算にこだわる必要がない
→売価にフルコストを反映させるための実際原価が分かれば充分
自社だけで売価が決められない
→あるべき原価が必要
→標準原価管理によるギャップ分析と改善活動が必要
これは、5フォースモデルの業界内構造の分析のうち、買い手の交渉力から原価計算方法の決定を考えるようなアプローチでとても面白いと思いました。
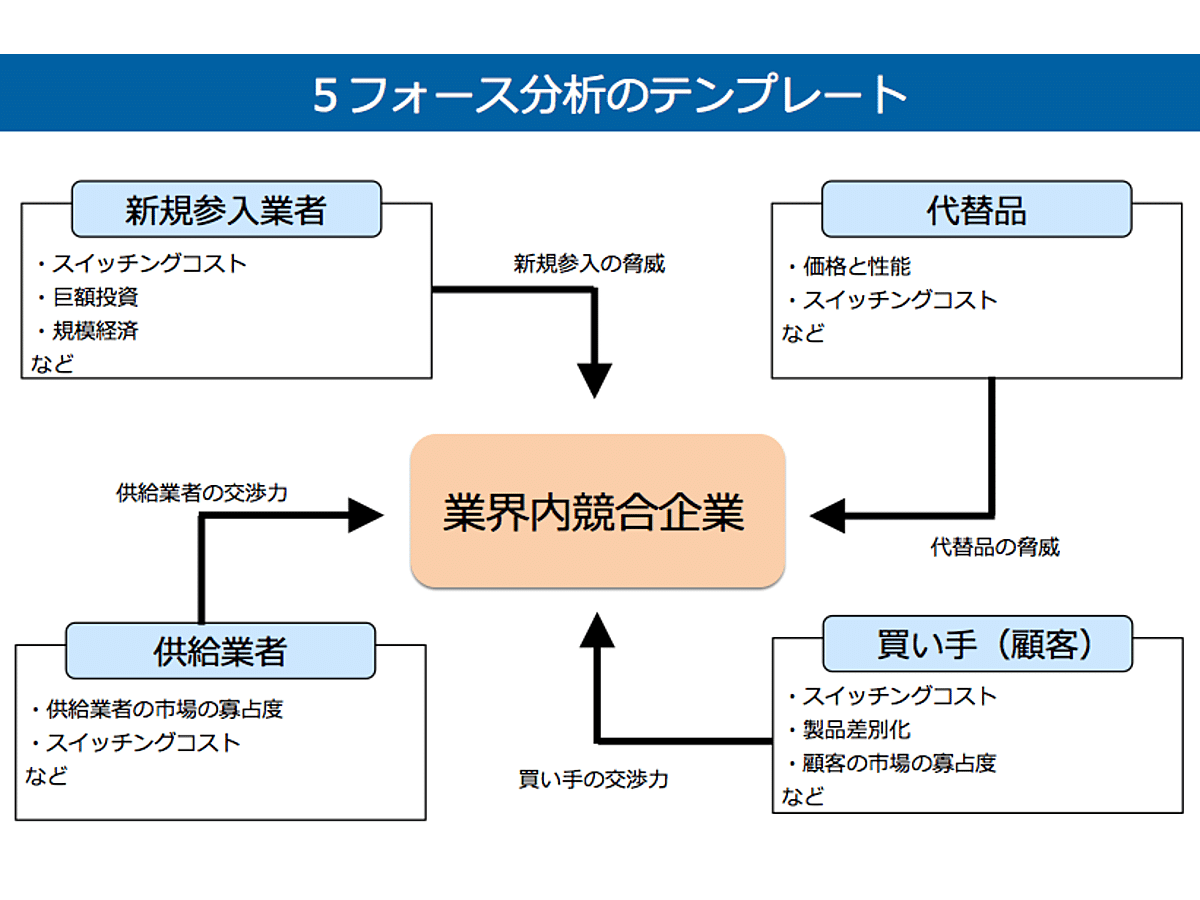
せっかくなので、私も製品別計算において企業戦略からの整理を考えてみたいと思います。
「システムや管理体制でどのような製品別計算も可能な場合、計算方法は企業の戦略が規模の経済性と範囲の経済性のどちらを追求するかで決まる。」
以下、説明します。
規模の経済性の追求
例えば、設備集約型のコストリーダーシップを取るような戦略の場合は、オペレーションも画一的に工場内のセグメントも単一に近づくでしょう。
工程は長くなるかもしれないですが、原価要素が沢山詰まった大きな仕掛品T勘定が直列に並ぶような計算になるはずです。
このような業態な場合、企業の製品別計算は総合原価計算が主選択となると考えます。
範囲の経済性の追求
一方、多能工が一人で複数工程を同時に担うような労働集約的・高付加価値戦略を取る構造の企業の場合、セグメントと細かい原価管理の要請から個別原価計算が主選択になるはずです。
この場合、仕掛品T勘定は企業の管理したいセグメント単位に応じて細かく並列に分かれた個別ブロックの集積になると考えられます。
なお、学術的な裏付けはないので、個人の感想に過ぎないですが、業態に応じた製品別計算の型、特徴的な仕掛品勘定の形というものがある事は間違いないです。
ここまでで、製品別計算は終了です。
次章からは標準原価計算についてです。
4 実際原価と標準原価
やっときました最終章です。
標準原価計算!
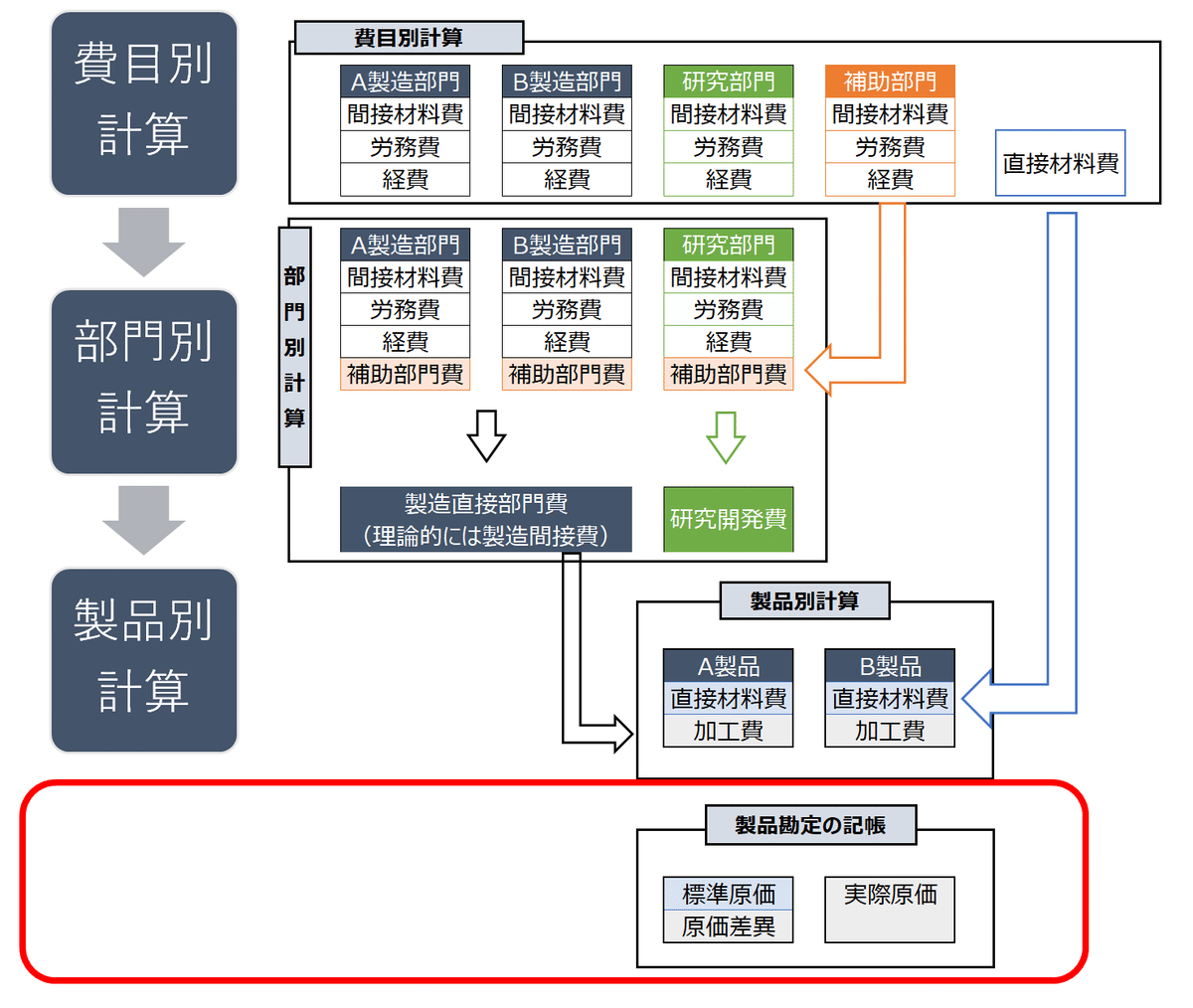
4-1 標準原価計算と実際原価計算の違い
標準原価計算と実際原価計算の最大の違いは、製品別計算における仕掛品から製品(半製品)への記帳が標準原価で記帳される点です。
標準原価計算は、予定単価であらかじめ製品別計算を行い、後追いで実際原価は仕掛品までの計算を行い、それぞれの原価要素で出た原価差額を調整する計算方法です。
要は製品計算を予定単価であらかじめ計算する点が一番の相違点です。
正確には、予定単価(1年以内)or 正常単価(3〜5年の平均)のどちらかで計算しますが、予算との整合性から予定単価を使用する場合が多いと思います。
4-2 原価差異は標準原価計算だけ??
標準原価計算が嫌いな人の理由の第一位が原価差異がよく分からないことでしょう。
ところで、あまり原価計算に馴染みのない方に質問なのですが、下記の計算を行う場合は、標準原価計算でしょうか?
原料費を予定原価で計算
加工費(製造直接部門費)を製品に予定配賦して計算
答えはNoです!
理論的な標準原価計算は、あくまで製品勘定への記帳を標準原価で行う場合だけを呼びます。
実際原価計算は予定単価に実際消費量を乗じたものは実際原価と考えるので、直接原料費、製造間接費に関して予定配賦の場合があるのです。
予定配賦がある限り、原価差額は発生します。
このように実際原価計算でも原価差異が出る場合が沢山あるのです。
四五 実際原価計算制度における原価差異
実際原価計算制度において生ずる主要な原価差異は、おおむね次のように分けて算定する。
(一) 材料副費配賦差異
材料副費配賦差異とは、材料副費の一部又は全部を予定配賦率をもって材料の購入原価に算入することによって生ずる原価差異をいい、一期間におけるその材料副費の配賦額と実際額との差額として算定する。
(二) 材料受入価格差異
材料受入価格差異とは、材料の受入価格を予定価格等をもって計算することによって生ずる原価差異をいい、一期間におけるその材料の受入金額と実際受入金額との差額として算定する。
(三) 材料消費価格差異
材料消費価格差異とは、材料の消費価格を予定価格等をもって計算することによって生ずる原価差異をいい、一期間におけるその材料費額と実際発生額との差額として計算する。
(四) 賃率差異
賃率差異とは、労務費を予定賃率をもって計算することによって生ずる原価差異をいい、一期間におけるその労務費額と実際発生額との差額として算定する。
(五) 製造間接費配賦差異
製造間接費配賦差異とは、製造間接費を予定配賦率をもって製品に配賦することによって生ずる原価差異をいい、一期間におけるその製造間接費の配賦額と実際額との差額として算定する。
(六) 加工費配賦差異
加工費配賦差異とは、部門加工費を予定配賦率をもって製品に配賦することによって生ずる原価差異をいい、一期間におけるその加工費の配賦額と実際額との差額として算定する。
(七) 補助部門費配賦差異
補助部門費配賦差異とは、補助部門費を予定配賦率をもって製造部門に配賦することによって生ずる原価差異をいい、一期間におけるその補助部門費の配賦額と実際額との差額として算定する。
(八) 振替差異
振替差異とは、工程間に振り替えられる工程製品の価額を予定原価又は正常原価をもって計算することによって生ずる原価差異をいい、一期間におけるその工程製品の振替価額と実際額との差額として算定する。
第四章 原価差異の算定および分析
予定単価を一切使用しないガチガチ実際原価計算もSAPなどの現代会計システムでは可能でしょうが、多くの実際原価計算を行っている企業は記帳の迅速化の点で予定配賦をゼロには出来ないと思います。
実際原価と標準原価計算の境界は、実務上は非常に曖昧です。
4-3 標準原価計算の一般的なメリット
記帳の迅速化
能率差異の把握
見積原価の安定した提示
4-3-1 記帳の迅速化
読者の皆さんは工場経理の原価締めが何営業日目で行われていると思いますか?
弊社の場合、本社のPL確定が5営業日なので、4営業日で原価を確定しています。部門費計算の終了は3営業日です。
圧倒的に締めまでに時間がないのです。
その状況で、製造間接費の実際配賦、工程別原価を次々に転がす計算などをやっていては締めることが出来ません。
その点、標準原価計算を採用している場合、仕掛品の計算まで終われば原価が締めれるのです。
4-3-2 能率差異の測定
製品(半製品)を標準原価で計算することで、生まれる標準原価計算だけの原価差異が存在します。
それは能率差異です。
これは、製品別に原価要素別投入量と予定単価で原価を事前に計算する標準原価計算のみが把握できる差異です。
実際原価の原価要素別投入量と製品出来高数量を比較することで、作業能率や得量率など原価能率を測定出来ます。
一般的に能率差異の分析により原価改善に役立つとされています。
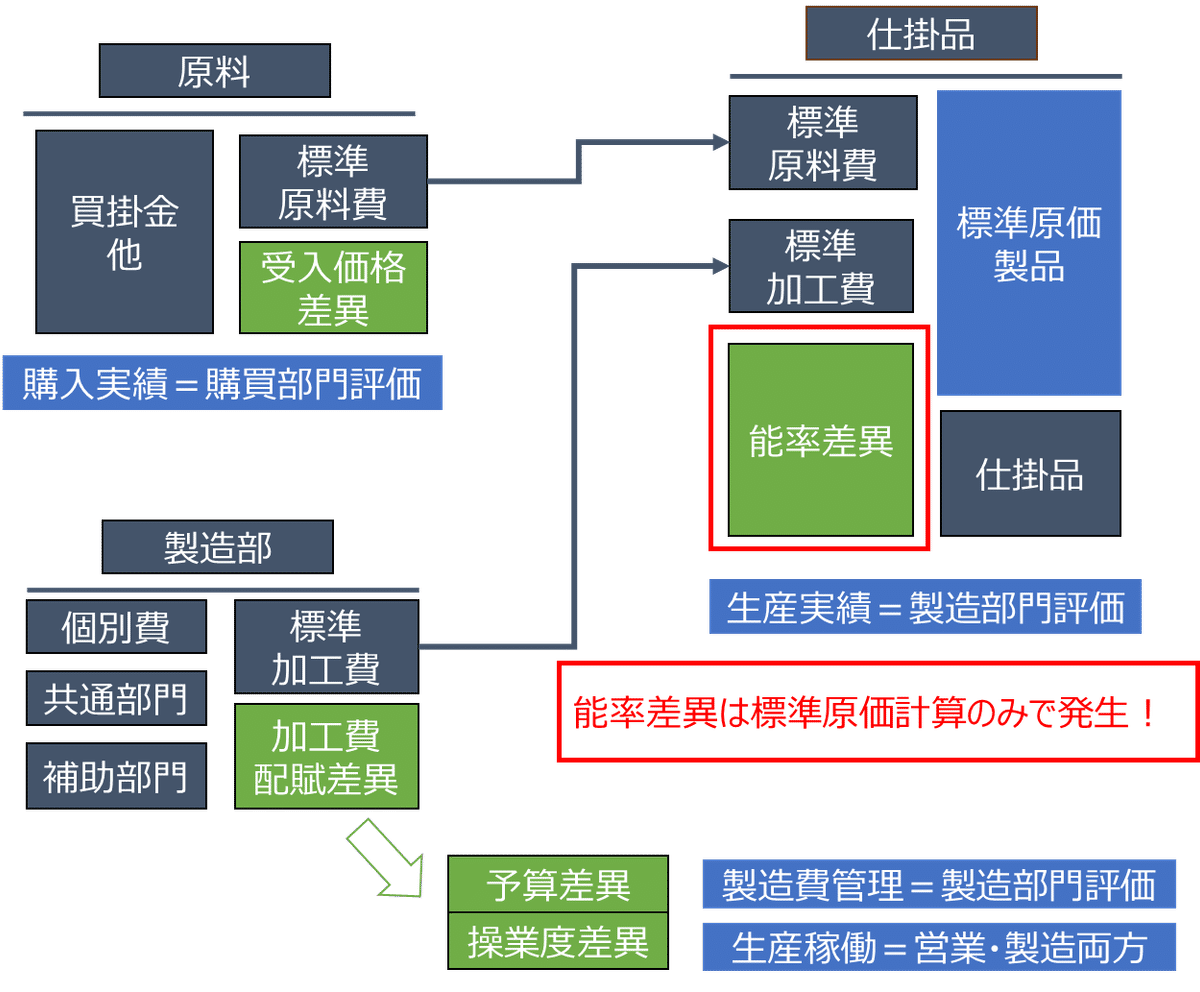
4-3-3 安定した原価の提示
通常の実際原価計算は原価締めのタイミングで品目別の原価が判明します。
日々の営業活動の時点では、原価が分からないのです。標準原価計算であれば、事前に製品計算は終わっているため、営業に見積のための原価提示が可能です。
また実際全部原価計算の場合、販売が悪化した状況では、製造固定費(製造間接費)が在庫に多く配賦されます。
その後、販売が回復した時は過去の製造固定費(製造間接費)が原価に混入するので、販売が回復しても思ったよりも利益が出ない状況が発生します。
標準原価を採用しているのであれば、標準原価ベースの原価と稼働損による原価差異を分けて利益管理することが出来るので、責任範囲を分けることが出来ます。
また、大量の多品種生産を行い、様々な顧客に販売する場合、月度の製造費で個別原価がコロコロ変わると販売価格の決定が困難になるため、営業活動に支障をきたします。
また固定費がそれなりにある場合、限界利益のみを基準とした営業施策も取りにくいです。(どの品目に固定費がどれだけ乗っているか分からないから)
その場合、折衷案として年ベースの標準固定費が賦課された標準原価を基準にした方が営業活動は、やりやすくなります。
4-4 標準原価に必要な設定と具体的運用
4-4-1 マスタ設定
標準原価を採用する場合、標準直接材料単価、標準固定費単価、標準操業度、製造レシピ(BOM)の設定が最低限、必要になります。
原料コード、半製品コード、製品コード全てに対して標準単価が必要になるため、経理だけでなく、製造部門、購買部門など全社的に多大な労力がかかります。
予定単価と製造レシピは毎年変更するケースが多いですが、予算編成のポリシー次第で半期ごとに変更するケースもあります。
(企業会計2023年4月号の記事によると東ソーは毎月変更しているようです。)
情報システム部門やシステムベンダーのサポートが充分にない場合、各部門がマスタ管理で疲弊することも多いです。
4-4-2 原価管理に必要な検証と社内調整
標準原価を安定させるためには、マスタデータの整備が必要なことは、上記で述べました。
次にその原価要素の妥当性の確認作業は、原価を積み上げる経理部門が担うことが多いです。(算定した標準原価を工場、営業に投げて承認を取るプロセスは当然ありますが、、)
具体的には、原料予定単価、予算から算出される製造固定費(直接部門費配賦率)の計算・検証だけでなく、時には製造レシピの妥当性も確認する必要があります。
設定が甘い製造レシピばかりが設定された時、多額の能率差異が発生することになります。
この時、能率差異のチェックを行う経理部門の作業が異常データのシステム的不備を見つける作業になってしまい、本来の原価改善のための分析とは程遠い作業になることもあります。
標準原価計算移行時には、以前の実際原価を標準原価として一時的にスライドさせることも実務的にはありますが、その後も多額の原価差異(能率差異)が発生する場合は、製造部門を指導して是正する運用が必要になります。
また、このようなシステム的不備の検証を経理部門だけでやっていては、本来的な標準原価による改善活動は進みません。マスタの主管となる各部門単位で自主的にマスタ管理を行う体制を整える必要があります。
SAPなどのERPを導入した標準原価計算の運用を社内で定着させるには、製造、品管、物流、研究、経理、経営企画、情報システムなど様々な部門で連携した全社プロジェクトとして導入を進める必要があります。
ERPは各部門が相互に密接に結びついた広大なDBとなります。データ間の連携や他部門がSAPを使ってどのような業務をやっているか理解している(例えば、どのマスタが更新されていないと誰が困るか理解している)キーマンが各部門にいなければ、運用は維持できません。
ERPの運用の破綻は、必要なマスタが更新されないことを意味しますので、必然的に標準原価計算は崩壊します。
4-5 原価差異分析
4-5-1 原価差異の内容と運用
下記は実務で運用される原価差異の一例です。
皆さんの会社の原価差異はどのような費目として管理されていますか?
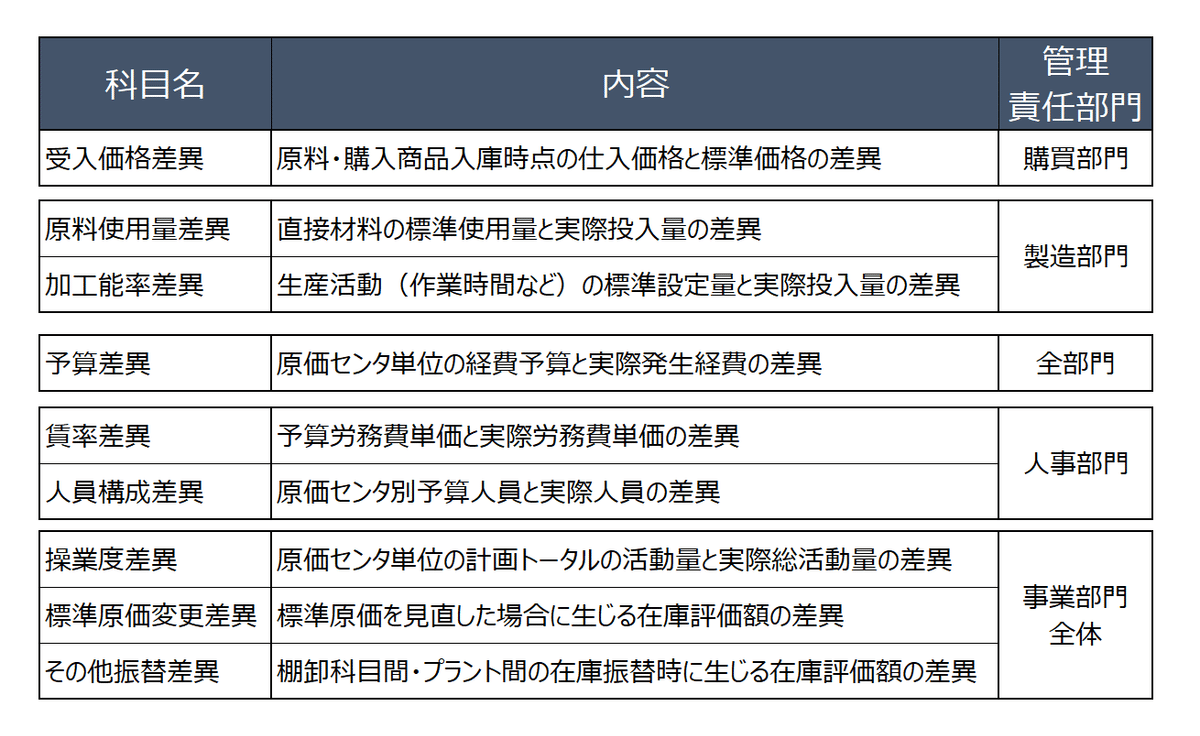
実務的には月次でこれらの差異を各管理者に報告し、内容を分析して改善に繋げるPDCAサイクルを回すことが一般的だと思います。
しかし、各管理者に差異分析をしてもらう事は容易ではありません。各管理者から定性的な情報を集めて経理部門で報告書としてまとめる実務を行なっている企業がほとんどだと思います。
また、差異の中にはある管理者にとって管理不能な差異が混在することもあります。例えば、操業度差異は、営業責任と工場責任が混在しやすい差異です。
普通に考えると販売計画から生産計画は作られるため、工場稼働の増減を示す操業度差異は、営業責任とも思えます。
しかし、操業度差異には間接時間の増加による生産量の低下など工場責任の差異も混在します。
また、生産品目件数や数量、工程の入り組みによっては、営業が出した販売計画から積み上げた生産計画を立てることが出来ない場合があります。(実績が減収傾向の場合、営業が無理矢理積んだ販売計画が生産計画から見て非現実的な数字の時もある。)
その場合、製造サイドは大雑把に出した想定人員の年間所定時間に直接作業時間比率を乗じる方法などで、年間稼働時間を算出することになります。
結果、販売計画と生産計画の連動が分断され、操業度差異の分析が定量的に出来ず、責任の所在は曖昧になってしまいます。
4-5-2 製造間接費配賦差異
「管理会計・原価計算の変革」の調査によると製造間接費配賦差異を分解していない企業は、58.1%となっており、ほとんどの企業で分解して運用されていないようです。
私が関わった企業も全く分けていないか、分けても操業度差異と管理可能差異(予算差異)までの2分法の企業が多かったです。
私はさらに能率差異まで分ける3分法の実務を経験したのですが、公式法変動予算は採用していませんでした。
正直、公式法変動予算は実務ではあまり使えないと思います。
公式法変動予算は、製造間接費予算の総額を変えずに変動費に該当するものを稼働に応じて経費予算に含める、いわば操業度差異を予算差異に付替する手法です。
実務的には、予算差異の比較軸になる経費予算値が変わることになるため、非常に分析しづらいです。
思うに、原価計算基準が出された当時は年間予算が基本で月別予算などは運用されていなかったのではないでしょうか。
急激な稼働変動により、精度の低い製造間接費予算が陳腐化して使えなくなる状況を、固変分解を基礎とした予測値で少しでも緩和するように編み出された手法だと考えています。
現代ではあらゆるステークスホルダーが計画の進捗状況を気にするため、月別予算の精度も求められます。
むしろ、コミットした数字が後から何らかの要因で組み変わってしまうと現場の混乱を招くのです。
実務では製造間接費配賦差異については、下記のような固定予算での分析が多いかと思います。
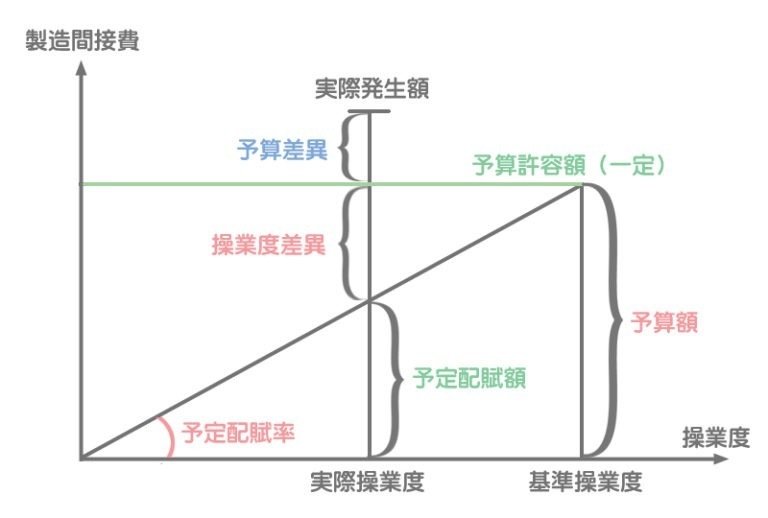
4-5-2 原価差異の全社的共有
差異の要因分析については、能率差異、予算差異、操業度差異の状況について、定常的に工場内で報告会を実施することで原価改善に繋げている企業がありました。
その企業では、特に能率差異について、製造部門で下記のような差異要因の整理を行い、熱心に改善活動に取り組んでいたため、工場の原価管理意識は高かったです。
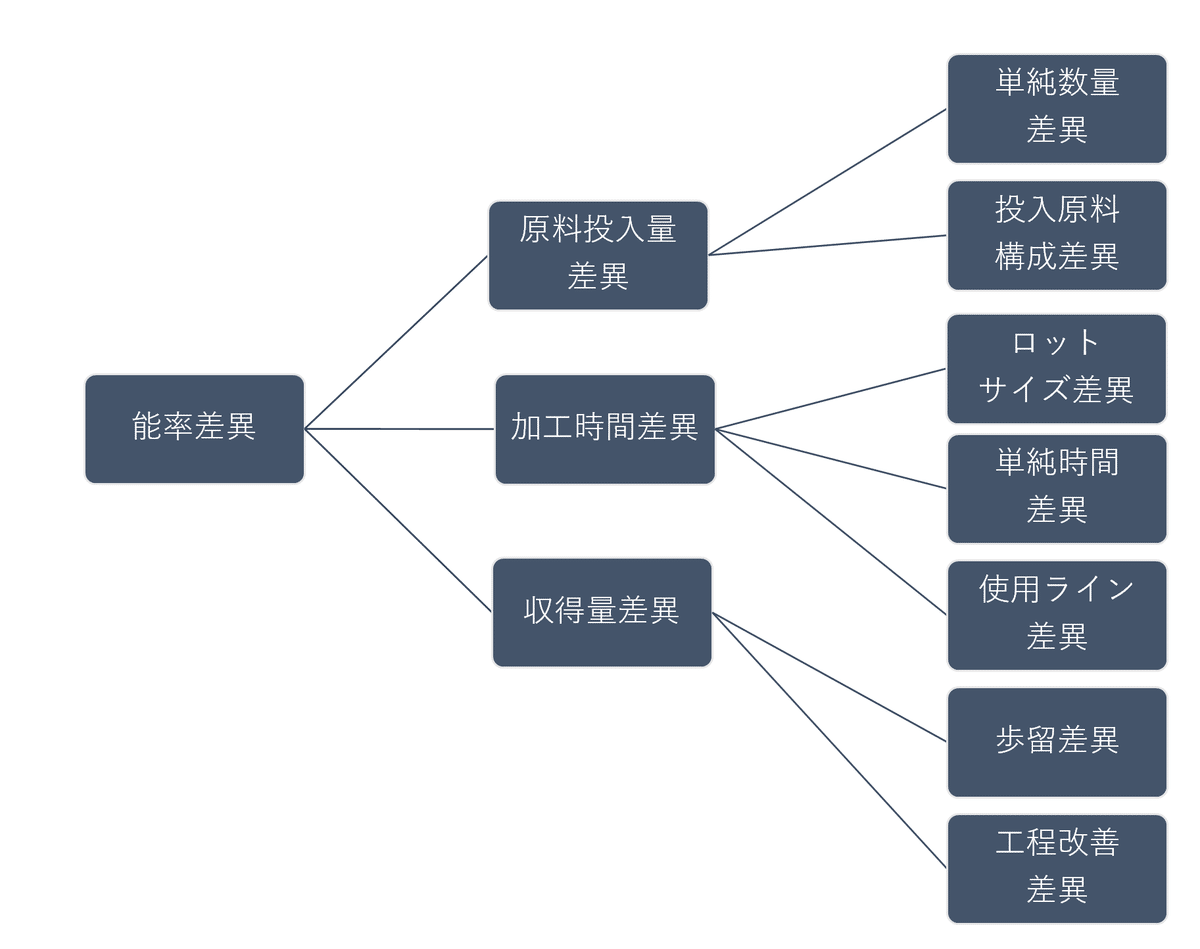
一方で原価差異は必ずしも差益であれば良いというものではないのですが、十分な理解と分析がされず、数字だけが一人歩きする場合もあります。
予算差異のうち、設備予算(修繕費、償却費)については未執行の場合は差益となるため、工場原価差異の利益調整弁のような使い方をされるケースもありました。
4-6 原価差異の配賦
4-6-1 原価差異の処理
原価差異は会計的には多額の差異でなければ、売上原価に配賦するとされています。実務上は法人税法の規定に合わせた基準で、いわゆる売上原価と棚卸の転がし配賦調整をする場合が多いです。
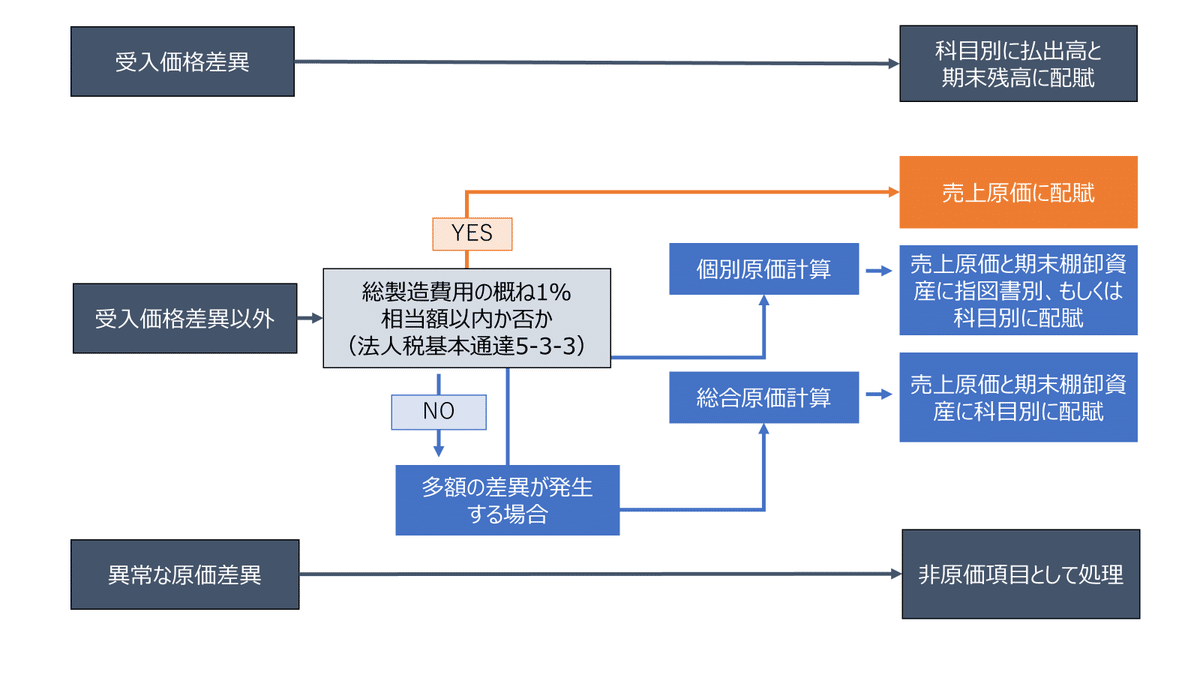
この調整は、半期ごとに処理する企業もあれば、毎月厳密に行う企業もありますが、実務的に煩雑なので、半期に一度がオススメです。
4-6-2 セグメント別PLへの影響
発生した原価差異は前述のとおり売上原価と棚卸に配賦する以外にも、事業セグメント別の配賦が必要になってきます。
原価差異の原価センタや要因となる製品により、差異発生時点でセグメントを識別できることがベストですが、共通工程の半製品で出た差異などついては、セグメント別の再按分が必要な場合もあります。
このようなセグメント共通の原価差異が多額に出た場合、各事業部への説明は非常に難しくなります。按分された原価差異をさらに按分するようなバーチャルな説明になることが多いからです。
4-6-3 原価差異のあるPLは分かりにくい
PL上で原価差異の科目が多数分かれて表示される場合、それが何を意味するかについて、事業管理者から見て、非常に分かりにくい場合があります。
また標準原価を導入している企業は、なぜか独自性のある名前をつける傾向があると思います。
例えば、操業度差異を工場増減産差異と呼んだり、受入価格差異を購入価格差異と呼んだりしている企業もあります。
特に、実務上、期首に発生する標準原価の一斉変更により発生する差異は、
期首改定差
標準原価変更差異
標改差異など
様々な呼ばれ方をしていました。
経理担当者であれば、内容を聞いてから、理論上の一般的な呼称に脳内変換できますが、他社から来た事業管理者は馴染みのない用語にかなり混乱すると思われます。
4-7 それでも標準原価を採用すべき??
4-7-1 記帳の迅速化の観点
SAPによる実際原価計算の機能は、スナップショット原価計算という考え方で、標準原価と同様の階層型レシピを利用することで実際原価をリアルタイムで積み上げる仕様になっているそうです。
単位原価計算とは、製品の部品表や工程表等の製造基本情報、賃率等の会計情報等の大量の情報を用いて、製品番号単位の製品原価を、材料から仕掛品、半製品、製品へと一単位ごとに積み上げて集計する原価計算の方法である。
単位原価計算はスナップショット原価計算とも呼ばれている。
ERPパッケージが採用している品目別実際原価計算は部品表を用いて積み上げ計算を行う点で、単位原価計算を採用しているともいえる。
確かにこのような機能があれば、営業への見積原価の提示や月次締めの迅速化にも対応出来そうです。
下記のような意見もあるので、品目数や共通前工程の有無+SAPの計算パワー次第で実際原価計算も取りうるのだと思われます。
ただ大半の会社は、最低でも製造間接費ぐらいは予定配賦を使用しないと締めの迅速化や見積原価の提示には対応できないと思います。
そういう意味で、予定配賦を全く使わないガチムチ実際原価計算は少数派だと考えています。
4-7-2 標準原価計算の内部統制機能
標準原価計算は複雑です。
原価差異が入り乱れるので、PLが分かりにくいことも認めます。
また、工程間の前工程原価が標準原価で流れるため、串刺しで原価要素別に実際原価を把握することも難しいです。(累加法なら尚更)
しかし、標準原価計算を採用した場合、各原価要素で起きる異常値を差異として明確に把握できます。
私は、「原価差異として要因を明確に分けることや計算のために各種マスタを整備することが、内部統制として機能する」と考えています。
説明します。
突然ですが、原価要素投入の仕掛品への記帳をパーシャルプラン(実際)、シングルプラン(標準)のどちらで行うかという話があります。
製造レシピ(BOM)にもれなく使用予定原料の投入量が設定されていれば、原料投入時点で実際と標準の差異を把握できるので、理論的にはシングルプランを採用出来るのですが、、
機械装置の製造など、投入する部材の変更が頻繁で、長い工程に散らばる場合は、初期に設定された標準レシピ(BOM)のままで投入すべき部材がタイムリーに更新されないことがあります。製造の負担が大きいからです。
この場合は、パーシャルプランを採用して、月末に実際使用した部材の情報を一括して仕掛品勘定に記帳する方法を取るのが普通です。
しかし、実際の原料投入量すら製造側が月次で正確に把握出来ないような場合があるのです。
この時、恐ろしいことが起きます。
しょうがないので、当月仕上がった製品の標準製品レシピから便宜上の原料投入量を逆算して計算・仕訳するのです。
このような方法を取った場合、棚卸が現物と合わなくなるので、期末に実地棚卸を行った時に実数カウントで大幅にアンマッチが発生します。
これにより、期末に原価差異(予算差異or能率差異)が発生することになります。
似たような逆算記帳方法で、バックフラッシュ原価計算という記帳方法がありますが、、
バックフラッシュ原価計算とは、ジャストインタイム生産方式を採用する企業が、原価計算に要する手数と経費を節約するために工夫した原価計算であって、当期に発生した製造費用はすべて売上原価勘定に借方記入しておき、期末になって残った在庫品へ、製品単位あたり標準原価または予定原価を利用し、売上原価勘定からその製造費用をバックフラッシュ(逆流)させる、
あるいは差し戻す原価計算方式をいう。
実際投入を全く把握していない上記の手法は、バックフラッシュとは似て非なる計算方法です。私はこれを勝手にバックドラフト原価計算と呼んでいます。(後で棚卸が爆発するからです。)
前置きが長くなってしまいましたが、バックドラフト原価計算による原価差異は、以下を示唆してくれます。
製造のレシピ管理意識が甘い(無い)→BOMが無茶苦茶
棚卸管理体制がヤバい
標準原価に反映されてない原料が大量にある→原価がおかしい→販売価格の設定もおかしい
このように、原価差異発生要因を分析をする過程で内部統制上の不備を読み取れるのです。
私が関わった会社では、実際原価を採用していた頃は、一回限りの特注用原料などがコード管理できずに期末に多額の棚卸減耗費が発生していました。
しかし、標準原価への移行にあたり、特注原料も含めたほぼ全ての直接原料をコード化してSAPへ設定する運用を構築したため、棚卸のアンマッチは大幅に減りました。
標準原価が正しく反映されるように運用を検討する過程で内部統制が整備される事は一つのメリットだと考えています。
4-7-3 実際原価計算の方がいい会社
生産に応じて製法やBOMが頻繁に変わる企業
能率差異の把握が困難(無理)なので、厳密な標準原価を運用する必要性は薄いと思われます。
ただ、変更の履歴管理や実際原価を正しく計算するために、やはりマスタ関連の整備は必要だと思います。
事業環境から最新原価の必要性が高い企業
例えば半導体関連企業は、ライフサイクルが短く、また需要の変動に稼働が影響されやすい装置産業と言われています。
このような企業の場合、需要の変動で自社の固定費の回収がどうなるかを把握したいニーズが強いです。そうなると、実際原価による最新原価の必要性が高まります。
またコストを全て売価に転嫁できるような特殊な企業も実際原価の方がいいでしょう。
4-7-4 明確な管理指標を持たない企業には標準原価が必要?
事業環境から実際原価を採用した方がいい企業以外は、実際原価と標準原価をどちらを採用するかは、結局は会社として明確なKPIを見つけているかによると考えています。
実際原価計算派の方からは下記のような意見があります。
・原料の得量差異及び稼働による増減産差だけを把握できれば良いので実際原価を採用している。
・最新稼働を反映させた結果、個別の原価のバラツキがあっても、それはラインの稼働率そのものを示しているから逆に分かりやすい。
このように、自社で原価の管理指標を見つけている場合も、複雑な原価差異を把握する必要性は低いと思われます。
ただ、KPIが明確になっていない大半の企業にとっては標準原価計算のフレームワークは必要なのではないでしょうか。
京セラのアメーバ経営のような必勝パターン(?)や明確な経営哲学を持たない企業にとって、事業戦略→販売計画→投資・要員計画→購買・経費計画→生産・在庫計画→原価計画と、あらゆる計画が有機的に連動して標準原価に収束する予算統制は強力なフレームワークだと考えています。
原価差異が出ている場合、あるいは出るべき原価差異が出ない場合、事業活動や統制のどこかが歪になっているはずです。
大半の企業は、このような予算統制のフレームを正しく連動させることすら難しいです。
私にとっては、標準原価という枠無しで適切な原価管理を成立させることは、キャンパスを用いずに空に絵を描くに等しい行為です。
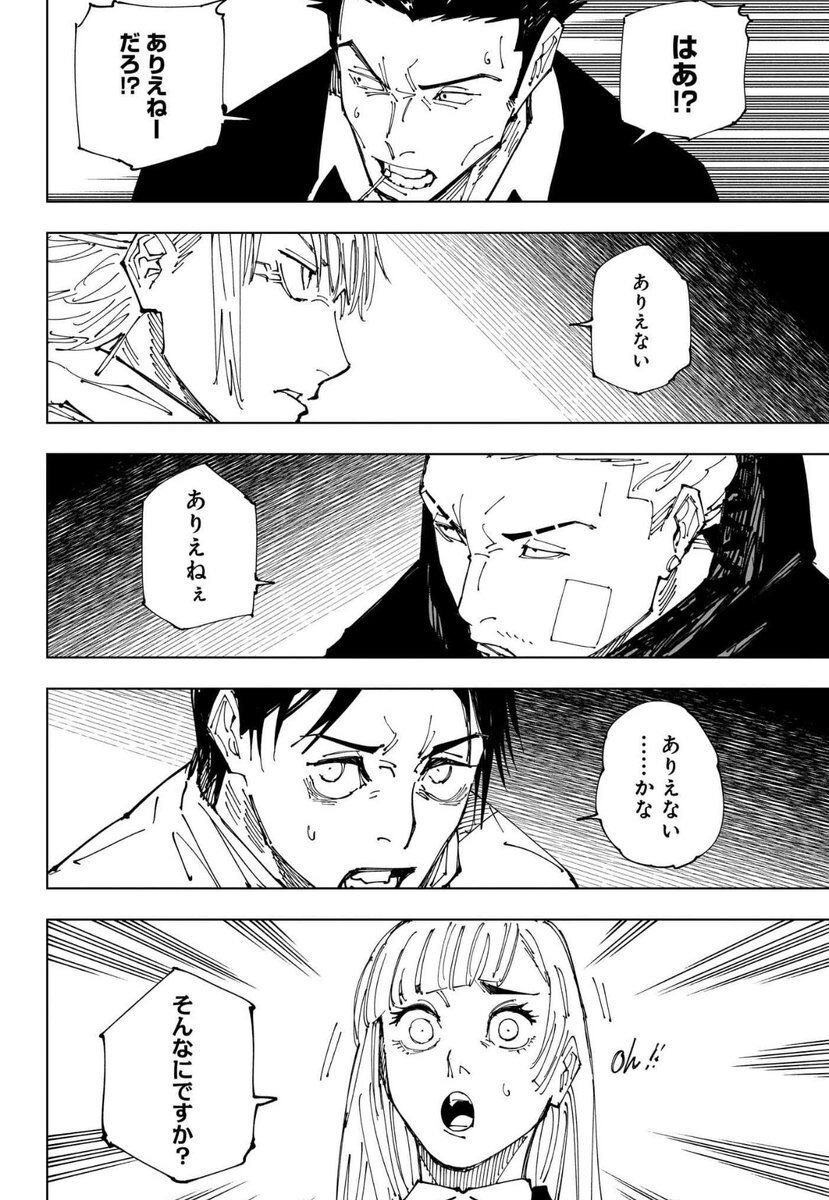
実際原価でも機能間で有機的結合のある予算編成を行い、内部統制も整備している企業は、標準原価での管理もおそらく可能でしょう。
しかし、杜撰な標準原価管理の企業が実際原価を採用しても原価管理が上手くいくケースはとても低いと思います。
個人的には、年間総製造費に対して発生する原価差異が5%以内に抑えられるように運用できてから、はじめて標準原価本来の目的の原価改善に取り組めるのではないでしょうか。
4-7-3 標準原価の運用で一番大事なこと
標準原価計算で一番大事なことは、自社の原価差異発生のメカニズムを理解して、全社で共有することです。
ただ原価差異を垂れ流しても無意味です。差益でも差損でもそこから意味を見出すことに意味があります。(哲学的)
組織の機能間で連携のとれた予算編成を行う
運用ルールの整備などマスタ管理を徹底する
原価差異科目を要因別に分けて可視化する
原価差異の責任部門を決める
責任部門で差異要因を分析する
プロセスの不備は全社的に対応して改善する
このような差異の検証プロセスなくして、標準原価計算の活用は不可能です。
標準原価の嫌な部分もたくさん書きましたが、標準原価とSAPに教えられたことも沢山あったので、私自身は、やっぱり標準原価を憎むことは出来ません。
計算に必要なマスタと運用を紐解く過程で、自社の原価計算の理解が深まったことは間違いないです。私にとっては、標準原価計算は人を育ててくれる計算方法でした。
あとがき
最後までこのような長文(駄文)を読んで頂いた皆さんには感謝しかありません。
簡単にまとめようと思ったのですが、書きたいことを書いてたら長くなってしまいました。
原価計算ってほんと難しいですね。
最後は以下に簡単な総括を書いて締めさせて頂きます。
科目別計算
・科目マスタはマメに整備
・原料コードは可能な限り設定
部門別計算
・原価センタは無駄に増やさない
・1次配賦、2次配賦は出来るだけシンプルに
製品別計算
計算方法選択の基準は下記の通り、
・どういう収益管理をしたいか
・どこまで管理できるか
標準原価
・標準原価管理は複雑なので前提の社内共有と検証は必須
・標準原価による統制は企業の自浄作用にもなりうる
明日はケイバリュエーション☻ (鈴木健治)さんの記事になります~!
長時間のお付き合い、ありがとうございました。
参考文献
川野 克典 .管理会計・原価計算の変革: 競争力を強化する経理・財務部門の役割. 中央経済社,
Accounting(企業会計).「聴け、工場の声」(2023年3月3日号). 中央経済社,
KPMG/あずさ監査法人アカウンティングアドバイザリーサービス.勘定科目統一の実務.中央経済社, 2019/7/18.
清水 孝.わが国原価計算実務の現状 (2022年3月).早稲田大学,
岡本 清 .原価計算.国元書房,
大野 貴史.プロジェクト別原価計算の実務Q&A. 中央経済社,
この記事が気に入ったらサポートをしてみませんか?